PureSpeed Concept Redefines Mercedes AMG Design and Tuning
PureSpeed Concept Redefines Mercedes AMG Design and Tuning - Examining the PureSpeed Styling Direction
Turning our focus now to the visual aspect, the PureSpeed concept's styling direction warrants close examination. This segment aims to unpack the design choices made, considering how they position this vehicle within the evolving landscape of high-performance luxury aesthetics and whether they truly break new ground or merely adapt existing trends.
Observations concerning the vehicle's exterior treatment reveal several notable technical approaches:
The integrated roll protection structures, while serving their primary safety function, exhibit a visible, tightly controlled carbon fiber laminate. The decision to leave this structural composite exposed beneath a clear protective coating appears to deliberately position material composition itself as a key visual element, blending the inherent mechanical properties with the sculpted form. It's an interesting statement on transparency in design.
Analysis of the upper body surfaces highlights an unexpected level of micro-engineering. Reportedly shaped through extensive computational fluid dynamics analysis, the subtle variations in surface curvature – including localized depressions and raised sections – are intended to actively manage airflow dynamics specifically over the cockpit region. This suggests a complex, almost 'invisible' aerodynamic function embedded directly into the form language, seeking performance gains through seemingly minor surface manipulations.
A specifically developed surface coating, described as being infused with nanoparticles, goes beyond conventional paint. Beyond its apparent visual depth and luster, its technical specification includes an exceptionally low coefficient of surface friction. This suggests a direct attempt to derive measurable, albeit likely small, aerodynamic benefits from the paint surface itself, presenting the exterior finish as an active, engineered layer rather than passive coloring.
Critical functional elements necessary for performance, such as ventilation inlets or targeted airflow guides, appear to be largely integrated into the overall sculptural flow of the bodywork. This approach utilizes advanced internal channeling to route air, seemingly prioritizing the preservation of clean exterior lines. While effective for visual purity, the engineering challenge of embedding such functional requirements without compromising efficiency or adding excessive complexity is significant.
PureSpeed Concept Redefines Mercedes AMG Design and Tuning - Concept Design and its Connection to AMG Evolution
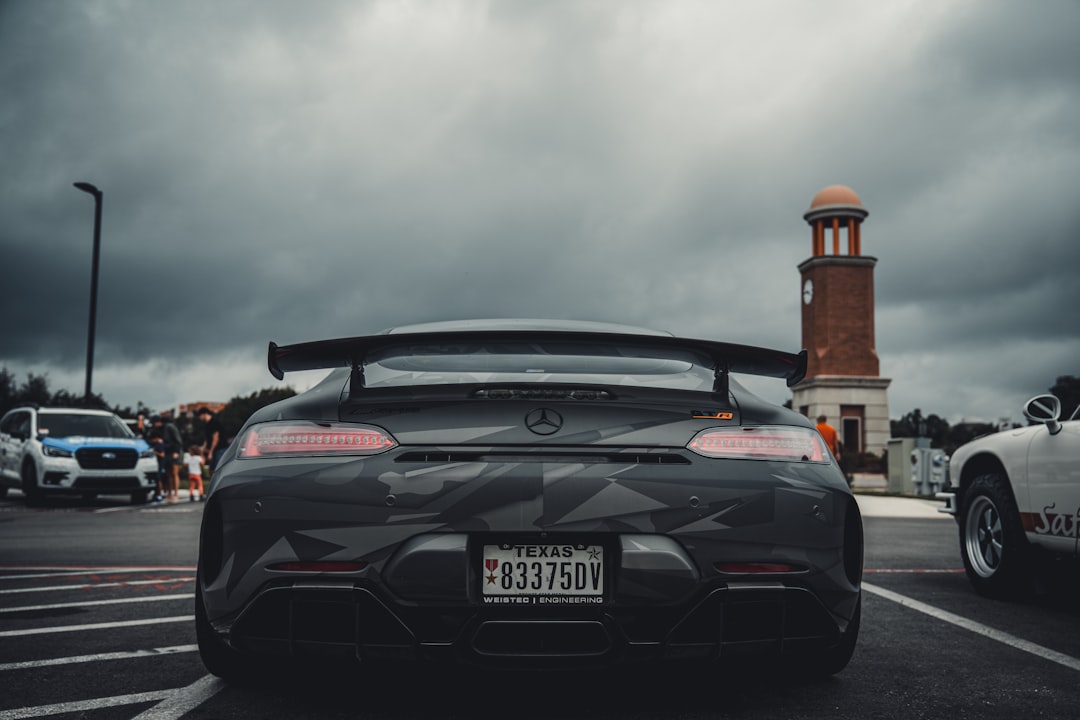
Concept design serves as a vital testbed for AMG as it navigates the evolving landscape of high-performance luxury. Projects like the PureSpeed aren't just about exploring new shapes; they represent an intent to forge a closer relationship between aesthetic ambition and engineering reality. The aim appears to be the creation of vehicles where every aspect, from the foundational structure to the minute details, serves a clear purpose while contributing to a striking overall presence. This approach suggests a desire for a certain level of transparency in design – where functional elements are not hidden but potentially celebrated as part of the visual identity – though achieving this balance without compromise is challenging. By integrating forefront thinking in areas like material use and airflow management into these concept explorations, AMG is signalling its potential future direction, pushing the boundaries of what's considered possible for a luxury performance machine. It will be insightful to see how effectively the principles showcased in such concepts ultimately translate into production vehicles and genuinely influence the broader conversation around automotive design at the highest level.
Future AMG concept development often starts its life purely within high-fidelity computational environments. Utilising complex physics models, engineers can undertake extensive simulation and validation across areas including nuanced aerodynamic performance, structural integrity under extreme loads, and even early driver-vehicle interface ergonomics, all before any physical component is manufactured. This rigorous virtual phase provides crucial, data-driven insights into system interactions and overall performance characteristics, allowing for rapid, iterative refinement long before committing to expensive hardware.
A key methodology in probing the boundaries of potential future designs involves the routine employment of advanced additive manufacturing. This allows for the rapid prototyping of complex, often lattice-like or intricately channeled structural components using exotic materials, directly testing the feasibility and real-world performance of incorporating such designs into future production vehicles for critical weight reduction and functional integration benefits. These processes enable geometries simply not achievable through conventional subtractive methods, continually pushing engineering limits.
Many concept vehicles are deliberately engineered to serve as critical testbeds for validating extreme thermal management architectures and sophisticated energy recovery systems, especially those tailored for the demanding power densities and unique heat loads associated with high-output hybrid and future electric propulsion systems. Testing these under simulated demanding conditions provides vital operational data on cooling loop efficiency, power electronics behaviour, and overall system performance consistency, directly informing the core engineering backbone of upcoming models navigating this powertrain transition.
Beyond immediately visible wings or diffusers, a number of design elements in AMG concepts feature adaptive or multi-stage active aerodynamic systems, including dynamic internal ducting and movable underbody components. These are developed to continuously optimize airflow management across a wide operational spectrum for varied requirements like cooling, downforce, or drag reduction. The performance mapping and real-time response data gathered from these complex systems are invaluable, significantly influencing the more refined active aero packages that eventually appear in production cars.
Exploring how to maximise stiffness while minimising mass, concepts frequently incorporate radical structural carbon fiber integration methods directly into primary load-bearing structures, such as the chassis monocoque or suspension hardpoints. This involves rigorous testing of novel manufacturing techniques, bonding processes, and composite layups under extreme simulated and real-world load conditions. The aim is to gather empirical data on composite durability and performance benefits that are fundamental to the lightweighting and torsional rigidity strategies of future high-performance vehicle platforms, extending composite use well beyond purely aesthetic applications.
PureSpeed Concept Redefines Mercedes AMG Design and Tuning - Considering Technology Platforms in the Context of Design Concepts
Considering technology platforms within the realm of automotive design concepts has shifted considerably. It's no longer merely about packaging existing tech; the underlying digital and physical infrastructure now actively shapes the aesthetic and functional vision from the outset. This influence extends from software-defined user interfaces fundamentally altering interior layouts to advanced manufacturing techniques enabling previously impossible exterior forms. For high-performance and luxury vehicles, this means the engineering blueprint is inherently intertwined with the visual narrative. The challenge lies in ensuring these powerful platforms serve the design intent meaningfully, pushing boundaries without design becoming purely a byproduct of technological capability rather than creative expression.
Let's consider how the underlying technological infrastructure influences the design process itself in these concepts. Beyond traditional sculpting and material choices, the computational platforms employed are becoming generative tools in their own right. Advanced algorithms, fed with specific performance parameters – perhaps aerodynamic targets or structural stiffness requirements in certain zones – can now propose intricate, often counter-intuitive forms for elements. These aren't just minor tweaks; the software essentially invents shapes optimized purely for function, which then present novel challenges and opportunities for the aesthetic language.
Furthermore, the increasing reliance on sophisticated sensor arrays, crucial for various system functionalities, places unusual demands on exterior surfaces. Integrating elements like high-frequency radar or LiDAR means specific areas of the bodywork, including their precise curvature and even material composition, must be carefully engineered to allow these sensors to operate unimpeded, often requiring solutions that avoid visually disruptive openings. This forces designers and engineers into subtle compromises or innovative material layering to maintain a clean aesthetic while ensuring critical data flow.
There's also noticeable exploration into dynamic materials for external applications. Conceptually validated surfaces capable of altering properties – whether momentary textural changes or shifts in colour under specific conditions – are being investigated. This moves the exterior away from being merely static cladding towards potentially becoming an active, responsive interface element, presenting interesting questions about durability, control systems, and driver interaction paradigms.
Underpinning much of this is the extensive use of real-time 'digital twin' environments. These aren't just static computer models but live simulations mirroring the physical prototype. Bidirectional data flow between the actual car and its virtual counterpart enables exceptionally rapid iterative development. Engineers can virtually alter a design parameter and immediately see its simulated impact on the physical test data, or vice-versa, allowing complex integrated systems to be refined at a pace previously unachievable, short-circuiting traditional development loops.
Finally, the idea of incorporating haptic feedback directly into external body panels represents a perhaps less obvious but technologically complex direction. Imagine surfaces capable of subtle vibration or pulsation to convey information or warnings. This requires rethinking the fundamental engineering of exterior panels and their substructures to accommodate actuation and control systems, adding another layer of complexity to the seemingly simple outer skin of the vehicle. These are all fascinating areas where the pursuit of function, enabled by cutting-edge technology platforms, directly shapes the form in unexpected ways.
More Posts from tunedbyai.io: