Evaluating Truck Running Boards Function and Design
Evaluating Truck Running Boards Function and Design - Evaluating the integration of running board design with contemporary truck aesthetics
Evaluating how running boards fit visually with today's truck designs is a critical aspect for owners who want their vehicle to look as good as it functions. With trucks evolving rapidly towards more sculpted bodies and defined silhouettes, running boards are pushed to be more than just a step; they need to integrate seamlessly into the vehicle's aesthetic language. The prevalent direction in design now favors solutions that appear integrated and clean, often using materials like lighter metals for a contemporary feel that aligns with modern vehicle finishes. Features such as those that stow away electrically when not needed are becoming popular precisely because they address the desire for convenience without compromising the truck's intended lines. The key challenge remains crafting boards that enhance the truck's stance and character, rather than looking like an afterthought bolted on, thus achieving a balance where practicality and modern design principles coexist effectively.
Contemporary truck design presents an interesting challenge: integrating functional elements like running boards with increasingly streamlined and complex body surfacing. It’s fascinating to examine the engineering and design approaches taken to reconcile utility with modern aesthetics.
One critical area is the influence of aerodynamics. Rather than being afterthought add-ons, running boards on many new models are shaped with airflow in mind. Extensive use of computational fluid dynamics simulation is common during their development. This isn't just about reducing drag for efficiency, though that's a goal; it's also about managing turbulence along the vehicle's side, which can impact stability, especially at higher speeds. The attempt to make a necessarily protruding element play nicely with the air underscores the performance considerations now baked into seemingly simple components.
Material science plays a significant role too. Moving beyond basic stamped steel, premium and performance-oriented trucks often feature running boards crafted from advanced materials. Think hydroformed aluminum, allowing for complex, strong, yet lighter structures, or even structural carbon fiber composites in some high-end applications. This material sophistication isn't solely for weight savings or durability; it enables designers to sculpt forms that transition more smoothly into the truck's bodywork, facilitating a look that's less "bolted on" and more organically integrated. It’s about enabling intricate shapes that wouldn't be feasible with traditional materials and processes.
The popular trend of retractable running boards highlights the lengths gone to preserve a clean side profile. The engineering behind these systems is quite intricate. It involves not just robust mechanical linkages and potent electric motors capable of deploying a step in varying conditions, but also integrated safety systems like pinch sensors. The design goal here is clear: make the step completely disappear, sitting flush with the body when not needed, thereby achieving the uninterrupted lines favored in modern vehicle aesthetics. This complexity is a direct response to the demand for both utility and visual seamlessness.
Integrated lighting, often via LEDs embedded along the step surface, is evolving beyond mere function. While crucial for safe entry and exit in the dark, designers are utilizing this feature artistically. Precise placement, diffused light effects, and even subtle animated sequences upon approach or door opening are becoming more common. This transforms the running board from a static piece into a dynamic element of the vehicle's nighttime identity, contributing to its overall presence and tying into other exterior lighting themes. It's a detail that enhances the perceived sophistication and welcoming nature of the vehicle.
Finally, the manufacturing techniques employed are key to achieving the complex, flowing shapes seen on integrated running boards. Simple stamping is insufficient for forms intended to look like a natural extension of the vehicle's structure. Multi-axis CNC machining for metal components or advanced, multi-shot injection molding using reinforced polymers allows for the creation of contours that truly blend with the truck's existing body lines. These sophisticated processes are fundamental enablers for designers aiming to make the running board appear as if sculpted from the chassis itself, rather than being an ancillary piece.
Evaluating Truck Running Boards Function and Design - Running board materials and finishes a critical look at contributing to vehicle presentation
Running boards have fundamentally transitioned from mere utility items to vital components dictating a truck's overall look and perceived quality. The materials chosen are central to this transformation, with options extending beyond basic steel to encompass lighter alloys and specific polymer blends, each contributing distinctively to the visual mass and texture presented along the vehicle's side. Hand-in-hand with material is the finish applied; whether a matte texture designed for grip, a brushed metallic surface aiming for refinement, or a painted finish intended to blend, this layer is the most immediate point of visual interaction. However, the real test lies in how these finishes withstand daily abuse from road debris, weather, and constant foot traffic. Maintaining that initial presentation proves challenging, as scuffs, chips, and fading can quickly diminish the aesthetic contribution, revealing the critical need for materials and finishes selected not just for initial appeal but for their long-term resilience in a demanding environment.
When considering running boards as elements contributing to a vehicle’s overall presence, the selection and engineering of their surface treatments and constituent materials reveal interesting technical challenges and solutions aimed squarely at maintaining aesthetic integrity over time.
The resistance of modern running board finishes, particularly advanced polymer coatings, to environmental assault involves sophisticated material science. These aren't simply layers of paint; many employ complex cross-linked polymer networks designed to absorb impact energy from flung debris without fracturing and to create a robust barrier against corrosive agents like road salts or acidic rain, maintaining a consistent visual state despite harsh operating environments.
Achieving surfaces that actively repel dirt and water, thus contributing to a cleaner look with minimal effort, often relies on manipulating surface energy at a microscopic scale. Techniques borrowed from other fields create finely structured textures or incorporate low-surface-energy materials that promote superhydrophobicity. Water beads up and rolls off easily, carrying contaminants with it, a subtle engineering detail that directly impacts the board's presentation day-to-day.
Preventing the electrochemical drama that can unfold when dissimilar metals are in contact, such as where the running board attaches to the chassis, demands careful consideration of materials and interface layers. Specialized insulating materials or sacrificial coatings are strategically placed to manage galvanic corrosion potential, ensuring that structural integrity isn't silently compromised in a way that would eventually manifest as unsightly rust or mounting failures, detracting significantly from the vehicle's presentation.
For running boards or trim components made from aluminum, achieving durable, integrated color finishes often involves electrochemical anodizing. This process converts the surface layer of the metal into a porous oxide that is then dyed. The resulting finish isn't merely a coating sitting on top; it's integral to the metal substrate itself, offering inherent resistance to scratching and UV-induced fading far exceeding conventional paints or powder coats, although its final appearance is highly dependent on the specific aluminum alloy used.
Creating specific metallic sheens and colors on decorative running board elements frequently utilizes Physical Vapor Deposition (PVD). This process, conducted in a vacuum, allows for atomic-level deposition of thin films, yielding highly uniform and durable metallic finishes. It provides a means to achieve specific luxury or performance-oriented visual effects – from deep black chrome to lustrous satin – on complex shapes that might be difficult or less durable with traditional plating or painting, though care is still needed to avoid abrasive damage that penetrates the thin deposited layer.
Evaluating Truck Running Boards Function and Design - Function versus form the running board dilemma on customized truck builds
Customizing trucks often highlights the tension between what works and what looks good, nowhere more obviously than with running boards. Historically, these were straightforward, functional steps to help people get into a tall vehicle. Today, they're judged just as much on how they impact the truck's lines and stance. The trend leans heavily toward designs that minimize their visual impact or disappear altogether when not needed. While this satisfies the desire for clean aesthetics, it can raise valid questions about their primary purpose – are they still the most effective or convenient way to step up if they're narrow, awkwardly placed when deployed, or simply too high because the designer wanted them tucked up tight? The challenge for anyone building a personalized truck becomes navigating this duality, choosing a solution that fits their vision for the vehicle while genuinely serving its passengers.
Shifting focus to the technical repercussions within customized truck builds, the decision surrounding running boards introduces several less obvious engineering challenges and performance trade-offs often encountered when deviating from factory specifications. For instance, detailed Finite Element Analysis frequently highlights the mounting interfaces where running boards attach to the chassis or body structure as critically stressed regions, particularly when bespoke boards employ heavy-duty materials or the truck is subjected to higher loads or extreme off-road articulation beyond its original design intent. Furthermore, swapping factory boards for more robust, aftermarket options intended for protection can significantly increase the vehicle's unsprung mass; this addition directly influences how effectively the suspension manages wheel control and ride quality, potentially degrading the carefully tuned damping and handling characteristics inherent in the base platform, especially on performance-oriented customs. From an aerodynamic standpoint, the geometry and placement of running boards aren't solely about frontal area and simple drag; they can subtly alter airflow patterns along the truck's flanks, occasionally introducing unintended lift or asymmetrical forces that might compromise high-speed stability on lowered or performance-tuned configurations. On trucks specifically modified for demanding off-road exploration, fixed running boards, whether factory or aftermarket, frequently become critical contact points on obstacles, drastically reducing the effective break-over angle and risking substantial damage not only to the boards themselves but potentially the rocker panels and underlying frame members. Lastly, the chosen materials possess inherent vibrational characteristics; a poorly selected or mounted running board can act as an acoustic amplifier, picking up and transmitting road surface vibrations or turbulent wind noise directly into the cabin environment, introducing unwanted NVH (Noise, Vibration, and Harshness) on a long highway journey, detracting from the intended driving experience.
Evaluating Truck Running Boards Function and Design - Exploring the evolution of running board design beyond traditional steps for trucks
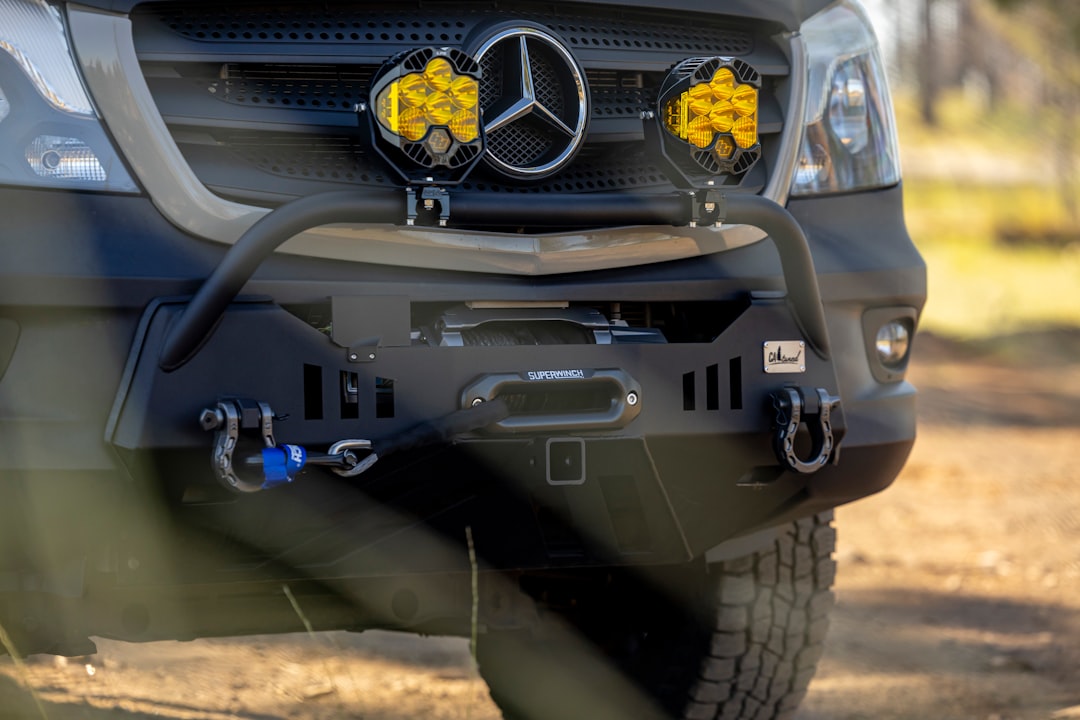
Examining the evolution of truck running boards shows a significant departure from their historical role as simple steps. This shift aligns with broader trends in automotive design and engineering, positioning these components as key elements in a vehicle's overall visual impact. The move involves embracing more sophisticated shapes and leveraging advanced materials designed for weight efficiency and improved aesthetic integration. Modern designs often incorporate functional refinements like deployment mechanisms or subtle illumination, effectively merging practical accessibility with a refined presence. The persistent design challenge remains reconciling the fundamental requirement for convenient entry and exit with the pursuit of the clean, flowing profiles that characterize contemporary truck styling.
Beyond their foundational role as aids for cabin access, the engineering behind contemporary truck running boards reveals layers of functionality often overlooked. Consider, for instance, the structural contribution some designs are now intended to provide in a side impact scenario. Rather than merely being attached elements, certain running boards, particularly those integrated closely with the vehicle's rocker panel structure, are engineered to manage and absorb collision energy. This isn't their primary safety restraint, but their calculated deformation or load transfer during a side crash is a demonstrable technical evolution from a simple stepping surface to an element playing a role in augmenting the vehicle's crashworthiness profile. It highlights a multi-functional design imperative now embedded in what might appear to be a simple exterior component.
Looking at the convenience aspect, the implementation of automated, power-retracting running boards often goes deeper than just concealing the step for aesthetics. The sequence of their deployment, their final height relative to the ground, and even the dwell time before retraction are frequently informed by extensive ergonomic research and analysis of passenger biomechanics. Engineers study how people of varying heights and mobilities step into a tall vehicle to define an optimal step height and position. While sometimes the aesthetic drive to completely hide the step leads to compromises in its ultimate deployed position or width, the underlying technical goal is to create a human-centered interface aiming for enhanced, data-driven accessibility.
Another less obvious technical evolution involves how running boards are utilized as discreet locations for integrating vehicle systems. In some modern truck designs aiming for exceptionally clean exterior lines, critical antenna modules used for radio communication, cellular connectivity, or keyless entry systems are subtly embedded within non-metallic segments or composite covers of the running boards themselves. This requires careful material selection to ensure radio frequency transparency and clever packaging engineering to protect sensitive electronics in a physically vulnerable location, solving a packaging challenge while preserving uninterrupted body surfaces elsewhere on the vehicle.
Furthermore, the fine-tuning of a running board's specific contour and surface texture can extend beyond managing simple aerodynamic drag. It can influence the vehicle's aeroacoustic performance. The precise shaping and even the porosity or texture of the surface material can be designed to disrupt or guide airflow in a way that reduces localized turbulence or wind noise generated along the truck's flanks, contributing directly to a quieter cabin environment at speed. This focus on noise reduction, driven by sophisticated computational aeroacoustics simulations and wind tunnel testing, represents a subtle yet technically demanding refinement aimed squarely at enhancing passenger comfort and the perceived quality of the vehicle experience.
More Posts from tunedbyai.io: