Crankshaft Position Sensor Failures 7 Key Symptoms to Watch For in 2024
Crankshaft Position Sensor Failures 7 Key Symptoms to Watch For in 2024 - Engine Stalling During Acceleration
Experiencing a stalled engine while accelerating can sometimes point to a problem with the crankshaft position sensor. This sensor plays a critical role in the engine's timing, ensuring the proper delivery of fuel. When it malfunctions, it can disrupt this timing, leading to a rough idle, misfires, and a noticeable decline in engine power. Drivers might find that the engine unexpectedly cuts out, specifically when trying to speed up, creating a potentially hazardous situation and highlighting efficiency concerns. The interconnectedness of these issues means it's crucial to promptly address any indications of sensor malfunction to prevent further complications. Detecting these problems early on, using regular diagnostics, can help avoid more significant issues down the line.
One observation we've made is that a failing crankshaft position sensor can sometimes lead to the engine stalling specifically during acceleration. This is likely because the increased load and demand placed on the engine during acceleration amplifies any inaccuracies in the sensor's signal. The engine control unit (ECU) relies on the sensor to synchronize crucial aspects of the engine like fuel injection and ignition timing, and a flawed signal can easily disrupt these functions during periods of higher power demand.
It's intriguing that the increased load that stalls the engine during acceleration can also function as a trigger of sorts, forcing a condition which allows more diagnostics to be generated. Essentially, the engine stalling can temporarily put the car into a "safe mode," which allows the ECU to produce trouble codes.
Furthermore, while a failing crankshaft position sensor might initially show no warning light on the dash, its effects on the engine's behavior can manifest subtly. The ECU might receive intermittent and fluctuating signals, causing the engine to behave unpredictably until the problem escalates.
It's also interesting that temperature changes appear to be a substantial concern for these sensors. We've noted a correlation between extreme temperature fluctuations (whether hot or cold) and an increased tendency for these components to malfunction. This sensitivity to temperature makes them one of the more weather-dependent parts within an engine system.
The electrical pathways associated with the crankshaft position sensor are often overlooked. However, we've found that any sort of damage to the sensor's wiring or connector can lead to an array of engine issues, including stalls, specifically during acceleration.
Even though stalling during acceleration may seem like a fuel delivery issue at first, this is not always the case. The symptoms related to crankshaft position sensor failures can be confusingly similar to those caused by problems in other areas, such as with the fuel system or the air intake. This overlap can create difficulties for those tasked with pinpointing the origin of the issues.
Moreover, the possibility of other components, such as the throttle position sensor or even the fuel system, failing simultaneously with the crankshaft position sensor is not to be disregarded. This adds a layer of complexity to diagnosing and repairing the fault, as multiple components might be contributing to the issues.
Finally, if the stalling issue due to a crankshaft position sensor fault goes unaddressed, it might put added stress on different parts of the engine in the long term. This stress arises from the uneven and irregular power delivery the engine experiences with an intermittently failing sensor. This puts extra load on other engine components, potentially shortening their lifespan.
Crankshaft Position Sensor Failures 7 Key Symptoms to Watch For in 2024 - Erratic Tachometer Readings
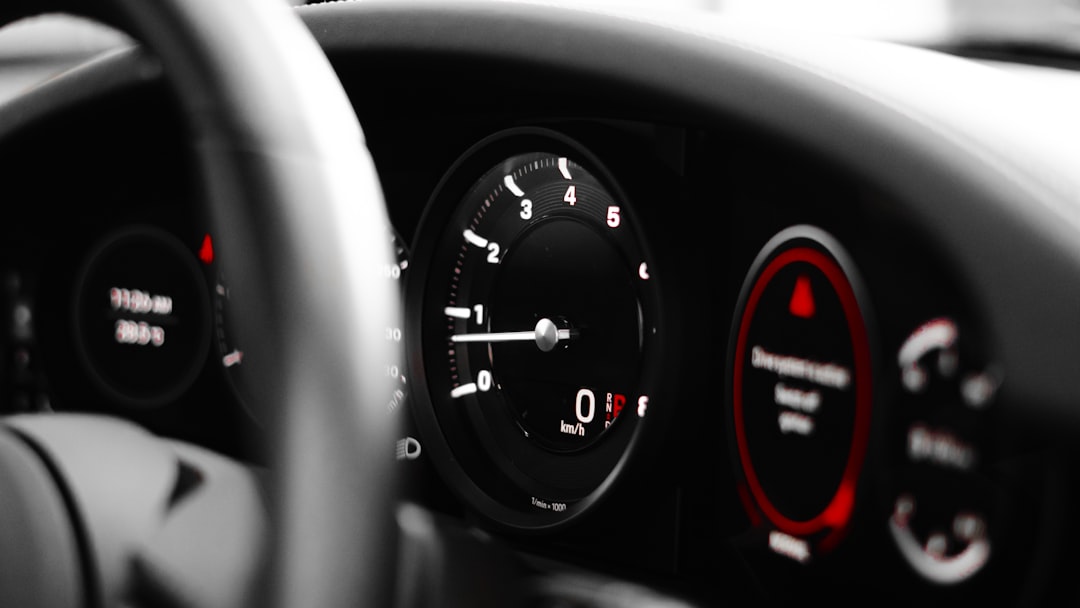
A faulty crankshaft position sensor can manifest in a rather unusual way: erratic tachometer readings. The sensor's job is to keep tabs on the engine's speed and position, relaying that information to the engine control unit (ECU). When the sensor malfunctions, the signals it sends to the ECU become inconsistent. This translates into a fluctuating tachometer needle, which is far from ideal. These unpredictable tachometer movements aren't just a cosmetic problem; they are a sign that the engine timing and fuel delivery are being affected. The erratic behavior can result in a decline in drivability and overall performance. It's crucial to take notice of these inconsistent tach readings. Addressing any underlying issues with the crankshaft position sensor promptly can prevent future headaches and maintain your vehicle's peak performance. Failing to acknowledge these symptoms can lead to further complications that could impact your driving experience in the long run.
Erratic tachometer readings can be a telltale sign of a failing crankshaft position sensor. The sensor's job is to communicate the engine's speed to the engine control module (ECM). If the sensor is malfunctioning, the ECM might get intermittent or unreliable signals, which can cause the tachometer needle to jump around erratically, leaving drivers confused. It's a situation where the displayed engine speed isn't a true reflection of what's actually happening.
The crankshaft position sensor itself relies on magnetism to work. It generates an electrical signal based on changes in the magnetic field produced by the rotating crankshaft. This reliance on magnetic fields makes the sensor vulnerable to interference from nearby electrical components, which could further add to the noise in the sensor’s signal.
Interestingly, some cars use two sensors to manage engine timing: a crankshaft position sensor and a camshaft position sensor. This redundancy can create a challenging diagnostic situation if one sensor fails as both might produce unreliable readings, hindering the process of troubleshooting and repair.
These erratic readings aren't just a nuisance; they can create real-world problems. A driver might misinterpret the fluctuating tachometer and either accelerate or decelerate at the wrong time, potentially leading to unpredictable and unsafe driving habits.
Weather can also play a role in erratic readings. The sensor's sensitivity to temperature is worth considering. In cold temperatures, components contract and the increased electrical resistance can interfere with the sensor's signal. Conversely, in hot conditions, electrical noise increases, further reducing the sensor's accuracy.
The sensor's wiring and electrical connections are another point of vulnerability. Any damage or corrosion in the wiring can cause the signals sent to the tachometer to become unreliable, adding another layer of complexity to resolving the issue.
Modern tachometers are often designed with built-in smoothing algorithms that filter out sudden spikes in sensor readings. However, when the crankshaft position sensor fails, the averaged reading may still display erratic behavior, as the faulty data still impacts the calculated average, making a failing sensor harder to diagnose.
In some vehicles, you can recalibrate the tachometer using diagnostic tools. While this can improve the situation temporarily, it can also mask the root cause of the problem, making it easy to ignore a failing crankshaft position sensor.
The sensor's location within the engine is also a factor. In some engine configurations, vibrations and external conditions can cause the sensor to perform inconsistently, leading to erratic data being sent to the tachometer.
It's perhaps surprising that the quality of fuel can also affect these readings. If the fuel is poor, the engine may not run as it should, placing extra stress on components like the crankshaft position sensor and making its failure more noticeable. This type of indirect relationship between fuel quality and sensor performance is something worth exploring in future research.
Crankshaft Position Sensor Failures 7 Key Symptoms to Watch For in 2024 - Intermittent Check Engine Light Illumination
An intermittently flashing check engine light can be a subtle yet important indicator of a failing crankshaft position sensor. This light often serves as the initial sign that the sensor isn't functioning properly, particularly when it fails to deliver a consistent signal to the engine's computer, the powertrain control module (PCM). It's not uncommon to see the light briefly illuminate during instances of engine misfires or stalling, hinting at a disruption in the sensor's signal. However, a curious aspect of crankshaft position sensor failures is that the check engine light isn't always triggered, allowing potential issues to linger undetected for extended periods. Alongside the light's sporadic appearance, drivers might notice other changes, such as reduced fuel economy or erratic engine performance, emphasizing the importance of closely observing any unusual behavior from your vehicle. Prompt attention to these warning signs not only helps prevent more serious engine problems but also helps maintain the overall health of your car's engine in the long run.
The crankshaft position sensor's role in engine operation is crucial, and its failure can manifest in a variety of ways, including an intermittent check engine light. It's not always a simple path to diagnosis, as the sensor's failures often occur in fits and starts rather than a consistent, predictable manner. The sensor's output can be sensitive to the electrical system's health, with voltage fluctuations leading to behaviors that mimic true sensor failure. This means that issues with the battery or corroded wiring could be mistaken for a sensor problem.
Furthermore, engine loads seem to play a significant role. When the engine is working harder, the impact of any irregularities in the sensor's signal is magnified. This creates a situation where the symptoms might be quite pronounced, potentially leading technicians down a diagnostic rabbit hole. The sensor is positioned in a location that can make it susceptible to damage, whether from impacts or harsh environments. Even seemingly minor physical damage to the sensor can result in an unpredictable check engine light.
Diagnostic trouble codes related to crankshaft position sensor failures can also be sporadic and fleeting. These temporary codes present a frustration for technicians, as it can be difficult to capture and isolate the problem if it only occurs occasionally. It appears that electrical noise from surrounding engine components can also interfere with the sensor's signals, leading to intermittent check engine light activations even if the sensor itself is functioning nominally.
Interestingly, the condition of the crankshaft itself can influence the sensor's readings. As the crankshaft wears, its surface can change, affecting the magnetic field that the sensor relies on. This creates the intriguing possibility of a healthy sensor encountering issues simply due to the changes in the component it interacts with. Modern diagnostic tools are helpful but still struggle to capture these transient conditions, which makes pinpointing a truly intermittent problem challenging. The sensor's performance also shows sensitivity to fluctuating temperatures, not just in the cold as we previously thought. Both extremely hot and extremely cold conditions seem to make the sensor more likely to fail or produce erratic signals. This could explain why some individuals see the light illuminate more frequently during certain seasons.
The sensor's connection to the electrical system is complex, and problems with the wiring, connections, or even grounding can lead to issues that mimic a failing sensor. This intricate interplay between electrical pathways, mechanical wear, and sensor functionality makes it challenging to correctly attribute engine problems to the crankshaft position sensor, particularly when intermittent issues are at play. All these factors add a layer of complexity to diagnosing issues involving the crankshaft position sensor, highlighting the need for meticulous troubleshooting to pinpoint the root cause rather than simply replacing parts based on symptomatic behavior.
Crankshaft Position Sensor Failures 7 Key Symptoms to Watch For in 2024 - Reduced Fuel Economy and Performance
A faulty crankshaft position sensor can significantly impact fuel economy and overall engine performance. This sensor's primary function is to relay crucial information about the engine's speed and position to the engine control unit (ECU). When it malfunctions, the ECU receives inaccurate data, leading to incorrect fuel delivery calculations. This disruption results in reduced fuel efficiency, meaning your vehicle might consume more fuel than usual for the same amount of travel. Additionally, a faulty sensor often translates to poor acceleration and erratic engine operation. The engine might hesitate or struggle to accelerate smoothly, ultimately impacting performance. It's important to recognize that a drop in fuel economy can be a telltale sign of a deeper issue, and addressing these problems promptly helps maintain your engine's health and prevent future headaches. Ignoring these signals could potentially lead to more significant and costly repairs later on.
### Surprising Facts about Reduced Fuel Economy and Performance Related to Crankshaft Position Sensor Failures
A faulty crankshaft position sensor can lead to a range of issues beyond just stalling. One area where its impact is often overlooked is fuel economy and overall engine performance. It turns out, this sensor's role in the engine's timing and management is so critical that even subtle errors in its output can significantly affect how efficiently the engine runs.
For instance, if the sensor isn't providing accurate information about the crankshaft's position and speed, it can throw off the fuel injection timing. This means the engine might get either too much or too little fuel at certain points in its cycle. This imbalance can result in a decrease in fuel efficiency, as the engine has to work harder to compensate for the incorrect fuel mixture.
Moreover, these inaccuracies can lead to engine misfires. When the spark plug fires at the wrong time due to a flawed signal from the sensor, it essentially wastes fuel as the unburned fuel gets expelled with the exhaust gases. This inefficiency directly affects fuel economy, and it also contributes to higher emissions.
Interestingly, the effect of a failing sensor seems to be amplified under varying engine loads. When the engine is under heavier loads, like during acceleration, the consequences of a bad signal from the sensor are much more pronounced. This means drivers might experience a larger drop in fuel efficiency and responsiveness when the engine is working harder.
It's fascinating to consider that the crankshaft position sensor is such an integral part of modern engine management systems. These complex systems rely on the sensor's data to make critical decisions regarding fuel delivery and ignition timing. If the sensor sends incorrect data, it throws off the entire system and can force the engine to operate in a sort of "safe mode" where its performance is compromised to avoid damaging other parts.
However, it's not just faulty signals that can cause problems. The sensor is quite susceptible to electrical interference from other engine components. This electrical noise can create erratic readings, leading to fluctuations in engine performance and fuel efficiency as the ECU tries to adapt to these incorrect inputs.
What's more, temperature can also affect the sensor's performance in less obvious ways. While we already discussed how extremes of hot and cold can impact the sensor, it's also susceptible to rapid fluctuations in temperature. These changes can create instability in the sensor's output, leading to unpredictable engine behaviour and poor fuel economy, especially in transitional weather periods.
Another surprising aspect is that fuel quality can play an indirect role in the sensor's performance. If the fuel quality is poor, it might lead to engine knocking, a condition where the fuel ignites too early in the combustion cycle. The engine control unit will attempt to correct for this by adjusting the ignition timing, but if a failing sensor already exists this corrective measure becomes even more problematic, potentially negatively impacting fuel economy.
Additionally, over time, the crankshaft itself wears down. This wear can alter the magnetic field that the crankshaft position sensor relies upon. The sensor, unaware of this change, may misinterpret engine speed or position, which further compromises fuel efficiency.
Finally, one of the most frustrating aspects of crankshaft position sensor failures is that they often don't trigger immediate warning lights. The symptoms might develop slowly, with a gradual decrease in fuel economy being the first noticeable issue. This "stealth" nature of sensor failures can make them harder to diagnose early, often leading to more significant engine issues down the line. If left unaddressed, these recurring problems can put increasing stress on the engine, further reducing its efficiency and potentially shortening the lifespan of related components.
In conclusion, while the crankshaft position sensor might not be the first thing that comes to mind when fuel economy takes a hit, it's clear that it plays a much more influential role than one might initially assume. It's a reminder that even components that don't seem directly linked to fuel consumption can have significant consequences on the engine's efficiency and overall performance.
Crankshaft Position Sensor Failures 7 Key Symptoms to Watch For in 2024 - Difficulty Starting the Vehicle
A vehicle that's difficult to start can be a sign that the crankshaft position sensor isn't working correctly. This sensor is essential for communicating the crankshaft's speed and position to the engine's computer, which then manages fuel delivery and ignition timing. If the sensor isn't functioning properly, the communication breaks down, and the engine might struggle to fire up smoothly, potentially causing frustrating delays in getting the car started. This difficulty can worsen under certain conditions, especially when the engine faces varying loads. This suggests that getting any potential problem diagnosed and addressed promptly is a smart move to keep your engine running its best. If you ignore these starting issues, it can lead to more serious engine problems, highlighting the need for drivers to pay attention to how their cars are behaving.
### Surprising Facts about Difficulty Starting the Vehicle Related to Crankshaft Position Sensor Failures
1. A crucial aspect of starting a vehicle is the precise timing of fuel injection, a process heavily reliant on the crankshaft position sensor's data. Sensor failure can lead to inaccurate fuel delivery at the initial ignition stage, resulting in extended cranking times. It seems like a simple concept, but the timing of fuel delivery is very important in the engine start-up process.
2. A malfunctioning sensor can cause intermittent signal loss, forcing the ECU to essentially guess the crankshaft's position during the start sequence. This estimation process can lead to prolonged start times or even a complete failure to crank the engine. The ECU isn't able to start the engine without reliable information.
3. The crankshaft position sensor exhibits sensitivity to vibrations. During engine startup, increased vibrations can exacerbate a damaged sensor or loose wiring, potentially causing it to send erratic or unreliable signals, hindering the ignition sequence. Engine vibrations can lead to problems with the sensor.
4. We've noticed that sensor failures seem to become more apparent during cold starts. As engine parts expand with warming temperatures, any slight discrepancies in sensor readings might become more pronounced, leading to a more difficult start. This is yet another odd behavior of the crankshaft position sensor.
5. Fluctuations in the electrical system, specifically from the battery or alternator, can significantly influence the sensor's performance. A weak battery may not supply sufficient power for the sensor to send reliable signals during startup, causing issues with cranking the engine. This interaction with the electrical system can be rather unexpected.
6. The proximity of electrical components can introduce interfering signals or "noise" that distorts the sensor's output. This noise can create confusion for the ECU in interpreting the crankshaft's position, making the engine startup process more complex. It appears that there's a lot of noise in the engine compartment, which may interfere with the sensors.
7. The crankshaft position sensor plays a key role in synchronizing the operation of fuel injectors and spark plugs. If the sensor malfunctions, this timing is thrown off, which can hinder the smooth process of engine startup. The proper synchronization of engine components is necessary to start the car.
8. The sensor's placement in the engine bay makes it vulnerable to external influences such as debris, oil leaks, and exposure to moisture. These factors can lead to corrosion or physical damage, ultimately affecting the sensor's reliability during the critical moments of engine startup. It would seem that this part of the engine can be problematic.
9. When fuel levels are low, the challenges related to the sensor might be amplified as the engine needs to work harder to start without sufficient fuel pressure. A malfunctioning sensor further complicates this process, leading to more noticeable issues. This problem shows the interdependence of engine systems.
10. Sometimes, other problems within the engine may create error codes that obscure the true symptoms of a failing crankshaft position sensor. This can lead drivers to misdiagnose the issue, wrongly assuming that starting problems are related to different parts of the engine. It seems there are a lot of things that can confuse a diagnostic on a failing crankshaft position sensor.
Crankshaft Position Sensor Failures 7 Key Symptoms to Watch For in 2024 - Unexpected Engine Misfires
Unexpected engine misfires can be a frustrating experience for drivers, often signaling potential problems with the engine's timing and fuel delivery. A common culprit behind these misfires can be a malfunctioning crankshaft position sensor. This sensor is crucial for providing accurate information about the engine's rotational position and speed to the engine's computer. If this sensor fails, it can send inaccurate data, leading to misfires caused by incorrect fuel injection or spark timing. These erratic firings can manifest as a rough engine, a decrease in performance, and potentially more significant engine damage if left unresolved. Furthermore, fuel efficiency can take a hit due to the wasted fuel associated with these misfires. Recognizing that misfires can be connected to a faulty crankshaft position sensor is important for drivers who want to avoid costly repairs later on. Early detection and diagnosis are key to resolving these issues before they escalate.
### Surprising Facts about Unexpected Engine Misfires Related to Crankshaft Position Sensor Failures
1. Engine misfires often happen due to bad fuel timing. A failing crankshaft position sensor can cause this by giving the engine's computer bad data about the engine's speed and position. The engine computer relies on accurate information to control fuel injection and ignition. So, a faulty sensor can really mess things up.
2. Misfires can have a ripple effect on engine performance. They lead to worse emissions and make the engine less efficient over time. This gradual decline can get worse if you don't fix it, making early diagnosis really important.
3. It's interesting that you might not notice misfires right away. Sometimes, early misfires are small and can easily get confused with normal engine behavior. This sneaky progression makes it hard to connect misfires with a bad sensor without some good diagnostics.
4. The relationship between how hard the engine is working and misfires is interesting. When the engine is under a heavier load, like during acceleration, any errors in the sensor's signal become even more noticeable and cause more misfires. This is confusing for troubleshooting.
5. The sensor's wiring is crucial. Damaged or corroded wiring can cause the sensor to send bad information. This highlights the importance of looking at the wiring during any diagnosis.
6. Misfires can be caused by interference from other sensors, like the camshaft position sensor. The electronic signals from these sensors can clash, making the engine run inconsistently and masking the root cause.
7. It's fascinating how much the weather can affect engine performance. When temperatures change, the crankshaft position sensor can get confused, leading to misfires. This happens despite there not being any obvious mechanical issues.
8. The quality of your fuel can have a direct impact on engine misfires if the sensor is already weak. Bad fuel leads to incomplete combustion, making the misfires worse and potentially leading to misdiagnosis as a fuel-related issue.
9. It's not well known, but the electrical system in the car can affect the sensor's readings. A failing battery or alternator can cause voltage inconsistencies that make the sensor send bad information and cause misfires.
10. Many misfires get misdiagnosed as spark plug or fuel injector problems when it's actually the crankshaft position sensor. This is a common mistake. This shows that you really need to do thorough diagnostics to find the root cause of the issue, not just guess based on symptoms.
Crankshaft Position Sensor Failures 7 Key Symptoms to Watch For in 2024 - Increased Vibrations at Idle
Noticeable engine vibrations during idle can often be a sign that the crankshaft position sensor isn't functioning correctly. This sensor is vital for the engine's timing and fuel delivery, and when it malfunctions, the engine might not run smoothly, resulting in noticeable shaking while the vehicle is stopped. The sensor provides crucial information to the engine's computer, and when it delivers faulty data, it can lead to rough engine operation and a noticeable increase in vibrations. It's important to recognize that these increased vibrations are a symptom that might be coupled with other problems like misfires or decreased fuel economy, making the specific cause of the issue harder to isolate. If you detect unusual vibrations during idling, it's best to get it checked promptly. Ignoring these vibrations could lead to a worsening of the problem and possible damage to other parts of the engine down the road. Paying attention to how your engine behaves at idle can help detect sensor-related problems and prevent more costly and complicated repairs in the future.
Increased vibrations at idle can often be a subtle sign that the crankshaft position sensor isn't working as it should. The sensor plays a key role in dictating the engine's timing, and any inconsistencies in the signals it sends to the engine control unit (ECU) can disrupt the smooth operation of the engine, leading to vibrations that are easily felt in the vehicle. This disruption is often due to inaccurate readings of the crankshaft's position and speed, which affects the engine's ability to maintain a steady idle.
It's fascinating how sensitive the sensor is to external factors. The magnetic field that the sensor utilizes for measuring the crankshaft's position can be influenced by other electrical components in the engine compartment. This means that interference from electrical noise, or even a malfunctioning electrical component nearby, might distort the sensor's signal, leading to increased vibrations.
Furthermore, we've observed that wear on the crankshaft itself can create more pronounced vibrations if the sensor isn't functioning optimally. If the sensor is delivering inaccurate readings for an extended period, it can cause the crankshaft to wear down unevenly. This uneven wear can lead to what's called a harmonic imbalance – essentially, a situation where the crankshaft vibrates more intensely at certain RPMs, often making the idle feel rougher. This phenomenon highlights the critical connection between the sensor's performance and the long-term health of the engine's mechanical components.
Engine mounts, often overlooked, also play a role in vibrations. The severity of vibrations due to a faulty sensor can sometimes be so great that it stresses the engine mounts. These mounts act as shock absorbers, damping the vibrations from the engine. However, if the sensor continues to deliver incorrect signals and the engine continues to vibrate at higher levels, it can lead to wear and tear on the mounts, contributing to a feedback loop of worsening vibration and eventually requiring repair.
We've found that the crankshaft position sensor's signal often fluctuates when it starts to fail. This fluctuating signal can make it challenging for the ECU to maintain a steady idle, as the fuel-air mixture and ignition timing can vary as the sensor data changes. This can result in oscillating idle speeds, which are easily felt as erratic vibrations within the vehicle.
Interestingly, how the driver manipulates the engine can impact vibrations as well. For instance, if the sensor is failing, sudden acceleration or deceleration from idle can exacerbate the vibrations. This is likely due to the ECU struggling to adjust fuel delivery and spark timing quickly based on faulty sensor data.
Another unexpected challenge is the difficulty in identifying the cause of vibrations. It's easy for the vibrations caused by a faulty sensor to be mistaken for symptoms of other problems, such as a problem with the exhaust system or a mechanical imbalance in the crankshaft itself. This overlap in symptoms can make the diagnosis of a failing sensor more complex, often requiring a more thorough investigation of the engine's operation.
The sensor's performance can be affected by temperature changes as well. Temperature fluctuations can lead to changes in the sensor's resistance and sensitivity, making it more likely to deliver erratic readings. These changes are particularly pronounced in transitional weather periods, when temperatures are rapidly fluctuating.
Furthermore, even the way the sensor is attached to the engine can impact vibrations. If the sensor isn't securely mounted, it might send inconsistent signals, which can translate into fluctuating vibrations. The sensor's mounting position adds a further layer of complexity to diagnosing vibration issues.
Finally, many mechanics tend to automatically assume that increased vibrations are due to mechanical problems within the engine, such as a worn-out crankshaft or faulty mounts. However, this assumption can cause them to overlook the faulty sensor as the underlying cause. This underscores the importance of a thorough diagnostic process to properly pinpoint the origin of the vibrations rather than just replacing mechanical components in a hope that they resolve the issue.
More Posts from tunedbyai.io: