AI Designed Tuning What Auto Parts Stores Mean for Tomorrow
AI Designed Tuning What Auto Parts Stores Mean for Tomorrow - AI as a design assistant for bespoke automotive components
AI's integration into bespoke automotive design, as of mid-2025, has notably evolved. No longer just a conceptual tool, it actively assists in creating specialized components for high-performance and luxury vehicles. Leveraging advanced algorithms and machine learning, designers can rapidly iterate on forms and explore material combinations once considered impractical, allowing for incredibly intricate and precise detailing. This technological partnership undeniably accelerates development and refines component precision, potentially elevating both the visual impact and the functional prowess of modern supercars. However, while AI undeniably expands the scope of unique, high-performance parts, it also introduces questions: does this algorithmic assistance sometimes streamline creativity into predictable patterns, rather than fostering true artistic leaps? Despite such considerations, this evolution significantly challenges traditional manufacturing limits and redefines the very essence of automotive design, pushing personalization towards a new standard in car craftsmanship and tuning.
* The sheer computational grunt of AI in generative design is something to watch. It allows for rapid iteration through countless structural forms, identifying component geometries that maximize structural efficiency while shedding unnecessary mass. This often results in shapes that are strikingly unconventional, forms a human designer might never intuitively sketch, pushing the boundaries of what a component can look like while meeting performance targets. One has to wonder, however, how often these purely optimized forms integrate aesthetically or practically into broader vehicle designs without further human refinement.
* Beyond just shape, AI is proving adept at modeling material behavior down to a microscopic level. For specialized parts, particularly those subject to immense forces, like a hypercar's braking assembly, this means designing multi-material structures at a far more granular level than before. The promise is the ability to 'engineer' entirely new composites virtually, tailor-made for specific stress profiles, though the real-world validation of these novel material compositions remains a rigorous task.
* The speed at which AI can now run computational fluid dynamics (CFD) simulations is transforming aerodynamic development. Custom bodywork elements can be iterated and analyzed for airflow characteristics – pressure zones, turbulence, lift, and drag – almost on the fly. This capability is reducing the dependency on costly and time-consuming physical wind tunnel tests for initial design validation, although full-scale empirical validation remains a critical step for final performance claims.
* When paired with additive manufacturing techniques, AI’s design capabilities become even more intriguing. It can craft incredibly intricate internal lattice structures and complex geometries within components, optimizing for strength with minimal material use. These are forms simply impossible to achieve with traditional casting or machining, allowing for significant weight reductions in performance parts, though ensuring repeatable structural integrity across manufactured batches of such intricate parts presents its own set of engineering challenges.
* Perhaps one of the more fascinating applications is AI’s ability to personalize components for the human element. It can factor in a driver's unique biometrics and even their preferred driving dynamics to subtly reshape interior touchpoints or control interfaces for optimal ergonomic fit. The balancing act then becomes integrating these personalized forms seamlessly within the existing aesthetic and, crucially, the rigorous safety architecture of a vehicle, which demands careful human oversight.
AI Designed Tuning What Auto Parts Stores Mean for Tomorrow - Visual innovations driven by machine learning for vehicle profiles
Machine learning is fundamentally altering how vehicle silhouettes are conceived, ushering in a new era of visual innovation for automotive profiles. Designers, leveraging these advanced digital capabilities, are now exploring a spectrum of radically different body shapes and unprecedented surface intricacies, pushing beyond conventional notions of beauty and form. This rapid digital exploration allows for a degree of individual aesthetic tailoring that was once unimaginable, ensuring custom exterior elements are not merely optimized for function but also possess a compelling visual identity.
Yet, a pertinent question arises regarding whether such algorithmic approaches might inadvertently steer design towards a predictable visual uniformity. The constant pursuit of an 'ideal' form, guided by code, could potentially diminish the idiosyncratic artistic expression that historically imbues each car with a truly distinct character. As these tools continue to mature, the central challenge remains: fostering genuine visual diversity and stylistic boldness, preventing a future where algorithmic refinement triumphs over raw, unmistakable automotive artistry.
We're observing a fascinating trend where computational models are being trained on vast repositories of automotive imagery, not just to mimic but to extract what might be termed the fundamental "grammar" of vehicle aesthetics. This allows them to generate entirely fresh exterior profiles, sometimes tailored to reinforce an existing marque's visual identity, other times exploring genuinely uncharted stylistic territories. One must consider, however, whether such a data-driven approach inherently gravitates towards an aggregation of past successes, rather than sparking truly discontinuous design breakthroughs.
The capacity for advanced learning algorithms to analyze emotional responses and public sentiment regarding visual stimuli is translating into predictive models for car aesthetics. Designers are reportedly using these insights to refine elements like front fascia geometry or roofline flow, ostensibly with a higher degree of certainty about their eventual acceptance by particular demographics. Yet, the question lingers: is this simply an elaborate statistical model for popularity, potentially leading to designs optimized for broad, perhaps unchallenging, appeal, rather than fostering bold, category-defining statements?
An intriguing development involves the convergence of machine learning with new material science, particularly programmable surfaces and flexible body panels. This allows for vehicle profiles that are not static, but can subtly alter their appearance – perhaps a shift in surface texture, or a dynamic interplay of light refraction. The vision is for personalized visual themes or even a vehicle visually communicating its 'state' or driving mode. The engineering hurdles for real-world durability, regulatory compliance, and maintaining aesthetic coherence across such transformations remain significant considerations.
We're witnessing algorithms capable of performing a form of 'cross-modal translation' in design. By ingesting vast datasets not limited to automotive visuals but extending to fields like architecture, high fashion, or even biomorphic forms, these systems can extract abstract design principles and project them onto vehicle profiles. The output can indeed be surprising, pushing beyond conventional automotive archetypes. However, one might ask whether such synthesis truly generates a novel, coherent design language, or if it sometimes risks producing an amalgamation of disparate influences without a unified artistic vision.
The evolution of automotive lighting is no longer just about illumination; AI is now fundamentally shaping how integrated light elements contribute to a vehicle's perceived profile. We see complex, programmable light signatures emerging – dynamic patterns and animated sequences that actively sculpt the vehicle's contours and alter its visual presence, even after sunset. This is certainly redefining visual character beyond static form. From an engineering standpoint, ensuring these dynamic displays meet stringent safety and regulatory requirements, avoiding potential distraction for other road users, presents an ongoing and non-trivial challenge.
AI Designed Tuning What Auto Parts Stores Mean for Tomorrow - The intersection of human craftsmanship and computational engineering in tuning
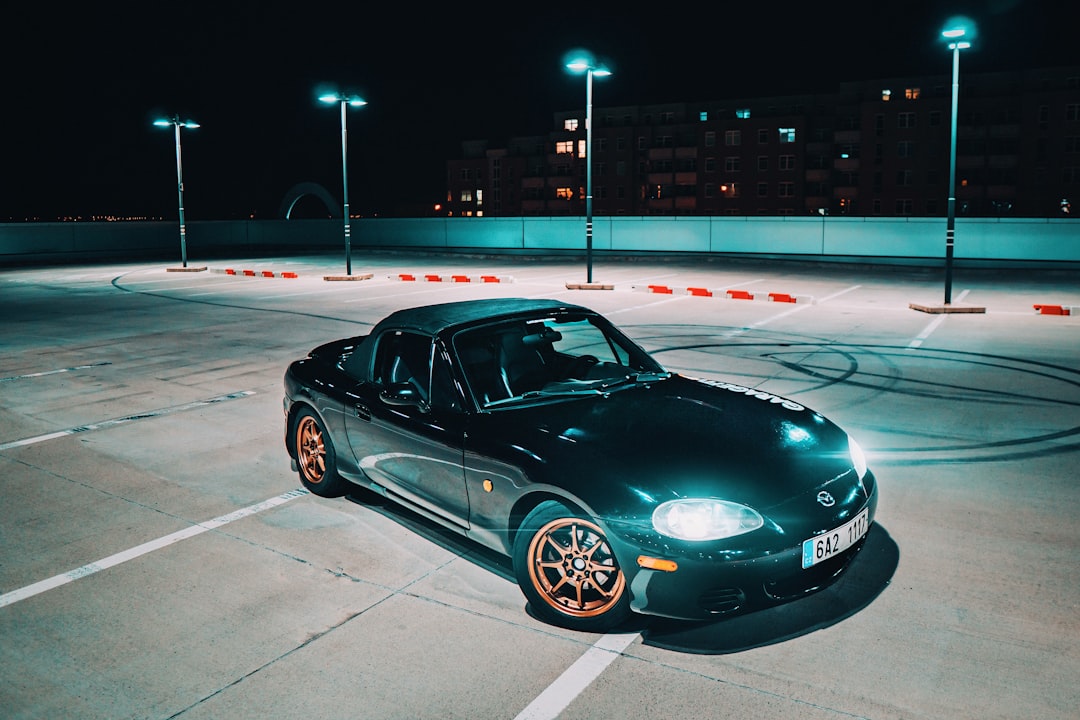
The conversation around computational influence in automotive has often highlighted its role in creating bespoke components and novel visual identities. However, by mid-2025, a more intricate challenge has emerged, particularly within the specialized domain of vehicle tuning. This is where the deep-seated artistry and experiential knowledge of human master tuners meet sophisticated computational engineering, not just in designing parts, but in the nuanced calibration of an entire machine. Consider the delicate balance: algorithms can now precisely refine power delivery curves, optimize suspension kinematics for specific track conditions, or dynamically adjust aerodynamic surfaces for ultimate efficiency. Yet, this algorithmic pursuit of statistical peak performance inevitably raises a crucial question: does such optimization risk stripping away the unique 'feel' and subjective character that a master tuner, through years of hands-on intuition and a personal understanding of the driver, traditionally imbues? The evolving landscape for performance vehicles suggests that true distinction will increasingly depend on finding the sweet spot where technological precision elevates, rather than dilutes, the irreplaceable human craft in perfecting a vehicle.
The paradigm of tuning is evolving beyond static, pre-set configurations. We are witnessing AI systems moving into a dynamic, real-time advisory role within the vehicle itself. These systems can ingest continuous streams of data—everything from a driver's physiological responses to their steering inputs and brake pressures—and, in theory, suggest immediate, granular adjustments to parameters like active damping or power delivery profiles. The aim is to optimize vehicle response directly to the moment, creating a purportedly seamless symbiosis between the human operator and the machine. However, the precise calibration of such systems to avoid 'over-optimization' that might alienate a driver's intuitive feel remains a complex challenge, raising questions about control authority and natural driving rhythm.
The abstract realm of digital vehicle twins is being brought closer to tactile reality through advanced haptic interfaces. Engineers and tuners are now employing specialized feedback devices that translate the simulated forces and deflections of a virtual component—be it a redesigned suspension arm or an altered aerodynamic surface—into physical sensations. This allows a human to 'feel' the virtual car's dynamic response or the resistance of an airflow pattern without ever milling a physical prototype. While undeniably accelerating early-stage conceptualization by providing a more intuitive sense of impact, one might ponder if this haptic bridge truly captures the full spectrum of real-world road dynamics, or if it provides a curated, perhaps overly simplified, sensory representation.
Interestingly, the computational approach to material selection is beginning to transcend purely quantifiable performance metrics. Algorithms are now being trained on extensive datasets that catalog not just the raw strength or thermal conductivity of materials, but also their inherent aesthetic qualities, their amenability to traditional artisanal processes like hand-polishing or detailed engraving, and even their projected long-term patina. This enables the AI to propose specific alloys or composites for bespoke components, ostensibly aligning functional requirements with a client's desire for a particular visual aging characteristic or a handcrafted feel. Yet, the question of whether an algorithm can genuinely grasp the subjective nuances of 'aesthetic finish' or the intangible allure of a specific patina, rather than merely correlating visual data, is a compelling one.
There's a fascinating trend toward AI systems being tutored, in a sense, by the historical artifacts of automotive craftsmanship. By analyzing detailed 3D scans and production blueprints of iconic, often hand-finished, bespoke components from previous eras, algorithms are learning to identify and subtly weave in the "signature" or "invisible hand" aesthetic nuances of master builders. The ambition here is to produce novel designs that simultaneously benefit from computational optimization while carrying an echo of a celebrated artistic legacy. One must critically evaluate, however, if such algorithmic assimilation truly captures the intuitive genius and spontaneous imperfections that define human artistry, or if it merely creates a statistically derived pastiche of established stylistic patterns.
The traditional tuning bay is transforming into a highly immersive, mixed-reality workspace. Future-forward facilities are incorporating interactive, gesture-controlled interfaces that project detailed holographic representations of vehicle components directly into the physical space. This allows a tuner to intuitively "manipulate" virtual parts in three dimensions—twisting a holographic turbocharger or flexing a projected suspension strut—while an integrated AI concurrently processes these changes, providing instant, real-time feedback on potential performance implications or suggesting optimized alternative iterations. This innovative merging of the physical and digital offers unprecedented collaborative potential, though managing the sheer volume of interactive data and ensuring precise, ergonomic interaction within such visually rich environments presents its own set of ongoing engineering challenges.
More Posts from tunedbyai.io: