AI Reveals The Inner Workings Of High Performance Vehicles
AI Reveals The Inner Workings Of High Performance Vehicles - Interpreting Complex Vehicle Telemetry for New Insights
The way we glean knowledge from vehicle telemetry has notably shifted by mid-2025. Beyond the conventional metrics of speed and engine RPM, the cutting edge now involves dissecting vast, intricate datasets to uncover previously hidden behaviors and potentials. Advanced AI isn't just crunching numbers; it's identifying subtle, interlinked patterns across thousands of sensors, from microscopic chassis flex under extreme cornering to the precise airflow dynamics around bespoke bodywork. This deeper dive is delivering insights that go beyond simple optimization, influencing the fundamental architectural choices for tomorrow's supercars and bespoke luxury machines. Yet, with this deluge of information comes the critical task of distinguishing genuine breakthroughs from mere data artifacts, ensuring that algorithmic 'discoveries' truly enhance the driving experience and vehicle longevity, rather than just optimizing for a digital benchmark.
It's genuinely fascinating how granular data from vehicle operation can challenge our existing assumptions about design and performance.
One striking realization from digging into high-frequency pressure sensor data, captured at rates exceeding 2000 samples per second, is its unparalleled ability to pinpoint precisely where airflow detaches from a car's body, particularly on high-performance machines. While computational fluid dynamics (CFD) provides an excellent starting point, this real-world telemetry unveils subtle inefficiencies—sometimes leading to insights for up to a 3% improvement in drag or downforce—that even the most sophisticated simulations struggle to capture fully. This level of fidelity means we can truly fine-tune elements like vortex generators or undertray diffusers, ensuring every square millimeter contributes to optimal aerodynamic efficiency.
Similarly, examining multi-axis accelerometer and lidar-based ride height measurements offers a previously unachievable view into a chassis's dynamic behavior. We can now discern transient flex and body roll oscillations with microsecond precision, moving beyond the laborious, iterative physical tests that once defined suspension tuning. This allows engineers to dial in spring rates and damper valving with astonishing accuracy—think within 0.01 Ns/mm—for very specific driving conditions, whether optimizing for a particular race circuit or crafting an exceptionally plush luxury ride. Such detailed feedback is clearly foundational for truly adaptive suspension systems, yet one wonders if the sheer volume of data might sometimes obscure simple mechanical truths.
A deeper dive into high-resolution exhaust gas temperature and individual cylinder pressure profiles provides a virtual window into the combustion process itself. This real-time, per-cylinder analysis of combustion efficiency helps to pinpoint the precise optimal ignition timing and fuel delivery, potentially leading to a modest, yet significant, reduction in fuel consumption, perhaps around 1.5%. Critically, this data stream offers the ability to foresee pre-detonation events before any audible engine knock occurs, serving as an invaluable safeguard for highly stressed powertrains and potentially extending their operational life. The challenge, of course, is converting this diagnostic power into active, real-time control without introducing undue complexity.
Integrating strain gauge telemetry at key structural points, like chassis hardpoints or wheel hubs, has demonstrated an impressive capacity to forewarn of material fatigue. By constantly monitoring subtle micro-deformations, these systems can project potential structural failures hundreds of operating hours before they would physically manifest. This predictive capability shifts maintenance from reactive to truly proactive and provides invaluable feedback for future design iterations, allowing engineers to target material reinforcement with precision. It represents a significant step towards engineering vehicles for extreme longevity and safety, though the robustness of such sensing systems in harsh operational environments remains a perpetual engineering concern.
Finally, venturing beyond purely mechanical metrics, some of the most intriguing insights emerge from studying driver interaction. Advanced eye-tracking combined with steering wheel torque telemetry isn't just about lap times; it starts to paint a picture of a driver's cognitive workload and their unique input preferences. This understanding opens the door for future vehicles—particularly in the luxury segment—to dynamically adjust characteristics like steering assist, throttle mapping, or even how infotainment systems present information. The aim is a personalized and less fatiguing driving experience that goes far beyond simple 'comfort' or 'sport' modes. The ethical implications and the fine line between helpful personalization and intrusive over-automation are areas that warrant continuous consideration.
AI Reveals The Inner Workings Of High Performance Vehicles - Designing for Efficiency The AI Assisted Evolution
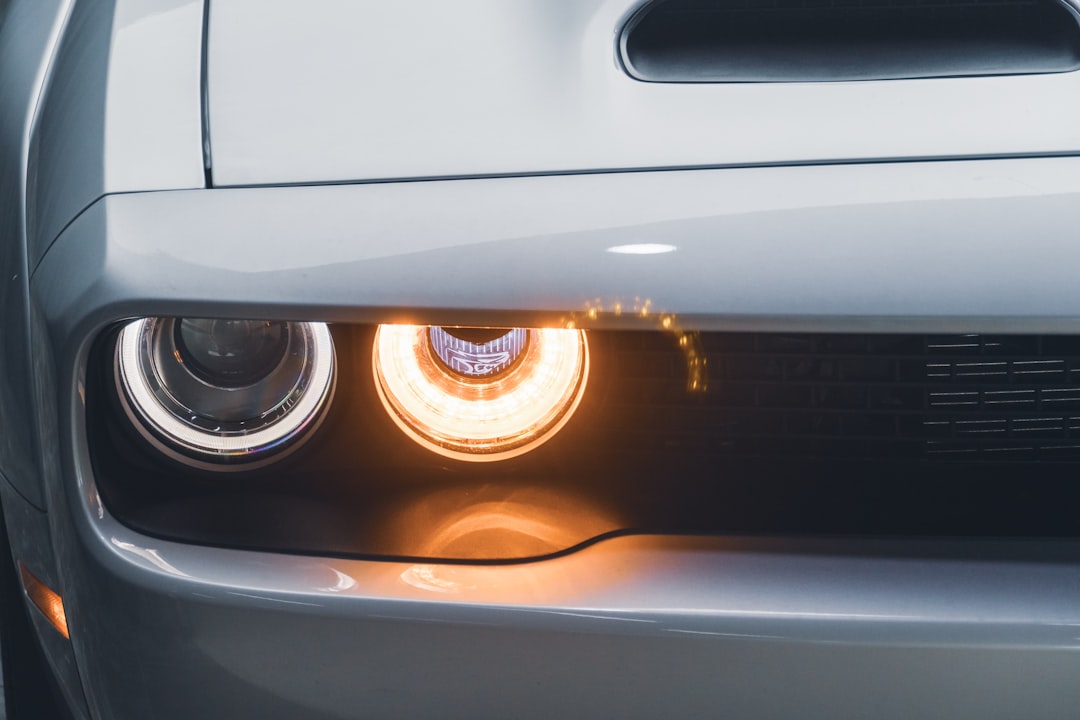
As of mid-2025, the conversation around high-performance vehicle design has significantly evolved, moving beyond mere analysis of operational data to a proactive embrace of AI in the very conception of new models. Where AI previously served primarily to interpret the complex telemetry of existing machines, revealing their subtle behaviors and hidden potentials, its role now extends to shaping fundamental architectural choices. This paradigm shift means AI isn't just about understanding what a vehicle *does*, but increasingly, what it *could be*. The focus now is on how AI facilitates genuinely novel design pathways, allowing engineers to explore an expansive, often counter-intuitive, space of forms and structures, yet the challenge remains in ensuring these AI-driven designs maintain a human-centric driving essence.
It’s genuinely intriguing to witness the shift in how vehicles are conceived, particularly when artificial intelligence steps in to reshape the design process for efficiency.
One striking development is the use of multi-objective generative design, where AI engineers components that are not only significantly lighter—in some cases, 15-20% less mass—but also notably stiffer, perhaps 5-10% more rigid than what was achievable through conventional means. This paradigm shift in optimizing material placement, often down to a microscopic scale, genuinely redefines how we approach the foundational structures of high-performance and luxury vehicles.
Another intriguing area is the way advanced AI models are conceptualizing entirely new thermal management routes for demanding battery systems and powertrains. This has led to designs demonstrating a significant decrease in coolant volume and pumping power, potentially by as much as 25%. From an engineering standpoint, this directly impacts electric vehicle endurance and allows internal combustion engines to sustain their maximum power output without thermal compromise, a genuine step forward.
Furthermore, by harnessing extremely detailed simulations that delve into material properties at a near-atomic scale, AI algorithms are significantly speeding up the development and refinement of custom alloy formulations and intricate composite structures. The result? New materials exhibiting properties like a 30% improvement in strength-to-weight characteristics or a 15% boost in thermal conductivity. This empowers us to specify materials for very particular vehicle components with a level of bespoke tailoring that's genuinely remarkable.
It's also intriguing to see how integrated multi-objective optimization is now at play, where AI concurrently designs the vehicle's exterior surfaces alongside its internal airflow pathways. The goal is two-fold: achieving optimal aerodynamic efficiency while also significantly reducing cabin wind noise, sometimes by as much as 5 dB. This holistic perspective ensures that a luxury-level acoustic environment is maintained without any detrimental impact on the vehicle's dynamic performance—a balancing act that was once extremely challenging.
And lastly, a truly forward-thinking application sees AI analyzing actual manufacturing process data directly during the design phase. This allows it to predict and then help mitigate potential flaws in highly complex components—like a new monocoque chassis or custom-forged wheels—before a single physical part is even produced. Such a preemptive strategy not only leads to a tangible reduction in material waste, potentially by 10%, but also significantly enhances the overall structural integrity of these vital vehicle parts. This predictive power is certainly a leap forward, though the reliance on accurate historical manufacturing data becomes a crucial underpinning.
AI Reveals The Inner Workings Of High Performance Vehicles - Optimizing Drivetrain Responses and Chassis Balance
The dynamic interplay between a vehicle's engine output and its response to the road is being continually reshaped by artificial intelligence. Today, advanced computational models are guiding the nuanced calibration of how motive force is managed and how the vehicle's structure reacts, leading to an incredibly adaptive and versatile machine. This deep refinement isn't solely about achieving peak performance; it's also about sculpting a driving experience that feels instinctively intuitive across diverse conditions, whether navigating demanding race circuits or traversing everyday commutes. By continuously processing an immense flow of operational data, these integrated systems can anticipate both environmental shifts and a driver’s preferences, dynamically adjusting power delivery and chassis demeanor to maintain both acute command and passenger comfort. This intelligent foresight also aids in preemptively preserving vital components while maintaining the crucial balance between agile responsiveness and composed stability. Nevertheless, the ongoing task for vehicle development remains ensuring that these technologically advanced layers enhance, rather than diminish, the profound connection and genuine enjoyment a driver seeks from a finely tuned automobile.
Our observations confirm that advanced AI, rather than reacting, often anticipates optimal gear changes. By scrutinizing real-time data from accelerator pedal inputs and nuanced steering adjustments, the system selects the next ratio even before a driver consciously commits. This pre-emptive action translates into genuinely imperceptible power delivery in high-end touring machines and significantly sharper, more precise shifts for outright performance, ensuring torque arrives exactly when the chassis demands it. One might even question if such perfect synchronization, while technically superior, starts to remove some of the tactile engagement typically valued by purists.
The dynamic behavior of electronic limited-slip differentials is increasingly dictated by AI algorithms. These systems continuously recalibrate the differential's locking bias—several hundred times per second—drawing on granular data points like individual tire friction coefficients, real-time vertical loads on each corner, and the precise rotational velocity of every wheel. This level of granular control over torque bias across the drive axle profoundly refines a vehicle's ability to maintain traction through a corner and improve its initial turn-in response, seemingly extracting grip beyond conventional mechanical expectations.
Beyond simple deployment, integrated AI routines now orchestrate active aerodynamic surfaces with acute awareness of powertrain output fluctuations and the dynamic load transfers within the chassis. This complex ballet ensures that elements such as variable-angle spoilers or adjustable undertrays adopt their most effective configuration without introducing momentary instability during aggressive high-speed maneuvers. The outcome is a marked improvement in stability during rapid changes of direction or heavy braking at speed, optimizing high-speed cornering equilibrium.
Intriguing developments in active suspension see AI systems leveraging high-definition road-scanning lidar and multi-spectrum camera input to anticipate changes in road surface texture and undulations microseconds before the wheels encounter them. This allows for an extraordinary pre-emptive adaptation of individual damper characteristics and, where applicable, dynamic ride height, effectively 'ironing out' irregularities. The net effect is an almost seamless negotiation of obstacles, preserving the chassis's composure and significantly elevating both occupant comfort and the vehicle's stability during spirited driving.
Expanding beyond its more common role in cornering, AI-managed drivetrain systems are now observed to employ fractional torque vectoring at each wheel to subtly counteract minor external disturbances like subtle road camber changes or unexpected crosswinds. This largely imperceptible, continuous modulation significantly bolsters straight-line stability, contributing to a tangible reduction in driver exertion over extended periods by autonomously preserving the intended vehicle trajectory through precise, minute adjustments to power delivery.
AI Reveals The Inner Workings Of High Performance Vehicles - Beyond the Test Track Predictive Performance Analysis
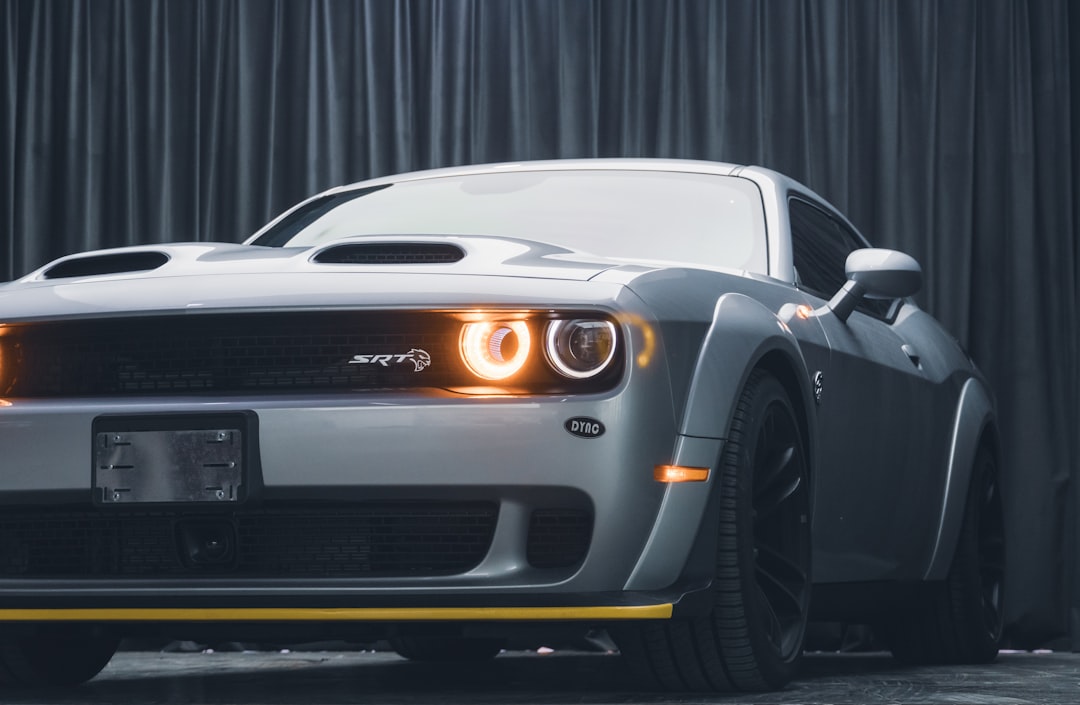
Beyond the Test Track Predictive Performance Analysis represents a significant evolution in how high-performance vehicles are envisioned and perfected. By mid-2025, the focus has shifted dramatically from merely interpreting the performance of existing prototypes to rigorously forecasting how new designs will behave across an astonishing breadth of future scenarios—all within a purely digital environment. This isn't just about faster simulations; it's about AI models building intricate 'digital twins' that predict the nuanced interplay of every system, from aerodynamics to powertrain response, chassis dynamics, and even material degradation under highly specific, anticipated conditions. The true innovation lies in the capacity to iterate and optimize complex designs millions of times over in a virtual space, pinpointing potential issues or unforeseen performance gains long before a single physical component is ever crafted. While this accelerates development and reduces costs, the perennial challenge remains ensuring these algorithmically optimized machines retain the tangible feel and intuitive connection that truly define an exceptional driving experience, rather than becoming abstract equations of speed.
It's quite intriguing how current AI models can project the long-term durability of vehicle components. By running countless virtual simulations across diverse operational conditions, they develop a detailed understanding of how materials might degrade over years, well beyond simple stress-point alerts. This computational foresight is enabling engineers to make informed choices about material and structural geometry during the very earliest design stages, even before a single physical part is manufactured. One still has to wonder about the "edge cases" not covered in the simulated data.
A somewhat more subtle application involves AI crafting individualized vehicle calibrations for new owners, even before the car leaves the factory. Drawing from broad simulated driving datasets and initial driver preference inputs, these systems can refine characteristics like steering feel, accelerator response, and suspension behavior. The goal is an immediately tailored driving experience, though the extent to which such algorithms truly capture individual nuance, rather than just statistical averages, warrants ongoing investigation.
Perhaps one of the most direct benefits for the tuning world lies in AI-powered simulation environments. These platforms can now forecast the precise impact of virtual engine software adjustments or even subtle aerodynamic revisions on performance, thermal stability, and long-term component wear. This analytical capability potentially bypasses the extensive physical testing traditionally required, allowing for rapid iteration through a vast number of hypothetical configurations. The critical question, however, remains the fidelity of these simulations when encountering unforeseen real-world interactions.
On the safety front, predictive AI models are now delving into crash dynamics with remarkable granularity. They can simulate how new composite materials respond at extremely short timescales during an impact, identifying microscopic crack formations and the nuanced ways energy is absorbed that even sophisticated finite element analysis or physical crash tests might not fully reveal. This level of insight promises significant improvements in the passive safety of vehicle structures, though the sheer complexity involved in such precise modeling suggests continuous validation will be necessary.
A shift toward more intelligent vehicle maintenance is also evident. Advanced AI systems are developing a unique 'wear signature' for individual vehicles, forecasting ideal service timings for various components. This moves beyond conventional, fixed mileage or time-based schedules, basing recommendations instead on actual operational patterns, environmental stressors, and subtle performance shifts. While promising more efficient upkeep and extended component life, the reliability of these 'fingerprints' hinges on the quality and continuity of the sensor data, a known challenge in real-world deployments.
More Posts from tunedbyai.io: