Fuel Injector Testing Near You What to Expect in 2024
Fuel Injector Testing Near You What to Expect in 2024 - Advanced OBD2 Scanning Technologies for Fuel Injector Diagnostics
Modern OBD2 scanners are increasingly sophisticated tools for diagnosing fuel injector problems, leading to better and faster repairs. These advanced scanners can measure fuel pressure with greater precision and allow for individual fuel injector activation, providing a detailed look at how each injector is performing. The ability to check for specific trouble codes within the fuel system allows mechanics to quickly isolate the root of the problem. Some scanners even support the complex process of injector coding, which is essential for certain vehicles.
The development of these advanced diagnostic tools is ongoing, and we can expect to see even more improvements in 2024 and beyond. The improvements to come likely include refined data analysis and more accurate interpretations of fuel injector health. This constant technological evolution makes staying current with OBD2 scanning advancements important for anyone who wants the most effective fuel injector testing available. This will undoubtedly influence the way fuel injector diagnostics are handled, leading to more reliable diagnoses and improved overall vehicle health.
Fuel injector diagnostics have been revolutionized by the integration of advanced capabilities within OBD2 scanners. We're now able to see fuel injector performance in real-time, during actual driving conditions. This real-time data streaming is proving especially valuable in uncovering issues that might be missed during standard, static tests. A major advance is the ability to perform fuel injector balance tests. These tests allow technicians to compare the flow rates of each injector, quickly identifying any imbalances that could impact engine performance.
Some OBD2 scanners are now equipped with guided diagnostic features. This effectively acts as a tutor, providing technicians with clear steps to diagnose and troubleshoot specific fuel injector related trouble codes. The shift towards more complex communication protocols, like Controller Area Network (CAN), has greatly expanded the scope of information available. This newer technology enables a much deeper level of insight into potential fuel injector failures than older, simpler diagnostic systems were capable of. Intriguingly, some manufacturers have developed OBD2 tools that can utilize historical data to predict potential fuel injector issues. This capability of predictive analytics is a huge step forward, allowing for proactive maintenance strategies that could prevent breakdowns.
One remarkable aspect of this technology is its adaptability to a vast range of engine control systems. This universal applicability means it's relatively easy to diagnose injector issues across numerous makes and models, thus streamlining the repair process for a wider range of vehicles. Some scanners are even incorporating machine learning algorithms. This is where the diagnostic tool essentially “learns” and improves its ability to detect fuel injector faults over time, allowing for greater adaptability to newer vehicle designs and emerging problems. Advanced OBD2 tools can also now remotely activate injectors for testing purposes. This means a technician can initiate injector operation directly during a diagnostic session, watching how it performs and confirming its proper function.
Beyond the immediate diagnostic scope, the data collected from OBD2 systems offers a broader perspective. By monitoring injector performance trends over extended periods, mechanics can build a more complete picture of vehicle behavior. This data becomes a crucial resource for implementing effective preventative maintenance programs. Finally, while we typically associate injector failures with engine performance issues, they can trigger problems in other parts of the system, as well. For example, faulty injectors can trigger errors and issues with components like catalytic converters, which are also monitored via OBD2. It is fascinating how interconnected these systems are. As of October 2024, it's clear that ongoing advancements in OBD2 technology are paving the way for even more efficient, precise, and comprehensive fuel injector diagnostics, further improving our ability to both maintain and repair these critical engine components.
Fuel Injector Testing Near You What to Expect in 2024 - New Cleaning Methods Beyond Chemical Treatments
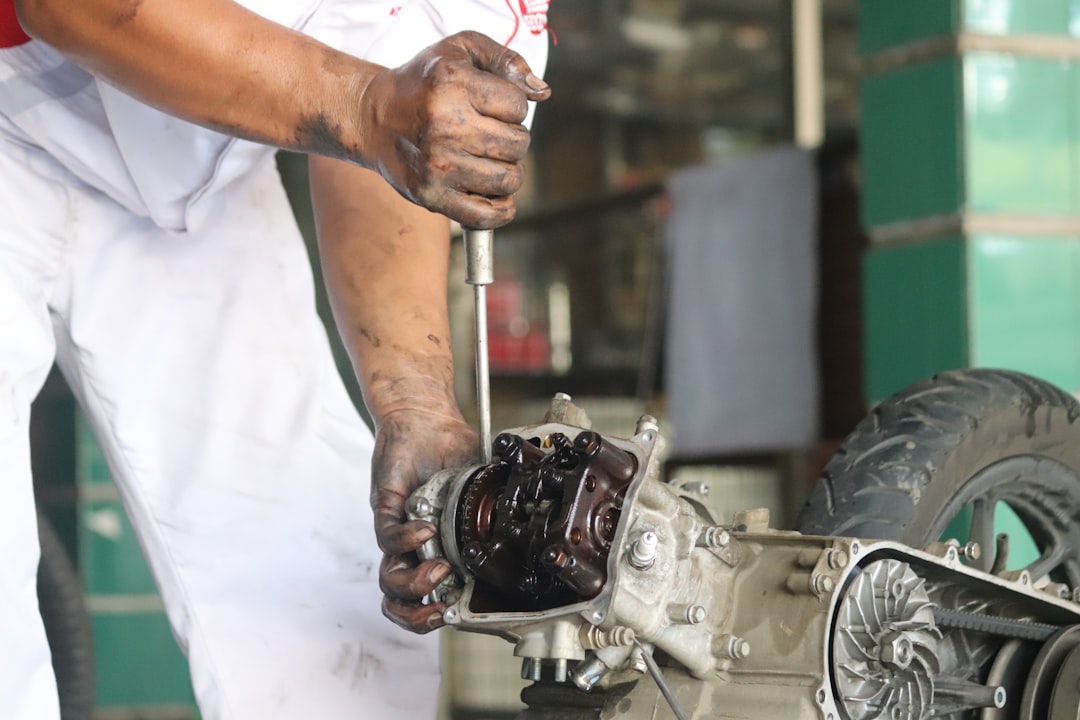
While chemical treatments have long been the standard for cleaning fuel injectors, new approaches are emerging that offer different cleaning methods. One promising advancement is ultrasonic cleaning, where high-frequency sound waves are used to remove stubborn deposits and blockages without having to physically remove the injector. This technique can provide a deeper clean compared to traditional methods. Another interesting development is reverse cleaning. In this process, the fuel flow is reversed through the injector, effectively flushing out contaminants and debris.
These new approaches, while promising, each have advantages and drawbacks. It's becoming increasingly important for vehicle owners and mechanics alike to understand these alternatives. Making informed decisions about cleaning methods will likely play a greater role in maintaining the health of a fuel injection system, especially as we move further into 2024. As fuel injector technology and cleaning approaches evolve, choosing the right cleaning method becomes more important for ensuring proper and efficient fuel delivery, which is fundamental to a vehicle's overall performance and reliability.
While chemical treatments have long been the standard for fuel injector cleaning, researchers and engineers are exploring alternative methods that promise better results and reduced environmental impact. These new approaches are fascinating because they address the limitations of traditional chemical cleaners, which can sometimes be harsh or leave behind residues.
One promising avenue is ultrasonic cleaning, where high-frequency sound waves agitate a cleaning solution to dislodge contaminants from injector components. The intricate nature of injectors makes this technique especially attractive as it can access hard-to-reach areas, leading to a more thorough cleaning.
Dry ice blasting is another intriguing concept. Dry ice pellets are propelled at high speeds towards the injectors, causing them to sublimate on impact. The rapid sublimation helps break up and dislodge stubborn deposits while leaving no moisture residue.
Microwave-assisted cleaning also shows potential. Microwaves can be used to heat cleaning solutions, accelerating the chemical reactions that break down contaminants. This technique can speed up the cleaning process and reduce the reliance on harsher chemical agents.
Laser cleaning is an emerging technology that employs high-powered lasers to remove carbon and other deposits from fuel injectors with precision. The highly targeted nature of laser cleaning makes it ideal for delicate components.
Plasma cleaning is another option that utilizes ionized gas to clean surfaces. Plasma interacts with contaminants, causing them to break down and release from the injector. This method is useful for prepping injector surfaces prior to repairs, ensuring optimal adhesion for coatings or repairs.
Bio-enzymatic cleaners leverage the power of naturally-occurring enzymes to break down oil and grease. This approach is environmentally friendly and can be particularly effective at lower temperatures, needing less energy compared to conventional cleaners.
High-pressure water jetting provides a chemical-free option for cleaning various substrates. The intense force of water jets dislodges debris and buildup without resorting to harsh chemicals.
Electrolytic cleaning is another approach that relies on an electrical current to generate chemical reactions to break down contaminants, mainly on metal surfaces. This can effectively clean injectors without aggressive mechanical scrubbing and harmful chemicals.
Supercritical CO2 cleaning uses CO2 in a supercritical state to dissolve and remove contaminants. This dual role as both a solvent and a cleaning agent makes it especially effective for intricate parts.
Finally, sonic cavitation utilizes the formation and collapse of bubbles in a liquid through ultrasonic vibrations. These collapses create shock waves that break apart contaminants, offering a potent method for chemical-free cleaning.
These alternative methods are still being explored and refined, but they offer promising alternatives to traditional cleaning methods. If successful, these new methods may offer a way to clean fuel injectors more effectively, while also minimizing any adverse environmental impact or harmful chemical exposure. It's exciting to see how these novel techniques will shape the future of fuel injector cleaning.
Fuel Injector Testing Near You What to Expect in 2024 - Improved Balance Testing Techniques for Precise Injector Flow Measurement
The importance of accurate fuel injector flow measurement is becoming increasingly clear in 2024, particularly as engines become more sophisticated. Improved balance testing techniques are now at the forefront of diagnosing injector problems, allowing for much more precise assessments. These new techniques aim to measure the fuel delivered by each individual injector with greater accuracy, helping pinpoint any issues early on. Modern testing often involves evaluating injector performance in real-world driving situations, offering a more comprehensive understanding of how they function. However, not all injectors are created equal—direct injectors, multiport systems, and others each require specific testing protocols. Luckily, technology advancements are making it easier to adapt to these various needs and create a more precise testing environment for all injector types. These new testing techniques have the potential to transform how fuel injector maintenance is handled, and could become an essential tool in extending the life and improving the performance of fuel injection systems moving forward.
Fuel injector balance testing is becoming increasingly crucial for understanding how well injectors deliver fuel, especially as engines get more complex. We're now able to detect very slight differences in fuel flow, even down to less than a 1% variation in how each injector performs. This kind of fine-grained analysis is essential to squeeze every drop of efficiency out of an engine and ensure smooth operation.
It's also become clear that fuel temperature has a big influence on how injectors work. Newer balance testing approaches factor in the effects of temperature changes, so the flow measurements we get are closer to what happens in real-world driving situations. This should result in more accurate assessments of injector health, ultimately leading to better repairs.
One advancement in balance testing is the use of pulse width modulation (PWM). PWM mimics how an engine controls fuel delivery, and testing with it lets us see how quickly and consistently each injector responds to changes in the electrical signal it receives. This offers a much more complete picture of an injector's overall capability.
Ultrasonic flow meters are another fascinating addition to fuel injector testing. They measure the flow of fuel without needing to take the injector apart, which is great because it's faster and reduces the risk of damage. The ability to get precise measurements without invasive procedures is a notable improvement.
We're also seeing balance testing techniques shift toward gathering data in real-time. This means we can watch how an injector performs during operation, which is vital because some problems might not show up during a simple, stationary test. Continuous monitoring of injector behavior is a valuable diagnostic tool.
The benefits of regular balance testing extend beyond just diagnosing problems. By spotting and correcting minor flow irregularities before they cause bigger issues, we can actually extend the lifespan of the injectors themselves. Catching minor discrepancies early helps prevent larger, more costly repairs later on.
Automation is playing a bigger role in calibration processes related to balance testing. Automated systems help make sure each injector is performing within the manufacturer's specifications. This reduction in human involvement in the process helps prevent errors and standardizes testing.
Another interesting development is the use of machine learning algorithms in analyzing injector flow data. These algorithms can spot patterns that might hint at future injector performance problems, allowing for preventative maintenance. Predictive maintenance can be a game-changer for preventing unexpected breakdowns and maximizing engine reliability.
It's important to recognize that fuel injectors don't operate in a vacuum. Modern balance testing looks at how injectors impact the rest of the fuel system, including things like pressure regulators and fuel pumps. This holistic view allows for a more complete understanding of the overall fuel system's health.
Finally, the improved balance testing techniques we're seeing today are incredibly versatile. They can work with a wide array of fuel types and injector designs, which means they can be used for both older and newer vehicles. This adaptability is essential for maintaining a diverse fleet of cars and trucks effectively.
As of October 2024, it's clear that advancements in balance testing techniques are continuing to enhance our ability to thoroughly diagnose and understand how fuel injectors are performing. These improvements have the potential to optimize engine efficiency, reduce maintenance costs, and increase the lifespan of these critical components.
Fuel Injector Testing Near You What to Expect in 2024 - Emerging Repair Solutions for Previously Irreparable Injector Damage
In the realm of fuel injector repair, we're witnessing a shift towards innovative solutions that can address previously considered irreparable damage. New technologies like ultrasonic cleaning are providing deeper cleaning capabilities, removing stubborn deposits and blockages more effectively than older chemical methods. Furthermore, advanced testing techniques, including those that utilize pulse width modulation, are now able to assess injector performance with unprecedented precision. These assessments, coupled with newer balance testing methods, are revealing subtle flow inconsistencies and providing a more comprehensive view of injector health. It's becoming increasingly possible to diagnose and repair injectors that were previously thought to be beyond repair.
The inclusion of machine learning and the ability to monitor fuel injector behavior in real-time during driving conditions offers an exciting new dimension to diagnostics. Predictive maintenance, enabled by these innovations, allows for proactive intervention and potentially prevents major breakdowns. While these novel repair approaches are undeniably promising, a crucial factor for vehicle owners is understanding their limitations. Carefully weighing the potential benefits and drawbacks of these emerging methods is essential to achieving optimal fuel system health and efficiency, moving forward in 2024.
The landscape of fuel injector repair is evolving, moving beyond the limitations of what was once considered irreparable. Previously, certain damage like cracks and significant wear often meant replacement, but emerging solutions are offering new pathways to restoring injectors to working order. Novel epoxy blends and specialized welding techniques are allowing for repairs that could potentially extend the life of these vital components.
The realm of 3D printing is also starting to impact injector repairs. By using this technology, engineers can create customized replacement parts with intricate designs, overcoming some traditional manufacturing constraints. This could lead to better-performing injectors that are specifically tailored to different engine requirements.
Nanotechnology is showing promise in improving injector performance during repair. By incorporating nanomaterials, it's possible to create smoother surfaces within the injector at a microscopic level, which can lead to more efficient fuel flow.
We're also seeing the early stages of what could be termed "smart injector" technology. Modern injectors are starting to integrate self-diagnostic capabilities, giving mechanics real-time insights into injector issues. This type of built-in intelligence could revolutionize how repairs are carried out, with technicians gaining a more direct understanding of the problems and the optimal fixes.
Electrochemical surface treatments are offering a new approach to injector repairs. Using these techniques, injector surfaces can be treated to better resist contaminants and corrosion, resulting in repairs that are likely to last longer compared to older methods.
An interesting development is the application of machine learning algorithms to predict injector failures. By analyzing historical data patterns, technicians can potentially anticipate problems before they occur. This proactive approach has the potential to decrease vehicle downtime and potentially reduce the cost of repairs by catching issues before they escalate.
The field of fuel injector repair is becoming more multi-faceted as well, with a growing trend toward hybrid repair techniques. These approaches combine traditional mechanical repairs with newer technologies, aiming for better overall results. This combined strategy could ultimately lead to a higher rate of success in returning damaged injectors back into service.
Microfluidics, which studies fluid behavior at the microscopic level, is starting to play a role in advancing injector repair methods. With such precise analysis, it may be possible to identify subtle issues that might otherwise be missed, enabling more effective repair solutions.
Diagnostic tools are evolving, now incorporating elements of cognitive capability. These newer tools not only evaluate injector performance, but also "learn" from previous repair attempts. This continuous improvement could lead to a streamlined repair process, with faster and more accurate outcomes.
Finally, significant strides in material science are impacting injector repairs. New alloys and composites are under development with the potential to create stronger, more resilient, and potentially lighter injector parts. This could further improve overall engine performance and efficiency.
While many of these emerging repair solutions are still in the development phase, they hint at a future where injector repairs are more effective, efficient, and potentially more environmentally friendly. It will be fascinating to see how these innovations impact fuel injector repair in the coming years.
Fuel Injector Testing Near You What to Expect in 2024 - Integration of AI-Driven Diagnostic Systems in Fuel Injector Testing
In 2024, we're seeing a shift in fuel injector testing with the increasing integration of AI-powered diagnostic systems. These systems allow for continuous monitoring of injector performance, providing insights into their operational status. They often utilize a mix of data-driven and theoretical models, creating a way to diagnose issues in real-time without needing to physically interfere with the injectors. This is particularly important as we encounter more complex injection designs like common rail and direct fuel injection found in many modern vehicles. These systems are being developed to predict the impact of an injector's performance on overall engine efficiency.
While this is an exciting development, the ability of AI systems to be effective hinges on how well they can adapt to the wide range of vehicle types and engine control systems currently in use. The practical application of these technologies is crucial: can technicians readily use them to improve engine performance? We'll need to see how easily accessible and usable these tools are for the average mechanic. The goal, of course, is to use these advancements to enhance the overall engine performance and diagnostics that benefit vehicle owners.
The integration of AI into fuel injector testing signifies a notable shift towards more sophisticated diagnostic capabilities. We're seeing a move from relying solely on experience and traditional methods to a data-driven approach where AI algorithms analyze complex patterns in injector performance. This allows for more nuanced assessments of how injectors are working, capturing subtle variations that might have been missed before.
One exciting aspect is the potential for predictive maintenance. AI-driven systems can sift through vast amounts of historical data to predict potential injector failures, essentially giving us a heads-up about potential problems. These systems learn and adapt over time, improving their predictive abilities through machine learning. The hope is that this could lead to proactive maintenance strategies that prevent breakdowns and extend the lifespan of these crucial engine components.
These new systems are also equipped with powerful error detection mechanisms. By quickly analyzing large datasets, these tools can spot minute discrepancies in injector performance, leading to more reliable diagnoses and repairs. Additionally, they're enhancing the ability to visualize data, making it easier for technicians to understand injector health and performance.
The impact extends beyond just the injectors themselves. These AI-powered tools are capable of monitoring the entire fuel system, recognizing the interactions between injectors, pumps, and pressure regulators. This more holistic perspective is valuable for identifying potential cascading failures or interconnected problems.
Automation in the calibration process, driven by AI, is another area showing improvement. This helps standardize testing and reduces the risk of human error during calibration procedures. Interestingly, AI-driven systems also enable real-time control during testing, allowing technicians to adjust variables and observe the impact instantly.
Furthermore, these systems are demonstrating an aptitude for recognizing fault patterns that repeat across various vehicle makes and models. This can lead to a more standardized approach to diagnosing and fixing problems, potentially speeding up repair times. As these systems continue to be used, they accumulate knowledge about successful repair strategies, building a robust knowledge base that enhances future diagnostics.
It's promising to see the potential for broader compatibility across vehicle types and brands. The aspiration is to develop AI-driven diagnostic systems that can be used seamlessly in various repair shops, creating a more standardized approach for injector testing and troubleshooting. This has the potential to improve service efficiency and accessibility for a wider range of vehicles.
The integration of AI into fuel injector diagnostics is shaping a new era of engine maintenance. While the technology is still developing, it suggests a path towards more efficient, reliable, and proactive approaches to engine health. It's exciting to witness how this technology will continue to evolve and contribute to a better understanding of fuel injection systems, ultimately benefiting vehicle owners and mechanics alike.
Fuel Injector Testing Near You What to Expect in 2024 - Rising Costs and Pricing Trends for Fuel Injector Services
The cost of maintaining a vehicle's fuel injection system is steadily climbing as we approach the latter part of 2024. Basic services like cleaning fuel injectors typically fall within a range of $60 to $150, though comprehensive services that include throttle body cleaning can easily jump to $250 to $300. The price of replacing fuel injectors is particularly variable, with simple fixes like an electrical repair potentially costing as little as $10, but a more extensive replacement potentially topping $1,000. Replacement of individual injectors on average is about $1,033 which includes part and labor, however that can be highly dependent on vehicle and complexity of replacement. The costs can fluctuate greatly based on a number of factors, including the type of vehicle and the scope of the repair, making budgeting for fuel injection services more difficult. Fortunately, advancements in testing and diagnostic tools can lead to earlier detection of issues, which might ultimately help minimize future repair costs. It's becoming increasingly important for drivers to be aware of these evolving costs and to explore potential preventive measures offered by local repair facilities.
The expenses related to fuel injector services are subject to a variety of factors, ranging from general market trends to the specific technology involved in repairs. One notable driver of fluctuation is the increasing sophistication of diagnostic equipment. As these tools become more advanced, the mechanics using them need more specialized training, pushing up labor costs.
The type of fuel injection system in a vehicle also has a significant impact on service prices. For instance, direct fuel injection systems—which are becoming increasingly common—tend to be more complex, requiring specialized tools and potentially driving up the service cost. We see the effects of inflation and supply chain pressures on fuel injector services too. Rising costs of materials, including metals like aluminum and stainless steel, directly influence the price of replacement injectors and the overall cost of repairs.
It's also worth considering that location impacts fuel injector service costs. Labor rates tend to be higher in cities and metropolitan areas due to a number of economic factors, such as higher overhead and greater competition. In contrast, rural areas might have lower service prices due to a different economic climate and possibly lower overhead costs.
Service providers are employing various strategies to attract customers, including offering longer warranties and service guarantees, which can factor into overall pricing. This increased warranty coverage reflects the growing intricacy of fuel injection systems and the desire to instill consumer confidence. The diagnostic process itself is getting more intricate, needing more time and labor. This has led to a rise in the complexity of the service, directly impacting the pricing structure providers use.
The decision to utilize either original equipment manufacturer (OEM) or aftermarket parts for repairs has a direct effect on cost. OEM parts tend to be more reliable, but they often come with a higher price tag, ultimately impacting the total service cost. The incorporation of newer technologies like AI in diagnostics, while offering greater accuracy, can initially inflate service prices. This is due to the costs involved in purchasing and maintaining these more advanced systems, and the need for specialized training to effectively utilize the technologies.
Interestingly, as drivers gain a greater understanding of fuel injector maintenance, a shift towards proactive, preventive services is taking place. This can lead to higher costs for preventative services, offsetting some of the overall service cost fluctuations seen in the market. Fuel injector services can also experience seasonal variations in demand, reflecting typical driving habits and weather patterns. To counter these changes, service providers often adjust their pricing in response to changes in demand. In essence, the fuel injector service landscape is dynamic, subject to technological evolution, economic factors, and consumer behavior, all shaping the cost and pricing trends we observe today.
More Posts from tunedbyai.io: