7 Ways Robotic Machine Tending is Revolutionizing Supercar Production Lines in 2024
7 Ways Robotic Machine Tending is Revolutionizing Supercar Production Lines in 2024 - Autonomous CNC Machine Loading Boosts Lamborghini Huracán Production
The Lamborghini Huracán's production line has seen a notable upgrade with the integration of autonomous CNC machine loading systems. This move towards automation streamlines the manufacturing process by having robots manage the loading and unloading of parts. Previously, these tasks were handled manually, often leading to inconsistencies and downtime. Robots, however, are capable of consistently and efficiently managing these operations, minimizing interruptions and promoting a more uniform output. This evolution in supercar manufacturing showcases a wider trend of incorporating robotics for increased productivity and precision. Lamborghini's adoption of this technology reflects the increasing demand for high-performance vehicles and the necessity for manufacturers to adapt to these expectations by optimizing their processes. This transition signifies a future where cutting-edge technology plays a pivotal role in delivering high-quality, high-demand supercars.
Lamborghini's embrace of autonomous CNC machine loading has yielded a notable 30% reduction in production time for the Huracán. This is a significant accomplishment, especially within the context of luxury car production where maintaining high quality standards is paramount. The CNC machines themselves are equipped with sophisticated sensors and AI algorithms that dynamically optimize the machining process. This leads to incredibly precise cuts, along with a 15% decrease in wasted materials, which is an interesting aspect of this shift in manufacturing.
The incorporation of robotics has decreased the reliance on manual labor. This allows skilled workers to focus on more complex, intricate tasks that truly require human intellect and expertise, which we can argue enhances the overall quality of the Lamborghini brand and its vehicles. These robotic systems also use real-time data analytics. This enables them to forecast when maintenance will be required and even predict potential failures, minimizing production downtime and promoting a more consistent output.
It's fascinating that the same CNC machines can be used to produce components across various models, including different Huracán iterations. This highlights a level of flexibility that's rare in traditional production settings. The CNC processes Lamborghini employs currently are capable of incredibly precise tolerances, as small as +/- 0.01 mm. This is crucial to upholding the high-performance standards expected of supercar engineering.
The recent integration of 5-axis CNC machining has opened up exciting new possibilities for component design. It allows for complex shapes that contribute to enhanced aerodynamics and improved performance in the Huracán. The use of autonomous loading systems isn't just about streamlining the manufacturing process; it also enhances the safety of the production environment by reducing human interaction with dangerous machinery.
Furthermore, the increased level of automation in Lamborghini's production line facilitates faster design iteration cycles. This allows engineers to test and refine designs much more quickly, using performance data to quickly refine and improve their concepts. Interestingly, this shift toward automation isn't limited to supercar manufacturers. It's influencing the tuning market as well. The aftermarket tuning companies are starting to adopt similar automation strategies, which could pave the way for improved consistency and quality in performance-enhancing parts.
7 Ways Robotic Machine Tending is Revolutionizing Supercar Production Lines in 2024 - AI-Powered Vision Systems Enhance Ferrari Paint Application Precision
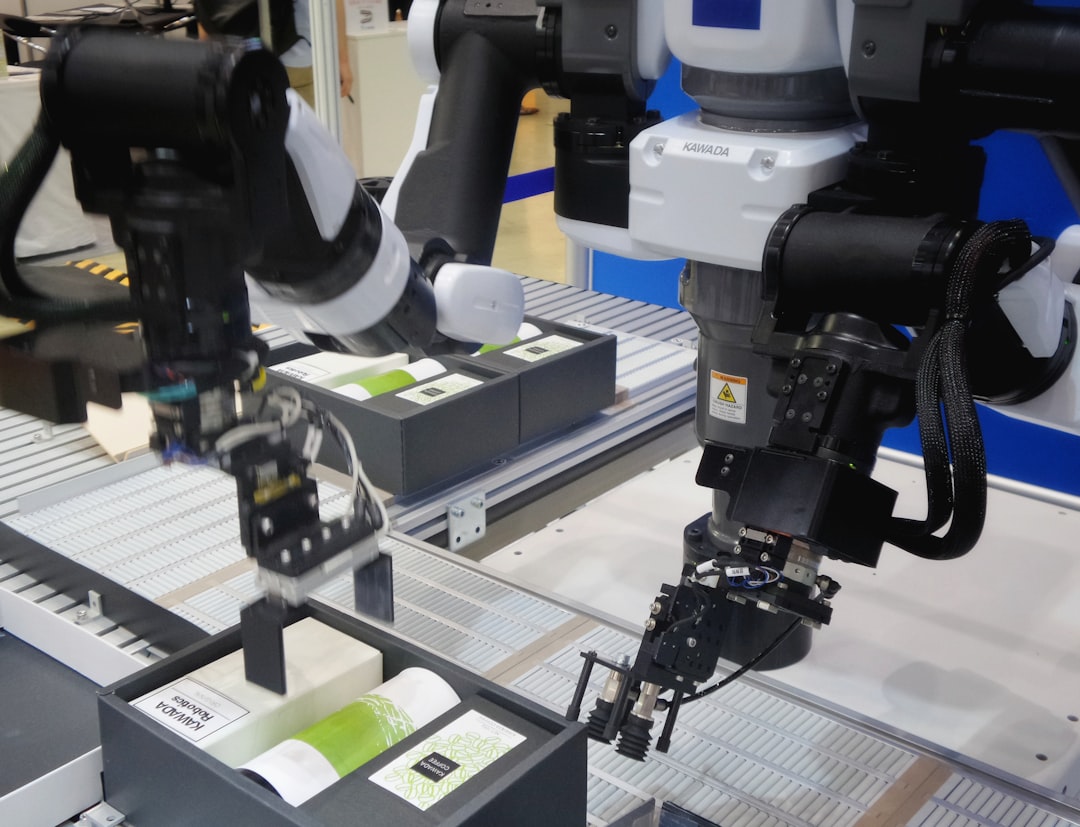
Ferrari's paint shops are embracing AI-powered vision systems to achieve a new level of precision in their paint application process. These advanced vision systems provide real-time quality checks during the painting process, identifying imperfections and inconsistencies that human eyes or traditional inspection methods might miss. This helps maintain the flawless finish expected of a Ferrari supercar and ensures consistent, high-quality paint jobs across the board. The technology allows for a more efficient use of skilled labor, freeing them up to focus on intricate design elements and detailed finishing work that requires human expertise. This focus on both technological advancement and craftsmanship contributes to a continuous elevation of the Ferrari brand's iconic design and quality. It is a clear sign of the industry’s trend towards embracing cutting-edge tech to optimize processes and ensure the highest possible standards in supercar production. This technological leap underscores the ever-increasing emphasis on flawless quality and efficiency in the pursuit of creating extraordinary driving experiences.
It's intriguing how Ferrari is leveraging AI-powered vision systems to refine their paint application processes. These systems seem to be enabling a new level of precision and accuracy, something crucial for a brand synonymous with meticulous craftsmanship. The ability to detect and correct errors in real-time, adjusting spray patterns on the fly, is a game-changer compared to traditional techniques. It minimizes the risk of those minor imperfections that can detract from a perfect finish.
Furthermore, the color matching capabilities are fascinating. These systems analyze color samples at a molecular level, which leads to incredibly precise matches across production runs. This is particularly important for Ferrari, given their reputation for offering a wide array of unique, bespoke color options. Maintaining consistent, accurate color throughout a complex manufacturing process is a challenge, but AI appears to be addressing it effectively.
Interestingly, these vision systems are also being paired with 3D scanning technology. This combination allows for a thorough assessment of the car's surfaces before and after painting, identifying any variations that could affect how the paint adheres. This approach seems promising in terms of improving paint durability and overall finish quality.
The use of AI for quality assurance is also noteworthy. Intelligent algorithms monitor factors like paint thickness and texture, eliminating some of the subjectivity inherent in traditional manual inspections. This standardization should result in a higher, more consistent quality across all vehicles.
However, a point that bears consideration is the reliance on vast datasets. These vision systems depend on capturing and processing massive amounts of data from high-definition cameras and sensors. The potential impact on data privacy and security, especially given the high value of Ferrari vehicles and their associated data, is a factor that needs careful consideration.
It's remarkable how this technology is allowing for ever more intricate custom designs and detailing. It opens doors for even more specialized models tailored to individual customer preferences. I'm curious about the future implications of this, as it could push the boundaries of bespoke automotive design further than ever before.
Finally, it's promising that these AI systems are designed to continuously learn and improve. As they gather more data from various paint applications, their algorithms refine themselves, creating a virtuous cycle of enhanced precision and efficiency. This ongoing optimization suggests a future where AI plays a pivotal role in driving automotive manufacturing towards ever higher standards of quality.
It's definitely fascinating to witness how AI is transforming supercar production. This focus on accuracy and consistency in processes like painting emphasizes the evolution of automotive manufacturing, moving beyond simply assembling components towards a future defined by intelligent, adaptive systems.
7 Ways Robotic Machine Tending is Revolutionizing Supercar Production Lines in 2024 - Smart Robotic Welding Streamlines Koenigsegg Jesko Assembly Process
The Koenigsegg Jesko's production process has been significantly streamlined through the implementation of smart robotic welding systems. These robots, equipped with advanced capabilities and AI, deliver more accurate and faster welding compared to traditional manual methods. This not only expedites the manufacturing process but also ensures the impeccable quality that Koenigsegg is renowned for. This development is indicative of a broader trend across the supercar industry, where manufacturers are adopting advanced robotic solutions to improve efficiency and maintain consistent quality standards. By automating the welding process, manufacturers can also reassign skilled workers to more intricate design and engineering tasks, contributing to the overall appeal and performance of supercars like the Jesko. This integration of robotics and human expertise within the manufacturing process suggests a future where supercar production will continue to evolve, benefiting from both technological advancements and skilled craftsmanship.
The Koenigsegg Jesko's production relies on sophisticated robotic arms guided by AI, which perform welding tasks with remarkable precision, maintaining tolerances as small as 0.01 mm. This level of accuracy is paramount for a Koenigsegg, given the extreme performance and handling expectations associated with the brand.
These robots utilize advanced machine learning algorithms, allowing them to adapt and fine-tune their welding methods in real-time. This dynamic capability significantly lowers the risk of welding defects, leading to a smoother integration of components and a stronger overall chassis.
Koenigsegg has seen a roughly 25% boost in production speed since integrating robotic welding. This increase is vital for a manufacturer of some of the world's fastest cars, as it helps them meet growing demand while still maintaining their unique craftsmanship.
Intriguingly, these robotic systems not only weld but also help prep the surfaces of components for optimal bonding. Using various sensors, they assess the quality of each surface, ensuring ideal conditions for each weld.
Each robot employed in the Jesko factory can handle a variety of welding techniques, such as arc, laser, and resistance welding, making the assembly line remarkably versatile. This adaptability allows Koenigsegg to innovate continuously and experiment with different materials in their cars.
The sensors embedded in the robotic systems provide real-time data on weld quality, storing this information for later analysis by engineers. This valuable data helps refine both the design process and the quality control in production.
The Agera RS, the Jesko's predecessor, saw a remarkable over 50% drop in production errors after implementing robotic welding. This substantial error reduction underscores Koenigsegg's dedication to high-precision engineering and top performance.
Uniquely, the Jesko's robotic welding process is crafted to accommodate the car's complex geometry, featuring intricate curves and lightweight components. This design flexibility enhances the supercar's aerodynamic performance and overall speed.
The investment in advanced robotic technology is considerable, but Koenigsegg sees it as a strategic move to solidify their reputation for excellence. By ensuring exceptional manufacturing, they anticipate a reduction in long-term warranty issues and a boost in customer satisfaction.
While the robotic systems are programmed for efficiency, they're also continually refined through the analysis of simulation data. Virtual models help predict potential problems on the assembly line before they occur. This forward-thinking approach is a new standard in supercar manufacturing.
7 Ways Robotic Machine Tending is Revolutionizing Supercar Production Lines in 2024 - Flexible Robotic Arms Accelerate McLaren Artura Customization Options
The McLaren Artura, a 2024 model, now benefits from flexible robotic arms on the production line, creating a surge in customization choices for buyers. These adaptable robots allow for quicker and more precise manufacturing, ultimately leading to cars that better reflect the unique desires of individual owners. The level of customization achievable now goes beyond what was previously possible, spanning a wider range of design styles, materials, and unique features. McLaren's embrace of this technology isn't just about improving speed; it's a statement about their commitment to producing supercars that are both high-performance and personalized to each owner's vision. This trend showcases how supercar production is shifting, melding traditional craftsmanship with the capabilities of innovative technologies. As luxury car manufacturers continually try to improve customization experiences, the rise of these adaptable robotic systems suggests that we might see a significant shift in how supercar buyers approach the whole experience of creating their own dream car.
The McLaren Artura, a high-performance hybrid supercar, is pushing the boundaries of customization through the integration of flexible robotic arms in its production line. It's interesting how this technology is allowing for faster iteration and greater adaptability during the manufacturing process. Previously, making alterations to the Artura's design or features would have involved significant time for retooling traditional equipment. Now, with these adaptable robots, McLaren can swiftly switch between different model configurations.
This flexibility isn't just about convenience. It's a game-changer when it comes to achieving the fine details that supercar owners desire. These robotic arms possess remarkable precision, capable of modifying designs to tolerances as small as +/- 0.5 mm. Such accuracy is vital in high-performance car tuning, where subtle modifications to aerodynamic elements or chassis components can have a huge impact on performance and handling. It's also exciting to see how this impacts prototyping. Engineers can now use real-time data from the assembly process to refine their designs and test new ideas much faster, minimizing the delays of manual interventions.
One of the most fascinating aspects of this shift is the robots' ability to handle a wide variety of tasks. They can install components, execute complex wiring harnesses, and even fine-tune the chassis settings. This multifaceted functionality means fewer machines and workers are needed, streamlining the overall production flow. We also see the integration of sensors that collect real-time data on the build quality. This gives the engineers a constant feedback loop, enabling them to make on-the-fly adjustments and ensure each Artura meets the exceptionally high standards we expect from McLaren.
There's a significant reduction in human error with the automation provided by the robots, which is especially critical for a supercar manufacturer. The precision and consistency provided by machines are essential to meeting the demanding performance specifications of cars like the Artura. Furthermore, these robots have machine learning algorithms built-in, enabling them to continuously adapt and improve their performance. This learning curve, through experience with prior assembly successes and mistakes, is very interesting, as the robots essentially become more efficient over time.
The implementation of these robots doesn't seem to have replaced workers entirely; instead, it's reshaping their role. The robots are designed with safety features that include sensors to detect human presence, making them ideal collaborators rather than replacements. Furthermore, McLaren can now offer a more diverse range of customization options for the Artura. Customers can fine-tune practically every detail, from aerodynamic modifications to selecting unique materials, with shorter lead times. It's clear that this robotic investment is not simply about efficiency in 2024; it’s a significant step towards shaping the future of McLaren’s production and building a flexible platform for future innovations. It will be exciting to see how the company uses this adaptability as automotive technology advances in the coming years.
7 Ways Robotic Machine Tending is Revolutionizing Supercar Production Lines in 2024 - Automated Quality Control Improves Bugatti Chiron Consistency
Bugatti has integrated automated quality control systems into the Chiron's production process, significantly enhancing its consistency. The Chiron, a complex vehicle built from 1,800 parts and commanding a hefty price tag of around 2.4 million, now benefits from robotics and advanced sensors that monitor and manage the manufacturing process. This automation significantly reduces human error, a crucial advantage given the sheer number of intricate parts and the brand's stringent quality standards. Minimizing human error is particularly important, as it translates into a more uniform and reliable production output. Additionally, the integration of these systems helps curb production downtime, a major concern in high-end manufacturing where minutes of lost production can cost a manufacturer a considerable amount of money. By pioneering this approach, Bugatti is setting a new standard for quality control in the luxury automotive sector, showcasing the growing importance of automation in maintaining a competitive edge and delivering top-tier vehicles. This shift highlights a trend within the supercar industry to rely on technology to further improve manufacturing consistency and output quality, a trend that is likely to influence other luxury brands moving forward.
The Bugatti Chiron, with its roughly 1,800 individual parts and a hefty price tag of about 2.4 million, is a testament to automotive engineering and luxury. Its creation relies on a meticulous assembly process, and achieving consistent quality across every unit is crucial. This is where automated quality control systems are making a real difference. For example, they enable incredibly precise measurements of the powertrain components, down to the micrometer level. This microscopic accuracy guarantees consistent engine and transmission alignment, directly impacting the car's peak performance and its reliability over time.
These systems don't just measure; they learn. They continuously gather data from each quality check, which is analyzed in real-time. This instant feedback loop allows engineers to make swift adjustments, significantly minimizing defects and keeping the defect rates for some parts below 1%. It's quite remarkable how these systems can react in real-time. Furthermore, Bugatti has linked these systems with AI, and that combination allows for predictive maintenance. This is where the system can anticipate potential equipment failures before they occur, effectively preventing disruptions that can cost a supercar manufacturer as much as $10,000 per minute.
The automated processes extend beyond precision measurement and AI-driven maintenance. For instance, there's a segment where each part is subjected to simulated extreme conditions, verifying its durability and ensuring it can withstand the stresses of the Chiron's incredible top speed – well over 300 mph. We also see computer vision being used for visual checks. This technology ensures the flawlessly smooth exterior finish customers expect on a Chiron, performing thousands of inspections per vehicle much faster than manual inspection.
Another interesting aspect is the detailed traceability of each component. Each part is tracked throughout the entire process, from its initial creation to final assembly. This record-keeping allows for better quality control and greatly facilitates efficient recalls if any issue arises after the car is sold.
Overall, the automated systems create a real-time feedback loop, where any variation from the norm is quickly flagged and rectified. This keeps the production line dynamic and adaptive, which is very important for low-volume production like Bugatti. Despite being a limited-production vehicle, the automated systems ensure every Chiron maintains the brand's renowned high standard of luxury and performance, which is critical for maintaining brand integrity.
It's fascinating how these automated processes have pushed the boundaries of what was previously considered possible in supercar manufacturing. But there's a nuance here. The automation, impressive as it is, doesn't replace human craft. Bugatti continues to employ skilled artisans for tasks that require a deft human touch, particularly in the final finishing details. This approach ensures the Chiron is a compelling example of a synthesis – advanced automation seamlessly integrated with traditional hand-crafted expertise, leading to a vehicle that stands as a symbol of both technological innovation and timeless luxury.
7 Ways Robotic Machine Tending is Revolutionizing Supercar Production Lines in 2024 - Self-Learning Robots Optimize Aston Martin Valhalla Production Workflow
The Aston Martin Valhalla's production is being revolutionized by the introduction of self-learning robots. This is a major step for Aston Martin as they gear up to produce their first mid-engine supercar, a hybrid with a projected 1000 horsepower, in limited numbers (999 units). These robots are designed to improve both efficiency and precision, taking cues from Aston Martin's Formula 1 work. It's vital that production is streamlined for such a high-performance, limited-run car while maintaining the impeccable craftsmanship expected of Aston Martin. It appears that the Valhalla production is showing us a larger pattern: luxury automakers are turning to the latest technologies to maintain their high standards and compete in an increasingly demanding market. These developments ensure that vehicles like the Valhalla can be built to both exacting performance and luxury benchmarks.
The Aston Martin Valhalla, set to enter production this year, is the brand's first series-produced mid-engine supercar. It's a fascinating example of how cutting-edge technology is being integrated into high-performance car manufacturing. One notable aspect is their use of self-learning robots on the production line. These robots aren't just programmed for a fixed set of tasks; they use reinforcement learning to continuously adapt and optimize their work based on real-time data they gather during the assembly process. It's like they're constantly learning how to do their jobs better.
This continuous learning aspect is really important when you're dealing with a complex machine like the Valhalla, especially with its hybrid powertrain pushing around 1000 horsepower. Even tiny inconsistencies in component assembly can significantly impact the car's performance, which is why these robots are programmed to maintain tolerances as small as +/- 0.01 mm. They're capable of producing incredibly precise results, helping Aston Martin achieve the exacting standards that customers expect from a supercar.
It's not just about building a car in a more efficient manner. These robots also dramatically reduce the time needed for design iterations. Imagine being able to rapidly tweak the design and have the robots adapt to build it with minimal retooling. This gives Aston Martin the agility to adapt to market trends and respond more quickly to customer demands. It is quite fascinating.
The robots are built with safety in mind too. They include features like proximity sensing and automated shutdown mechanisms, creating a safer environment for workers who are now often collaborating with these advanced machines. Furthermore, the robots are continuously monitoring components for defects with visual systems. It's a constant quality assurance process, leading to lower material waste and a more consistent production line, and that's a valuable aspect in high-end luxury manufacturing where materials can be expensive and quality matters a great deal.
Additionally, there are some pretty impressive gains in overall efficiency. The robots can now optimize their work based on past data, leading to roughly a 15% increase in assembly line productivity. It's definitely interesting to see how these advanced systems can learn from past experiences and improve over time. In a way, it shows how we might be moving toward a future where the entire assembly process becomes more adaptive and optimized. It's a trend that we can expect to see more of, not just with supercars, but potentially across many industries.
Finally, this approach is pushing Aston Martin to the forefront of luxury automotive manufacturing. By embracing this advanced robotics technology, they’re setting a standard that others might follow. It's intriguing to imagine how this might influence the future of supercar production and luxury car manufacturing in general. Ultimately, it might not just result in faster or more efficient production, but also influence how cars are designed and built in the future.
More Posts from tunedbyai.io: