7 Essential Checks Auto Shops Make When Tuning High-Performance Vehicles in 2024
7 Essential Checks Auto Shops Make When Tuning High-Performance Vehicles in 2024 - Engine Control Unit Mapping Tests Using Motec M150 ECU System
The MoTeC M150 ECU is a powerful tool for fine-tuning high-performance engines, offering a level of control previously unseen in many automotive applications. It stands out for its flexibility, allowing tuners to not only adjust engine parameters but also seamlessly connect with other vehicle systems like advanced transmissions, like the Tremec TR9070 DCT. The M150's design revolves around torque-based tuning, letting users precisely define things like torque limits and boost pressure. This approach, paired with rigorous validation checks such as ignition and throttle mapping, allows for comprehensive optimization of engine output. The MoTeC M150 is designed to be versatile and secure, making it a popular choice in diverse racing and tuning settings. Its compatibility with various vehicles, achieved through integration harnesses and sensor integration, along with strong security features, makes it an attractive solution for professional tuners looking to push performance limits and ensure the reliability and safety of the tuned vehicles.
The Motec M150, a sophisticated engine control unit, stands out due to its computational prowess, handling complex algorithms to optimize engine performance beyond what many stock ECUs can achieve. This capability is particularly valuable during mapping tests, where tuners can monitor vital parameters like air-fuel ratios and ignition timing in real time. These real-time insights allow for immediate adjustments, leading to notable performance increases—sometimes as much as 10-15% in high-performance vehicles.
The M150's multi-channel data logging capacity is a cornerstone of its effectiveness. By recording data from numerous sensors simultaneously, it provides an exhaustive picture of engine behavior under various conditions, a crucial component in refining engine maps. The M150's adaptability extends to its customizable mapping, enabling tuners to tailor engine behavior to specific performance goals or driving scenarios, whether for track days or everyday use.
Calibration often involves a strategic balance between 'open loop' and 'closed loop' tuning. This approach allows engineers to strategically determine when to rely on pre-programmed maps versus real-time sensor feedback for optimizing engine performance. Beyond fuel and ignition, the M150 can also fine-tune boost levels in turbocharged vehicles, empowering tuners to enhance turbo efficiency and responsiveness.
This type of ECU management is prevalent in some of the most impressive supercars, suggesting the significance of meticulous tuning in achieving the mind-blowing performance levels seen in vehicles like those from Bugatti. In fact, ECU mapping has revealed that some vehicles possess untapped potential, with some showing over 20 hp increases from simple calibration adjustments. These revelations highlight the level of hidden performance often concealed by standard ECU limitations.
Furthermore, the M150's sophisticated software enables simulation of diverse driving scenarios, allowing predictions of engine behavior and performance without exhaustive real-world testing. This capability represents a significant resource and time saver for development and refinement. Finally, the M150 extends to throttle mapping, which allows the tuning of the throttle response to driver inputs. This offers the ability to tailor the throttle for smooth transitions or aggressive response, catering to driver preferences and track demands. This capability emphasizes how subtle tuning can refine the driving experience and amplify a vehicle's potential for peak performance.
7 Essential Checks Auto Shops Make When Tuning High-Performance Vehicles in 2024 - Advanced Suspension Setup Analysis with Ohlins Track Telemetry
Advanced suspension setup analysis is becoming increasingly vital for extracting maximum performance from high-performance vehicles, especially when combined with tools like Öhlins Track Telemetry. The use of technology like Öhlins SmartEC3, which automatically adjusts damping and preload based on real-time inputs, allows for finely tuned suspension setups. These systems are designed to accommodate the demands of luxury and supercars, maximizing handling and ride comfort even under extreme track conditions. This focus on fine-tuning is evident in how these systems seamlessly integrate complex algorithms that are specifically tailored for track-focused driving.
The constant evolution of Öhlins suspension technology, spanning OEM and aftermarket applications, ensures that enthusiasts have access to customization options that merge a refined street ride with aggressive track capabilities. While often overlooked by casual drivers, regular inspections and adjustments of the suspension are critical for maintaining optimal performance. This becomes even more critical in high-performance situations where any deviation from optimal settings can negatively impact the car's performance and handling. Ultimately, understanding the intricate interplay between suspension components and their impact on handling and overall driving experience is a critical aspect of tuning high-performance vehicles in 2024.
Ohlins Track Telemetry offers a deep dive into suspension performance, going beyond basic measurements like ride height and spring rates. This kind of data-rich approach allows engineers to truly understand how a vehicle's suspension behaves under various driving conditions. For instance, the detailed telemetry provides insights into wheel travel dynamics and damping forces. This information is particularly valuable when tuning for high-speed driving scenarios.
Modern high-performance vehicles often utilize active suspension systems that adapt to changing conditions using this sort of telemetry. The suspension can automatically adjust damping rates based on the road surface or driver inputs. This ability to self-optimize improves both ride comfort and handling.
It's also interesting how temperature can affect suspension performance. The viscosity of the damping fluid changes with temperature, which directly influences the system's responsiveness. Therefore, high-performance applications need precise temperature monitoring to ensure the suspension works as intended across a variety of conditions.
Frequency analysis is another crucial tool. By looking at how often the suspension oscillates in response to different inputs (bumps, turns), engineers can precisely refine damping rates to eliminate unwanted harshness or vibrations. This can significantly refine the overall ride quality while also potentially improving performance.
Furthermore, there's a noticeable connection between suspension tuning and vehicle dynamics. The roll gradient, how much the vehicle body leans in turns, is directly affected by suspension geometry and stiffness adjustments. A fine-tuned suspension can drastically minimize body roll, enhancing driver confidence and allowing for faster cornering speeds.
It's also critical to understand the effect of weight and weight distribution. Light-weight components like aluminum control arms can greatly improve responsiveness. Engineers can then fine-tune the distribution of the vehicle's weight to enhance traction during acceleration and braking, optimizing performance in these dynamic situations.
Moreover, suspension tuning in modern cars needs to factor in aerodynamics. Ride height adjustments can affect ground effect and alter downforce, which becomes extremely important for high-speed stability. The challenge lies in achieving a setup that optimizes both aerodynamic efficiency and suspension performance.
A fascinating aspect of high-performance vehicle development is the link between the driver and the suspension. Ohlins telemetry permits real-time feedback from drivers during testing. This feedback can further refine suspension settings to better match driver preferences and input styles. This personalization elevates the overall driving experience, tailoring the suspension to individual drivers for peak performance.
Another recent trend in high-performance suspension technology involves multi-phase dampers. These dampers can adapt their response to various driving conditions and inputs, allowing for a customized driving experience. This advanced technology ensures optimal performance on both the racetrack and everyday roads. The ability to finely tune the suspension to handle a range of inputs is a significant advancement in luxury and high-performance vehicle design.
7 Essential Checks Auto Shops Make When Tuning High-Performance Vehicles in 2024 - Aerodynamic Downforce Measurements via Wind Tunnel Testing
Wind tunnel testing has become indispensable in the quest for enhanced performance in high-performance vehicles, particularly within the worlds of motorsports and luxury car development. These specialized facilities provide a controlled environment for assessing aerodynamic downforce—a crucial factor in stability and speed, especially at higher velocities. The process involves subjecting a vehicle model or a full-scale vehicle to carefully controlled airflow, allowing engineers to meticulously observe and measure the resulting forces. These forces, including downforce and drag, provide insights into how design modifications affect vehicle performance. Modern wind tunnel models are a far cry from the handcrafted wooden or metal versions of the past, benefitting from advanced materials which enable much more refined and precise testing of cutting-edge designs seen in current supercars and new car models.
Auto shops looking to maximize the performance of tuned vehicles in 2024 will find that manipulating variables such as the vehicle's angle, ride height, and the airflow's angle (yaw angle) is crucial for optimizing downforce and overall aerodynamic efficiency. However, achieving accurate data depends not only on manipulating the variables but also on factors such as the quality of airflow within the wind tunnel itself. This attention to detail highlights the need for meticulousness and the critical role wind tunnel testing plays in attaining optimal aerodynamic performance. The insights gained from wind tunnel testing directly translate to improvements in handling, high-speed stability, and overall performance. It underscores the essential connection between achieving both high speed and stability and how modern car design and supercar engineers have taken advantage of this tool.
Wind tunnel testing remains a cornerstone of aerodynamic analysis, particularly when fine-tuning the performance of high-performance vehicles. Organizations like the Subsonic Aerodynamic Testing Association (SATA) and the Committee on Commonized Aerodynamics Automotive Testing Standards (CAATS) have established rigorous methodologies for documenting aerodynamic performance, a practice vital for racing and the development of new models. The evolution of model building techniques over the past few decades has seen a shift from handcrafted models to more sophisticated materials. Modern production vehicles, too, undergo wind tunnel testing under standardized conditions, ensuring their design meets performance targets.
It's fascinating how much influence seemingly small adjustments can have on aerodynamic performance. For example, carefully controlling variables like a car's orientation, ride height, and yaw angle is crucial for accurate downforce measurements. At the same time, the quality of test results relies on factors like the smoothness of the wind tunnel air flow, test protocols followed, and the construction of the tunnel itself. This is all important as we see in modern luxury and supercars the emergence of active aerodynamic elements that adapt to the driving conditions. The ability to adjust elements like wings or air deflectors in real-time allows for optimized downforce during high-speed driving or minimal drag for fuel efficiency.
However, some might assume that a lower drag coefficient always equates to improved aerodynamic performance, which isn't always true. In fact, maximizing downforce sometimes involves increasing drag, a trade-off that prioritizes cornering over top speed. This is an area where the engineering challenges become interesting. For instance, manipulating airflow to create vortices with flaps and spoilers can result in higher downforce without a corresponding increase in drag. It's this ability to fine-tune aerodynamic performance that allows for advanced cornering capabilities in supercars or the cutting edge racing machines we see on track.
It's important to note that wind tunnel testing using scale models can be tricky. Aerodynamics can behave quite differently at smaller scales, often due to changes in the Reynolds number, requiring validation with larger prototypes. In a similar vein, managing the airflow near the surface of the car, what's known as the boundary layer, is critical. This area can have a major impact on both drag and lift. Techniques like vortex generators can influence this area, making the airflow smoother and helping to produce more downforce.
Another aspect of aerodynamic tuning is the impact of what is known as ground effects. The proximity of the vehicle to the road's surface can be utilized to create suction, producing downforce. While the concepts of these systems are well-established in race car designs, they are still making their way into higher-end performance vehicle models. Even small changes in ride height can have a large influence on the airflow patterns and the overall downforce that is generated.
Beyond wind tunnels, computational fluid dynamics (CFD) simulations are being increasingly used to analyze airflow and optimize vehicle design. These computational tools offer a cost-effective way to analyze different design iterations before going to the expense of building physical models and doing physical testing. This, in combination with careful testing and quality control in the testing environments, is essential when tuning performance vehicles in 2024. The reason for this care is that seemingly minor things like the shape of mirrors, grilles, or body kits can significantly affect downforce. Wind tunnel tests can uncover that small aesthetic changes can lead to major changes in how air flows around a vehicle. As a result, tuning needs to consider such effects carefully. These observations highlight how the detailed control and optimization of airflow through creative design and rigorous testing is a continuing priority in the design and development of high-performance vehicles.
7 Essential Checks Auto Shops Make When Tuning High-Performance Vehicles in 2024 - Powertrain Stress Testing Through Rolling Road Dynamometer Runs
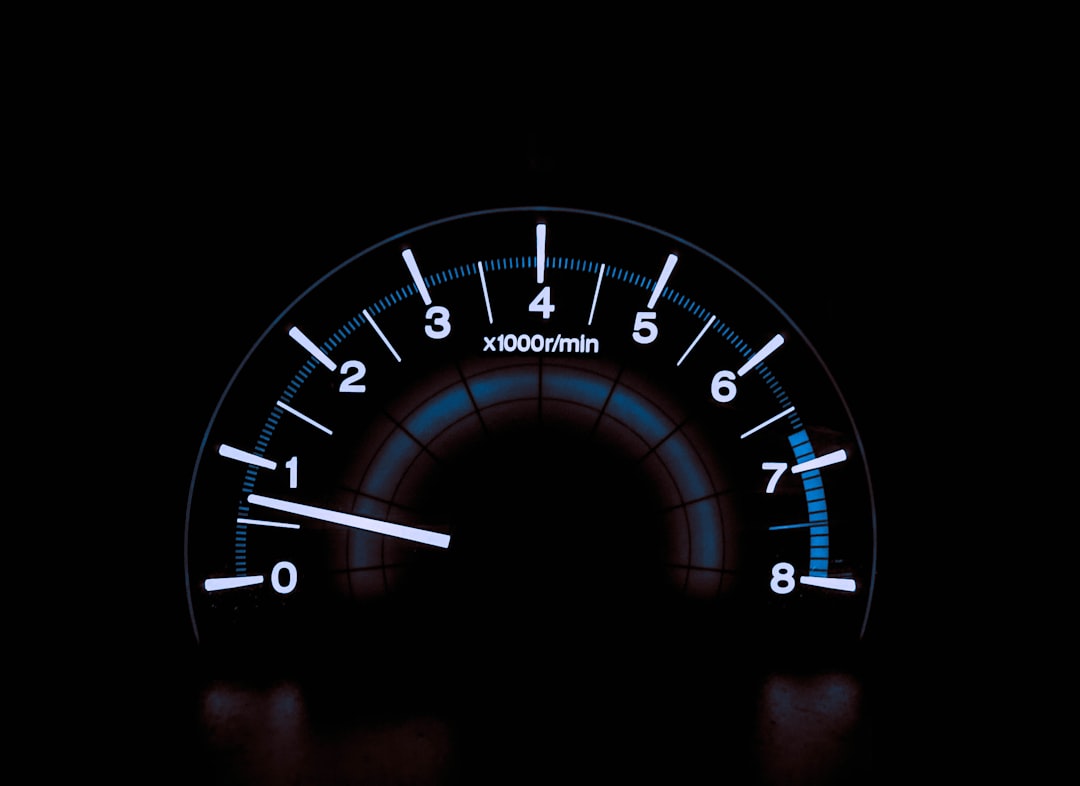
When tuning high-performance vehicles, understanding how the powertrain performs under stress is crucial. Rolling road dynamometers are valuable tools for this, offering a way to simulate real-world driving conditions in a controlled setting. They essentially replicate the forces a vehicle encounters on the road, allowing tuners to precisely gauge engine performance, fuel efficiency, and other key metrics. This type of testing has become even more vital with the evolution of powertrains, as hybrid and electric systems add complexity to the evaluation process.
Modern dynamometers are designed to handle diverse powertrain setups, from traditional engines to cutting-edge electric drivetrains. This flexibility is essential for simulating realistic road load conditions, which is particularly important for calibrating advanced engine control systems. Furthermore, these tests also help in analyzing aspects like noise and vibration that are generated by the powertrain, which are becoming increasingly relevant as vehicle designs become more intricate.
The ability to simulate challenging road scenarios, such as hill climbs and hard acceleration, gives valuable insights into powertrain behavior under duress. This data-driven approach is not just about optimizing performance, it also informs the development of future high-performance powertrains and helps in the overall design of today's sophisticated supercars and luxury vehicle models. The insights gained from these tests are instrumental in achieving optimal performance while also ensuring the long-term reliability of the vehicle's powertrain.
Powertrain stress testing through rolling road dynamometer runs has become a critical tool in evaluating the performance and durability of modern vehicles, especially those tuned for high performance. These dynamometers essentially replicate road conditions, allowing engineers to precisely control factors like speed, load, and incline, mimicking the demands placed on the powertrain in the real world. This level of control helps identify issues that might not be evident in static testing, providing a truer picture of how a car will perform in various situations.
One of the significant benefits of using dynamometers is their ability to subject the powertrain to extreme thermal cycles. This mimics the intense heat generated during high-performance driving, allowing engineers to pinpoint any potential weaknesses in components like the engine and transmission. By observing how these components react to heat, engineers can identify potential failure points before they occur on the track, which is important given that heat-related issues are a frequent problem when dealing with tuned vehicles.
Moreover, dynamometers provide real-time data collection, using advanced instrumentation to record a plethora of parameters, including torque, horsepower, RPM, and environmental conditions. The ability to capture this data while making adjustments to the vehicle's setup enables engineers to observe in real-time how tuning modifications impact the powertrain's performance.
Furthermore, these systems can simulate different altitudes. This is crucial since engine performance changes significantly at higher elevations because of lower air density. This feature is especially helpful for car manufacturers who develop vehicles for global markets that experience a wide range of elevations.
It's also interesting that dynamometers allow engineers to gain insight into the interaction between various powertrain components. They can see, for example, how a turbocharger reacts to increased exhaust flow under load. This knowledge is particularly valuable for high-performance setups, enabling engineers to ensure that all components work in harmony. This is interesting as there is a wide range of turbocharger options available for those who are looking to maximize horsepower for use in diverse environments.
Durability is a crucial factor in dynamometer testing. The ability to run the vehicle under extreme conditions for extended periods allows engineers to accurately simulate the stresses associated with extended high-performance driving. This helps assess whether or not the powertrain can withstand real-world scenarios without premature wear and tear.
Another valuable aspect of modern dynamometers is their adaptability. They can adjust their testing protocols based on performance feedback during the test. This allows engineers to iteratively refine tuning parameters like engine control unit (ECU) maps and transmission settings, leading to faster optimization. This process is becoming increasingly important with the rise in popularity of hybrid and electric powertrains, each with its unique set of challenges and opportunities in the tuning space.
Further, dynamometer tests provide visual representations of power delivery curves. This allows tuners to readily identify areas for improvement across the RPM range, boosting throttle response and overall driveability. This visual perspective helps in ensuring that the power is delivered in a way that is optimal for the vehicle's intended use, whether it's for track racing or street driving.
It’s also worth noting that by using dyno runs and precise powertrain tuning, engineers can optimize both performance and fuel efficiency. For example, subtle changes to air-fuel ratios and ignition timing can lead to considerable improvements in miles per gallon without compromising power output. This is increasingly important in the modern era as customers are now more conscious about fuel efficiency than in years past, as the cost of fuel has also been rising and the need for better fuel mileage becomes increasingly important.
Finally, the design of modern rolling road dynamometers incorporates vehicle dynamics that are present during real-world driving scenarios. Things like variations in wheel slip, load transfer, and tire characteristics are taken into account in these designs, resulting in a holistic understanding of how things like acceleration and braking forces affect performance during driving. This level of detail is particularly important as there are now more vehicles being designed with complex suspension setups that are more challenging to model accurately using traditional methods.
The insights gleaned from dynamometer testing are helping to push the boundaries of vehicle performance and provide data that are instrumental in refining new car models. The data they provide can lead to improvements in everything from acceleration and top speed to fuel economy and driveability. It seems that in the quest to create ever more sophisticated automobiles, the dyno's role will only continue to grow, particularly as engineers grapple with the complex powertrains and new design challenges facing the automotive industry.
7 Essential Checks Auto Shops Make When Tuning High-Performance Vehicles in 2024 - Transmission Response Time Analysis with Launch Control Systems
When tuning high-performance cars, understanding how a vehicle launches is critical, especially when dealing with sophisticated launch control systems. These systems are designed to maximize acceleration from a dead stop, a feat requiring a delicate balance between engine power and tire grip. Each car has an ideal engine speed (RPM) at launch that optimizes acceleration while minimizing strain on the drivetrain components. Sophisticated launch control systems can manage the flow of torque and minimize wheelspin, creating a smoother and faster launch. Many vehicles require activating a specific driving mode, like a "sport" or "track" setting, to engage the launch control function. Furthermore, launch control systems often involve carefully controlling the engine speed prior to launch, often by using an ignition cut to manage engine RPM. The rise of launch control systems is notable in both manual and automatic vehicles, although adapting them for different types of transmissions necessitates distinct approaches. This includes understanding the impact on conventional automatics, continuously variable transmissions (CVTs), and newer dual-clutch setups. It's interesting how traditional automatic transmissions, with their torque converters, are experiencing renewed relevance due to their role within launch control setups. The inclusion of launch control within performance-focused cars shows how these systems have moved beyond simple driver aids to become integral performance-enhancing technologies in a growing array of luxury and supercar designs. This is a clear indicator of how the boundaries between performance and driver assistance are blurring in high-performance automotive engineering.
Launch control systems, a staple in performance vehicles, are increasingly intertwined with transmission technology to optimize acceleration, particularly from a standstill. These systems aim to perfectly match engine output with tire grip, maximizing the launch. Their activation often requires specific driving modes, like 'Sport' or 'Track', highlighting the specialized nature of their function.
Each vehicle has an ideal engine speed (RPM) for launch, a sweet spot that maximizes acceleration while mitigating wear on the transmission. However, this sweet spot can be quite sensitive, so skilled tuning is often required to identify the optimal settings for different vehicle and transmission types. Sophisticated launch control systems intelligently manage torque delivery, minimizing wheelspin and delivering smoother, quicker launches. This refined control helps prevent the kind of rough shifts that can cause unnecessary stress on the drivetrain.
Many systems hold the engine at a pre-determined speed to build boost prior to launch, making use of turbocharger technology for quicker acceleration. This feature often incorporates a secondary rev limiter, sometimes using ignition cut to fine-tune the engine speed during the launch phase. It's worth noting that rev limiting can lead to engine roughness if not perfectly calibrated and can stress components.
The growing popularity of launch control has led to adaptations for both manual and automatic transmissions, showcasing the flexibility of these systems. Automatic vehicles, whether they have conventional automatic, continuously variable, or dual-clutch transmissions, can all benefit from well-tuned launch control. In recent years, there has been a resurgence in the design and application of torque converters for automatics, which helps to improve their performance, specifically when combined with launch control systems.
Launch control, unlike some other advanced driving assistance systems (ADAS), focuses on performance enhancements rather than safety. It represents a deliberate shift towards providing the driver with maximum control during acceleration, and this can change how a car behaves on the track and sometimes on the road. While ADAS is broadly categorized as a safety feature, launch control systems can be considered to be an enhancement to driving performance, a type of technology that is becoming increasingly common in modern luxury vehicles. While we might expect these kinds of systems to be primarily in racing or high-performance vehicles, it is interesting to note that they are increasingly available in vehicles that are targeted towards everyday drivers, perhaps a sign of the trend towards increased performance for a wide variety of automobiles.
7 Essential Checks Auto Shops Make When Tuning High-Performance Vehicles in 2024 - Variable Valve Timing Optimization Through High-Speed Data Logging
Optimizing variable valve timing (VVT) through high-speed data logging has become a key aspect of tuning high-performance vehicles, particularly in the realm of luxury and supercars. The goal is to create a balance between the flow of exhaust gases and the incoming air charge, enhancing performance, especially at higher engine speeds. This precise control over valve timing, which is now achievable with technologies like electronically controlled double-acting Variable Valve Actuation (VVA), significantly impacts power, fuel efficiency, and emissions.
Modern tuning relies on high-speed data logging to capture engine behavior under various conditions. This data is then used to fine-tune valve timing for optimal performance. This approach is vital for pushing the limits of engine performance, as seen in the latest high-performance vehicle designs and some of the most innovative new car models. It’s interesting to note how sophisticated mathematical models and algorithms are now being used to further refine the process of finding the ideal valve timing across different engine speeds and loads, a clear example of the blending of automotive engineering and computational technologies.
While advanced techniques like multi-objective optimization methods are being used to improve the tuning process, a core challenge remains in accurately predicting how adjustments in valve timing will impact various engine parameters. It’s important to understand that these sophisticated tuning processes must carefully balance the conflicting demands of peak performance, fuel economy, and emissions. It’s a delicate balancing act that requires highly skilled technicians and advanced diagnostic tools.
The increasing adoption of these advanced tuning techniques, including high-speed data logging and more intelligent optimization methods, underscores a trend toward maximizing engine potential across a range of conditions. This shift towards precision tuning reflects the increasing demands of luxury car buyers and performance car enthusiasts who are seeking greater performance from their vehicles. It also hints at how the future of engine design may incorporate even more sophisticated tuning methods that can be optimized for real-time driving conditions.
Variable valve timing (VVT) is a fascinating area of engine optimization that's really come into its own in modern luxury and supercars. It allows for incredibly precise control over when the valves open and close, letting the engine adapt to different driving conditions. This kind of adaptability can squeeze out extra performance and improve efficiency, which is a win-win for both horsepower and fuel economy. It's a bit like having an engine that can 'think' about what it needs to do, optimizing itself on the fly.
The ability to finely tune this timing relies heavily on high-speed data logging. Modern tools can record engine parameters at incredibly fast rates, sometimes up to 1000 times per second. This kind of high-resolution data is a game-changer for tuning. Before this, we were often limited to coarser measurements, which meant you'd miss subtleties in how the engine performs. Now, with this precision, we can really identify small changes in the engine that can lead to noticeable improvements.
Some of the most advanced tuning setups can even make real-time adjustments to the VVT based on feedback from a bunch of sensors all over the engine. This adaptive capability is particularly useful when you're driving in situations that change rapidly, like a racing circuit. The engine can adjust its own timing in a split second, which gives a real advantage in competitive driving where the environment changes. It's like the engine is able to 'react' to the demands being placed on it.
Camshaft profiles play a big role here, as the exact shape of the cam lobe influences the way a valve opens and closes. We're seeing systems that can quickly shift between different camshaft profiles to optimize either power or efficiency as needed. This is a pretty clever trick for getting the most out of an engine, allowing it to be both powerful and fuel-efficient depending on the situation.
When you add turbocharging into the mix, things get even more interesting. You can adjust the valve timing based on the turbo boost and engine speed, which can help smoothen out the power delivery. Many turbo engines tend to have a bit of a lag before the turbo kicks in. VVT can help to mitigate this, giving you a quicker response from the turbocharger when you hit the gas. This improved response is a critical factor in high-performance vehicles where every tenth of a second matters. It's intriguing to see how technology like VVT can tackle the performance issues of using turbos.
It's not all roses though; engine temperature can really throw a wrench into things. The ideal VVT settings can shift depending on whether the engine is cold or hot. This means you have to maintain a very precise temperature regulation system, which is often a challenge with tuned engines. If you don't get the temperature just right, the benefits of VVT can be somewhat diminished, meaning there's another element of tuning to consider to get the best results.
One surprising aspect is how VVT has a role to play in improving fuel economy. It may seem like a technology associated with only performance but it's proven to be useful in helping the engine operate more efficiently, reducing emissions at the same time. The ability to optimize valve timing in different parts of the combustion cycle has the effect of reducing fuel consumption without having to necessarily give up power. It's intriguing that one technology could have both performance and fuel efficiency benefits.
Recently, we've seen the incorporation of Computational Fluid Dynamics (CFD) in VVT optimization. This type of engineering tool allows engineers to simulate airflow in the combustion chamber, providing much better insight into how different valve profiles will affect things like combustion efficiency and power output. Essentially, we can test potential changes on a computer before even building them, and we're able to make some predictions of what may happen. This type of approach is quickly gaining popularity and shows how simulations are playing an ever-increasing role in designing future engine components.
Additionally, we've seen an increase in advanced diagnostic tools being developed that allow us to monitor and simulate how VVT systems behave. This is a huge help for both the tuning process and predictive maintenance. We can identify issues before they become a problem, reducing the risk of system failure. These capabilities demonstrate how advancements in monitoring and diagnostics have become integral to tuning and developing more reliable VVT systems.
In the end, many of today's supercars are at the forefront of VVT implementations. These manufacturers are really pushing the boundaries of what's possible, which is beneficial to the entire automotive industry. The lessons learned from developing these high-performance VVT systems have led to advancements in tuning methodologies in more widely available vehicles, highlighting how knowledge developed in the highest performance market has a 'trickle-down' effect onto other areas of car design and tuning. We see these performance benefits and refinements to tuning practices continuing to develop into the future.
More Posts from tunedbyai.io: