The True Cost of Replacing Your Wheel Bearing
The True Cost of Replacing Your Wheel Bearing - Understanding the Core Components of the Bill
When discussing the true cost of replacing a wheel bearing and diving into "Understanding the Core Components of the Bill," we're really talking about breaking down the final invoice you receive for the service. This section isn't about navigating complex legislation or broad economic policy. Instead, it focuses on the specific line items that contribute to the total expense for your vehicle's repair, primarily the parts required and the labor involved in fitting them. For owners of performance-tuned cars or those with a penchant for premium vehicles, appreciating these details helps clarify where the investment in maintaining your machine is directed.
Examining the foundational elements that comprise the expenditure reveals several technically grounded factors.
The material itself isn't trivial; precision-engineered bearing steel undergoes specific metallurgical processes and advanced thermo-mechanical treatments. This is essential for the bearing's capacity to reliably manage the immense dynamic loads and resist fatigue over potentially millions of rotational cycles, representing a primary driver of the component's fundamental cost, far beyond the simple mass of metal.
Many contemporary vehicle platforms, particularly those focused on performance or refinement, integrate what was once a separate bearing into a complete hub module. This assembly often includes critical elements like the integrated magnetic reluctor or encoder necessary for the anti-lock braking and stability control systems, meaning replacing a failed bearing now necessitates replacing an entire sophisticated sensor package, significantly elevating the component cost compared to older press-in designs.
Beyond the mechanical exchange, servicing bearings on vehicles equipped with sophisticated driver-assistance or stability control frameworks may mandate electronic validation procedures or sensor recalibration routines post-installation. This adds a layer of specialized diagnostic time and technical expertise, an invisible labor cost not associated with purely mechanical repairs, requiring specific tools and software interfaces.
Accessing the wheel bearing on vehicles featuring complex multi-link suspension architectures or expansive high-performance brake systems, common on tuned or high-specification cars, isn't always a straightforward task. These intricate designs can pose significant challenges regarding access and procedural time for the bearing replacement, acting as a direct determinant of the necessary labor investment simply due to the surrounding vehicular packaging.
Furthermore, the lubricant sealed within the bearing unit contributes to its cost. This isn't merely generic grease but often an application-specific, engineered synthetic blend. It's formulated specifically to maintain lubrication integrity and film strength under the severe thermal and mechanical stresses encountered during dynamic, high-load operation, representing a hidden material science expense embedded within the unit price.
The True Cost of Replacing Your Wheel Bearing - How Vehicle Type Shapes the Price Tag
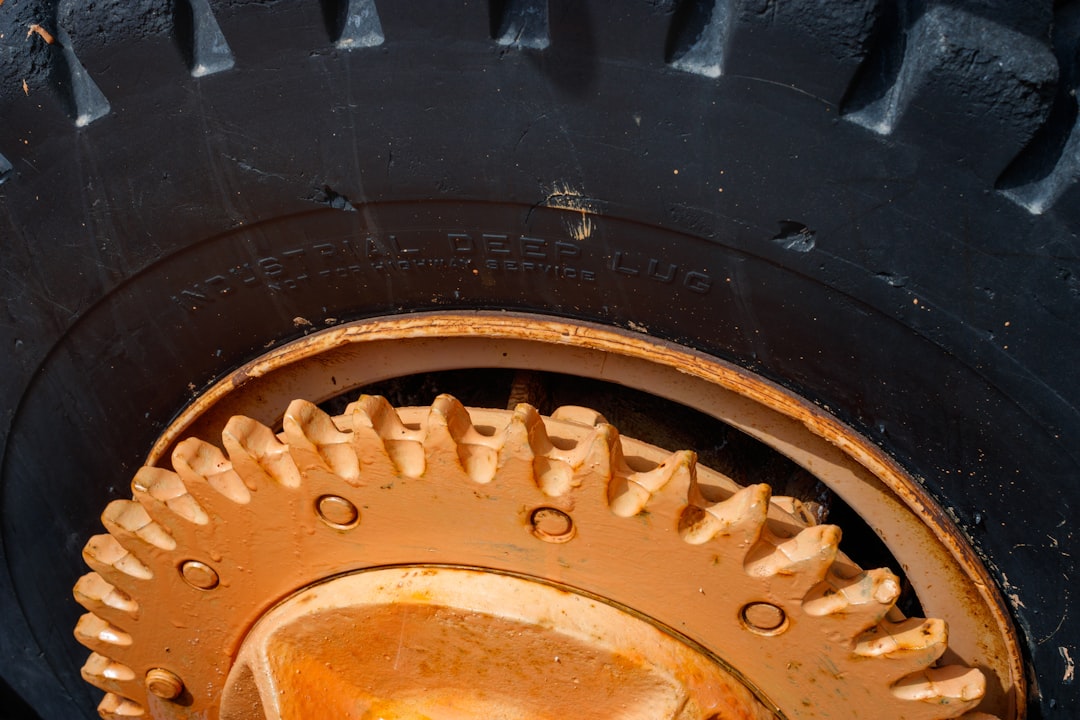
When you consider the cost of replacing a wheel bearing, the type of vehicle occupying your garage exerts a substantial influence on the final sum. Shifting from typical road cars to performance builds, luxury cruisers, high-end sports cars, or bona fide supercars invariably elevates the financial commitment. This isn't simply down to specific technical design choices already mentioned in prior discussions. It's often tied to the fundamental cost of parts engineered for higher demands, lower production volumes typical of specialized vehicles, or simply the premium associated with prestigious brands and their required component specifications. Acquiring a replacement bearing for something engineered for track performance or opulent comfort generally starts at a higher price point for the part itself compared to components for more ubiquitous models. Likewise, the expertise and facilities geared towards maintaining these distinct automotive segments might necessitate higher labor charges, reflecting a standard of service or specialized knowledge presumed necessary for such vehicles. Ultimately, the vehicle's inherent market position and intended capabilities build their own layer of expense into maintenance tasks like this.
Investigating further into the cost variances reveals how the specific vehicle platform itself fundamentally dictates the expense of a replacement wheel bearing. It's not a universal component, despite serving a common purpose.
Consider vehicles produced in limited numbers, perhaps those in the hypercar realm or specialized tuners' creations built on unique architectures. Their required wheel bearings aren't simply pulled from a vast production line shared with millions of sedans. Instead, they might be custom-specified or built in small batches. This fundamentally bypasses any meaningful economy of scale, a primary driver of cost efficiency in manufacturing. Consequently, the individual component price tag can appear disproportionately high when viewed against common parts, reflecting the engineering NRE (Non-Recurring Engineering) and setup costs spread over very few units.
Moving to high-performance models, think track-capable machines or those designed for aggressive driving dynamics. These vehicles subject their wheel bearings to stresses far beyond typical road use – extreme cornering forces, sudden load reversals during braking or acceleration, and elevated thermal conditions. Simply put, they demand bearings engineered with significantly higher dynamic load ratings and potentially more intricate internal architecture. Achieving this required robustness and durability often necessitates tighter manufacturing tolerances and the use of perhaps even more specialized materials or heat treatments compared to a standard passenger car bearing, which directly translates to a higher unit production cost.
A phenomenon seen particularly in luxury and exotic vehicle segments involves manufacturers specifying or even designing their own distinct wheel hub and bearing configurations. This isn't always for purely functional reasons; sometimes it's part of their specific platform architecture, other times it seems intended to tie owners strictly to the authorized service network. Regardless of the *why*, this creates a dependency on a manufacturer-controlled supply chain for that specific, often proprietary, component. The lack of readily available aftermarket alternatives, combined with the brand's inherent pricing strategy, means acquiring a replacement bearing can often be a significantly more expensive proposition than even a high-quality equivalent for a mass-market car.
As vehicles become increasingly sophisticated, especially in the electric performance or advanced luxury space, we observe wheel bearing units becoming less of a standalone component and more a nodal point within a complex system. On some cutting-edge designs anticipated around 2025, the bearing might be physically integrated into an active suspension module designed to counteract body roll, or even potentially part of a hub-mounted electric motor unit (though true hub motors are still less common than centralized drivetrains). This level of integration means that what appears to be a 'bearing' replacement might actually involve swapping out a much larger, more complex, and therefore considerably more costly assembly that incorporates multiple functionalities beyond just simple rotation.
Finally, consider the operational environment many performance or versatile luxury vehicles are expected to handle. Occasional track days, varied climates, or simply exposure to road salt and debris necessitate robust protection for the sensitive internal bearing elements. To address this, many high-end bearings feature advanced, multi-stage sealing solutions – think labyrinth seals combined with lip seals, designed to resist both contaminants and pressure washing effectively. While seemingly minor, engineering and implementing these sophisticated sealing arrangements adds layers of manufacturing complexity and cost to the component compared to simpler, single-lip seal designs found on less demanding applications.
The True Cost of Replacing Your Wheel Bearing - The Labor Contribution to the Total Cost
The time investment required from a technician significantly shapes the overall expense of replacing a wheel bearing, frequently accounting for the largest segment of the final invoice. For vehicles designed for high performance or those in the luxury segment, this contribution from labor becomes even more pronounced. It's less about the simple act of swapping parts and more about the precise, careful procedure demanded by modern, intricate automotive designs. Navigating the tightly packaged components and specialized assemblies common in such machines necessitates a level of expertise that goes beyond basic mechanical aptitude. This often requires familiarity with specific diagnostic procedures and proprietary tools. The process involves delicate disassembly and reassembly to ensure the integrity of surrounding systems, many of which are complex and costly. Ultimately, a substantial portion of the cost reflects this specialized skill, the time taken to execute the job correctly within the specific demands of a high-value vehicle, and the crucial attention to detail needed to maintain peak performance and functionality. Understanding that much of the expenditure resides in this skilled human input is essential for owners committed to properly maintaining their sophisticated automobiles.
Examining the labor involved in replacing a wheel bearing reveals specific nuances, particularly as vehicles become more complex and specialized. From an engineering perspective, it's not simply the act of removal and replacement, but the intricate processes demanded by modern designs.
One notable factor adding to labor time, particularly on performance vehicles, is the sheer necessity of navigating around highly sensitive and expensive adjacent components. Technicians must meticulously work around delicate items like carbon ceramic brake rotors, precision-machined suspension linkages, or integrated sensor arrays. The risk of damaging these parts during disassembly or reassembly is considerable, requiring slower, more deliberate actions, a factor implicitly built into the required labor hours or rate.
Furthermore, on certain advanced vehicle platforms, installing the new bearing isn't always a straightforward press-fit at ambient temperature. The manufacturer's specified procedure might call for thermal manipulation – heating the knuckle assembly or chilling the bearing itself to facilitate precise seating and ensure the correct interference fit is achieved. This adds a controlled, timed step to the process, necessitating specific equipment and verifying temperatures, moving beyond basic mechanical force.
Frequently overlooked is the mandatory replacement of numerous seemingly minor fasteners. Many high-stress applications, common on tuned or performance vehicles, utilize bolts and nuts that are specified as single-use or torque-to-yield. Once tightened to specification, their material properties are altered, rendering them unsuitable for re-use. Identifying, removing, and replacing all these specific fasteners, torquing each one to its exact specification (which might be a multi-stage angle-torque process), consumes significant labor time and adds a recurring material cost often lumped into the overall service charge.
Beyond the physical installation, the post-repair validation process on vehicles with sophisticated integrated systems requires significant labor. For tuned or performance cars, a simple road test isn't enough. The procedure often involves rigorous, manufacturer or tuning-house specified system checks and dynamic verification runs. This labor ensures that the newly fitted bearing and its associated speed sensors are properly communicating with complex ABS, traction control, and vehicle stability management systems, confirming functionality under representative load and speed conditions. It's a diagnostic validation phase that adds considerable time.
Finally, on the cutting edge of automotive integration, anticipated designs around 2025 may feature wheel bearing modules tightly coupled with other sensitive systems, possibly even within active suspension components or advanced electric drive units. Servicing these could necessitate unusual labor constraints, such as working within temperature or humidity-controlled environments to protect delicate electronics, or precisely managing the application and curing of specialized structural adhesives – complexities that directly impact the workshop requirements and the skill set, and therefore cost, of the labor provided.
The True Cost of Replacing Your Wheel Bearing - Front Wheel Work Versus Rear Wheel Work Differences
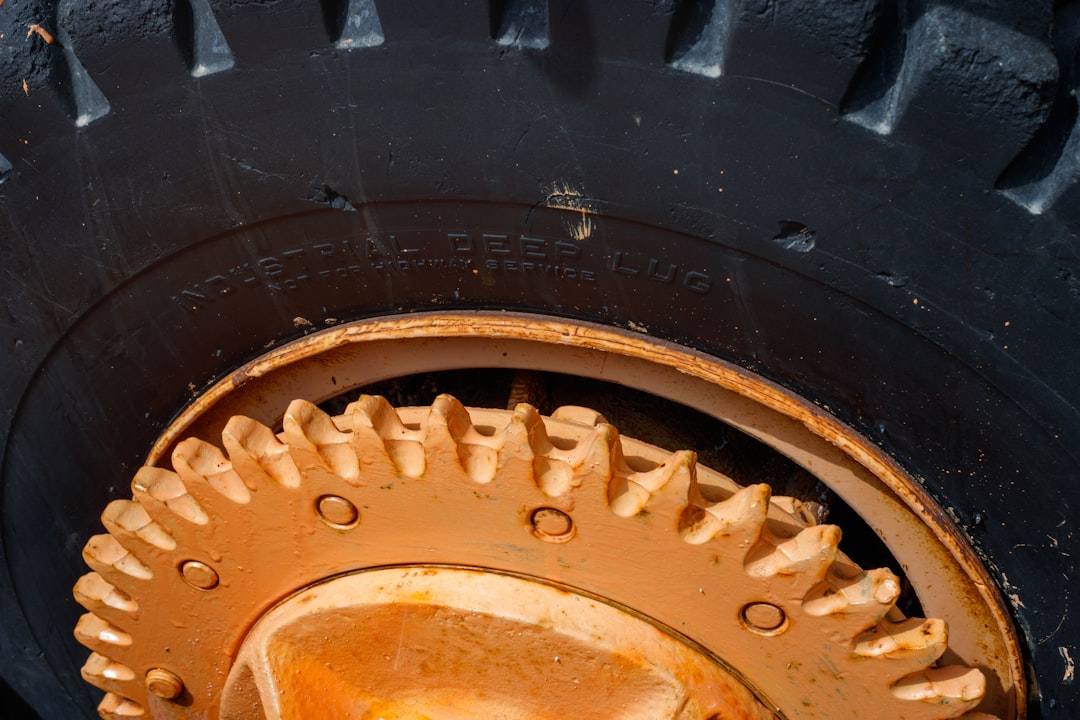
Understanding the divergence in maintenance approaches for front versus rear wheel bearings becomes particularly pertinent when dealing with performance machinery or upscale vehicles. The front axle carries the brunt of steering and usually a significant portion of the vehicle's weight, absorbing substantial forces during acceleration, braking, and cornering. This inherent burden often dictates that front wheel bearings might face higher wear rates and, consequently, be candidates for replacement more frequently than their rear counterparts on some platforms, despite advancements in sealed units. The repair itself frequently involves a higher expenditure.
In contrast, while the raw cost of a rear wheel bearing component might sometimes register lower, the job isn't automatically cheaper. Vehicle manufacturers often design rear suspension systems with considerable complexity – multi-link arrangements, integrated brake components, or specialized hub carriers common on sophisticated models – which can escalate the labor time required for access and removal significantly. The total bill then becomes a balance between the part price and the intricacy of the installation, leading to a range of potential outcomes where either front or rear might end up being the more expensive job depending entirely on the specific vehicle's engineering. There isn't one simple rule.
Navigating this requires recognizing that for tuned or high-end cars, replacing a wheel bearing on either end isn't merely a bolt-off, bolt-on task. It involves careful work around expensive adjacent systems and adherence to specific procedures. The cost difference between front and rear work isn't just about two different parts; it's profoundly shaped by how each axle's assembly is integrated into the overall vehicle architecture and the demands placed upon it, a factor only likely to become more complex with future integration of propulsion and chassis control systems.
It's often assumed that front wheel bearing replacement is inherently more complex or costly than rear, and historically, there's been some truth to that for many common vehicle layouts. However, peering closer from an engineering perspective reveals nuances, and the distinction isn't universally absolute, especially as vehicle designs evolve.
For one, consider front-wheel-drive architectures: the front bearing unit here isn't merely supporting load and managing cornering forces; it's simultaneously tasked with transmitting significant propulsion torque. This combination imposes a unique, multi-directional stress profile on the bearing and its surrounding housing, a mechanical load scenario distinctly different from a non-driven rear wheel, potentially influencing the fasteners, interfaces, and extraction methods required.
Then there's the packaging challenge presented by integrating the drive axle on driven front wheels. The necessary sealing provisions around the CV joint where it passes through the hub assembly introduce specific complexities. Disassembling and reassembling this interface requires careful attention to seal integrity, a step completely absent when working on simpler rear spindles or beam axles.
Furthermore, the front steering knuckle, which typically houses the bearing, serves as the pivot point for steering linkages and suspension arms. This geometric complexity means the bearing installation isn't just about fitting the part; it involves working within constraints imposed by steering axis inclination and scrub radius requirements. Achieving correct seating might be more sensitive compared to inserting a bearing into a relatively static rear suspension arm.
Engineers also dedicate particular effort to managing noise, vibration, and harshness (NVH) at the front axle. Because steering feel is paramount and the front is closer to occupants, the specifications and potentially the installation tolerances for front bearings can be tighter, demanding a level of procedural precision that might not be mirrored on the rear unless specifically required for acoustic isolation or other performance reasons.
Looking ahead to advanced architectures, particularly in high-performance segments, the notion that rear wheel work is inherently simpler is being challenged. Future active rear suspension systems or advanced electric drivetrains integrated tightly at the wheel hub – configurations we anticipate seeing more of towards 2025 – could introduce a level of electronic and mechanical complexity to the rear wheel bearing assembly that equals or even surpasses the demands currently associated with the front. The tools, diagnostic steps, and multidisciplinary expertise required for rear work on such vehicles could become significantly more involved, effectively blurring the traditional distinction in repair complexity.
The True Cost of Replacing Your Wheel Bearing - Considering the Parts Quality Factor
When facing a wheel bearing replacement, the quality of the component you choose injects another significant variable into the equation, directly influencing the overall cost, both immediately and down the line. It's tempting to look for the lowest price, and the market certainly offers options ranging from components seemingly identical to factory parts down to considerably cheaper alternatives. For owners invested in the performance or longevity of their vehicles – especially those with specific or high-value machines – this choice warrants careful consideration. While a more budget-friendly part might reduce the initial bill, these components often lack the stringent material specifications, manufacturing tolerances, and internal engineering details found in higher-quality options. They might not endure the dynamic loads, thermal cycling, or environmental exposure specific to certain vehicle platforms or driving styles, potentially leading to premature failure. Ultimately, for vehicles where performance, precision, and reliability are paramount, opting for a part that meets or exceeds original equipment standards often becomes an investment in avoiding repeat repairs and maintaining the vehicle's intended characteristics, even if the upfront cost is higher.
Stepping back to evaluate the component itself, the idea of 'parts quality' in a wheel bearing isn't a simple matter of branding or perceived prestige; it dives into the specifics of materials science and precision engineering. For the kind of loads encountered by a performance vehicle or the durability expected in a luxury tourer, the devil is truly in the details within that sealed unit. Consider the actual rolling elements – the balls or tapered rollers. High-quality bearings destined for demanding applications aren't just made from generic steel; their internal architecture, the specific alloys used, and even the structural design of the cage holding them, are engineered to withstand cyclical stresses and thermal loads far exceeding those seen in standard applications. This isn't arbitrary; it's about ensuring integrity over potentially millions of revolutions under intense pressure. Furthermore, that seemingly mundane grease packed inside is critical. We're not talking about common lubricant; its precise viscosity profile across a wide temperature range and the inclusion of specific Extreme Pressure (EP) additives are calibrated to maintain a protective film strength under crushing dynamic forces that would obliterate a lesser compound.
For contemporary vehicles, particularly those where safety and control systems are deeply integrated, the electronic aspect of the bearing is equally vital. If the wheel speed sensor is part of the unit, the quality of its magnetic encoder ring isn't negotiable. Its calibration and the density of its magnetic poles must align exactly with what the vehicle's ECU expects. Any deviation here isn't just a minor fault; it can fundamentally compromise the anti-lock braking or stability control systems, introducing unpredictable or delayed responses at critical moments. Ensuring this precision, along with the sheer mechanical resilience, demands rigorous validation. Reputable component manufacturers don't just produce parts; they employ sophisticated multi-axis test rigs and even accelerated corrosion chambers to simulate years of worst-case road conditions and performance abuse, pushing the components to failure points well beyond typical expectations.
It’s also a stark reality that the global supply chain includes sophisticated fakes. For parts like wheel bearings used in premium or performance cars, counterfeits can be alarmingly convincing externally. Yet, they often rely on substandard internal materials or manufacturing tolerances. Installing such a component isn't just a risk to longevity; it directly compromises safety by potentially failing catastrophically under load or providing inaccurate data to critical electronic systems. The diligence in sourcing is, therefore, not just about managing cost, but mitigating a genuine safety hazard originating from the component's quality, or lack thereof.
More Posts from tunedbyai.io: