The Evolution of Pulley Systems in Modern Supercar Design A Look at San Antonio's Influence
The Evolution of Pulley Systems in Modern Supercar Design A Look at San Antonio's Influence - From Ancient Mechanisms to Modern Marvels The History of Pulleys in Cars
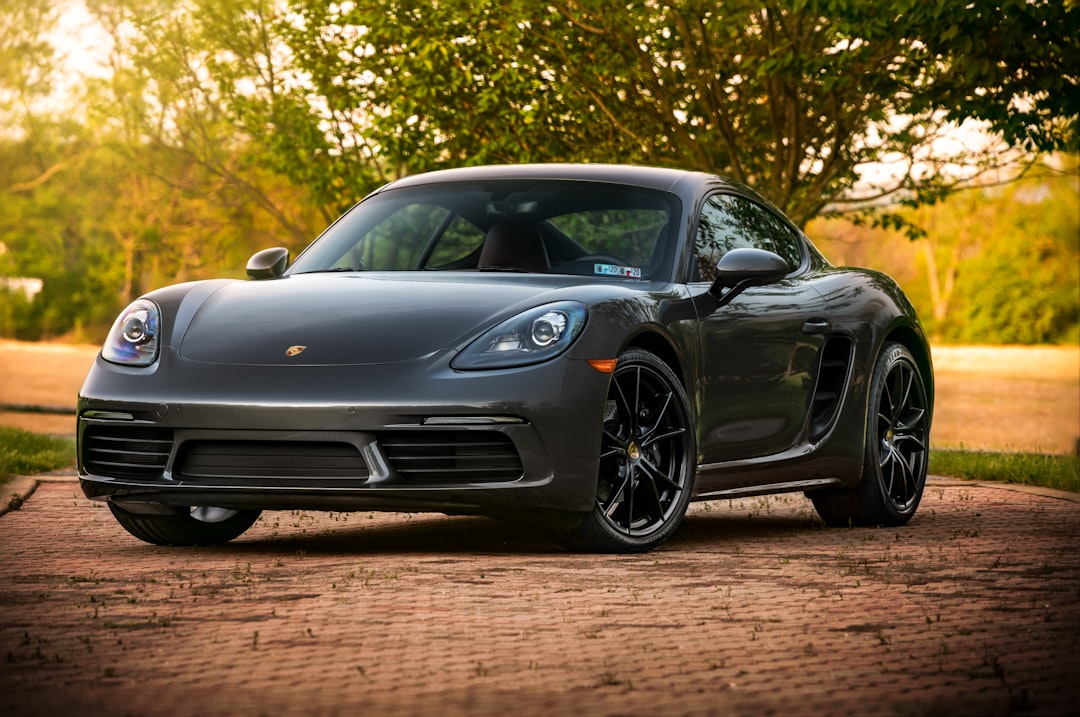
The journey of the pulley, a fundamental element of mechanical systems, stretches back to the dawn of human ingenuity. Its origins are intertwined with the need to manipulate heavy objects, evident in early cranes that relied on this simple yet powerful principle. Archimedes, with his famous proclamation about moving the Earth, highlighted the immense potential of pulleys to overcome physical limitations. Throughout history, pulleys have been harnessed for diverse tasks, including hoisting heavy loads, managing irrigation, and even facilitating theatrical performances.
Modern supercar engineering has embraced this ancient technology, reimagining it for enhancing performance. Sophisticated pulley systems in these vehicles demonstrate a fascinating marriage of historic principles with cutting-edge design. Locations like San Antonio have played a crucial role in refining pulley technology, influencing the direction of automotive engineering, especially within the sphere of high-performance vehicles. This continuous development, driven by the pursuit of greater efficiency and power, exemplifies how the ingenuity of the past can shape the future of automotive design. The pulley's journey illustrates the enduring power of fundamental mechanical concepts in addressing modern engineering challenges, a testament to humanity’s relentless drive to optimize and innovate.
The journey of the pulley, a seemingly simple mechanical device, stretches back millennia. Evidence suggests its use in ancient Mesopotamia, specifically in construction projects like the impressive ziggurats, revealing its early importance in enabling ambitious human undertakings. This foundational technology, along with its connection to the development of cranes, firmly established its role as one of the essential "mechanical powers" crucial for lifting and moving heavy loads.
Archimedes' theoretical insights provided further impetus to the understanding of pulleys. His famous claim of moving the Earth with enough pulleys, while perhaps hyperbolic, underscores the concept of mechanical advantage inherent in these systems. This advantage, allowing a smaller force to lift a larger weight, proved invaluable throughout history, from hoisting goods to intricate irrigation systems and even the theatrical machinery of ancient theaters.
As automotive technology evolved, particularly in the pursuit of ever-higher performance, pulley systems found a new stage. Supercars, driven by the relentless demand for enhanced performance, employ complex multi-vee pulley systems to optimize engine output, especially when dealing with high torque applications and the need to reduce slippage. The clever implementation of dual-pulley systems in some supercharger setups provides a compelling example, offering a rapid boost response that eliminates much of the typical turbo lag—a feature particularly beneficial on the race track.
The unique engine configurations of supercars, such as the increasingly popular flat-plane crank V8 designs, present fascinating engineering challenges. Pulley systems must be meticulously designed in these instances to maintain rotational balance while simultaneously extracting maximum power. This precision engineering extends to the realm of car tuning, where enthusiasts leverage lighter aftermarket pulleys to decrease the rotational inertia of the engine. This modification improves acceleration and offers a perceptible performance bump.
The sonic landscape of supercars is another area where pulleys play an indirect, but important, role. The careful orchestration of belt-driven accessories like alternators and water pumps, influenced by pulley design, creates the signature sound that contributes to a supercar's distinctive character.
Modern design tools like CAD are revolutionizing pulley design. This allows for intricate models that have led to innovations like variable diameter pulleys, which can alter their size based on engine load. These dynamic pulleys enable even greater performance and responsiveness by optimizing the engine's efficiency under a broader range of operating conditions.
The pursuit of optimal performance and weight reduction has also driven the increasing use of advanced synthetic materials in pulley production. High-performance plastics and composites now play a vital role, offering improved durability and reduced weight while enduring the harsh environment found within modern supercar powerplants.
Despite being largely hidden from view, pulley systems remain a critical component of modern supercar design. They are not just functional parts; they are often subtly incorporated into the car's overall aesthetic. In some cases, visible belt systems are even showcased under transparent covers, offering a glimpse into the fascinating internal workings of the car.
The history of the pulley is a testament to humanity's enduring ingenuity. From its ancient beginnings as a facilitator of impressive construction projects to its critical role in modern supercar engineering, this simple mechanical marvel continues to inspire and demonstrate how we can harness basic principles to solve complex problems and push the boundaries of what's possible.
The Evolution of Pulley Systems in Modern Supercar Design A Look at San Antonio's Influence - San Antonio's Contribution to Supercar Pulley Innovation
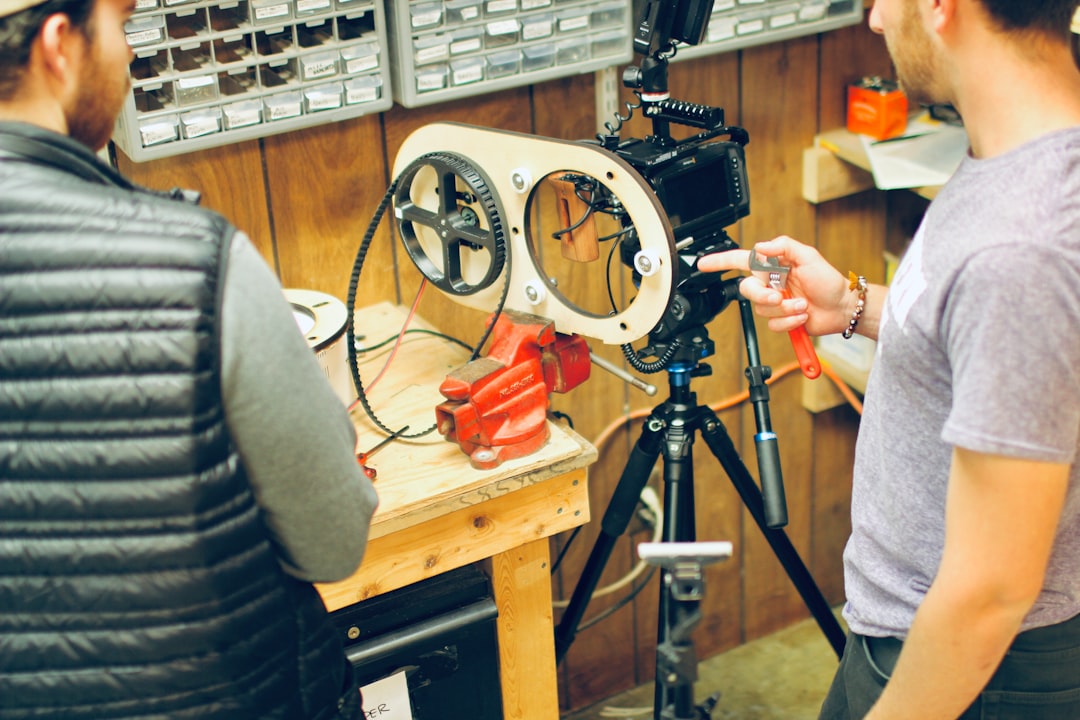
San Antonio has played a notable role in the progression of pulley systems, specifically within the realm of supercar development. The area has blended classic engineering principles with advanced technologies to refine lightweight, efficient pulley designs that enhance high-performance vehicle output. This forward-thinking approach is noticeable in the adoption of cutting-edge materials and dynamic pulley configurations, leading to engines that are both responsive and efficient. With auto manufacturers continually striving for greater speed and power, San Antonio's contribution to pulley technology underscores the critical value of flexibility and clever design within the automotive field. This continuous evolution, a mixture of historical know-how and current demands, propels the engineering of supercars forward. The influence is evident in the development of new pulley materials and the design of highly-tuned engine components within today’s luxury and high-performance vehicle market. While San Antonio may not be immediately associated with the supercar industry, its engineering insights have helped shape the technology that powers these impressive machines. The evolution of pulley technology, often hidden from view, exemplifies how seemingly basic mechanisms can become highly advanced components in modern vehicles. This journey underscores the ongoing innovation and improvement needed to meet the demands of today's performance car market.
San Antonio's engineering scene has played a noteworthy role in the evolution of supercar pulley systems, particularly in the realm of extreme performance. They've tackled the challenge of creating pulleys capable of handling the high RPMs demanded by these powerful engines, pushing the boundaries of what's possible without compromising reliability. The local focus on lightweight materials is also notable, with companies in the region leading the charge in developing composites and employing 3D printing to produce pulleys that are both stronger and lighter. This reduces the engine's rotational inertia, leading to faster acceleration and a potential improvement in overall engine longevity, a key factor under the immense stress of a supercar engine.
Another facet of San Antonio's influence lies in the integration of real-time data into pulley design. By transmitting data on current engine conditions to the pulley system, engineers can adjust the pulley's behavior on the fly. This allows for dynamic optimization during varying driving situations, maximizing engine efficiency across a broader spectrum of conditions. This is especially interesting because it creates an incredibly responsive and adaptive pulley system that essentially learns the car’s needs.
San Antonio’s engineers have also contributed to innovations like asymmetrical pulley designs. These non-standard shapes provide a more efficient engagement with the belt, mitigating slippage and improving power transfer. This is crucial for supercars, which need rapid and instantaneous power delivery to deliver the exhilarating acceleration that defines them. While this may seem a minor change, it has a real world impact for drivers and the overall engineering problem of power delivery.
Further exploring the fine details, some research efforts within San Antonio have centered on the auditory properties of pulleys. This may seem odd, but it links to the sonic signature that contributes to a supercar's allure. By influencing the sound frequency generated by the pulley and belt systems, engineers can subtly fine-tune a car’s auditory identity, which creates a more enjoyable and immersive driving experience for the driver while potentially matching performance and aesthetic goals.
Furthermore, the concept of variable pulley diameters, a feature becoming increasingly popular in high-performance cars, has strong roots in research initiatives from San Antonio. These pulleys are able to dynamically adjust their size based on engine load and driving conditions, optimizing performance for different scenarios. This adaptive capability, driven by the research in San Antonio, demonstrates a forward-thinking approach to pulley engineering, leading to potentially greater efficiency in supercar design.
San Antonio’s influence isn't limited to gasoline engines. The city's researchers are also applying their insights to hybrid systems, focusing on how pulley technology can optimize the integration between gasoline and electric engines. This allows for smoother transitions between power sources, harnessing the strengths of both technologies to create a better overall driving experience.
Interestingly, San Antonio's research community has also championed the use of computational fluid dynamics (CFD) in pulley design. CFD helps create more aerodynamically efficient pulley shapes, minimizing drag and ultimately enhancing overall engine efficiency. This is vital for vehicles that prioritize both raw power and fuel economy.
Beyond current technology, San Antonio's engineers are looking further ahead. There's active exploration of the potential for magnetic pulleys, a fascinating proposition that could revolutionize supercar design. This system uses magnetic resonance for motion transfer, eliminating traditional friction found in mechanical components. If successful, it could lead to even more efficient and powerful supercar drivetrains.
Beyond institutional research, the city also serves as a hub for specialized automotive workshops. In these workshops, master craftsmen meticulously tune pulleys to exact specifications for individual supercar owners, essentially tailoring the car's performance to their specific needs and desires. These customized systems are designed for both driving pleasure and performance on the track and provide a tangible link to individual preferences.
In conclusion, San Antonio's role in refining pulley technology within supercar engineering is multi-faceted. It reveals how seemingly simple components like pulleys can impact a vehicle's performance, aesthetics, and overall driving experience. These contributions showcase San Antonio's innovation in a sector that pushes the boundaries of automotive engineering.
The Evolution of Pulley Systems in Modern Supercar Design A Look at San Antonio's Influence - The Role of Advanced Pulley Systems in Improving Supercar Performance
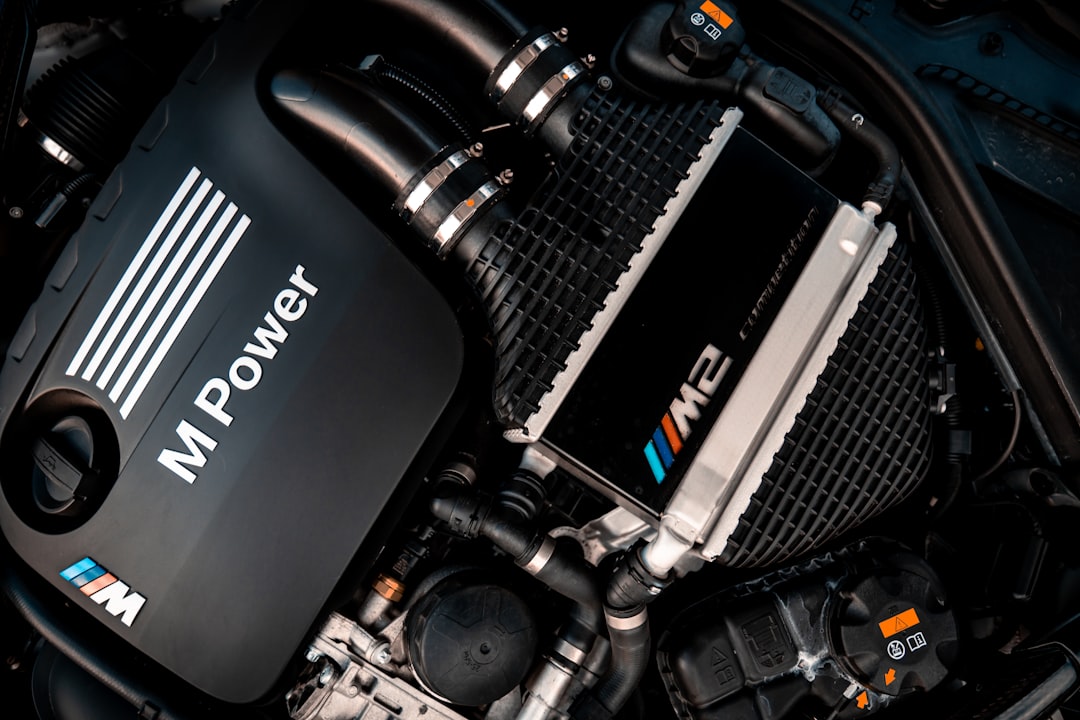
Advanced pulley systems are a crucial part of improving supercar performance, blending historical design with modern engineering advancements. These systems optimize engine power by minimizing belt load and managing torque more effectively, which is critical for maintaining high power outputs in lightweight supercars. The incorporation of sophisticated features, such as variable diameter pulleys, enables dynamic adjustments based on driving circumstances, effortlessly balancing performance and efficiency. As supercar manufacturers constantly strive for increased speed and handling, the emphasis on refining these systems highlights their critical role in achieving peak performance. The evolution of pulley technology within this context is not just a technical achievement; it showcases the ongoing drive for automotive excellence. While the design may seem relatively simple, the engineering behind modern pulley systems has become extremely complex in high-performance cars, a factor not always readily apparent to the casual observer. The design and tuning of these pulleys contribute heavily to a supercar's ability to deliver its intended performance and the expected driving experience, especially under strenuous conditions.
Advanced pulley systems are increasingly vital for optimizing supercar performance. The ability to dynamically adjust pulley tension based on engine demands is a prime example of this evolution. These systems not only enhance performance but also reduce wear and tear on critical components during fluctuating loads. It's fascinating to observe this shift towards adaptive engineering, where components can self-adjust in real-time, reflecting a move beyond fixed designs.
Asymmetrical pulley designs are another intriguing development. By altering the pulley's shape, engineers can create a larger contact area with the belt, minimizing slippage. This subtle change is significant for supercars, which often require lightning-fast power delivery. It emphasizes that even seemingly small adjustments can yield noticeable differences in a supercar's driving experience.
The concept of variable diameter pulleys takes this adaptive approach a step further. Some modern designs allow the pulley to change size based on engine load. This provides greater flexibility in optimizing engine efficiency across a wider range of operating conditions, delivering a boost in both overall performance and fuel economy.
The increasing use of lightweight composite materials in pulley construction has revolutionized performance. These new materials reduce weight significantly, allowing for improved acceleration and responsiveness while retaining the strength needed to handle the immense forces found in a supercar engine. The pursuit of lighter components is becoming a dominant design theme, and pulleys are no exception.
Beyond performance, engineers are paying closer attention to the cooling implications of pulley design. Improvements in airflow within the system contribute to a healthier operating temperature for the engine. This is especially important in supercars that often operate at high speeds or under intense conditions for extended periods.
Another area that's seen interesting development is the interplay between pulley systems and sound design. Engineers can now tune a car's acoustic profile by controlling the frequencies generated by pulleys and belts. The outcome is a more visceral driving experience, where the aural feedback mirrors the car's power and character. It's a fascinating blend of mechanical engineering and aural design.
The influence of data is also becoming more pronounced in pulley system design. Real-time telemetry data about engine performance is now used to optimize pulley operation in diverse driving scenarios. This data-driven design approach leads to engines that can adapt and learn, becoming more efficient over time.
Minimizing friction has always been a primary engineering goal, and this principle is being refined in pulley systems through innovative bearing designs and better lubricants. This reduction in friction improves engine efficiency and potentially increases its lifespan, vital considerations in vehicles pushing the boundaries of automotive technology.
The future of supercar pulley systems might involve a complete departure from traditional designs. Research into magnetic pulleys is underway, and if successful, it could revolutionize how power is delivered in future supercars. By harnessing magnetic fields instead of mechanical contact, these systems could potentially eliminate friction, leading to even greater performance and efficiency.
Finally, the rise of customization within supercar engineering has reached the realm of pulleys. Manufacturers are offering tailor-made pulley configurations, allowing drivers to influence a wide range of aspects, including acceleration and engine sound. This opens up a new dimension of individualization for supercar enthusiasts, allowing each owner to perfectly match their car to their unique driving preferences.
In essence, pulley systems are no longer just functional components. They are becoming increasingly sophisticated elements within the supercar engineering puzzle. It’s exciting to see how a seemingly simple mechanical principle from the past continues to drive innovation and optimization in these high-performance machines.
The Evolution of Pulley Systems in Modern Supercar Design A Look at San Antonio's Influence - How Pulley Configurations Impact Aerodynamics in High-Speed Vehicles
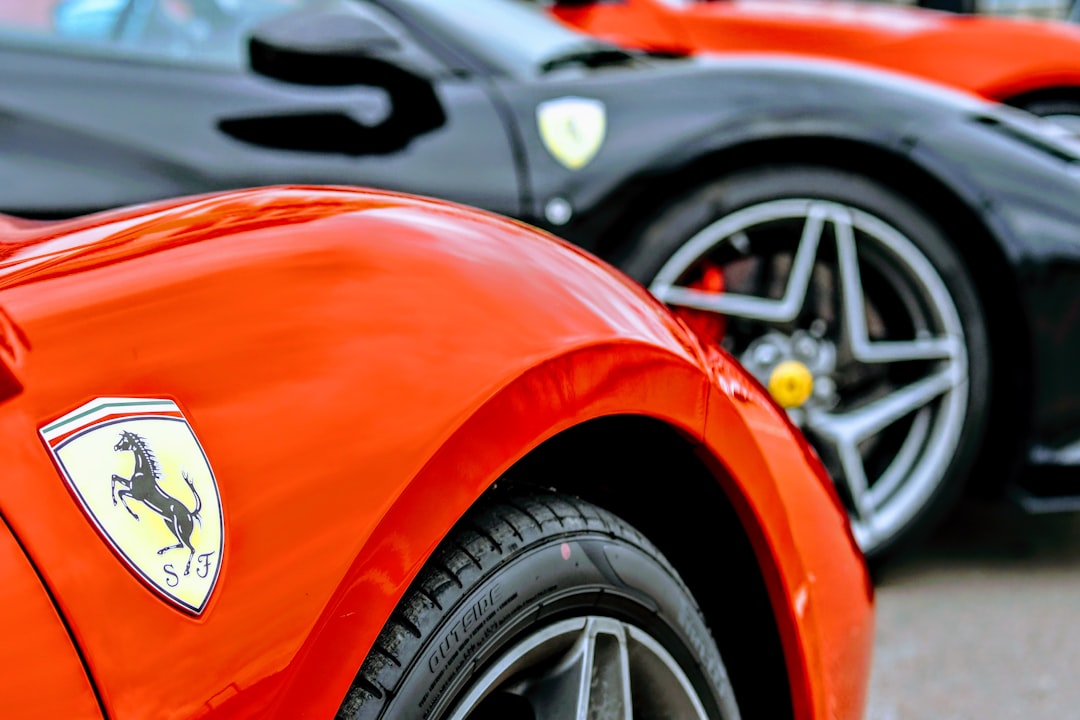
The aerodynamic performance of high-speed vehicles, especially supercars, is significantly impacted by the design of their pulley systems. The way these systems transfer power to the wheels directly influences a vehicle's stability and overall performance at high speeds. Modern developments, such as variable diameter pulleys and asymmetrical pulley shapes, are aimed at reducing power loss due to slippage and maximizing engine efficiency. This signifies a trend towards more adaptable pulley designs that can react to varying driving conditions. As the pursuit of higher speeds in supercars continues, designers face the complex challenge of optimizing performance while also adhering to increasingly stringent environmental standards. Pulley systems are becoming essential tools in meeting both these goals, demonstrating how innovative adaptations of traditional mechanics can reshape the capabilities of high-performance vehicles. The ongoing advancements within this area of automotive engineering show a remarkable convergence of historical knowledge and modern technological advancements, resulting in a truly fascinating evolution within the supercar landscape.
Pulley systems within supercars, while seemingly simple, involve a surprising degree of complexity. Engineers must meticulously design not only the pulley's diameter and material but also its shape, as asymmetrical designs can demonstrably minimize belt slippage and enhance power transmission. This is especially critical when considering that supercar engines often operate at incredibly high RPMs, exceeding 10,000 in some instances. Building pulleys that withstand such extreme conditions without failing pushes materials to their limits and necessitates a deep understanding of materials science.
Furthermore, the integration of real-time data into pulley systems allows for dynamic load management. The pulley's behavior can be adjusted instantly based on the engine's current load, ensuring optimized power delivery across different driving scenarios. This makes supercars impressively agile and responsive, a critical element in high-performance driving.
Another facet of pulley evolution is the growing emphasis on minimizing weight. Utilizing advanced composite materials has enabled significant reductions in the weight of pulleys, subsequently improving acceleration and fuel efficiency. It's remarkable how a seemingly minor change in a single component can positively impact overall vehicle performance.
This intricate interplay between mechanical engineering and sound design is gaining more attention. Engineers are now actively tuning the fundamental frequencies produced by pulley and belt systems. This novel approach to acoustic engineering creates a more immersive driving experience, letting drivers experience a more engaging auditory connection with their car.
Research into magnetic pulley systems represents a potential game-changer. If successful, this technology could revolutionize power delivery by eliminating the friction inherent in conventional mechanical components. This would result in smoother, more efficient power transmission, potentially pushing supercar technology to a new level.
The development of variable diameter pulleys is another innovative approach that allows the pulley's size to adapt based on engine demands. This adaptability improves efficiency across a wider spectrum of driving situations, contributing to both enhanced performance and improved fuel economy.
Aerodynamics, often overlooked in pulley design, is becoming increasingly important. Computational fluid dynamics (CFD) is now being used to analyze and shape pulley configurations to minimize aerodynamic drag. This illustrates the intertwined relationship between engine efficiency and airflow management.
Furthermore, engineers are taking a refined approach to sonic signature. By tweaking pulley designs, they can precisely tailor a supercar's sound to a driver’s preferences. This adds a fascinating layer of personalization, enabling owners to shape the car's auditory persona to reflect their individual tastes.
The trend of personalization has extended to pulley systems themselves, with many manufacturers now providing customized pulley configurations. This affords supercar owners a greater degree of control over aspects such as throttle response and engine sound. It's a noteworthy evolution, strengthening the connection between the driver and their vehicle.
In conclusion, pulley systems are no longer just mundane mechanical elements; they're becoming sophisticated components that shape supercar performance, aesthetics, and the overall driving experience. This evolution demonstrates how seemingly simple historical mechanisms can be iteratively refined and applied to address contemporary engineering challenges, propelling high-performance vehicle design forward.
The Evolution of Pulley Systems in Modern Supercar Design A Look at San Antonio's Influence - Future Trends Integrating Smart Pulleys in Next-Generation Supercars
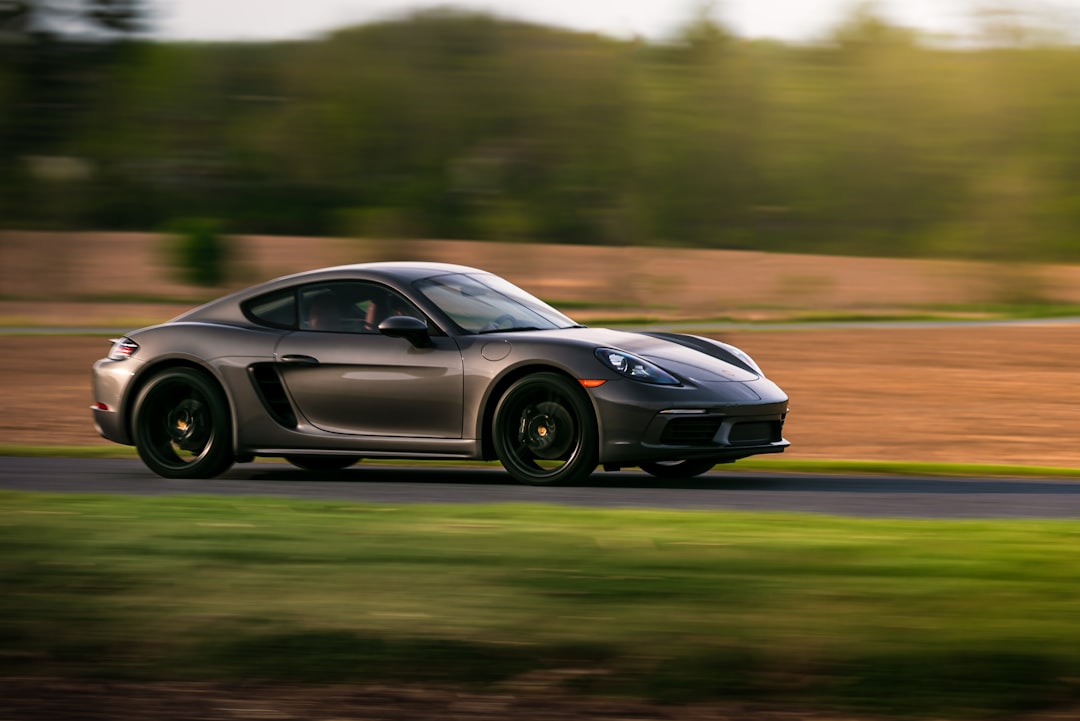
The future of supercar design is increasingly focused on achieving both peak performance and enhanced efficiency. A key element in this pursuit is the integration of intelligent pulley systems. These systems are designed to adapt to changing engine demands, employing advanced materials and real-time data to optimize power output. The ability to dynamically adjust pulley tension based on driving conditions minimizes energy loss and optimizes fuel efficiency, a critical factor as stricter environmental regulations are implemented. This is particularly evident in the growing adoption of variable-diameter pulleys, which can modify their size to match specific engine needs. Furthermore, the connection between pulley design and other elements of supercar engineering, such as aerodynamics and the carefully curated sound profiles, demonstrates a holistic approach to high-performance vehicle development. It is a fascinating evolution, emphasizing how seemingly simple mechanical principles remain relevant in modern supercar design and continue to shape the future of this exciting automotive sector, particularly within the arena of luxury vehicles and futuristic performance car concepts.
The future of supercar engineering is increasingly intertwined with the development of smart pulley systems. We're seeing a shift towards more dynamic and adaptable designs, where pulleys can respond in real-time to changing engine conditions. One intriguing development is the use of pulse-width modulation, which allows for fine-grained control over pulley operation based on torque demands. This is particularly important in scenarios demanding quick power delivery, like high-speed cornering, where engine responsiveness is crucial.
However, these advancements bring new challenges. Supercar engines routinely push the limits of speed, often exceeding 10,000 RPM. This necessitates the use of materials that can withstand immense stress and resist fatigue at such high rotational speeds. The selection of appropriate materials for pulley construction is becoming increasingly crucial, and it requires a deep understanding of materials science to address the thermal and mechanical stresses these systems experience.
The aerodynamic impact of pulley design is another emerging consideration. Engineers are employing computational fluid dynamics (CFD) to optimize the shape of pulleys, reducing aerodynamic drag and contributing to overall vehicle performance, especially at high speeds. This interdisciplinary approach highlights how seemingly simple mechanical components can interact with complex systems like aerodynamics.
Moreover, the interplay between pulley design and sound is becoming more sophisticated. The subtle manipulations of pulley physical properties allows for the fine-tuning of a supercar's audio profile. This creates a more engaging and immersive auditory experience for the driver, effectively aligning the sound signature with the vehicle's performance characteristics.
Interestingly, asymmetrical pulley designs are gaining traction. These configurations create a larger contact area with the belt, minimizing slippage and optimizing power transfer. This is particularly relevant for applications demanding rapid acceleration, an area where supercars always push boundaries.
The concept of variable diameter pulleys is a remarkable innovation, representing a step toward truly adaptive designs. By dynamically changing their size based on engine loads, these systems can optimize engine efficiency across a wide range of operating conditions. This flexibility is key to enhancing both performance and fuel efficiency.
The possibility of magnetic pulley systems is perhaps the most fascinating avenue of research. By potentially eliminating friction through magnetic fields, these systems could significantly enhance power delivery, opening up new realms of efficiency and performance in future supercar designs.
The trend of personalization in supercars is also impacting the design of pulley systems. Manufacturers are starting to offer customized pulley configurations, allowing drivers to fine-tune elements like throttle response and engine sound to align with their unique preferences.
Modern supercars leverage real-time telemetry data to dynamically optimize pulley performance. This data-driven approach enables adjustments on-the-fly, improving the overall driving experience and efficiency.
The increasing use of advanced composite materials for pulley construction is also transforming performance. These lightweight materials improve durability and reduce weight, contributing to quicker acceleration and better fuel efficiency—critical factors for achieving optimal performance.
In essence, pulley systems are no longer mere functional components in supercar design. They are evolving into highly engineered and intelligent parts of the drivetrain. This continuous innovation showcases how even the most fundamental mechanical principles can be reinterpreted and optimized to address complex engineering challenges in the ever-evolving world of high-performance vehicles.
More Posts from tunedbyai.io: