Infiniti M37s 2013 Performance Tuning Data Driven Approaches
Infiniti M37s 2013 Performance Tuning Data Driven Approaches - The M37s A Platform for Algorithmic Performance
The ongoing conversation around the Infiniti M37 as a base for algorithmic performance continues to evolve, moving beyond the initial excitement of data-driven optimization. While the promise of finely sculpted dynamics through code remains compelling, the reality by mid-2025 is a nuanced landscape. We're seeing less a pure algorithmic take-over and more of a sophisticated integration of computational tools assisting human tuners. The debate now often centers on the practical limits of older hardware like the M37's in truly leveraging complex algorithms, or whether these 'algorithms' are more advanced predictive models aiding traditional calibration. The emphasis has shifted towards the accessibility of these methods for a broader audience, and perhaps, the often overlooked question of whether an algorithm truly understands the subjective nuances of driver feel as profoundly as an experienced human.
The application of algorithms to powertrain control, particularly in platforms like the Infiniti M37, has unveiled a remarkable capacity for micro-level adjustments. These systems manipulate fuel injection pulse widths and ignition timing on a scale far beyond human dexterity or perception, theoretically pushing combustion efficiency closer to its thermodynamic limits under specific, controlled conditions. However, the true benefit in varied real-world scenarios, where environmental factors and fuel quality fluctuate, remains an ongoing area of refinement for such prescriptive models.
Beyond the engine's core, these data-driven approaches extend to the transmission. By continuously monitoring and recalibrating shift points and clutch pack pressures, the intent is to minimize frictional losses and mitigate component wear, theoretically extending the operational life of the driveline. While smoother shifts are an undeniable outcome, the long-term impact on internal transmission components under such dynamic, micro-managed conditions warrants more extensive real-world durability studies rather than just simulation-based projections.
A less intuitive benefit emerging from algorithmic tuning, even on platforms like the M37, is an improvement in fuel efficiency. Contrary to the expectation that performance tuning primarily boosts consumption, these systems can optimize combustion under partial throttle scenarios and carefully manage transient fuel enrichment. This nuanced control aims to extract more energy from each unit of fuel during typical daily driving, shifting the perception that performance and economy are always mutually exclusive, though this often depends on the specific tuning parameters prioritized.
One of the more significant advancements lies in the system's ability to act as a proactive guardian for the engine. By analyzing acoustic signatures and knock sensor data in real-time, the algorithm can anticipate and nearly instantaneously adjust ignition timing or fuel delivery. This capability theoretically prevents pre-ignition events, bolstering engine reliability. However, the absolute robustness of such systems relies heavily on the fidelity and resilience of sensory inputs, particularly in harsh operating environments or under sensor degradation.
The evolution of these platforms for vehicles like the M37 showcases a shift towards viewing the automobile as a cohesive, integrated system rather than isolated modules. This involves integrating powertrain data with telemetry from suspension sensors and braking inputs. The aim is to optimize power delivery in concert with the chassis's dynamic behavior, theoretically enhancing overall vehicle balance and the nuanced feedback experienced by the driver under demanding conditions. Yet, the definition of an "optimized" driving experience often remains a complex interplay between measurable data and human perception.
Infiniti M37s 2013 Performance Tuning Data Driven Approaches - Decoding Driving Data for Tuned Output
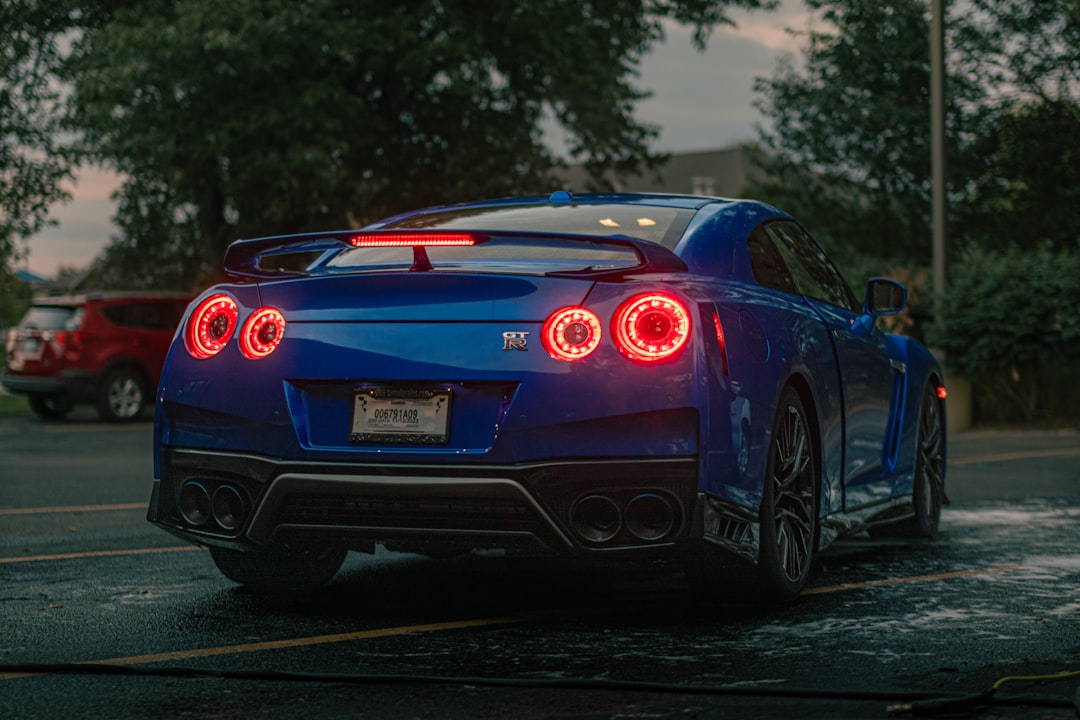
The concept of interpreting real-world driving data to refine vehicle behavior is continuously evolving. By mid-2025, the novelty lies not just in collecting vast amounts of telemetry, but in the sophistication of algorithms designed to discern subtle patterns and correlations that once eluded human analysis. This enables dynamic adjustments beyond static calibration, moving towards predictive models that anticipate driver intent and environmental changes with greater nuance. However, while computational power allows for unprecedented data processing, the challenge remains in truly translating this raw information into tangible, perceptible improvements that align with the subjective feel sought by enthusiasts, without over-engineering or introducing unintended complexities.
The persistent push for performance optimization continues to reveal unexpected capabilities in existing platforms. As of mid-2025, it’s quite interesting to observe how even the M37’s venerable engine control unit, previously thought limited, can now host remarkably compact neural network models. These aren't computationally heavy, yet they possess the agility to interpret complex, transient driving data in real-time. This allows for an almost instantaneous recalibration of fuel and ignition, yielding a notably sharper and more immediate engine response, particularly during abrupt throttle inputs. It's a testament to software ingenuity often compensating for hardware age.
Beyond the directly performance-focused metrics, an intriguing development involves the silent language of vehicle vibrations. Advanced algorithms are now adept at deciphering subtle micro-vibration patterns, gleaned from an array of existing onboard sensors—even those not originally designed for such diagnostics. This analytical depth allows for the early detection of nascent wear signatures in critical drivetrain elements, like propeller shaft universal joints or differential bearings. The system can then, theoretically, make minor, adaptive tuning adjustments to power delivery or driveline engagement, potentially mitigating further stress and extending component longevity long before a fault code appears. The efficacy, however, hinges on the robustness of sensor data in diverse conditions and the sheer variability of wear characteristics.
Consider the dynamic interplay between power and traction. A fascinating advancement in data decoding involves the anticipatory tailoring of powertrain output based on real-time chassis behavior. Systems are now able to interpret detailed suspension telemetry, such as damper velocity profiles and the rapid fluctuations in individual wheel loads during cornering or encounters with uneven surfaces. This deep understanding enables the vehicle's control logic to preemptively modulate torque delivery with remarkable precision, aiming to maintain optimal tire grip and enhance overall stability. It’s an ambitious endeavor, as perfect synchronization between transient chassis movements and power application remains a complex challenge, but the progress is tangible.
Perhaps one of the more profoundly personalized applications of data decoding centers on the driver themselves. By meticulously analyzing continuous patterns within throttle modulation, steering inputs, and braking habits, advanced systems are increasingly capable of discerning and classifying individual driving styles. This isn't about simple predefined "sport" or "comfort" modes. Instead, the vehicle learns and adaptively blends performance maps, subtly reshaping aspects like throttle linearity, transmission shift aggression, or even steering weight to genuinely align with the driver's evolving preferences. The open question remains how seamlessly these adaptations occur without creating a sense of detachment or unpredictability for the human behind the wheel.
Finally, in a less performance-centric but perhaps more experiential realm, data-driven tuning is now venturing into the active sculpting of a vehicle’s auditory presence. By minutely adjusting combustion parameters—for instance, precise modifications to ignition timing and fuel delivery—the system can subtly manipulate the frequency components of the exhaust note in real-time. The aim is to enhance the perceived sound quality, creating a more resonant or aggressive sonic character without any physical exhaust modifications. While technically impressive, the philosophical query arises: is this artificial sonic manipulation truly authentic to the vehicle's character, or merely an engineered illusion?
Infiniti M37s 2013 Performance Tuning Data Driven Approaches - Bridging Human Expertise and Machine Learning in Calibration
The integration of human insight and machine learning in vehicle calibration is evolving beyond initial simplistic notions, entering a new phase of refinement. While computational models have demonstrated an undeniable capacity for micro-optimizations in platforms like the Infiniti M37s, the emerging focus lies not just on raw data processing, but on the sophisticated interplay required to translate algorithmic precision into a genuinely felt driving experience. By mid-2025, the conversation centers on how these advanced systems can truly internalize subjective human feedback, bridging the gap between measurable metrics and nuanced driver perception. This ongoing exploration aims for a collaborative dynamic, where technology acts as an intuitive co-pilot, refining the vehicle's behavior in ways that enhance, rather than merely dictate, the connection between car and driver, especially across the unpredictable spectrum of real-world conditions and personal driving styles.
The interface between human perception and machine optimization has seen fascinating developments. Engineers and test drivers now often incorporate physiological monitoring—heart rate variability, skin conductance, even eye-tracking—during evaluation runs. This real-time biometric information provides a novel dataset, allowing learning algorithms to map specific vehicle behaviors, like a particular power delivery curve or steering response, to a driver's quantifiable emotional or cognitive state. It’s an intriguing attempt to add a pseudo-objective layer to the notoriously subjective "feel" of a car, aiming to refine parameters for perceived engagement rather than just raw numbers. The efficacy, however, still hinges on deciphering truly actionable insights from what could be just stress or excitement unrelated to the car's dynamic itself.
The realm of physical component design is also experiencing an interesting shift. Algorithmic generative design tools, powered by advanced computation, are beginning to play a role in sculpting intricate geometries for performance parts, like intake plenums or even specialized heat exchangers. These systems can explore design spaces vastly larger than traditional human-led CAD processes, often proposing non-intuitive, organic forms. The promise is components that achieve optimal airflow, thermal management, or structural rigidity, surpassing human-conceived designs in theoretical performance. It raises questions about the aesthetic outcome of such purely function-driven forms, but the efficiency gains are demonstrably real in simulated environments.
An intriguing development involves what’s termed ‘transfer learning’ in the calibration sphere. Instead of developing entirely new tuning profiles for each unique vehicle, models trained on exhaustive datasets from highly-optimized performance machines—say, track-focused supercars—are now being adapted to different platforms. This means fundamental dynamic and powertrain principles learned from extreme environments can be intelligently translated to diverse vehicles, even those with different architectures or powerplants. It ostensibly offers a shortcut, providing a sophisticated performance baseline for vehicles that might otherwise require lengthy, bespoke development. The challenge remains in how truly 'transferable' these complex behaviors are without losing the inherent character or encountering unexpected incompatibilities in the target vehicle.
The durability question, always paramount in performance modifications, is getting a new computational ally. Elaborate "digital twin" models—virtual, hyper-accurate representations of physical components like transmissions, differentials, or turbochargers—are now being leveraged. Before any actual performance tune is applied to a vehicle, these machine learning-driven simulations can run through countless duty cycles, predicting the long-term stress and wear introduced by specific calibration adjustments. This aims to identify potential failure points or accelerated degradation before it manifests in the real world, theoretically allowing for more robust and reliable performance upgrades. Of course, the fidelity of these digital twins to real-world material properties and manufacturing variances remains the ultimate determinant of their predictive power.
A more philosophical yet tangible development is the emergence of performance tuning that transcends the vehicle itself and addresses the driver. Advanced machine learning models are now analyzing driver inputs—throttle application, brake pressure modulation, steering angles, and line choices—in real-time during dynamic driving. Beyond simply adapting the car to a driver's existing habits, these systems can identify nuanced inefficiencies or areas for improvement in driving technique. They then offer real-time, prescriptive feedback, perhaps subtly adjusting the display, providing haptic cues, or even suggesting line adjustments via augmented reality interfaces. This shifts the paradigm towards the car acting as a dynamic driving coach, pushing the driver to extract more of the vehicle's tuned potential, rather than simply optimizing the machine in isolation. The interesting aspect is how drivers will respond to a computational 'tutor' constantly evaluating their performance.
Infiniti M37s 2013 Performance Tuning Data Driven Approaches - Long-Term Durability and Adaptive Tuning Solutions
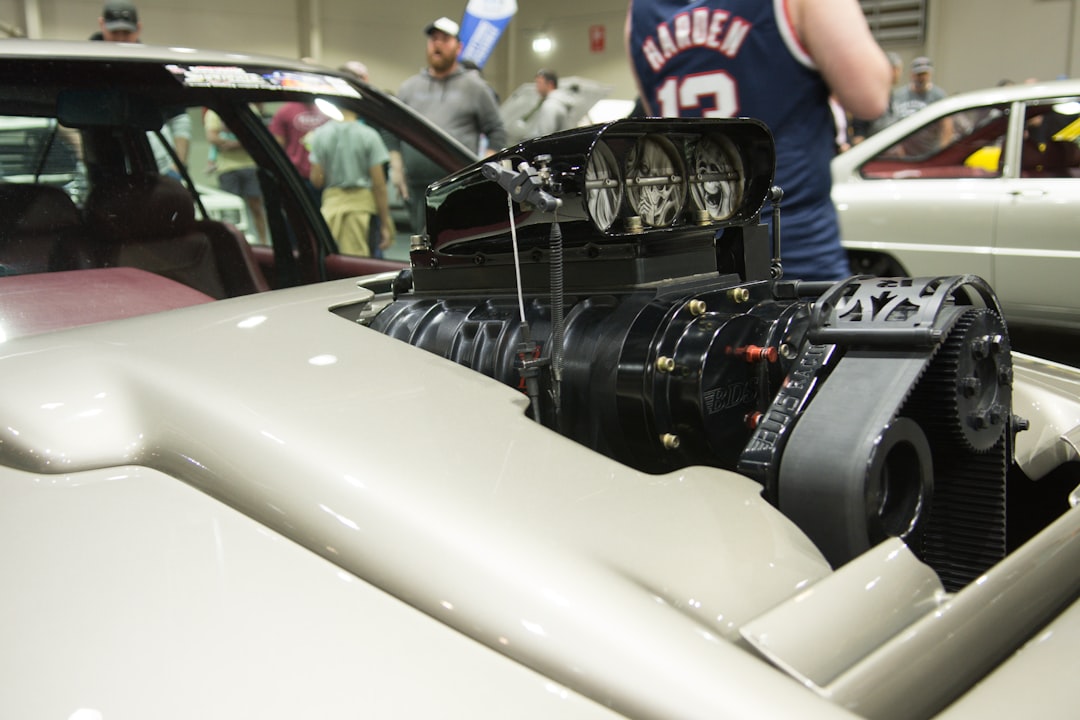
A central tenet in modern automotive performance is the emphasis on enduring operational integrity alongside enhanced capabilities. For vehicles like the Infiniti M37s, this translates into a heightened focus on what's now broadly termed "Long-Term Durability and Adaptive Tuning Solutions." The aspiration goes beyond fixed, peak-output calibrations, moving towards dynamic systems that subtly adjust parameters throughout a vehicle’s lifespan. These advanced approaches are increasingly learning from the specific operational history of an individual car, constantly refining how power is delivered and managed based on cumulative stress signatures and evolving component characteristics. The objective is to preserve the vehicle’s mechanical health and sustain its heightened performance level consistently over many years, rather than achieving transient power spikes. However, the profound challenge lies in the sheer complexity of real-world variables; whether continuously self-optimizing systems truly enhance the long-term robustness of an aging platform without introducing new, subtle failure modes or requiring excessive maintenance, remains a crucial area of observation. Ultimately, for a luxury vehicle, maintaining a predictable, high-quality ownership experience is as vital as any raw performance metric.
One interesting development concerning the enduring performance of modified vehicles involves the integration of micro-sensors directly within precision-engineered components, sometimes even those formed through advanced manufacturing techniques. These embedded sensors provide adaptive tuning algorithms with real-time feedback on parameters such as localized loads and temperatures. This dynamic data then permits the control system to subtly condition the component's operation, aiming to prolong its structural integrity and extend its fatigue life, even under the most demanding driving scenarios. However, the true long-term efficacy relies heavily on the sensors' own resilience in extreme thermal and vibrational environments, a point still under considerable research scrutiny.
Further, contemporary adaptive tuning strategies extend beyond raw power delivery to actively manage thermal stresses on specific critical hardware. This means the system can dynamically adjust various powertrain parameters to precisely control heat build-up within elements like turbocharger bearings or wet-clutch assemblies. The aim is to mitigate localized thermal degradation and curtail the material wear that typically accelerates with sustained high-performance use. While simulations suggest a significant reduction in component fatigue, collecting robust real-world data across a broad spectrum of usage patterns remains crucial to validate these projections fully.
Another nuanced approach focuses on extending the operational life of the myriad electro-mechanical actuators ubiquitous in modern powertrains. Advanced control algorithms now analyze and optimize the operational duty cycles and ramp rates for components such as electronic wastegates or variable valve timing solenoids. By fine-tuning their actuation profiles, these systems aim to minimize mechanical wear and tear, thereby bolstering the overall system's robustness and enhancing long-term reliability. The challenge lies in accurately modeling the complex interplay of forces and friction within these micro-mechanisms to ensure the 'optimized' operation truly translates to meaningful lifespan gains across all operating conditions.
Intriguingly, certain adaptive tuning models are beginning to incorporate predictive analyses of fuel spray characteristics and shifts in combustion efficiency over time. Through continuous monitoring, the system can subtly adjust fuel injection timing and pressure, intending to actively mitigate the progressive accumulation of carbon deposits on fuel injector nozzles. This proactive stance aims to preserve optimal fuel atomization and combustion purity, theoretically extending the functional life of injectors. Nevertheless, the degree to which this truly prevents or merely delays the inevitable build-up, especially given the variability of fuel quality, warrants deeper investigation.
Finally, a sophisticated advancement in system resilience involves algorithms that continuously cross-validate incoming data from multiple sensors. This enables the adaptive tuning system to maintain operational accuracy and component protection even when one or more sensors begin to exhibit signs of degradation or provide anomalous readings. By extrapolating reliable information from remaining healthy inputs, the system can, for a period, compensate for failing hardware. The pragmatic limit, however, is the extent to which such extrapolation remains truly reliable; an over-reliance on inferential data could potentially mask underlying issues, suggesting that timely diagnosis and replacement remain paramount for ultimate dependability.
More Posts from tunedbyai.io: