Tuning a 2023 Challenger Weighing the Investment
Tuning a 2023 Challenger Weighing the Investment - Understanding the 2023 Challenger Platforms for Tuning
The 2023 Dodge Challenger presents a range of opportunities for performance tuning, drawing significant interest especially for its powerful V8 variants. Enthusiasts often explore recalibrating engine control parameters, such as fuel delivery and ignition advance, with the goal of increasing horsepower and torque output. However, the effectiveness and approach can vary notably depending on the specific engine and transmission configuration. While many owners report achieving satisfying performance improvements through tuning, grasping the distinct characteristics and potential pitfalls of each platform offered in that model year is crucial before committing to modifications. It's important to carefully balance the anticipated performance gains against the financial outlay and any potential technical complexities involved. Ultimately, maximizing the Challenger's potential requires a knowledgeable approach to ensure tuning investments align realistically with performance goals for this generation of the vehicle.
Here are some observations from examining the technical landscape for optimizing vehicles like the McLaren Artura as of mid-2025:
The core computing architecture governing the Artura's hybrid powertrain, encompassing both the combustion engine and electric drive units, presents a significant technical hurdle. Accessing and modifying critical operational parameters requires overcoming deeply embedded cybersecurity measures and sophisticated communication protocols, often demanding specialized low-level interface hardware and extensive platform-specific reverse engineering efforts rather than straightforward flash procedures.
Pushing the performance envelope in such a highly integrated hybrid system brings the thermal management strategy to the forefront. The interplay of heat generated by the turbocharged V6, the electric motor, the battery pack, and associated power electronics is complex. Achieving sustainable performance increases necessitates not only augmenting power delivery but also a comprehensive understanding and often a recalibration of the intricate cooling circuits and control logic to prevent components from exceeding operational temperature limits under prolonged stress.
While currently less diverse in variants than some older platforms, the Artura's technical foundation is built for evolution. Understanding the subtle hardware revisions, software updates, and potential regional variations that emerge over its production cycle is crucial. A tuning approach successful on one specific build might encounter unexpected incompatibilities or require significant adaptation on another, highlighting the need for meticulous model-year and software version verification.
Modifications aimed at increasing raw power interact directly with the Artura's dynamic control systems. The vehicle relies heavily on active aerodynamics, adaptive suspension, and sophisticated stability/traction management to translate its output into predictable handling. Altering power delivery without carefully considering and potentially recalibrating the control strategies for these systems risks upsetting the car's finely tuned dynamic character, potentially leading to compromised handling balance or unpredictable behavior at the limit.
Structurally, the Artura utilizes McLaren's newer architecture, designed from the ground up for hybrid integration. This provides a modern, lightweight, and rigid base. However, its relative youth compared to platforms with decades of aftermarket development means there's less cumulative knowledge regarding how the structure responds to extreme, sustained mechanical stresses far beyond factory intent. This contrasts sharply with the immense electronic complexity governing its operations, creating a scenario where pushing limits requires navigating sophisticated digital guardians interfacing with a physically robust, but less extensively 'stress-tested' in the aftermarket, new structure.
Tuning a 2023 Challenger Weighing the Investment - Performance Hardware Options and Associated Investment
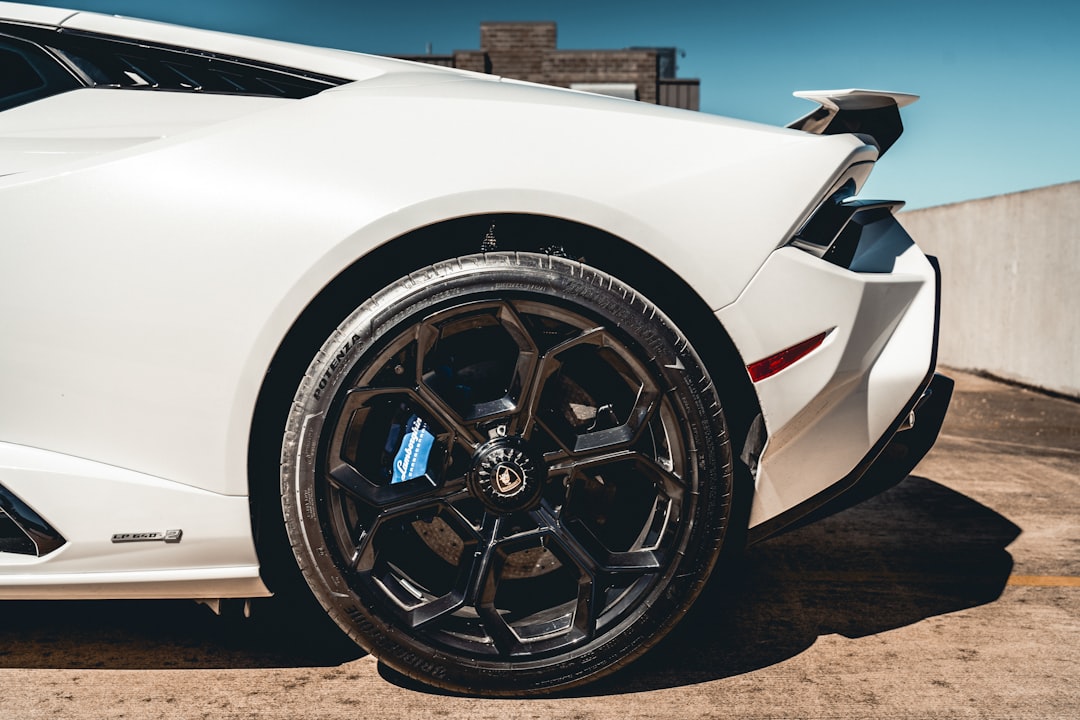
Exploring the hardware side of boosting a 2023 Dodge Challenger's capabilities means confronting a significant range in both cost and technical effort. Moving beyond just recalibrating existing systems, achieving substantial power increases generally involves acquiring and installing physical components. This spectrum runs from obtaining an unlocked powertrain control module (PCM) along with the necessary tuning interface – a step that permits more flexible calibration adjustments – all the way to integrating complex power adders like supercharger or turbocharger systems. While swapping in a modified PCM and applying a compatible calibration can indeed provide a noticeable improvement, especially for specific engine types, chasing truly significant horsepower numbers means committing to the substantial investment and labor tied to major hardware modifications. It's crucial to realistically evaluate the expected performance improvement against the considerable financial outlay for these parts and their installation. Simply purchasing bolt-ons without a clear understanding of their combined effect and the potential need for extensive retuning can easily lead to less than optimal results or create unexpected technical hurdles, highlighting that the investment extends well beyond the sticker price of the components themselves.
Considering the practical application of tuning modifications on platforms like the 2023 Challenger, a few observations emerge regarding common hardware investments and their potential outcomes as of mid-2025:
Investigating the effectiveness of enhanced charge air cooling for forced-induction variants frequently reveals it to be a notably efficient capital expenditure in the context of performance tuning. Addressing the detrimental impact of rising intake temperatures under demanding operation often provides more reliable, repeatable power gains for a given cost than pursuing marginal increases in peak boost or engine speed without such thermal stability.
Consideration of driveline components, specifically the torque converter in automatic-equipped models, suggests potential for significant improvement in acceleration metrics like 0-60 mph times or quarter-mile performance. This optimization of power transfer and launch dynamics can, in certain applications, yield more noticeable gains in specific acceleration tasks than simply elevating peak engine output without addressing how that power reaches the wheels effectively from a standstill.
Any analysis of increasing fuel injector capacity must inherently include the rest of the fuel delivery architecture. Real-world application demonstrates that the required flow rates at elevated power levels quickly exceed the capacity of the standard fuel pump and associated plumbing, rendering the injector upgrade ineffective or potentially problematic without a corresponding, and often non-trivial, investment in the supporting supply side.
While often considered solely for their effect on exhaust flow restriction, certain aftermarket catalytic converter designs are observed to influence exhaust pressure wave propagation and scavenging effects. Their internal structure and substrate properties can subtly interact with engine tuning and exhaust pulse dynamics, potentially offering modest, though often secondary compared to major changes, improvements to efficiency or torque characteristics beyond simple backpressure reduction.
Examination of camshaft profiles reveals a critical interplay with intake and exhaust manifold tuning; these components are often designed to leverage acoustic resonance effects within specific RPM ranges. Introduction of a new camshaft, despite ostensibly 'improved' lift or duration figures, can easily disrupt these intended harmonics, potentially shifting or even introducing significant weaknesses into the engine's power curve if the profile is not carefully matched to the entire system and the desired operating range.
Tuning a 2023 Challenger Weighing the Investment - The Impact of Software Tuning on Engine Behavior
Altering the software within a vehicle's engine control unit provides a direct path to influencing how the powertrain responds to driver input and environmental conditions. On a model like the 2023 Dodge Challenger, this typically means modifying the complex set of instructions governing everything from how quickly the throttle body opens based on pedal position to the intricate sequences of fuel delivery and spark timing under various load scenarios. The objective is often a shift in feel, perhaps a more immediate throttle response or a perceived improvement in acceleration, though the actual impact on measured performance or characteristics like fuel consumption can vary widely depending on the specific modifications. Understanding the 'cause and effect' of each parameter change requires careful observation and often relies on logging operational data from the vehicle's sensors to see how the engine is actually reacting. Unlike simple mechanical swaps, software changes interact dynamically across numerous maps and compensation tables, meaning an adjustment intended to improve one aspect can inadvertently affect another. Furthermore, accessing the necessary control modules on newer vehicles can require overcoming digital security measures, and having the capability to revert the system entirely to its original calibration state, essentially 'returning to stock', is a crucial consideration for troubleshooting or other needs. This layer of digital interaction adds a significant dimension of complexity beyond purely mechanical adjustments.
Examining the influence of software modifications on engine characteristics reveals several nuanced interactions. The engine control unit (ECU) utilizes sophisticated internal models to interpret data from myriad sensors. For instance, the system monitors acoustic feedback via knock sensors to detect the onset of detonation, enabling it to dynamically pull ignition timing back, often on a cylinder-by-cylinder basis. Recalibrating this strategy allows tuners to operate timing closer to the thermodynamic limit for peak power, though the margin for error is entirely reliant on the accuracy of the calibration and environmental conditions, posing inherent risks if not conservatively managed. Furthermore, the operational parameters for systems like variable valve timing are purely digital; adjusting the mapping of valve lift, duration, and phase across varying engine speeds and loads offers a powerful means to sculpt the engine's torque curve, potentially optimizing for high-RPM power at the expense of low-end grunt or vice-versa, fundamentally altering the engine's feel.
The perceived response from the accelerator pedal is also a direct output of software logic, translating the driver's input into a calculated torque request and subsequent command signals to the electronic throttle body, fuel injectors, and ignition system. Modifying the 'pedal map' can artificially heighten or dull responsiveness, creating a subjective sense of urgency or refinement that may not directly correlate to the engine's actual power output at that moment, effectively filtering the driver's connection to the powertrain. Similarly, fuel-saving technologies such as cylinder deactivation systems rely entirely on software logic to determine their engagement strategy; recalibrating or disabling these functions via tuning can ensure the full engine displacement is always active for consistent power delivery and potentially a more desirable exhaust note, albeit at the cost of the modest efficiency gains the factory calibration was designed to achieve. Finally, the precision required for optimal combustion during transient events, like a sudden increase in throttle, is handled by complex software algorithms that manage acceleration enrichment and wall-wetting compensation models. Tuning these parameters is critical for avoiding detrimental lean spikes or excessive richness that can impact performance, emissions, and engine longevity during dynamic operation, and perfecting these intricate adjustments is often a significant challenge.
Tuning a 2023 Challenger Weighing the Investment - Weighing the Durability Considerations of Modified Challengers
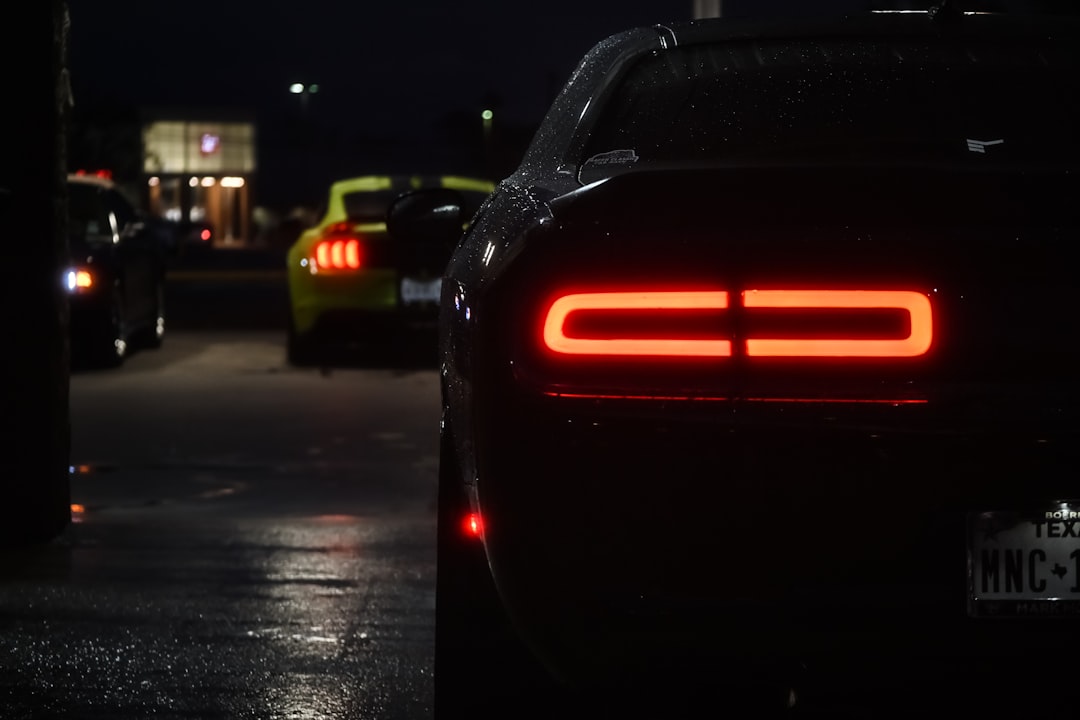
Pushing a Dodge Challenger beyond its factory specifications through tuning and aftermarket parts invariably introduces questions about how long the various systems will tolerate the increased demands. While unlocking extra power or sharpening handling feels rewarding, it's crucial to confront the reality that standard components were engineered for a specific level of stress. Significantly increasing engine output, for example, particularly with methods like forced induction, means critical internal parts, along with the cooling and lubrication systems, are working harder than intended. This heightened workload can certainly accelerate wear or even lead to outright failure if the supporting modifications aren't comprehensive or the original parts aren't robust enough for the new performance level. Similarly, modifying the transmission, driveshaft, or rear differential to handle sharper launches or higher loads requires careful consideration; an improperly balanced or insufficiently strengthened driveline element can become a new weak point under aggressive use. It's a balancing act where chasing maximum performance often means reducing the built-in margin of safety that contributes to a stock car's longevity, demanding a realistic assessment of the trade-offs involved.
Delving into the long-term consequences of pushing these machines beyond their original calibration brings several reliability aspects to the forefront, warranting careful consideration from a purely engineering standpoint as of mid-2025. For example, simply elevating peak engine output means critical internal components, like piston rings and connecting rod fasteners designed for specific operational loads and duty cycles, are subjected to stresses much nearer, or even exceeding, their calculated fatigue limits over time.
Further, aggressively recalibrating parameters such as ignition timing or air-fuel ratios, aiming for maximum power in specific conditions, can unintentionally generate highly localized thermal spikes in components like the upper piston surfaces or exhaust valve faces. This intense heat exposure accelerates unfavorable microstructural alterations within the metal alloys, potentially leading to brittleness and premature failure.
Modifications aren't always about sheer power; they can also subtly alter the engine's operational dynamics. Changes might shift the inherent harmonic frequencies and introduce unforeseen torsional oscillations within the rotating assembly, placing undue stress on components like crankshaft keyways or the bolt patterns securing the flywheel or flexplate – elements typically designed for the factory power pulse profile.
Maintaining significantly elevated engine speeds and higher average loads for extended periods, beyond the duty cycle factored into the original design, invariably increases the mechanical stress and thermal burden on auxiliary systems. Components like the alternator, power steering pump, and coolant pump often see their operational lifespan considerably shortened under these conditions.
Finally, the downstream effects are equally important. Sustained application of higher torque levels and the associated increases in acceleration forces translate directly into greater mechanical stress and thermal load on the vehicle's driveline components. This means the transmission and differential fluids operate at much higher temperatures, compromising their lubricating effectiveness and consequently accelerating wear on gears, bearings, and seals within those assemblies.
More Posts from tunedbyai.io: