Engineering Evolution How Pininfarina Refined the Ferrari 575M Maranello's Aerodynamic Profile in 2002
Engineering Evolution How Pininfarina Refined the Ferrari 575M Maranello's Aerodynamic Profile in 2002 - Wind Tunnel Tests at Pininfarina Turin Reveal 12% Drag Reduction for 575M
The Ferrari 575M Maranello, a symbol of Italian automotive prowess, underwent a significant transformation in 2002 thanks to Pininfarina's expertise. Wind tunnel evaluations in Turin yielded impressive results: a 12% reduction in aerodynamic drag. This accomplishment showcases how meticulous testing, combined with decades of knowledge in wind tunnel technology, can fundamentally improve a car's performance. Pininfarina's facility, one of a select few capable of full-scale vehicle testing, played a crucial part in this development. The advancements achieved, including improved efficiency and crosswind stability, are testaments to the continuous pursuit of optimization within the world of supercar design. These improvements represent a paradigm shift in aerodynamic design, pushing boundaries and reinforcing the critical role of sophisticated testing in developing the luxury vehicles of the future. While some might see this as a mere refinement, it signifies a deeper understanding of how aerodynamics interacts with a vehicle, offering a glimpse into the future of vehicle performance and luxury car design.
Intriguingly, Pininfarina's wind tunnel testing in Turin uncovered a substantial 12% reduction in aerodynamic drag for the Ferrari 575M. This finding underlines the profound impact that careful aerodynamic design can have on a car's performance. It seems that even subtle modifications to the front and rear sections of the 575M were enough to deliver significant improvements in both efficiency and top speed.
Interestingly, the team at Pininfarina relied on a combination of physical testing and computational fluid dynamics (CFD) simulations. This approach allowed for more accurate predictions of airflow patterns before committing to physical prototypes. It's fascinating how this blend of methods could help in achieving optimal results in such a short amount of time.
The 575M's rear spoiler was a crucial area of focus, with a clear emphasis on controlling the airflow turbulence it generated. This wasn't simply about drag reduction, but also about maximizing downforce. This was essential for maintaining stability at high speeds, something that's paramount for performance-oriented cars like the 575M.
While many thought high performance cars were inherently compromised in terms of aerodynamic efficiency, Pininfarina's work challenged that assumption. By drawing on aerospace engineering principles, like optimizing airfoil shapes, the design team created a supercar that prioritizes both speed and efficiency. This is evident in the 12% drag reduction, which not only benefits performance but also translates to improved fuel efficiency – showcasing that these two elements are not necessarily at odds with one another.
It's evident from Pininfarina's iterative approach that experimentation was key to finding the best aerodynamic solution. Multiple versions of key components were developed and tested in the wind tunnel to optimize airflow and drag. The subtle redesign of the front grille, for instance, illustrates how aesthetic considerations can be cleverly integrated with aerodynamic concerns, leading to improvements in both areas. This also showcases the need to prioritize cooling of the engine. The data from the wind tunnel tests had a tangible impact. It set a new standard for aerodynamic performance in the high-end sports car category, pushing design boundaries and influencing future Ferrari and other sports car designs. This influence highlights the far-reaching consequences of this type of research, setting a benchmark that extended beyond the 575M.
Engineering Evolution How Pininfarina Refined the Ferrari 575M Maranello's Aerodynamic Profile in 2002 - Redesigned Front Air Dam and Modified Hood Create Enhanced Air Flow Management
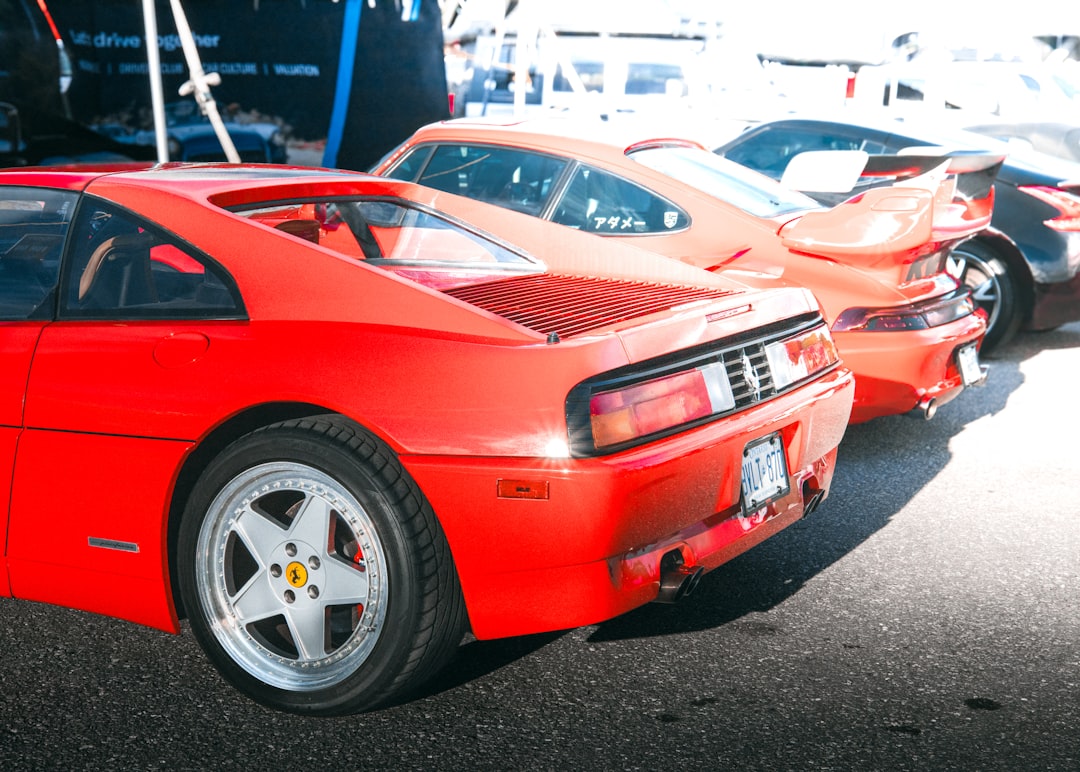
The Ferrari 575M Maranello's front end saw a significant makeover in 2002, with a redesigned air dam and modified hood playing a crucial role. These changes, spearheaded by Pininfarina, were focused on optimizing airflow around the vehicle. By manipulating the way air interacts with the front of the car, they aimed to enhance overall aerodynamic performance. It's not just about reducing drag—though that was a key aspect—but also about maximizing downforce and stability at high speeds. The changes reflect a shift towards integrating aesthetics with functionality. It's a fascinating example of how careful design can address seemingly contradictory goals. You get a car that looks fantastic while also performing at a higher level. It's evident that Ferrari, as always, is pushing the boundaries of what a high-performance sports car can achieve, leveraging advancements in wind tunnel testing and CFD to achieve a harmonious balance of form and function. This emphasis on refined aerodynamics showcases the ongoing evolution of the supercar, revealing how minor tweaks can make a considerable impact on the car's overall handling and driving experience. The legacy of Ferrari, known for its innovative spirit, is further solidified by this dedication to continuous improvement in design.
The Ferrari 575M Maranello's front end received a thoughtful redesign in 2002, with a revamped air dam and modified hood, primarily to refine how air moves over and through the vehicle. It's fascinating how the redesigned air dam not only shapes the overall airflow but also subtly manages air around the wheels, potentially contributing to reduced drag and potentially improving tire performance. This emphasizes the intricate interplay of even seemingly small components in achieving a cohesive aerodynamic profile.
The hood's modifications, including the integration of air extraction vents, are quite intriguing. The placement of these vents suggests a strategy for optimizing high-pressure air flow from the engine compartment. One would speculate that this helps manage lift, which can become a significant force at higher speeds. Maintaining stability at higher velocities is crucial, and managing this lift likely ensures better contact with the road.
It's also interesting to consider the limitations of purely computational methods. Though CFD simulations are a powerful tool, Pininfarina's decision to use wind tunnel testing alongside computational methods demonstrates a healthy skepticism towards relying solely on digital models. It's a testament to the understanding that theoretical advantages often need to be refined and validated in real-world testing environments, illustrating the need for a pragmatic approach.
The air dam and hood modifications likely play a role in engine cooling, too. Improved airflow management can have a direct impact on keeping the 575M's V12 engine within its optimal temperature range. This in turn should contribute to sustained high performance, especially under heavy load conditions, which is crucial for a high-performance engine.
Moreover, this redesigned system is clearly not a static element. Depending on speed, the airflow is subtly redirected—prioritizing engine cooling at lower speeds and minimizing drag and maximizing downforce at higher speeds. This highlights a thoughtful understanding of how air interacts with the vehicle at different velocities.
The refinement process wasn't a singular event. It involved multiple prototypes and countless iterations, rigorously tested within the wind tunnel. Even the smallest changes were carefully examined for their impact, demonstrating how the pursuit of aerodynamic perfection can involve meticulous experimentation. This iterative approach reflects the ongoing search for improved performance in high-end automotive engineering, showing that even with exceptional engineering, there's always an opportunity for advancement.
Intriguingly, the surface textures of the new components might be carefully optimized as well. The choice of materials and finish can impact the separation of the airflow from the vehicle's surfaces. This hints at how material science becomes deeply interwoven with high-performance car design.
The changes aren't just about performance – the integration of functionality with visual appeal is evident in this redesign. It suggests a deliberate blending of aesthetics and aerodynamic needs, indicating a continued pursuit of visually stunning automobiles that also achieve a high level of performance.
The impact on handling in crosswinds is likely considerable as well. Enhanced stability in crosswinds is essential for high-speed driving and emphasizes the interconnectedness of aerodynamics with safety and handling. Gusts can have a dramatic effect at high speeds, making stability control a critical aspect of high-performance cars.
Pininfarina's work on the Ferrari 575M represents a significant moment in aerodynamic design. The insights gained and advancements achieved likely trickled down to other models in the Ferrari lineup and beyond, reinforcing the idea that innovation in a single vehicle can help advance a whole sector. It illustrates that what may seem like a refinement is actually a step towards a future generation of high-performance vehicles, showing how continuous learning and improvement are paramount in automotive engineering.
Engineering Evolution How Pininfarina Refined the Ferrari 575M Maranello's Aerodynamic Profile in 2002 - Side Mirror Integration Changes Lower Turbulence at High Speeds
The pursuit of ultimate performance in high-performance cars often involves scrutinizing even the smallest details, and side mirrors have emerged as a key area for optimization. These seemingly innocuous components, if not carefully designed, can create significant aerodynamic drag and turbulence, particularly at higher speeds. Research has shown that side mirrors can contribute a substantial portion, up to 36%, of a car's overall drag. This leads to increased air resistance, negatively impacting performance and fuel efficiency. Beyond the performance impact, turbulence generated by side mirrors can create unwanted cabin noise, reducing the overall refinement and comfort of the driving experience.
However, this isn't a static problem. Engineers have found that adjusting the positioning and shape of side mirrors can greatly affect how air interacts with the vehicle. One crucial area of investigation has focused on the angle of the mirror's base. It turns out that finding the ideal angle to minimize wind noise and drag requires careful balancing. Positioning the mirror base at approximately 85 degrees seems to offer an optimal compromise, achieving a noticeable reduction in both turbulence and wind-generated noise.
This discovery represents a small but important step in the ongoing quest for refined aerodynamic design. It not only suggests ways to improve the aerodynamic profile of current vehicles but also provides valuable insights for future car design, highlighting the interconnectedness of aesthetic concerns with engineering practicality. In the competitive landscape of high-performance car development, even small advancements, like the optimized integration of side mirrors, demonstrate the constant drive to refine vehicles for better performance and a more refined driving experience.
Side mirrors, while seemingly minor, play a surprisingly significant role in a car's aerodynamic performance, especially at higher speeds. It's been known for a while that they contribute a considerable portion to overall drag, but more recent research highlights how their integration into the overall design of the vehicle can impact turbulence.
We know that the shape and position of the side mirror can have a substantial influence on airflow, generating turbulent wakes that can cause noise and drag. Finding the ideal position for the mirror base, relative to the A-pillar, is crucial for managing this. Interestingly, an angle around 85 degrees seems to strike a good balance between minimizing drag and keeping wind noise at bay. This is probably because that angle helps manage the interaction of the air flow around the A-pillar with the air flow disturbed by the mirror.
The interaction between the airflow around the side mirror and the A-pillar itself is fascinating. It creates a complex flow dynamic, particularly at higher speeds. One can see the complexity in wind tunnel testing, where the flow patterns are visualized through smoke or other methods. Numerical simulations can offer deeper insights into the behavior of airflow here, through approaches like Large Eddy Simulations (LES). These are a relatively recent technique that seems to be helpful in understanding turbulent flows.
The issue of noise, especially wind noise around the side windows, is a significant one. It contributes to a less than desirable cabin experience. The problem is even more severe in high-performance vehicles, where speed exacerbates the effects of turbulence. This wind noise can lead to driver and passenger fatigue. It is also a major contributor to what car buyers have complained about.
While modifying side mirror designs is a common avenue to reduce drag and noise, one has to carefully consider the constraints. Legal requirements related to visibility are extremely important, often making the design space smaller. It becomes a challenge to innovate while staying compliant with safety standards.
High-performance vehicle design tends to focus on achieving very high speeds, but this inevitably leads to turbulence issues. Minimizing the creation of low-pressure areas behind the mirror is a core part of the effort to manage this. Interestingly, this approach has some commonality with the techniques used in aerospace, suggesting there's potential to draw more from that industry.
It seems that the future might favor some sort of active aerodynamic control for side mirrors. Retracting them or adjusting their shape, as a function of speed, could offer a much more dynamic control. This is probably still years away, but it suggests that the simple side mirror might eventually disappear in favor of more complex and better integrated designs.
The move towards camera-based side view systems could be the next step in this direction. While it's not universally accepted yet, the potential for this approach to dramatically improve efficiency, by completely eliminating the mirror, is huge. In many ways this approach hints at the future of car design. It's likely to change how we view the car and its interaction with the world around it.
Engineering Evolution How Pininfarina Refined the Ferrari 575M Maranello's Aerodynamic Profile in 2002 - Rear Diffuser Modifications Stabilize Airflow Under High Performance Conditions
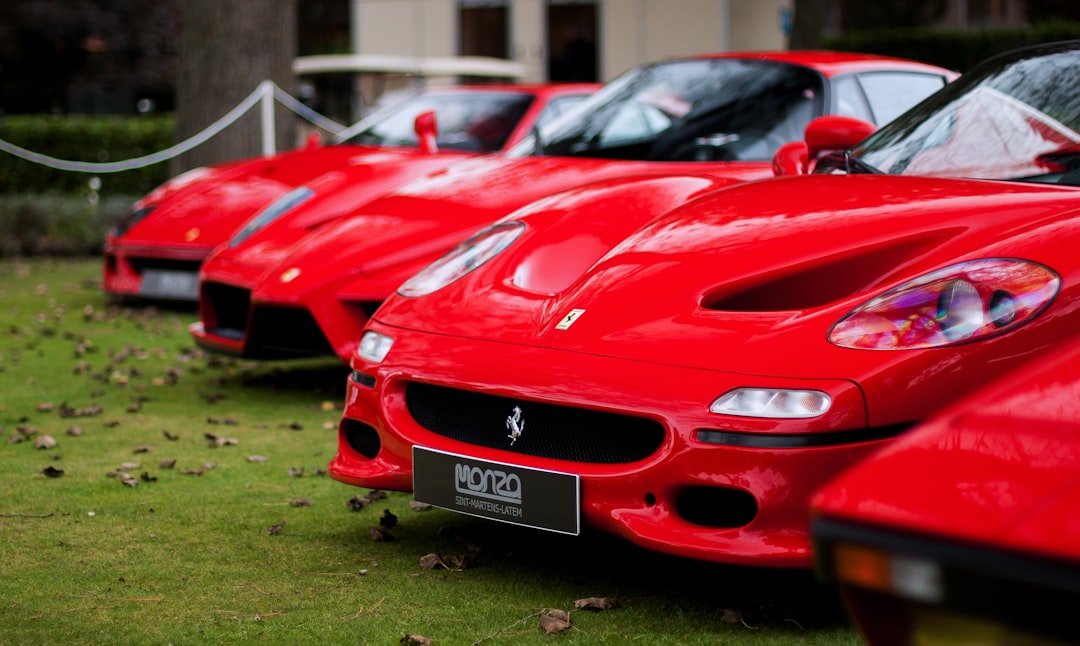
Rear diffusers have become increasingly important in achieving optimal aerodynamic performance, particularly in high-performance vehicles. Their primary role is to manage the airflow transition between the higher-pressure zone above the car and the lower-pressure area underneath. This intricate interplay is crucial for minimizing drag and enhancing vehicle stability at high speeds, which is especially vital for sports cars that push the boundaries of performance. The design and configuration of the diffuser have a direct impact on how well this transition occurs, influencing factors like drag reduction, overall stability, and even steering response.
It's not just about aesthetics either. Modifying a car's rear diffuser can significantly enhance its handling and performance capabilities. The changes made to the Ferrari 575M Maranello by Pininfarina illustrate this perfectly. Their refinements to the diffuser demonstrate that even seemingly minor alterations can result in substantial gains in aerodynamic efficiency. This is especially noteworthy given how complex airflow interactions become at higher speeds.
The focus on these kinds of modifications represents a shift in automotive engineering, a movement towards greater precision and optimization. We're moving away from the era where aerodynamic considerations were simply a secondary thought to a time when it's a crucial element in the design process. This push towards better understanding and integrating sophisticated aerodynamic components, like modified diffusers, will likely define the evolution of future high-performance cars.
Rear diffusers are essentially inverted wings situated at the back of a car, subtly manipulating the airflow underneath the vehicle. This manipulation, particularly at higher speeds, generates negative pressure, contributing to a decrease in drag and a corresponding increase in downforce. This is a pretty crucial interplay, as it helps maintain vehicle stability at high speeds where any disruptions in airflow can lead to unpredictable behavior.
The design of a rear diffuser has a powerful influence on the overall surface area interacting with the air. Research suggests that even subtle adjustments in a diffuser's shape can yield noticeable changes in the car's aerodynamic efficiency, impacting its performance metrics. It's not always about dramatic changes, but sometimes small tweaks can make a difference.
Understanding the dynamics of fluid flow is paramount in diffuser design. Computational fluid dynamics (CFD) techniques allow engineers to build digital models and predict how design choices impact airflow patterns. This capability is vital as it lets them virtually experiment with different diffuser designs before creating physical prototypes and going through costly wind tunnel testing.
Beyond just affecting aerodynamics, rear diffusers have an influence on tire grip. The increased downforce achieved with an effectively designed rear diffuser translates into a tangible benefit: enhanced traction, especially during high-speed cornering maneuvers that luxury and performance cars often encounter. This seems like a logical side effect of better airflow management, but it's still important.
Diffusers are generally part of a larger aerodynamic system. They're best deployed in conjunction with other components like front splitters and side skirts. This synergistic relationship creates a cohesive aerodynamic profile, which helps minimize any disruption of airflow, further contributing to vehicle stability at higher speeds. It’s a reminder that car design isn't a collection of isolated elements, it’s all interconnected.
Some high-performance vehicles are even incorporating active aerodynamic systems. These clever systems allow for real-time adjustments to the diffuser's angle or shape, based on speed or driving conditions. The ability to dynamically optimize this interaction between the car and air opens up possibilities for maximizing both drag reduction during cruising and the provision of enhanced downforce during aggressive driving.
Material selection is also important when considering diffusers. Composite materials and lightweight metals are often favored because of the weight reduction benefits, but engineers have to ensure that the structure can handle the forces generated at higher speeds, where structural integrity is absolutely critical.
Interestingly, rear diffusers can also influence the sonic landscape of a vehicle. By managing how the air interacts with the car and exhaust, diffuser designs can help refine or even amplify the exhaust note, leading to a more customized sound experience for both the driver and passengers. This isn't always planned, but the impact is clear.
Of course, testing is the ultimate arbiter of a good design. Designers repeatedly refine their diffuser designs through a mix of computational simulations and physical wind tunnel tests. The data obtained from these tests is used to refine the diffuser designs, creating a stronger understanding of airflow and enhancing the performance across various driving scenarios.
The innovations being implemented in diffuser design are not just improving current vehicles—they're setting the standard for future designs. Advancements in diffuser profiles and their integration with wider aerodynamic systems should lead to substantial performance gains across upcoming luxury and supercar models, which is clearly something we'll be looking forward to.
Engineering Evolution How Pininfarina Refined the Ferrari 575M Maranello's Aerodynamic Profile in 2002 - Active Aerodynamic Elements Adjust Based on Vehicle Speed and Drive Mode
Active aerodynamic elements represent a notable shift in automotive engineering, particularly in the realm of performance and luxury vehicles. These elements are no longer static design features but rather dynamically adjust based on factors like vehicle speed and the chosen drive mode. This dynamic adjustment allows for fine-tuning of the car's aerodynamic profile, maximizing downforce during aggressive driving or minimizing drag for improved efficiency during cruising. The ability to adapt in real-time, using information from various sensors including acceleration and braking inputs, highlights the increasing sophistication of vehicle control systems.
It's worth noting that this innovation is not solely confined to racing vehicles. Supercars and luxury cars are increasingly incorporating active aerodynamic elements, recognizing that they offer a significant performance advantage. This integration seamlessly weaves together aesthetics and functionality, leading to a greater sense of control and responsiveness.
As these technologies continue to evolve, they're shaping a new paradigm for automotive design. We see a clear movement away from a purely aesthetic focus towards a more holistic approach that incorporates active aerodynamics as a core performance element. In essence, these adaptive features signify a step towards a future where vehicle performance and control are seamlessly interwoven with the environment through intelligent and responsive systems. The potential impact on driving experience and overall vehicle performance is undoubtedly significant, demonstrating the continuing drive to refine the performance of supercars, luxury vehicles, and potentially everyday vehicles.
Active aerodynamic elements, increasingly common in modern supercars, are designed to adapt to a car's speed and driving mode. This means that these components can be actively controlled to optimize the car's performance in real-time. For instance, a rear spoiler might deploy at higher speeds to generate downforce, improving handling, while retracting at lower speeds to minimize drag and improve efficiency. This type of real-time adjustment to the car's aerodynamics highlights a shift in thinking about how cars interact with the air around them.
While it might seem like a simple change, optimizing airflow can become a very intricate task. Things like front splitters, rear diffusers, and even the car's underbody can all be shaped in such a way that the car interacts more effectively with the surrounding air. It’s interesting to consider that the shape of these elements can impact how air flows, potentially leading to increases in downforce in some areas, and decreases in drag in others. This capability allows the car to tailor its aerodynamic profile to a wider range of driving conditions.
Even features like side mirrors, often overlooked in aerodynamic discussions, can have a surprisingly large impact on how the car moves through the air. Research has indicated that the mirrors can generate a significant amount of drag and wind noise, sometimes adding up to as much as 36% of the total drag at higher speeds. This illustrates the importance of integrating design and functionality even with seemingly small elements. It also highlights the attention to detail necessary to create an optimal aerodynamic profile.
Thankfully, advanced computational techniques, like Computational Fluid Dynamics (CFD), have played a critical role in refining aerodynamic designs. CFD allows designers to build digital models and simulate airflow around the car. The ability to perform virtual testing in this way saves time and reduces the need for multiple physical prototypes during development, lowering costs. CFD, in many ways, lets designers "see" the impact of changes before committing to physical modifications, leading to a more focused approach to development.
Of course, a vehicle's aerodynamic profile is not just a collection of isolated elements. It’s the interconnectedness of components like the front splitter, side skirts, rear diffuser, and underbody panels that ultimately defines a car's aerodynamic efficiency. This interdependency underscores the complexity of aerodynamic optimization, a challenge that requires a holistic approach to design. It's a bit like a puzzle—each piece influences the others, and finding the best fit involves carefully balancing all of them.
It's important to note that the goal is to manage the air moving around and under the car. The challenge often involves minimizing areas of high turbulence or chaotic airflow, as those can disrupt the intended flow patterns. The interaction of air with the surfaces of the car is especially important for managing how the car behaves at higher speeds. The shape, angle, and positioning of elements like front air dams and rear diffusers directly impact turbulence. Even subtle changes can lead to substantial reductions in drag and improvements in vehicle stability at high speeds.
The materials used in creating aerodynamic components are also critical. Lightweight and high-strength materials, like advanced composites, are often preferred to minimize weight and maximize stiffness. It's important to remember that the airflow can generate tremendous forces on the car at higher speeds. Therefore, choosing materials that are capable of enduring these stresses is paramount for maintaining the car's aerodynamic profile during demanding driving scenarios.
A major goal in aerodynamic optimization is to maximize a car's handling and stability. By careful design, changes to components like rear diffusers can significantly enhance tire grip. The increased downforce that results from effective aerodynamic components translates to better traction during high-speed cornering and handling. This influence on handling reveals an interesting facet of aerodynamic design—its interconnectedness with critical elements of the car's performance and driving experience.
The shape of a car's aerodynamic elements directly impacts how the car moves through the air. For example, manipulating the profile of a rear diffuser can create distinct pressure zones, ultimately influencing drag and stability. Changes to these pressure zones, often leading to a slight variation in downforce or drag, can then impact handling and performance characteristics. This emphasizes the subtle but crucial role that shape plays in optimizing the car's interaction with the surrounding airflow.
The future of aerodynamic design likely involves increasing reliance on active aerodynamic elements. Incorporating sensors and actuators into aerodynamic components will open up the possibility of cars that continuously adapt to changes in their environment. The concept of actively adjusting aerodynamic profiles based on a variety of factors—speed, handling demands, and even road conditions—could transform how high-performance cars interact with airflow, potentially achieving unprecedented levels of performance and stability. We might be seeing the beginning of a paradigm shift in how cars handle in the years to come.
More Posts from tunedbyai.io: