Understanding Bank 2 Sensor 1 Location, Function, and Common Failure Patterns in V-Configuration Engines
Understanding Bank 2 Sensor 1 Location, Function, and Common Failure Patterns in V-Configuration Engines - Physical Location Behind Bank 2 Cylinders 2-4-6-8 in V Engine Setup
The physical placement of Bank 2, where cylinders 2, 4, 6, and 8 reside in V-type engines, is generally found toward the rear of the engine assembly. This bank's distinction is important as it houses the first oxygen sensor, designated as Bank 2 Sensor 1. Some might find this counterintuitive, as you'd expect the "first" sensor to be on the bank with cylinder number 1. Its location further back and upstream from the catalytic converter places it in a challenging environment where heat and engine byproducts are most intense. While intended to help with emissions control, this positioning also creates a situation where the sensor is prone to specific failures. Identifying its exact location can be a nuisance for mechanics and vehicle owners, especially when manufacturers use different numbering conventions. This means accurate engine diagnostics hinge on correctly deciphering the engine's layout and where Bank 2 and its associated sensor actually sit.
Okay, so we're digging into where exactly Bank 2 sits in a V-configuration engine, specifically cylinders 2, 4, 6, and 8. It's interesting how manufacturers place these cylinders opposite of Bank 1 (where 1, 3, 5, and 7 reside). But here's a curveball: not every carmaker plays by these rules. Some, like General Motors, have their own twist on this setup, which can get you scratching your head if you're not aware.
As of today, December 8, 2024, what's clear is that knowing the physical layout of these banks is key, not just for enthusiasts but also for us who are deep into engine diagnostics. It's worth noting, the specific placement of Bank 2 has a tangible effect on components, particularly exhaust systems and fuel delivery. It can be a bit of a pain for those of us getting our hands dirty with maintenance and repairs. This side of the engine typically runs hotter, leading to an increased chance of sensor malfunction.
Talking about sensors, the oxygen sensor (O2) for Bank 2, Sensor 1, is always upstream of the catalytic converter, unlike its counterpart on Bank 1. That's a smart move for monitoring the engine's air-fuel ratio accurately. Why? Because its upstream placement lets it sniff the exhaust before it's altered by the catalytic converter. This sensor placement also dictates how the sensor interacts with the engine management system, affecting diagnostics significantly. One thing I've noticed is that common issues, like wiring faults or sensor contamination, frequently plague this O2 sensor. It's vital to accurately identify and understand the sensor locations for troubleshooting emissions in V-engine setups. These configurations are predominantly found in V6 and V8 engines; inline engines simply don't have these complexities.
Understanding Bank 2 Sensor 1 Location, Function, and Common Failure Patterns in V-Configuration Engines - Upstream Position Before Catalytic Converter in Exhaust Flow
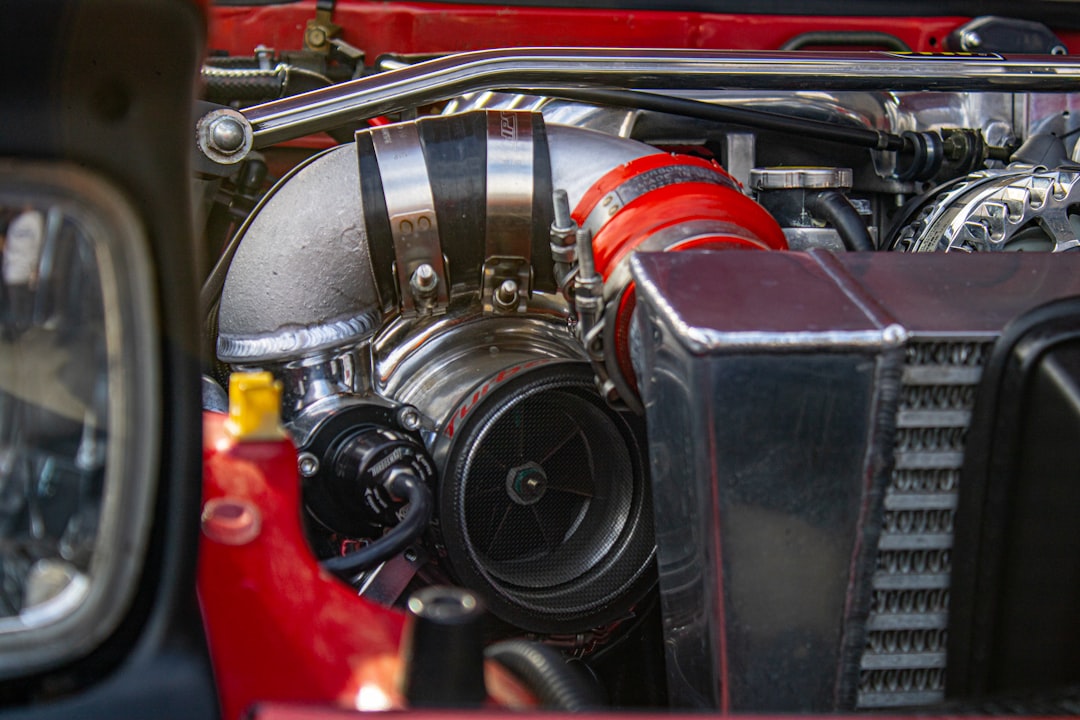
Bank 2 Sensor 1, the upstream oxygen sensor, is positioned in the exhaust flow before the catalytic converter. You'll find it either in the exhaust manifold itself or somewhere in the exhaust pipe, specifically on the side of the engine that houses cylinder number 2. Its job is to give the engine control unit (ECU) critical data on the air-fuel mix, allowing the ECU to fine-tune things for better engine performance and lower emissions. It's a harsh environment up there, ahead of the catalytic converter, where this sensor measures the oxygen levels in the exhaust gases. This placement, while effective, isn't without its challenges. Failures are not uncommon; think slow response times or wayward voltage readings. It kind of makes you wonder about the trade-offs in engine design. Such issues can throw a wrench in the works, messing with engine efficiency and emissions. Honestly, it seems like a constant battle to keep these sensors functioning correctly, highlighting why accurate diagnostics and timely maintenance are so important, especially in these V-configured engines.
"Upstream" means this sensor, Bank 2 Sensor 1, is sniffing the exhaust gases right after they leave the engine, before they hit the catalytic converter. This early sampling is vital. It's the first peek into how well the engine is burning fuel and mixing it with air, before any exhaust cleanup happens. It seems obvious, but the extreme heat at this point is no joke. We're talking temperatures that can soar past 1,000°F. This is tough on the sensor, making it prone to wearing out sooner than expected. I've seen this especially in cars that are pushed hard or stuck in constant stop-and-go traffic.
What's crucial is that the data from Bank 2 Sensor 1 is a cornerstone for the engine control unit (ECU) in figuring out the optimal air-fuel mix. Mess this up, and you're looking at an engine that's either too rich or too lean, neither of which is good for performance or your wallet at the pump. Interestingly, some carmakers use heated oxygen sensors (HO2S) here. These get up to operating temperature faster, helping cut down on emissions right when you start the car, which is a critical period for any engine. It's a clever design, but it does add another layer of complexity to the whole system.
In many of these V-engines, this sensor is also unfortunately located where it gets a front-row seat to oil and coolant leaks. This kind of contamination can skew the sensor's readings, tricking you into thinking there are engine problems when there aren't. I find it fascinating how exhaust flow changes so drastically from idle to full throttle. Bank 2 Sensor 1 has to accurately relay these changes. It's essential for the ECU to tweak fuel injection on the fly. And let's not forget about diagnostic trouble codes (DTCs) like P0420, which usually point to issues with the catalytic converter downstream. But guess what? A faulty upstream sensor can sometimes trigger these too. It's all connected.
Sometimes, the wiring for Bank 2 Sensor 1 runs alongside Bank 1 components. This can lead to a mess of signals if both sensors aren't playing nice. The variety of sensor technologies used here is also something to note. Wideband O2 sensors are gaining popularity because they offer finer control over the air-fuel ratio than narrowband ones. It's critical to know what you're dealing with for proper diagnostics. Lastly, even slight manufacturing differences can affect how and where this sensor fits, which can throw off readings. It's a reminder that thorough testing is always in order, no matter how identical two cars may seem.
Understanding Bank 2 Sensor 1 Location, Function, and Common Failure Patterns in V-Configuration Engines - Direct Impact on Air Fuel Ratio Through ECU Feedback Loop
In V-configuration engines, Bank 2 Sensor 1 directly influences the air-fuel ratio by sending immediate feedback to the engine control unit (ECU). This oxygen sensor, positioned before the catalytic converter, assesses exhaust gases and transmits real-time data. The ECU then adjusts fuel injection to sustain an optimal air-fuel mix. Should the sensor falter due to factors like heat or contamination, the ECU's ability to balance the mixture is compromised. This can lead to the engine running too rich or lean, impacting performance, fuel economy, and emissions. It's a bit of a design flaw, if you ask me, making the sensor prone to errors that ripple through the engine's operation. This highlights the sensor's crucial role in the engine's management system. Grasping the intricacies of the feedback loop involving Bank 2 Sensor 1 is vital for accurate diagnostics and efficient tuning of these engines. It's a complex dance of chemistry and mechanics, and when one element is off, the whole system suffers.
The engine control unit (ECU) is in a constant dialogue with Bank 2 Sensor 1, using its feedback to tweak the air-fuel ratio on the fly. It's a bit of a high-wire act; even the slightest hiccup in the sensor's readings can throw the whole system off, leading to performance hiccups that are often mistakenly chalked up to mechanical issues. You start to question the initial diagnosis when the real culprit is hiding in plain sight. This sensor lives in a pretty brutal environment, where temperatures can swing wildly, leading to a kind of thermal fatigue. I've seen cases where these sensors, especially when they're upstream, degrade twice as fast as their downstream counterparts. It's fascinating and a little frustrating how much stress they're under.
Since Bank 2 Sensor 1 is sampling the exhaust before it even hits the catalytic converter, it's extremely sensitive to any changes in exhaust flow. And let me tell you, that flow can vary dramatically depending on what the engine's doing, from idling to hitting high RPMs. The sensor's ability to accurately read these oxygen levels is paramount. This is further complicated by the fact that in V-engines, the design itself poses unique challenges. Things like exhaust crossflow and the specific firing order can mess with the exhaust pressure, which in turn affects how well the sensor can do its job. It really makes you appreciate the intricate balance that's being maintained.
Contamination from oil or coolant is a real issue, too. Not only does it mess with the sensor's accuracy, but it can also trigger false positives during diagnostics. This can lead mechanics down a rabbit hole, replacing parts that aren't actually broken. And while narrowband sensors have been the norm for ages, the newer wideband O2 sensors are a game-changer. They can monitor a broader range of air-fuel ratios, helping the ECU fine-tune fuel delivery more effectively. But, with some manufacturers adding dual heater circuits to get these sensors up to speed faster (which does cut down on cold start emissions), there's a flip side: an increased risk of the sensor burning out due to overheating.
Even the smallest variations in manufacturing can lead to noticeable differences in how these sensors perform. A tiny misalignment during installation can throw off the readings, so getting the sensor's position just right is crucial. And it's not just about keeping the engine running smoothly; this feedback loop from Bank 2 Sensor 1 is vital for staying on the right side of emissions regulations. Mess up the data, and you might find yourself staring down a "check engine" light and failing your emissions test. What's really interesting is how one faulty sensor, especially when it's misreading combustion conditions, can set off a chain reaction of diagnostic trouble codes. It's a domino effect that can make figuring out what's actually wrong quite the puzzle.
Understanding Bank 2 Sensor 1 Location, Function, and Common Failure Patterns in V-Configuration Engines - Most Common Failure Signs Through P0156 Error Code Display
When your car's computer throws a P0156 error code, it's signaling a problem with the heated oxygen sensor circuit for Bank 2 Sensor 2. This sensor sits downstream from the catalytic converter, keeping tabs on oxygen levels in the exhaust gases. It's a bit of a watchdog for your engine's efficiency and emissions. But this sensor doesn't have it easy. It's prone to a few common hiccups: wiring that's seen better days, the sensor itself calling it quits, or leaks in the exhaust system that mess with its readings. When these issues crop up, you'll likely notice your check engine light on, a dip in fuel economy, and an uptick in emissions—not exactly what you want from your ride. Ignoring the P0156 code isn't wise; it's not just about a pesky light on your dash. Drive around like this for too long, and you're looking at potential engine damage, which is a whole other level of headache. Getting to the bottom of this code means playing detective, as several culprits could be to blame. Proper diagnostics are crucial here. You need to accurately pinpoint what's causing the sensor to act up, ensuring your vehicle runs as it should, without unnecessary pollution or a hit to your wallet at the gas pump.
When the diagnostic system throws a P0156 code, it's signaling a hiccup with the heated oxygen sensor circuit for Bank 2 Sensor 2, specifically its role in keeping tabs on oxygen levels post-catalytic converter. It's intriguing how this sensor, nestled just after the catalytic converter on the engine's second bank, can be so pivotal. A common thread with this error code seems to be a faulty oxygen sensor itself or perhaps some wear and tear on the wiring, even corrosion getting in the way of proper function. Also, any quirks in the exhaust system can muddy the sensor readings, which isn't surprising given its location.
It's worth noting that when this P0156 code pops up, you're likely to see the check engine light on, and don't be surprised if your fuel economy takes a hit or your tailpipe emissions start to climb. This sensor, which by the way often uses a four-wire setup — a ground, a reference voltage around 0.5 volts, and two for the heater — sends its findings back to the engine control module. The whole point is to fine-tune that air-fuel mixture. But I can't help but wonder if sometimes, it's not the sensor at fault but something else entirely, like oil or coolant contamination, or even a sneaky exhaust leak, that's triggering the code.
You'd think that dealing with this would be straightforward: check the wiring, maybe test the sensor with a multimeter, and give the exhaust system a once-over. But it's not always that simple. The fact that driving around with this unresolved issue could lead to engine damage really underscores how critical it is to get to the bottom of it. It seems like a complex puzzle, doesn't it? Multiple factors could be at play, all leading back to this one error code. It just goes to show the importance of a thorough diagnostic approach, rather than jumping to conclusions about the cause of the P0156 code.
Understanding Bank 2 Sensor 1 Location, Function, and Common Failure Patterns in V-Configuration Engines - Wiring Harness Connection Points and Circuit Testing Methods
In the world of car diagnostics, particularly with V-engines, knowing the ins and outs of wiring harnesses and how to test circuits is a big deal, especially when dealing with finicky components like the Bank 2 Sensor 1. This oxygen sensor is tasked with measuring oxygen levels in the exhaust, a tough job considering the harsh conditions it operates under. To keep things running smoothly, technicians often turn to a variety of circuit testing methods. Visual checks are a good start, looking for obvious signs of wear or damage. Continuity tests are another tool, helping to trace any open or short circuits within the wiring harness that might throw off sensor readings and, consequently, mess with the engine's performance. It's not just about finding the problem, but also understanding how these issues can mislead diagnostics. Take corroded terminals or faulty connections, for instance; they can muddy the waters, making it harder to pinpoint the real issue. This whole process underscores just how vital it is to be methodical and thorough when testing circuits. Without a solid grasp of these techniques, maintaining the precise operation of the engine management system becomes a guessing game. And let's be honest, nobody wants to play guessing games with their engine.
The wiring harness connecting Bank 2 Sensor 1 is quite intricate, often bundled with various other engine components. This complexity makes it susceptible to electromagnetic interference, increasing the risk of short circuits or signal degradation. This situation can lead to inaccurate diagnoses. I find it curious how these intertwined wires can so easily mislead diagnostics. When testing for continuity, which is crucial for this sensor, we usually look for low resistance in the harness, typically under 5 ohms. Higher resistance often points to corrosion or damage within the wires, significantly hindering the sensor’s operation. It’s always a bit of a puzzle to pinpoint the exact location of these issues.
Observing the output voltage of Bank 2 Sensor 1, which ranges from 0.1 to 0.9 volts, reflects a broad spectrum of air-fuel ratios. This variability is critical for diagnosing if the sensor is accurately reflecting the engine’s conditions or if it's beginning to fail. It's fascinating how such a wide range can be indicative of either proper function or impending failure. Oxygen sensors, including Bank 2 Sensor 1, are known to fail prematurely due to thermal stress. I often wonder about the efficiency of thermal cycling tests in predicting a sensor’s lifespan. Rapid temperature changes can cause internal components to fail, a fact that underscores the harsh conditions these sensors endure.
Corrosion at the connection points of the wiring harness can lead to high resistance paths, causing intermittent sensor operation. A simple visual check for moisture and corrosion often reveals more than one might expect. The necessity of such inspections seems almost basic, yet they're frequently overlooked. Using an oscilloscope for circuit testing gives a real-time look at voltage fluctuations from Bank 2 Sensor 1. This method offers a clearer view of the sensor's performance compared to a standard multimeter, which can miss brief, transient problems. The detailed data from an oscilloscope can be incredibly revealing.
The integrity of the ground connection in the wiring harness is paramount. A poor ground can distort sensor readings, making it vital to ensure the ground point is clean and secure. This step is essential for accurate signal transmission. It's a reminder of the foundational aspects of diagnostics that can easily be neglected. High temperatures not only affect the sensor itself but can also degrade the wiring insulation over time. Using high-voltage insulation testers to check for insulation resistance can expose compromised wiring that might not be apparent visually. The degradation of insulation under heat is a slow but significant process.
The oxygen sensor operates within a feedback loop where rapid response times are critical. I find the use of faster testing methods, like pressure sensors alongside O2 sensors, particularly insightful for cross-verifying engine conditions. This approach enhances diagnostic accuracy, a point that can't be overstated. Even minor manufacturing differences in wiring harnesses can cause significant discrepancies in sensor output. Understanding the specific calibration requirements when replacing or repairing components in this system can save substantial time and resources in troubleshooting. It's surprising how much variability exists between seemingly identical parts.
Understanding Bank 2 Sensor 1 Location, Function, and Common Failure Patterns in V-Configuration Engines - Replacement Steps Without Breaking Exhaust Manifold Studs
Replacing the Bank 2 Sensor 1 in V-configuration engines can be tricky, especially when it comes to the exhaust manifold studs. You really don't want to break these during the process. A smart move is to hit those studs with some penetrating oil well before you plan to start wrenching. Give it time to work its magic on any rust or corrosion. When you're ready to remove the sensor, go slow and steady. Make sure you're not putting any unnecessary stress on the studs that could cause them to snap. And hey, if a stud does break, it's not the end of the world if you're prepared to extract it.
Another thing, always go for quality replacement parts and don't skip the anti-seize compound on the threads. This isn't just about making future removals easier; it's also about getting a good seal. Honestly, these steps might seem small, but they can make a huge difference. It's all about making the job, and any future maintenance, as smooth as possible. Skipping these can make the task more difficult.
Exhaust manifold studs endure some of the most brutal conditions under the hood, with temperatures soaring beyond 1,000°F. It's a wonder they hold up as well as they do, really. This kind of heat cycling can lead to serious metal fatigue over time. It makes you question the choices made in material selection for these components, as they're typically forged from high-strength steel alloys, like grade 8. These are supposed to withstand high temperatures and stress, but when it comes time to remove them, the risk of breakage is significant, especially if they've been twisted the wrong way during prior maintenance.
Corrosion is another beast altogether. In areas where moisture is prevalent or road salt is used in winter, these studs can seize up, making removal a delicate operation. Applying lubricants that resist moisture might help, but it's not a cure-all. And let's not overlook the importance of proper torque during reinstallation. Overdo it, and you're increasing the chances of snapping a stud, which brings its own set of headaches, requiring extraction tools and adding to the labor involved.
When a stud does break, getting it out is no small feat. It calls for specialized tools like reverse drills or extraction kits, and a steady hand to avoid damaging the surrounding threads. The heat cycling method—heating and then cooling the stud—can help break the corrosion's hold, but it's not foolproof. I've always wondered if there's a better way, considering the advancements in material science.
Using anti-seize compounds during installation is a good preventive measure, acting as a barrier against corrosion. It seems like a simple step, but it can save a lot of grief down the line. Engine vibrations also play a role, potentially loosening the studs over time. Regular checks might catch a loose stud before it breaks, avoiding more extensive repairs. And while impact tools are handy, they can be too much for these studs, risking breakage due to shock loads. A careful, manual approach is often best.
Replacing these studs requires a methodical approach: removing the manifold, cleaning the mounting surfaces, and ensuring the new studs are inserted evenly to minimize stress. It's a detailed process, and each step is critical to avoiding future issues. It really makes you appreciate the engineering that goes into even the smallest parts of an engine.
More Posts from tunedbyai.io: