The Rise of 3D-Printed Performance Parts How Online Stores Are Revolutionizing Custom Car Tuning in 2024
The Rise of 3D-Printed Performance Parts How Online Stores Are Revolutionizing Custom Car Tuning in 2024 - 3D-Printed Performance Parts Slash Production Time and Costs
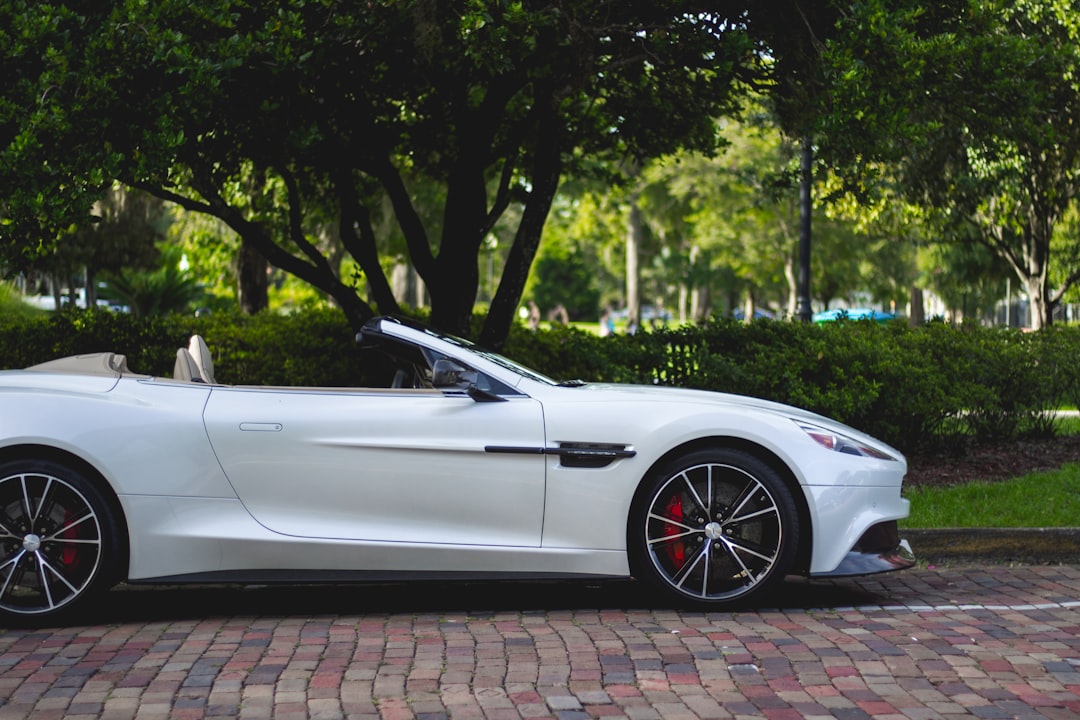
The rise of 3D printing is fundamentally altering how performance parts are manufactured, bringing about a new era of customization and streamlined production. By sidestepping the need for conventional molds and tools, manufacturers can dramatically reduce expenses and drastically shorten production cycles. This agility in the production process empowers them to respond to market demands and individual customer preferences much faster. Companies like Bugatti and Porsche have already embraced this technology, integrating lightweight, high-strength components into their vehicles, even reviving classic models with hard-to-find parts. This trend not only boosts the performance potential of high-end cars but also hints at a broader revolution in aftermarket car modifications, where rapidly created prototypes and bespoke accessories are reshaping the landscape of car tuning. As 3D printing technology matures, its influence on the luxury and performance car sectors will likely expand, creating a mixture of obstacles and fascinating prospects for both enthusiasts and industry players.
The use of 3D printing for performance parts is significantly reducing both production times and costs, a trend that's reshaping the automotive aftermarket. The speed at which prototypes can be produced is remarkable – what used to take weeks now can be achieved in hours. This allows for quicker evaluation of design changes, enabling faster development cycles in the pursuit of optimal performance.
We're also seeing the emergence of high-performance materials, such as specialized thermoplastics and alloys, being successfully implemented in 3D-printed automotive components. This opens a new world of possibilities, particularly for intricate geometries that would be incredibly difficult to manufacture using traditional methods. For example, the intricacies required in some supercar designs or the need for very specific components for high-performance luxury cars would be impossible without it.
The shift towards on-demand production is evident, with the potential for dramatic cost savings, especially for niche or smaller-scale operations like custom tuning shops. It's a game changer, offering an affordable alternative to the high tooling and mold costs often associated with conventional production methods.
Furthermore, the ability to manufacture parts in-house potentially reduces dependence on external suppliers. While still a relatively new technology, the ability to scale 3D printing, with the rise of '3D printing farms', suggests a shift towards a more decentralized and potentially more resilient manufacturing landscape for specialty parts. This is particularly beneficial for independent tuners who can be quick to respond to demands for new, often very specific, car modifications.
However, questions remain regarding the long-term reliability of 3D-printed parts subjected to the demanding environments of motorsport and high-performance driving. There's a clear need for comprehensive testing and validation procedures, potentially aided by advanced simulation techniques to bridge the gap between virtual design and real-world performance. Perhaps the next stage of this evolution will be the direct integration of sensors and electronics, leading to even more sophisticated and tailored performance tuning options. While some might see this as futuristic, I believe this technology, originally adapted from aerospace and now rapidly developing in the car world, is just scratching the surface of its potential for customization and design in high-end performance vehicles.
The Rise of 3D-Printed Performance Parts How Online Stores Are Revolutionizing Custom Car Tuning in 2024 - Custom Restoration Made Easy with Precise 3D-Printed Replicas
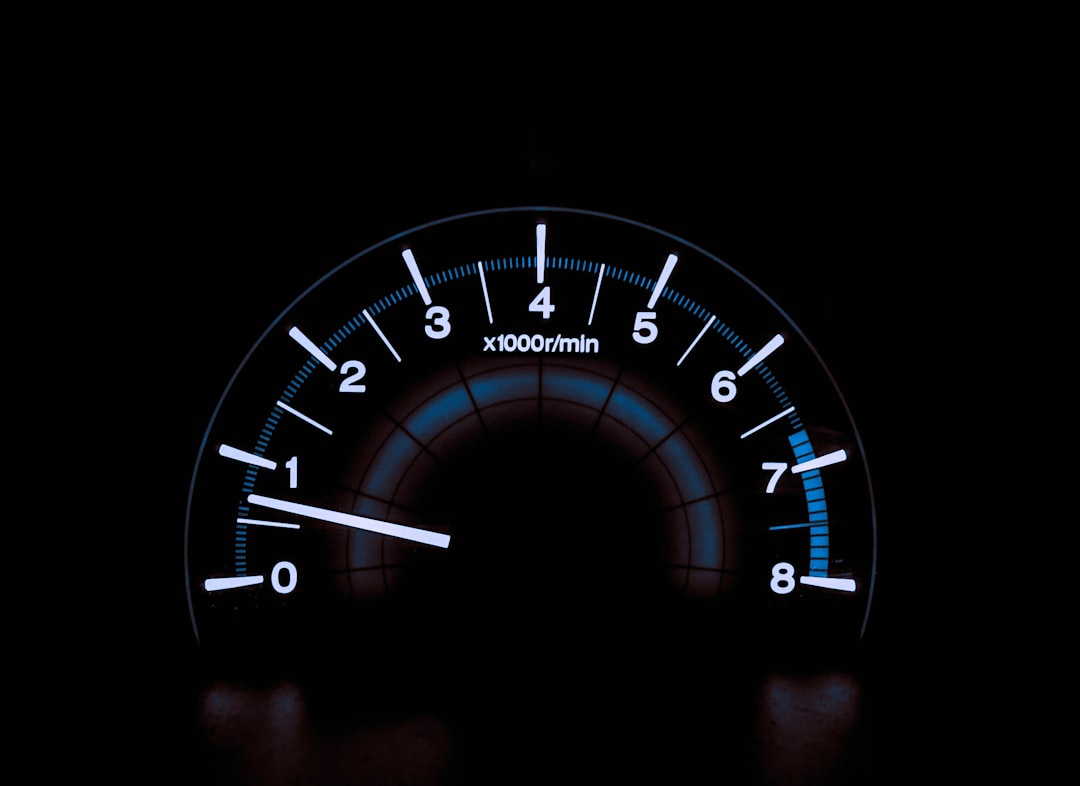
The growing accessibility of 3D printing is changing how we approach classic car restoration. It's now much easier to create highly accurate replicas of original parts, which is crucial for maintaining the authenticity of "restomod" projects—a trend that combines vintage styling with modern performance upgrades. This is achieved by digitally capturing a car's entire structure, producing precise 3D models that serve as the foundation for printing replacement parts. The precision of 3D printing allows for extremely detailed replication, with some applications demanding tolerances as small as 0.05 mm. This level of accuracy helps restore classic cars to their original glory or even improve upon their original design with modern touches.
Beyond just replicating lost or damaged parts, 3D printing opens the door to custom designs for classic cars. Enthusiasts can now create unique and personalized components, previously limited by the availability of traditional manufacturing methods. This allows them to truly express themselves through their car's aesthetics and functionality, pushing the boundaries of what's possible with classic car customization. It's a powerful tool in the hands of restoration specialists and hobbyists alike, further solidifying 3D printing's role in the future of custom car tuning. The digital design and fabrication process is steadily becoming integral to the world of car modification, providing greater control and freedom for creating truly bespoke vehicles. While the technology itself is still relatively young, it has already begun to reshape the landscape of classic car restoration, making it easier than ever to preserve and personalize automotive heritage.
The ability to create incredibly precise 3D-printed replicas is revolutionizing car restoration, particularly for those seeking to maintain the integrity of classic or high-performance models. We're talking about tolerances down to 0.1 millimeters, which is vital for ensuring a perfect fit when replacing or enhancing components, especially in intricate engine bays of luxury or supercars. It's fascinating to see how these 3D printed components can be tailored so accurately.
The materials used in 3D printing are also contributing to this shift. Advanced polymers and metals like titanium and carbon fiber composites offer a compelling combination of strength and lightness, surpassing what's possible with traditional materials in many cases. This is especially important for performance-oriented applications where shaving weight can have a significant impact on a car's acceleration and handling. Consider a classic sports car's chassis: 3D printing could potentially replicate it using these advanced materials, potentially improving performance and rigidity beyond the original design.
Moreover, the intricate designs that 3D printing allows for are game-changing. For instance, we can achieve aerodynamic enhancements that would be impractical with traditional manufacturing methods, refining things like air intakes, spoilers, and even chassis elements for optimum airflow. This degree of customization isn't just about aesthetics; it's about fine-tuning the car's performance in ways that were previously impossible.
One of the most impressive aspects of this technology is the speed at which prototypes can be developed. Where creating a custom part traditionally might take weeks or months, 3D printing allows engineers to rapidly iterate, completing a prototype within hours. This significantly shortens development cycles, pushing innovation in custom parts for a range of models.
Further fueling this customization trend, online stores specializing in 3D-printed parts are emerging, providing near-limitless possibilities for enthusiasts. It's now possible to specify and receive a custom-made component quickly, empowering the hobbyist to go beyond the limitations of mass-produced parts.
This move towards local, on-demand production also streamlines the supply chain. Tuning shops are less reliant on long lead times and global logistics, reducing bottlenecks and ensuring faster access to necessary components for modifications. This trend could also potentially lead to reduced reliance on existing parts suppliers, as businesses start manufacturing components locally with 3D printing.
And this ability to create designs digitally also extends to the maintenance of a virtual inventory. Rather than storing physical parts, businesses can maintain a library of digital designs, essentially printing components on demand. This leaner approach reduces overhead costs and maximizes flexibility to meet customer needs as they arise.
Looking beyond the present, we can imagine a future where historical cars are reborn thanks to 3D printing. Obsolete components that are no longer available can be replicated, allowing restorers to maintain the authenticity of these vehicles. 3D printing could help keep automotive history alive and kicking.
Additionally, we could see components that incorporate sensors directly into their design. Imagine performance parts equipped with sensors that feed real-time data on their behavior back to the driver or the car's control system. This opens up whole new avenues for fine-tuning performance and adapting to varying driving conditions. While still a futuristic prospect, it's an indication of the direction this technology could take.
Finally, the use of advanced simulation software coupled with 3D printing is paving the way for better testing of prototypes. This allows engineers to test designs under simulated extreme stress conditions before physical production, significantly reducing the risks associated with developing high-performance parts. It's a more efficient and informed way to innovate in this domain. Overall, 3D printing is undeniably reshaping the landscape of automotive customization, bringing a new era of possibilities in both restoration and performance enhancement.
The Rise of 3D-Printed Performance Parts How Online Stores Are Revolutionizing Custom Car Tuning in 2024 - Ford's Integration of 3D Printing Boosts Manufacturing Efficiency
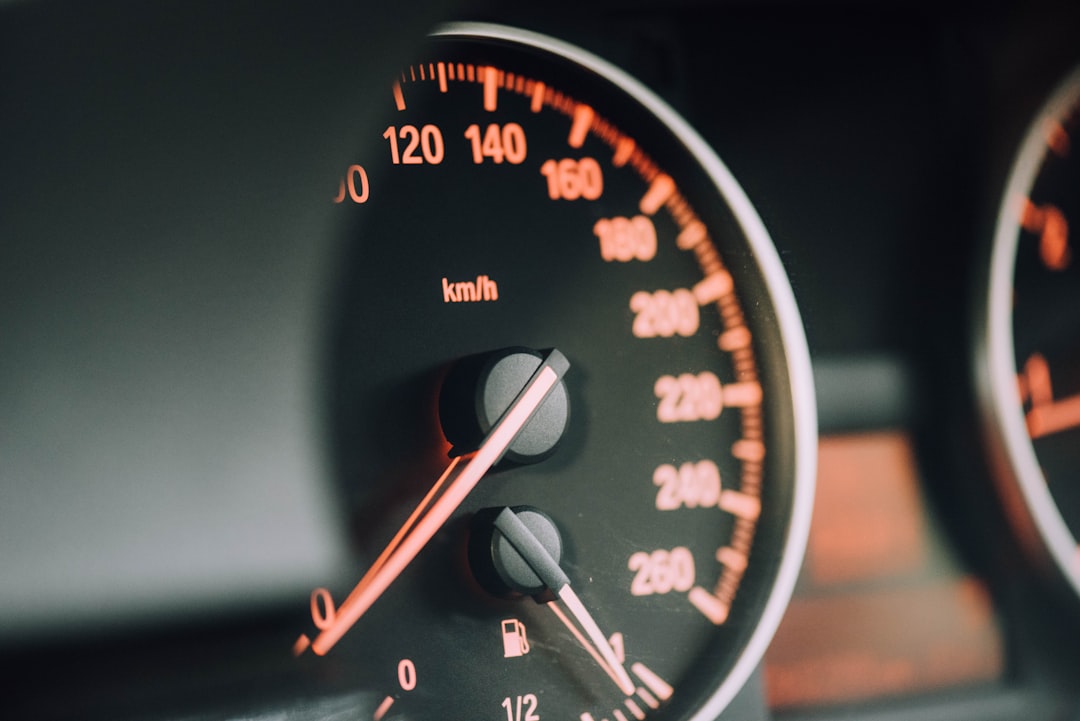
Ford's embrace of 3D printing is revolutionizing its manufacturing processes, especially as it pushes forward with its first European-built electric car. By automating 3D printing with robots that operate continuously, Ford is dramatically boosting output and lowering costs. This is evident in their new Cologne facility, where a dozen 3D printers are dedicated to making tools and components for their vehicles. This facility is a strong sign that Ford is actively using 3D printing to enhance efficiency and quality in production.
The ability to quickly print intricate parts is a key advantage, accelerating development time for new vehicles and allowing for more customization options, which is valuable in the evolving world of car tuning and performance upgrades. Ford's strategic deployment of 3D printing suggests that the wider industry might follow suit, ultimately impacting how performance parts are designed and produced. This could have significant repercussions for both car enthusiasts and luxury car brands, paving the way for a new era of innovation and customization in the automotive sector. However, there are concerns about the durability of 3D printed parts for demanding applications. Despite this, the clear direction Ford is taking with additive manufacturing techniques is a step forward, potentially reshaping the way high-performance components are developed and deployed in future vehicle models.
Ford's recent embrace of 3D printing is reshaping their manufacturing processes, pushing the boundaries of efficiency and design. It's interesting how they've automated the process, using mobile robots to run 3D printers around the clock. This continuous operation, documented in several patents, is a clever way to increase output and cut costs. Notably, they've established a new 3D printing hub in Cologne, Germany, which is playing a key role in producing parts for their first European-built electric vehicle. It's clear that they're aiming for improved production efficiency and quality control.
This Cologne facility utilizes a dozen 3D printers focused on creating tooling and fixtures for vehicle assembly. What's intriguing is that these printers can also handle parts for prototypes and small batches. Further, Ford has made 3D printing more accessible for its staff through an app. This allows employees to request custom-designed installation aids, a move that streamlines the process and highlights their commitment to incorporating this technology broadly within the organization.
It's fascinating that Ford relies on a seemingly simple technique called fused deposition modeling (FDM) with thermoplastics. Apparently, it's saving them millions. This makes one wonder how much further this simple technology can be pushed. The increased autonomy in their 3D printing operations is quite telling. The ability to have robots operate the printers overnight, a system currently awaiting patent approval, clearly tackles a production bottleneck and pushes their manufacturing capabilities further.
Ford's Advanced Manufacturing Center is a testament to their growing interest in additive manufacturing. It houses an impressive 23 industrial 3D printers. Recent applications showcase how quickly this can change vehicle development. For example, the engine cover for the new Mustang was rapidly prototyped using 3D printing. This is speeding up the entire development cycle for parts like cylinder heads and intake manifolds.
While impressive, some might question if 3D printing can handle the extreme performance demands found in supercars or hypercars. But Ford's push in this area shows they are serious about integrating 3D printing further into their designs. It seems this is a technology that will continue to evolve and affect automotive manufacturing. From restoration to future innovations, it's clear 3D printing will play a significant role in how we design, produce and experience cars. Whether we see 3D-printed luxury cars or just unique restoration parts remains to be seen, but Ford's current push is quite intriguing.
The Rise of 3D-Printed Performance Parts How Online Stores Are Revolutionizing Custom Car Tuning in 2024 - R3D's NXE 400 Printer Produces 7,000+ Custom Police Vehicle Parts
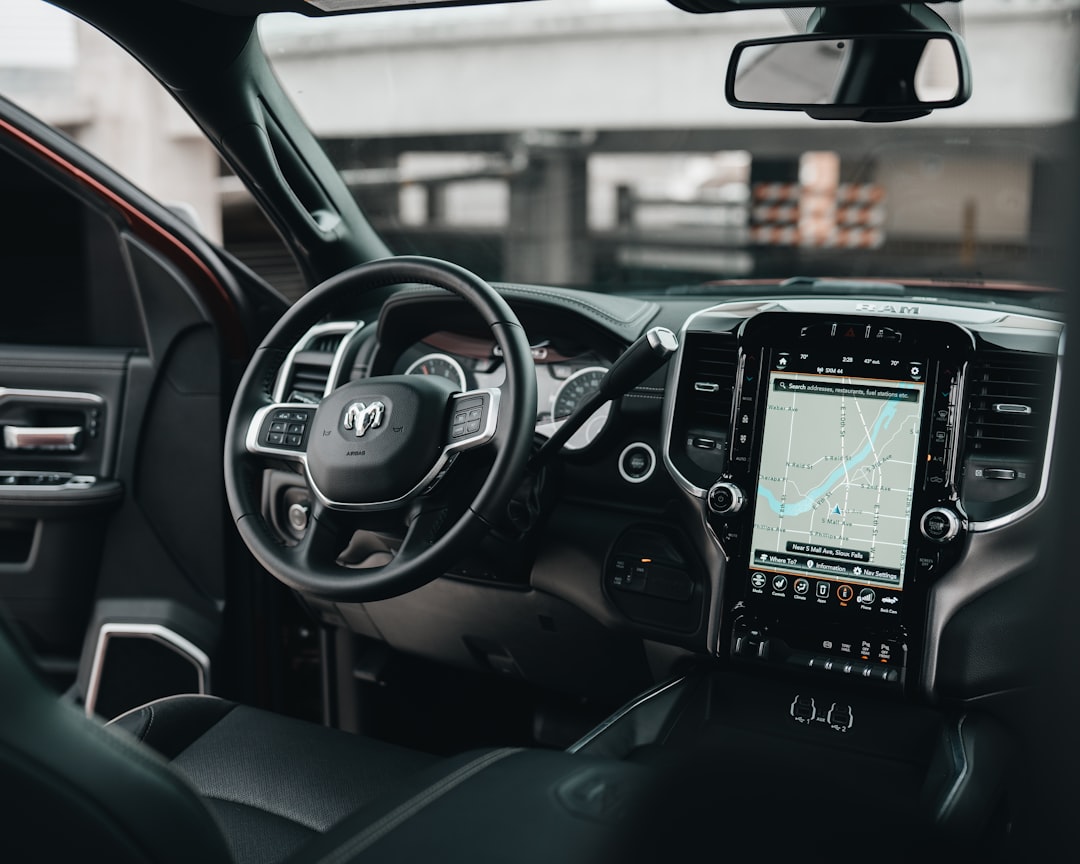
R3D's NXE 400 printer showcases a notable leap in 3D printing, having successfully produced over 7,000 customized components for French police vehicles in a single year. This achievement demonstrates the printer's ability to significantly slash the time and expense of creating functional prototypes, potentially revolutionizing how some aftermarket parts are made. The NXE 400's unique LSPc technology allows for swift prototyping and production, leading to faster design cycles and more efficient manufacturing within the automotive industry. This application isn't just beneficial for public service vehicles, it hints at a broader impact of 3D printing on car customization and potentially, even the design of future luxury vehicles. The growing integration of 3D printing in automotive manufacturing creates exciting possibilities and presents challenges for both car lovers and those who make the cars, making the future of vehicle design and tuning a complex and intriguing area of innovation.
The NXE 400 printer from R3D has demonstrated its capabilities in producing a massive quantity of customized parts—over 7,000—for police vehicles. This highlights the potential of 3D printing to create specialized components for niche applications like emergency vehicles. Interestingly, it seems the printer is using advanced materials to create parts that are both lightweight and structurally sound, crucial for handling the rigors of high-speed pursuits or demanding off-road situations.
One intriguing aspect of this is the ability to create complex internal structures, which wouldn't be possible with traditional manufacturing methods. For instance, they could potentially create cooling systems with optimized airflow paths, improving engine performance. The NXE 400 also offers design freedom, potentially reducing reliance on costly custom tooling. This means that bespoke orders can be fulfilled much faster, a benefit to both the manufacturers and the customers.
R3D's printer boasts integrated software, allowing for real-time monitoring and adjustments during printing, leading to increased precision and reduced material waste—a critical consideration when working with high-performance materials. Each part printed is tailor-made for specific vehicle models, accommodating minor variations in design without extensive modifications. This streamlined approach seems ideal for the customization process in performance tuning.
Looking at the speed advantages, 3D printing reduces the time for prototyping parts dramatically – from weeks to a matter of hours. This ability to rapidly iterate and test designs fundamentally changes the automotive development cycle, creating an environment for faster innovation. The cost benefits are particularly noticeable for small operations. Custom tuning shops can now affordably produce unique parts without the massive capital investment needed for traditional molding processes.
The NXE 400's capabilities continue to evolve, including features like multi-material printing. This allows for the integration of various materials within a single component, potentially enabling parts with different levels of stiffness or thermal resistance, improving performance in various ways. Looking further into the future, the precision attainable with printers like this suggests the possibility of incorporating 'smart' components that can monitor their own performance. This opens up fascinating avenues for future car tuning and maintenance practices. As the technology matures, it's clear that 3D printing is becoming a powerful force in the automotive world, and it will be exciting to see what innovations it brings next.
The Rise of 3D-Printed Performance Parts How Online Stores Are Revolutionizing Custom Car Tuning in 2024 - STL Files Emerge as Cornerstone of Rapid, High-Quality Part Production
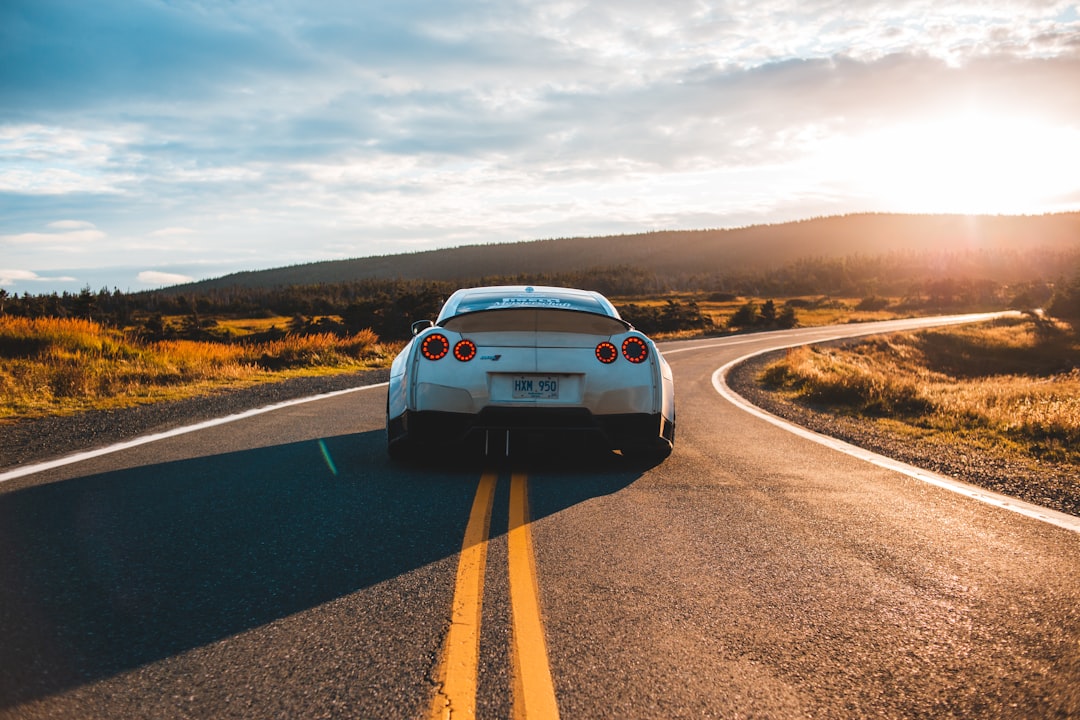
STL files are becoming the foundation for fast and high-quality part production, particularly impacting the custom car tuning scene. These files are the key that unlocks the potential of 3D printing, enabling the creation of highly specific and complex components that were previously hard to make. This revolutionizes the prototyping stage, giving enthusiasts the ability to explore unique designs swiftly, while also making customization more accessible to a wider range of individuals. The growing number of online platforms offering STL file libraries further broadens the horizon for unique car modifications, driving a new wave of innovation within the world of car tuning and design. This technology is especially compelling for the high-end car sector, where the integration of precision-engineered, 3D-printed parts becomes a viable reality. This shift towards customization could potentially alter the dynamics within the luxury car market, with a move toward greater personalized design and production. While the technology is still evolving, the impact of readily available STL files is already significant and likely to continue reshaping the landscape of car tuning and design in the coming years.
STL files have become increasingly important in the automotive world, especially for creating high-quality custom parts quickly. The use of 3D printing, made possible through these files, is fundamentally changing how car components are made, offering speed and precision previously unimaginable. This additive manufacturing approach allows for intricate designs that were once impossible to build, particularly for those complex shapes seen in supercars or high-performance luxury vehicles.
Online platforms are brimming with STL files, places like Thingiverse and Cults offer a vast selection of free and paid models for various automotive applications. This ease of access to designs has completely transformed the landscape of custom car tuning, opening up a world of possibilities for enthusiasts. They can now readily access and utilize designs for unique components, further bolstering the DIY aspect of car modification.
STL files are allowing for much more advanced design capabilities. It's become commonplace to use them to quickly produce prototype parts, which ultimately leads to better performance parts being developed faster. This ties in with the growing trend towards more personalized and modified vehicles, largely fueled by the accessibility of 3D printing and digital design.
When creating a 3D-printed component using an STL file, setting the correct parameters in the exporting process is essential. Ensuring the highest dimensional accuracy is key for successfully implementing these designs. The online sales channels popping up for 3D-printed car parts further emphasize the shift towards more individualized and DIY tuning solutions in 2024.
However, there's always a catch. It's still early days for 3D printing in the automotive space, and questions about the long-term durability of these printed parts remain, especially when used in high-performance environments. The material science aspect is evolving quickly, which makes things even more interesting. There's a definite need for a lot more testing, likely paired with increasingly advanced simulation tools, to truly understand the limits and potential of these 3D-printed components.
It's likely this is only the beginning. The potential for integrating sensors directly into these printed parts is intriguing. It raises the prospect of smart performance parts, constantly relaying information back to the car's systems or the driver, offering real-time feedback for tuning. This would change how people customize and maintain their cars going forward. It's fascinating to see how 3D printing, initially developed for aerospace, is rapidly impacting cars of all kinds, from classic restorations to the newest supercar designs. The possibilities are vast, and it's exciting to contemplate how the future of cars might be reshaped by this technology.
The Rise of 3D-Printed Performance Parts How Online Stores Are Revolutionizing Custom Car Tuning in 2024 - Desktop 3D Printers Accelerate In-House Automotive Design Process
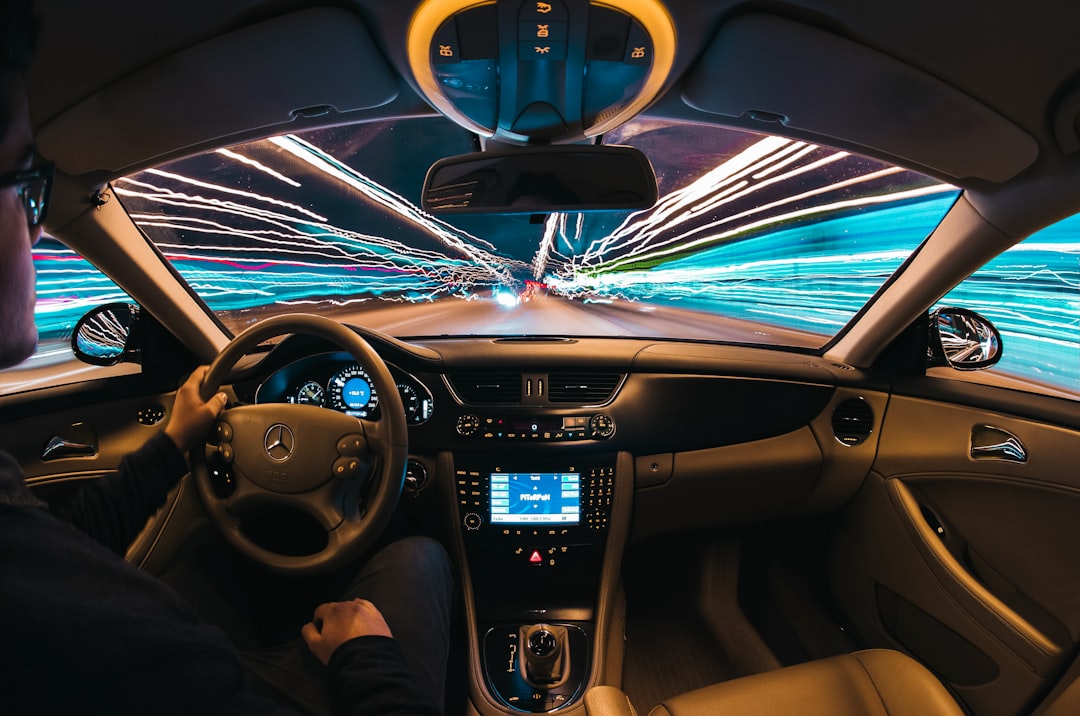
The rise of desktop 3D printing is reshaping how automotive design teams work, especially in areas like luxury and performance car development. These compact printers are allowing automakers to produce parts in-house, a shift that's streamlining the creation of components like electrical plugs and complex performance-related parts. This new approach allows for faster prototyping and less reliance on external suppliers, making the overall design process quicker and more adaptable. The ability to rapidly create customized parts is a game-changer, further fueled by the growth of online stores selling 3D-printed performance components. This trend is significantly altering the landscape of car tuning, giving enthusiasts and tuners previously unattainable customization options. This ability to tailor a car to precise specifications isn't just a trend anymore, it's pushing the automotive world towards a new era of mass customization where personalized vehicles are becoming increasingly common. It's a fascinating intersection of technology and personal expression, creating a future where a unique car design is less of a luxury and more of a possibility.
Desktop 3D printers are rapidly becoming a core tool in automotive design, particularly for performance and luxury vehicles. The ability to rapidly produce prototypes – tasks that once took weeks now achievable in mere hours – is drastically speeding up the design process for custom parts. This isn't just about quicker turnaround times; it's fundamentally altering the way designers approach innovation, allowing for much faster iteration and refinement.
Further enhancing design possibilities are the advanced materials now being used in 3D printing. Specialized thermoplastics and metals like titanium and aluminum alloys are enabling the creation of lightweight, high-strength components crucial for meeting the extreme demands of luxury and supercars. The potential for weight reduction and improved durability is huge, especially when it comes to engine components or chassis elements where every gram counts.
The precision attainable with 3D printing is another key aspect. Tolerances as small as 0.05mm are now feasible, which is simply mind-boggling when you consider the complexity of some engine bays or the intricate designs of supercar chassis. This allows for incredibly detailed replication of components, ensuring perfect fit and function, particularly important for parts that interact with high-performance engines or intricate suspension systems. It makes me wonder how these incredibly precise parts can be used in future hypercar designs or even more complex hybrid systems.
We're also witnessing a major shift in how customization is being approached. STL files are essentially digital blueprints that anyone can download and use to create unique car parts. It's remarkable how this is fundamentally democratizing design in the car world, offering a greater degree of personal control than we've seen before. This is especially impactful in the luxury car space, where personalization is often limited to a few pre-selected options.
One interesting side effect of this shift is the potential for greater independence in manufacturing. Instead of relying on traditional, often slow and complex, external supply chains, companies can now produce many parts in-house. This means they can be much more responsive to market trends and individual customer demands, potentially reshaping how tuning shops and performance-oriented manufacturers operate. It's a compelling idea – if the parts are made on-site, it potentially changes the nature of car modification, making it faster and perhaps more cost-effective.
Furthermore, this whole process is likely to become even more sophisticated as 3D printing integrates with advanced simulation technology. It's fascinating to envision design processes where prototypes are rigorously tested in virtual environments under extreme conditions before ever being physically printed. This level of testing and validation is vital to ensure that these custom parts can handle the stress and strain of high-performance driving. It suggests a future where the risks associated with developing new, complex performance parts are significantly reduced.
The ability to create complex internal geometries within a 3D printed part is also fascinating. Imagine building parts with optimized airflow channels for cooling or integrating internal structures to improve strength in a specific area. This could potentially have a significant impact on engine performance, especially in turbocharged or supercharged applications where heat management is crucial. I wonder how this could be adapted for use in the next generation of high-performance electric motors.
Looking further into the future, there's the intriguing prospect of integrating sensors directly into 3D-printed components. Imagine performance parts that constantly monitor their own behavior, feeding real-time data to the car's systems or the driver. This has huge implications for fine-tuning performance and even preventative maintenance. It could drastically change how enthusiasts interact with and modify their cars.
Online stores offering STL files are having a cultural impact on the tuning scene. Smaller, independent tuning shops are able to compete more effectively with larger manufacturers, quickly producing high-quality, low-volume parts without the need for huge investments in traditional manufacturing processes. This is levelling the playing field, creating a more vibrant and diverse landscape for performance enthusiasts.
And this revolution isn't just for the aftermarket scene. As high-end manufacturers adopt 3D printing for bespoke components, we're likely to see a greater degree of personalization in luxury and performance vehicles. Consumers in this market may start to expect unique features or specific performance options, and this could lead to significant shifts in the overall design and manufacturing processes. It makes one wonder how 3D printing will impact the next generation of hypercars or limited-edition luxury models.
While still in its relatively early stages, 3D printing is undeniably changing how automobiles are designed, modified and enjoyed. It's a potent technology with vast potential to disrupt and reshape the industry in ways we're only beginning to grasp. It's clear that 3D printing is not just a fad; it's ushering in a new era of creativity and customization in the world of performance and luxury cars.
More Posts from tunedbyai.io: