The Complete Breakdown of Front Brake Service Costs
The Complete Breakdown of Front Brake Service Costs - Dissecting Component Costs High Performance Versus Standard Applications
The discussion around front brake service costs has evolved considerably, especially when contrasting components for high-performance vehicles against those for standard applications. While the fundamental difference in cost due to superior stopping power and durability remains, recent advancements have introduced new layers of complexity. For today's luxury and supercar platforms, we're seeing an accelerating integration of braking systems with complex vehicle electronics and advanced material science. This isn't just about exotic pads and rotors anymore; it encompasses bespoke thermal management, adaptive braking software, and materials optimized not just for raw stopping force but also for whisper-quiet operation and specific feedback nuances crucial to the modern high-end driving experience. This ongoing innovation, while delivering unparalleled control and safety, often dictates more intricate manufacturing processes and highly specialized servicing protocols, pushing the cost envelope further. Conversely, the standard brake market has also seen shifts, with some materials improving but generally still prioritizing affordability over extreme performance under stress. For those tuning their machines or simply maintaining a finely crafted vehicle, navigating these increasingly divergent pathways of component costs and technological requirements is more critical than ever.
From an engineering perspective, a deeper dive into performance braking components reveals several intriguing aspects often overlooked in general discussions.
First, consider the behavior of carbon-ceramic matrix (CCM) rotors at extreme temperatures. Unlike their steel counterparts, these composites demonstrate an remarkably low coefficient of thermal expansion. This characteristic is crucial, as it allows the rotor to retain its structural integrity and shape even when glowing incandescently at temperatures exceeding 1,000°C. The practical upshot is a significant mitigation of brake fade, which is a common challenge when steel rotors deform or expand excessively under similar thermal loads, leading to inconsistent braking force.
Second, the composition of high-performance brake pads is a fascinating study in material science. Rather than simple organic compounds, these pads incorporate intricate multi-metallic or ceramic-metallic formulations, bound together by highly specialized polymers. The engineering objective here is to maintain a remarkably stable coefficient of friction across an exceptionally broad temperature spectrum and under immense shear forces. This is a non-trivial feat, ensuring reliable stopping power whether the brakes are cold at the start of a drive or scorching hot after repeated, aggressive applications, a performance envelope where standard formulations would simply lose their effectiveness.
Third, the manufacturing precision of performance brake calipers presents a stark contrast to typical mass-produced units. Many are not merely cast but are instead precision-forged or meticulously CNC-machined from single blocks of aerospace-grade aluminum. This demanding fabrication process yields a caliper with significantly enhanced structural rigidity—often cited as upwards of 30% stiffer than conventional cast designs. This increased stiffness is not an aesthetic choice; it directly translates to minimizing flex under the extreme hydraulic pressures generated during heavy braking, contributing to a more consistent and direct pedal feel, and ensuring all brake force is effectively transmitted to the pad.
Fourth, the impact of lightweight components, specifically the switch from conventional cast iron to carbon-ceramic composite rotors, on vehicle dynamics is quite pronounced. This transition can reduce unsprung mass by a substantial margin, often cited between 50% to 70% per wheel. For a curious engineer, this is a profound change. Less unsprung weight allows the suspension to react more swiftly and effectively to road imperfections, keeping the tire in more consistent contact with the asphalt. This, in turn, theoretically translates to improved grip levels and a noticeable enhancement in overall dynamic handling and vehicle responsiveness. One might ponder the diminishing returns for typical road use, but on a track, the difference is undeniable.
Finally, the properties of high-performance brake fluids, frequently either DOT 5.1 or non-DOT racing specific, are critical to sustained performance. These fluids often rely on advanced polyglycol ether formulations to achieve remarkably high wet boiling points, often well in excess of 200-260°C. This elevated boiling point is a direct countermeasure against vapor lock, a critical failure mode where standard fluids, with their lower boiling points, would boil under the extreme heat generated during intense braking, forming compressible gas bubbles that lead to a sudden loss of pedal pressure and braking ability. The trade-off, however, often involves a greater hygroscopic nature, demanding more frequent fluid changes for optimal performance.
The Complete Breakdown of Front Brake Service Costs - The Nuance of Labor Fees for Tuned Vehicle Brake Service
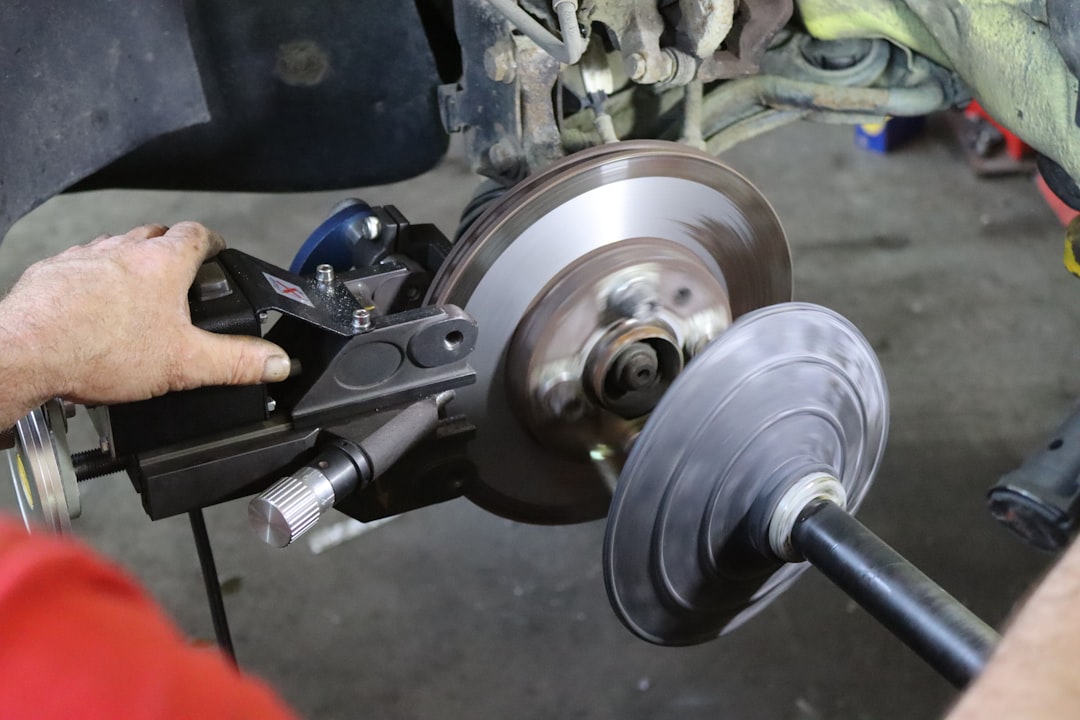
For vehicles that have undergone significant performance enhancements, particularly those with custom tuning, the cost associated with front brake service often carries an unacknowledged premium in labor. As of mid-2025, these advanced braking systems found on luxury and supercar platforms, often intertwined with intricate vehicle software, demand a level of diagnostic skill and installation precision far exceeding what’s typical for conventional vehicles. Technicians aren't merely replacing components; they are frequently engaging with sensitive electronic sensors, specialized bleeding procedures for complex ABS or stability control systems, and ensuring exact tolerances when dealing with lightweight or advanced material components. This heightened meticulousness, which is essential for preserving the vehicle's unique dynamic characteristics and ensuring safety, inevitably translates to extended shop time and requires a more specialized, often factory-trained, workforce. Consequently, the hourly rate for such specific expertise, combined with the sheer time investment, forms a significant, yet often underestimated, portion of the total expenditure, a point discerning owners must factor into their financial planning for such bespoke machines.
Here are some observations about the nuanced labor fees for tuned vehicle brake service:
1. Servicing modern performance braking systems, deeply integrated with vehicle ECUs, mandates extensive software recalibration of integrated dynamics control and driver-assistance features. This re-synchronization is not merely procedural; it's critical for restoring the engineered balance of braking force distribution and stability management, particularly at performance limits. An engineer would view this as vital for maintaining designed system behavior.
2. Labor costs are significantly elevated by the absolute necessity for specialized, often manufacturer-exclusive, diagnostic and calibration equipment. These proprietary tools are indispensable for intricate sensor alignment and complex system integration, tasks fundamentally beyond generic workshop apparatus. This exclusivity presents a notable barrier, contributing directly to higher labor rates, reflecting the significant capital investment and limited access.
3. A measurable portion of labor is dedicated to the precise "bedding-in" of new pads and rotors. This controlled thermal and mechanical conditioning, a scientific process, optimizes the tribological interface by carefully forming material transfer layers. Neglecting this meticulous preparation compromises the engineered friction characteristics, accelerating wear, or inducing NVH issues, thereby diminishing the system's intended performance envelope.
4. Achieving the rigorous, sub-micrometer runout and parallelism tolerances demanded by performance rotors requires meticulous labor. This involves painstaking measurement, precise hub cleaning, and often specific shimming to ensure the rotor is perfectly seated. From an engineering standpoint, this level of geometric accuracy is paramount to prevent pulsations, vibrations, and maintain consistent brake torque delivery, especially under extreme loads.
5. Ultimately, the specialized labor rate reflects the profound, continuous scientific and technical expertise required from certified technicians. Servicing these complex systems demands a deep understanding of electro-mechanical interactions, exotic material behaviors, and advanced diagnostic methodologies. This dynamic knowledge base necessitates ongoing, rigorous training, representing an investment in highly specialized human capital crucial for maintaining optimal system functionality.
The Complete Breakdown of Front Brake Service Costs - Unpacking the Ancillary Costs Beyond Pads and Rotors
Beyond the widely discussed cost of high-performance brake pads, rotors, and the specialized labor to install them, the true financial landscape of front brake service for luxury and tuned vehicles encompasses a range of less obvious ancillary costs. Owners of these sophisticated machines should anticipate expenses tied to the precise disposal of advanced, sometimes hazardous, materials, the complex logistics of sourcing exceptionally rare components across global supply chains, and the comprehensive system-wide evaluations necessary to ensure all integrated vehicle dynamics remain precisely as engineered. This consideration extends beyond the immediate component fitment, delving into environmental responsibilities and the inherent complexities of low-volume, high-value part procurement. Ultimately, the total outlay for maintaining these engineering marvels includes not just the hands-on work and part acquisition but also a broader array of hidden charges that reflect the vehicle's unique demands.
The electronic wear indicators on many high-performance braking systems have evolved beyond basic open-circuit triggers. By mid-2025, it's common to see designs incorporating multi-stage resistance changes or even Hall effect sensors, enabling the vehicle's control unit to estimate remaining pad life with greater precision rather than simply indicating imminent failure. From an engineering standpoint, this provides valuable predictive maintenance data, yet the complexity and calibration requirements mean these bespoke components, typically non-reusable, contribute noticeably to the service bill. One might question the cost-benefit for a component whose primary function is so fundamental.
Securing high-stress brake assemblies often relies on torque-to-yield (TTY) fasteners, particularly for caliper mounts and occasionally for wheel hubs. These bolts are fundamentally designed to operate within their plastic deformation zone upon initial installation, achieving an incredibly precise and consistent clamping load. This engineered preload is crucial for resisting the immense dynamic forces experienced during braking. However, by their very nature, they are single-use items; once tightened, their material properties are permanently altered, mandating replacement to prevent potential fatigue cracks or compromised structural integrity. This specific requirement, though critical for safety and performance, often comes as an unstated expense.
Despite their outward durability and braided steel reinforcement, the inner PTFE (polytetrafluoroethylene) lining of performance brake hoses is not entirely immutable. Over extended periods or intense use, it can exhibit microscopic permeation, allowing minuscule amounts of fluid to escape, and even subtle volumetric expansion under repeated pressure cycles. This gradual degradation, while often imperceptible until advanced, compromises the hydraulic system's rigidity, leading to a less direct pedal feel and potentially affecting fluid composition. As a result, engineers frequently advise their proactive replacement to preserve critical hydraulic efficiency and maintain consistent feedback, even if outwardly undamaged.
What might appear as simple dust shields on high-performance brake setups are, in fact, sophisticated thermal management devices. Beyond deflecting road grime, their geometry is meticulously designed to channel airflow, facilitating heat dissipation from the rotor and caliper, and to act as a radiant barrier. Constructed from specialized high-strength alloys or, in some cases, advanced composites, these seemingly minor components are crucial for shielding nearby suspension arms, ball joints, and wheel bearing assemblies from temperatures that can easily exceed 300°C. Their complex engineering and material costs often go unappreciated until their replacement becomes necessary.
The final crucial step in servicing these advanced braking systems, particularly those using low-viscosity, performance-oriented fluids, often demands specialized, precise deaeration equipment. Simply gravity or pump-bleeding often proves insufficient. Such apparatus employs controlled vacuum or pressure to meticulously extract not just gross air pockets, but also dissolved gases and microscopic air bubbles from within the hydraulic fluid. An engineer understands that even these minuscule voids significantly reduce the fluid's bulk modulus, directly translating to an undesirably "spongy" pedal feel and a critical loss of hydraulic efficiency, especially as fluid temperatures rise under severe braking. This seemingly minor process is anything but, and it adds to the specialized tooling overhead.
The Complete Breakdown of Front Brake Service Costs - Market Forces and Material Prices in Mid-2025 Affecting Brake Service
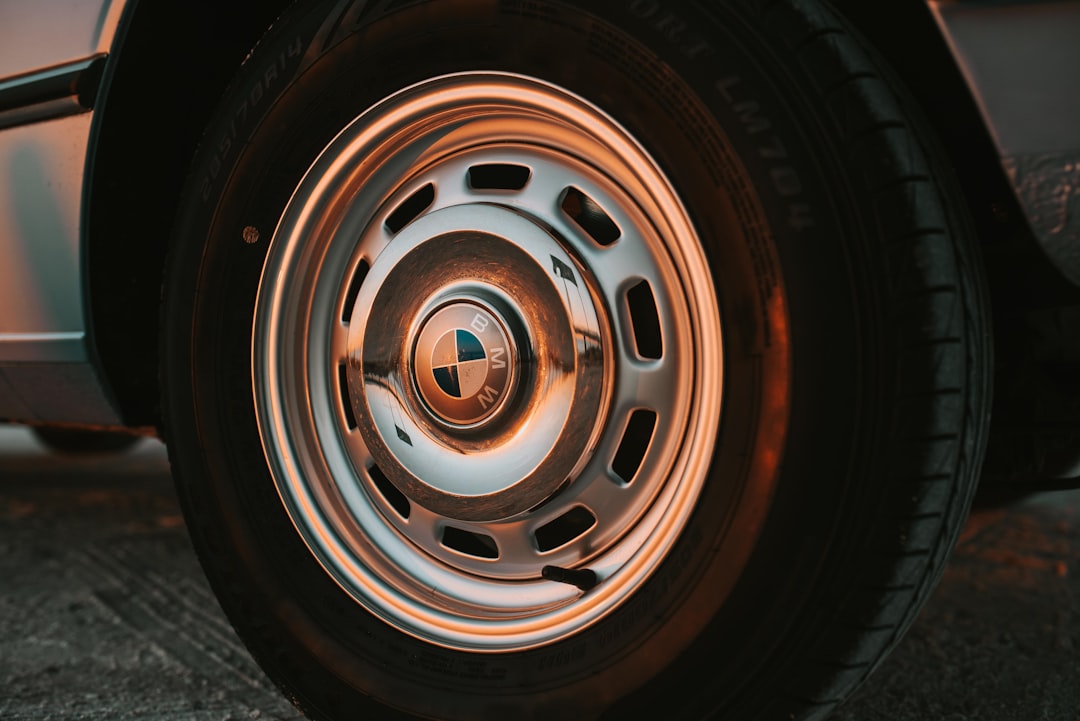
Looking ahead into mid-2025, the economic currents continue to exert considerable influence on the cost landscape of brake service, especially for the high-performance and luxuriously designed vehicles that demand top-tier components. We are observing a persistent volatility in the global commodity markets, impacting everything from specialized metal alloys used in high-strength calipers to the rare earth elements incorporated into advanced friction materials. This isn't merely about inflation; it's a complex weave of geopolitical factors, constrained mining outputs for niche materials, and an often-underestimated increase in demand for next-generation automotive platforms, all contributing to an upward pressure on component pricing. For owners and enthusiasts of bespoke or tuned machines, this translates directly into a higher outlay for the essential maintenance of their sophisticated braking systems, demanding a recalibration of financial expectations for what was once a relatively predictable service.
By mid-2025, the global pivot towards copper-free brake friction materials, driven by environmental mandates aimed at reducing metallic runoff into water systems, has fundamentally reshaped the materials market for performance pads. The necessity of replacing copper, a long-standing constituent, has intensified the search for and subsequently elevated the cost of alternative, often more exotic, compounds such as various titanates and refined ceramic oxides. This isn't merely a material substitution; it's a re-engineering effort that adds a notable premium to the final component.
Producing carbon-ceramic brake rotors, a process demanding multi-day thermal cycling at temperatures exceeding 1,800°C, remains inherently energy-intensive. We've observed a substantial increase in their manufacturing overhead—roughly an 18% climb in direct costs over the last two years alone. This spike appears largely inseparable from the fluctuating, and often high, global prices for industrial natural gas and electricity, underlining how foundational energy economics directly translates into specialist automotive component pricing.
Ongoing geopolitical shifts globally have created discernible instability in the supply chains for specific critical alloying elements, notably vanadium and cobalt. These are not merely esoteric materials; they are fundamental to the integrity of high-strength steels and specialized coatings found in high-performance calipers and rotor surfaces. Such external disruptions inevitably lead to unpredictable escalations in raw material costs and, perhaps more critically for development timelines, extended lead times, injecting significant uncertainty into the production pipeline.
A curious market dynamic has emerged with the expansion of electric vehicles. Their unique braking demands, prioritizing exceptional corrosion resistance and minimal noise, vibration, and harshness due to less frequent friction braking via regenerative systems, have ironically begun to compete directly for the same high-performance, quiet composite materials also desired by manufacturers of luxury internal combustion engine vehicles. This shared demand for specialized, low-NVH friction formulations effectively drives up material costs for both, despite their fundamentally different powertrain architectures. It’s an intriguing cross-sector material squeeze.
The availability of advanced, high-temperature thermoset polymers, which serve as crucial binding matrices within high-performance brake pads to ensure structural integrity and stable friction properties, is increasingly constrained. This scarcity is largely fueled by escalating demand from other high-tech sectors, particularly aerospace and defense, which require similar performance characteristics from these specialized resins. Since early 2024, this cross-industry competition has led to a noticeable 10-15% increase in the material cost for these foundational pad constituents, reflecting a broader competition for highly engineered raw materials.
More Posts from tunedbyai.io: