Understanding Engine Pinging A Critical Guide for High-Performance Engine Tuning and Prevention
Understanding Engine Pinging A Critical Guide for High-Performance Engine Tuning and Prevention - How BMW M3 Competition Pack Air Intake Design Prevents Engine Knock
The BMW M3 Competition Pack's air intake system is engineered to combat engine knock, a detrimental issue impacting performance. A key aspect is the integration of features like a Dinan carbon fiber cold air intake, which significantly boosts airflow. This increased airflow capacity plays a vital role in delivering a greater volume of air to the engine, thus enhancing performance. Moreover, the optimized airflow is instrumental in maintaining the ideal air-fuel mixture, a critical factor in preventing detonation that leads to knocking. The design meticulously considers material selection and construction, effectively minimizing heat soak. This ensures the potent S58 engine operates optimally, maximizing both power output and durability. By carefully managing the air intake process, the M3 Competition Pack strives to protect the engine from the damaging effects of knock, allowing the vehicle to unleash its full potential.
The BMW M3 Competition's air intake system is meticulously engineered to maximize airflow and minimize turbulence, aiming to promote stable combustion and prevent the dreaded engine knock. The design, likely born from extensive simulations and testing, strives to feed the engine with a consistent and cool air supply, a critical factor in achieving optimal power output without encountering destructive pre-ignition events.
One interesting aspect is the use of a multi-stage filtration system which not only enhances air volume but also works to maintain lower intake temperatures, a subtle yet significant detail for maximizing performance and mitigating the risk of knock. It seems they've employed advanced computational fluid dynamics (CFD) tools to model and predict the air flow throughout the intake path. This allows for a targeted optimization of every component, striving for maximum efficiency while minimizing the likelihood of knock.
Additionally, they've incorporated thoughtfully placed resonators within the intake manifold, intended to dampen turbulent airflow and contribute to smoother engine operation. There's a clear attempt to engineer for optimized throttle response by potentially implementing a dual-throttle body system. This innovative approach theoretically leads to a more controlled and uniform airflow distribution into the engine's cylinders, potentially lessening the risk of detonation across varying engine loads.
Another aspect of the design is the implementation of a sophisticated engine control unit that integrates with knock sensors. This dynamic system continuously monitors critical engine parameters, allowing it to adapt in real-time, dynamically altering the fuel delivery and ignition timing to counteract knock-inducing conditions.
While the use of lightweight materials like carbon fiber is often touted for weight reduction, in this case, it also contributes to the overall thermal management of the system. This is achieved by minimizing the thermal mass which can absorb heat, potentially jeopardizing optimal combustion temperatures and creating a higher risk of knock. It's a well-considered detail that hints at the design team’s thorough approach.
Furthermore, it appears they have taken steps to minimize heat soak by cleverly guiding outside air into the system, keeping combustion air as cool as possible. This design detail suggests an awareness of the importance of mitigating the detrimental impacts of high air temperatures on engine performance and potential knock issues. It's a fascinating example of leveraging careful engineering to minimize environmental impact on the combustion process.
It's speculated that the implementation of variable intake geometry may further enhance performance and knock prevention by optimizing the air intake across different RPMs. This would effectively lead to improved torque and power delivery while concurrently reducing the likelihood of encountering the knocking phenomenon.
The pursuit of high performance doesn't come without challenges, and the M3 Competition's air intake system demonstrates a considerable effort to intelligently address the risks associated with performance tuning, particularly engine knock. By balancing innovation and engineering principles, the M3 aims to provide a driving experience that showcases exhilarating performance without compromising reliability. The innovative technologies and engineering solutions discussed in this context are a testament to the ongoing development within the automotive industry as designers strive to meet the growing demand for increasingly potent and reliable high-performance vehicles.
Understanding Engine Pinging A Critical Guide for High-Performance Engine Tuning and Prevention - McLaren Artura Hybrid System Integration with Advanced Knock Detection
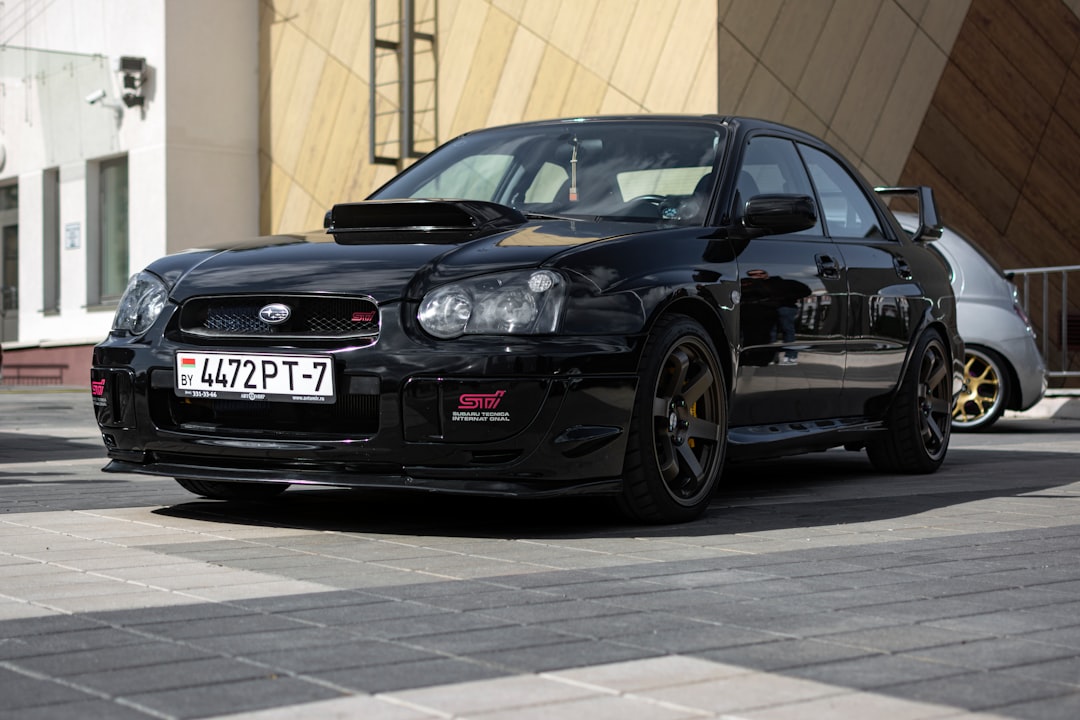
The McLaren Artura is a compelling example of how hybrid technology is reshaping the supercar landscape. At its heart is a unique 3.0-liter twin-turbo V6, boasting a 120-degree bank angle—a departure from the usual 60-degree designs seen in many cars. This engine, paired with an electric motor, delivers a potent 671 horsepower and 531 lb-ft of torque. McLaren's expertise in lightweight design is evident in the Artura's Carbon Lightweight Architecture (MCLA) chassis, contributing to the vehicle's remarkable performance.
Furthermore, advanced knock detection systems are integrated to prevent damaging engine pinging, which can occur when the fuel mixture ignites too early. This is crucial for maintaining performance and reliability, especially when dealing with the high power output of this hybrid system. The Artura, in essence, attempts to reconcile the exhilarating performance typically associated with McLaren's larger V8s with the fuel efficiency and performance benefits of hybrid technology.
It's interesting to see how McLaren has integrated the hybrid system, especially the electric motor housed within the gearbox. This clever engineering allows for smooth power delivery across the entire engine's operating range. This design, combined with its aerodynamic bodywork, pushes the boundaries of performance, making it a benchmark within the high-performance hybrid supercar space. The Artura, with its price tag around $254,100, successfully blends high performance and cutting-edge technology, representing a notable shift in luxury car design.
The McLaren Artura's hybrid system is a fascinating blend of a 3.0-liter twin-turbo V6 and an electric motor, a design choice that pushes the boundaries of conventional supercar engineering with its 120-degree bank angle – a departure from the typical 60-degree setup. This unconventional configuration, coupled with the electric motor integrated within the gearbox's bell housing, results in a combined 671 horsepower and 531 lb-ft of torque. The Artura, built upon McLaren's Carbon Lightweight Architecture (MCLA), emphasizes lightweight construction, a common theme in supercar design, pushing the performance envelope by reducing weight and improving agility. Interestingly, the Artura's hybrid setup isn't just about performance; it also provides improved torque at lower engine speeds, hinting at a broader application beyond just high-octane driving.
The Artura, being a modern supercar, benefits from advanced knock detection systems. This is particularly crucial considering the potential for knock to occur under high-performance driving scenarios. It appears McLaren's system utilizes a more sophisticated method than many conventional acoustic-based sensors. The Artura's approach seems to rely on precise vibration analysis to identify the early signs of knock. This enhanced sensitivity in identifying the very subtle changes in engine vibrations associated with knock likely translates into a better ability to differentiate true knock from benign combustion patterns. This precision is key to preventing engine damage while maintaining optimal performance.
It's likely that the control unit utilizes machine learning to adapt and optimize fuel and ignition timing in real-time based on various conditions, including driver input and ambient factors. Interestingly, they've employed carbon fiber, often found in structural elements, within the intake manifold, probably contributing to thermal management. This would align with strategies that reduce the risk of heat soak, a factor that could play a role in promoting pre-ignition conditions leading to knock. The dual intercooler setup and water-to-air cooling system further point towards a careful approach to managing engine temperatures, minimizing potential knock-inducing conditions.
The addition of a sophisticated telemetry system provides detailed performance insights, particularly regarding knock occurrences. This data offers an avenue for post-drive analysis and likely aids McLaren's development team in further refining the tuning strategies. This continuous improvement cycle is a hallmark of many high-performance manufacturers, aiming to extract maximum performance from their engines while mitigating the risks associated with aggressive driving.
The Artura's integration of hybrid technology with a focus on knock prevention reflects a current trend in high-performance vehicle development. It seems the automotive industry is moving towards more complex solutions, striking a balance between power, efficiency, and the need to minimize issues like knock, which can undermine an engine's lifespan and overall performance. The Artura, with its starting price around $254,100, positions itself within the high-end hybrid supercar market, likely appealing to a niche group of enthusiasts and collectors. While the performance capabilities of the Artura are impressive, there is a notable cost associated with accessing this technology, highlighting a potential barrier to wider adoption of such advanced engineering solutions in more mainstream vehicles.
Understanding Engine Pinging A Critical Guide for High-Performance Engine Tuning and Prevention - Porsche 911 GT3 RS Engine Mapping Strategies for Track Performance
The Porsche 911 GT3 RS is a prime example of track-focused engineering, built around a powerful 4.0-liter naturally aspirated six-cylinder engine. This engine, capable of producing 520 horsepower at 8,250 RPM, is a testament to Porsche's pursuit of high-revving performance. The GT3 RS is designed to excel on the track, with a power peak at 8,400 RPM and a rev limiter set even higher. The car's lightweight build and advanced aerodynamic design contribute to exceptional handling and responsiveness. It's not just about speed, though, as the GT3 RS boasts a sophisticated braking system and driver-adjustable chassis controls, enhancing the driver's ability to manage the car's performance on the track. These features, combined with its engine mapping, help the GT3 RS deliver a truly dynamic driving experience, and help prevent issues like engine knock that can hinder performance. The GT3 RS is a showcase of how Porsche has seamlessly merged meticulous engineering with a driver-centric approach to deliver an unforgettable track experience. It's a testament to their commitment to pushing the boundaries of performance.
The Porsche 911 GT3 RS, a testament to Porsche's commitment to track-focused performance, is powered by a naturally aspirated 4.0-liter flat-six engine. This choice, while eschewing the power gains of forced induction, provides a linear power delivery that's highly desirable for drivers who prize a predictable and intuitive connection with the car, especially on the track. This engine, with its screaming high-RPM character, epitomizes the classic Porsche ethos.
The engine management system for the GT3 RS incorporates sophisticated mapping strategies, offering drivers a choice. They can select between a map prioritizing peak power on the track and one that emphasizes torque delivery across the mid-range for those technical sections where cornering prowess is key. This adaptable nature provides a versatile platform for different driving styles and track characteristics. It's an intriguing example of how engine tuning can be tailored to suit diverse demands, not just prioritizing raw power.
One of the critical aspects of ensuring consistent performance in high-stress track environments is maintaining optimal engine operating temperatures. The GT3 RS uses specialized air intakes and an external oil cooler, reflecting the importance of meticulous thermal management. Keeping the engine within its ideal operating range is paramount for sustained performance, and it also plays a role in minimizing the risks associated with engine knock – a phenomenon that can seriously damage an engine when operating at high outputs. It's clear that preventing detrimental knock is a key consideration within the engine design and tuning approach.
While fuel economy takes a back seat in the GT3 RS's priorities, this sacrifice aligns perfectly with the car's purpose: relentless performance. It's designed to deliver the driver the ultimate track experience, and this means prioritizing power and throttle response over fuel consumption. The trade-off is obvious and probably well understood by the target audience – enthusiasts who relish the uninhibited performance and the resulting aural symphony.
Ignition timing is a crucial aspect of maximizing combustion efficiency. The GT3 RS's engine utilizes a complex strategy that dynamically adapts to real-time conditions, such as track layouts, driving input, and other factors that might influence optimal performance. The engine strives for precise ignition timing across various conditions, minimizing the chance of detonation and allowing for consistent power delivery. This precise control, however, requires exceptionally robust sensors and algorithms – a complex process with a high level of reliability being crucial.
Adding a layer of complexity is the inclusion of a dry-sump lubrication system. This intricate system not only plays a role in lowering the car's center of gravity – a benefit for handling and cornering – but it also guarantees consistent oil delivery during high-g track driving. This is essential as severe cornering can sometimes lead to oil starvation, and a dry-sump system mitigates this risk significantly. It's a detail that reflects a holistic approach to design, pushing beyond simply optimizing power delivery.
An advanced telemetry system serves as the backbone for ongoing refinement of the engine mapping. The system logs extensive data, such as throttle input, RPM, and engine load, during track sessions. This information offers invaluable insights for both the driver and engineers, enabling them to continuously refine the engine mapping for enhanced performance and reliability. This constant refinement is a testament to the commitment to excellence, and it underlines the importance of track testing and real-world data to achieving optimal performance.
The GT3 RS's exhaust system, a masterpiece of titanium construction, doesn't merely expel exhaust gases; it also produces a unique and recognizable sound signature. The purposeful engineering of exhaust routing and header design creates a unique aural experience that is arguably part of the car's appeal. Moreover, the distinct sound cues provide useful feedback for the driver, indicating when the engine is delivering optimal power. This is not just about aesthetics but about forging a deeper driver connection.
The GT3 RS provides a surprising degree of driver-adjustable control over engine mapping through the steering wheel. This functionality empowers drivers to adapt on the fly, allowing them to instantaneously optimize performance based on changing track conditions. This capacity showcases the adaptability of the GT3 RS and provides a high level of control rarely seen in other sports cars. It's one more component that enhances the car's racing pedigree.
Finally, high-precision sensors scattered throughout the engine play a critical role in optimizing performance and preventing detrimental knock. They monitor engine behavior, measuring knock levels, cylinder pressure, and other key indicators that feed into the engine control unit. These sensors are vital in allowing the system to dynamically adjust fuel delivery and ignition timing, safeguarding the engine from knock and maximizing its operational efficiency under extreme conditions. This intricate web of feedback and control makes the GT3 RS a remarkable piece of engineering that blends raw performance with sophisticated technical underpinnings.
Understanding Engine Pinging A Critical Guide for High-Performance Engine Tuning and Prevention - Ferrari 296 GTB Twin Turbo V6 Detonation Control Technologies
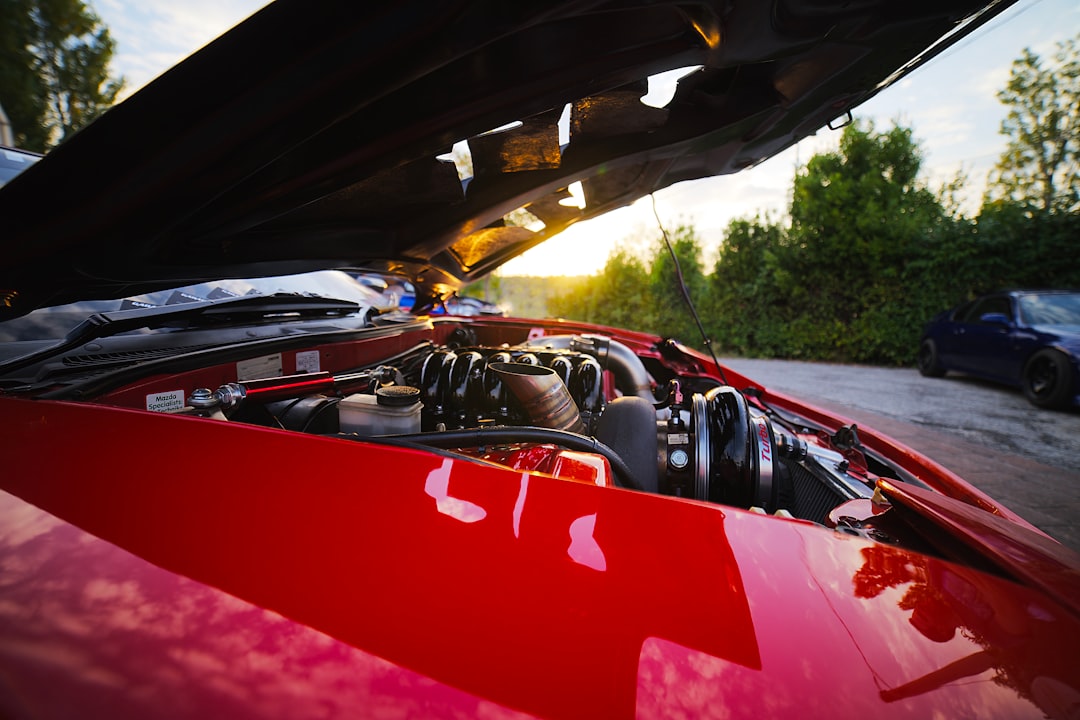
The Ferrari 296 GTB, a standout in the realm of high-performance luxury sports cars, exemplifies modern engine design through its advanced detonation control systems. This car leverages a twin-turbocharged V6, combined with a hybrid powertrain, to achieve a remarkable 819 horsepower. Ferrari's design choices, including a unique 120-degree bank angle for the engine and a “hotvee” turbo placement, are not merely stylistic; they are strategic moves intended to optimize both power output and combustion stability.
One of the key elements contributing to the 296 GTB's high performance is its ability to effectively mitigate engine knock, a potential issue with highly tuned engines. It accomplishes this with a combination of sophisticated fuel injection and engine management techniques. This Ferrari is outfitted with 320 bar fuel injectors, aiming for enhanced fuel/air mixing during combustion. This is especially critical when considering the high pressures and temperatures generated by a twin-turbo engine, factors that can contribute to knock. Ferrari’s engineers have likely also implemented intricate software control to refine ignition timing and adjust fuel delivery, keeping the engine operating within optimal parameters and preventing harmful knock events.
In essence, the 296 GTB represents Ferrari's ability to balance the pursuit of extreme performance with the necessity of protecting the engine's long-term health. This careful approach to both engine tuning and detonation control highlights a shift in modern supercar design, moving beyond simply maximizing power to incorporating intelligent systems for sustained reliability and peak performance. It is also suggestive of a larger trend across the high-performance automotive sector to improve engine responsiveness and efficiency, ensuring a future for thrilling, yet reliably engineered, vehicles.
The Ferrari 296 GTB is a fascinating departure for the marque, ditching its traditional V8 and V12 layouts for a twin-turbocharged 3.0-liter V6. This unique 120-degree bank angle engine design, a departure from the more common 60-degree designs seen in other cars, offers a lower center of gravity. This not only enhances the handling, particularly during spirited driving, but also likely contributes to the car's overall performance characteristics. The compact nature of the V6 combined with the clever hot-vee turbo layout helps in positioning the turbos for optimal efficiency and responsiveness, minimizing the dreaded turbo lag.
One of the key innovations in the 296 GTB lies within its advanced detonation control technologies. It's a system designed to address the potential for engine knock or pinging, a phenomenon where the air/fuel mixture ignites too early in the combustion cycle, resulting in a destructive shock wave. This system relies on a network of sensors strategically placed throughout the engine to constantly monitor for any pre-ignition events. When detected, the engine control unit instantaneously adjusts ignition timing and fuel delivery to counteract the knock. It’s an elegant solution aimed at protecting the engine from potential damage while ensuring optimal performance.
The inclusion of a hybrid system, a first for a Ferrari V6, is another interesting development. While the electric motor primarily enhances performance and responsiveness, its contribution to maintaining ideal operating temperatures is not insignificant. The hybrid system, coupled with the sophisticated detonation control, likely helps prevent the engine from reaching temperature ranges where knock becomes more probable. It's a clever way to mitigate the challenges inherent in high-performance engines operating under varying conditions.
Furthermore, Ferrari’s Variable Boost Management system adds another layer of control. It allows the driver to select drive modes, adjusting the boost levels delivered by the twin turbochargers. This feature offers a level of flexibility, allowing drivers to dial in the engine's power output while minimizing the chances of knock, particularly when pushing the car to its limits.
The careful design of the air intake system and a focus on optimized cooling are crucial elements in the quest to control detonation. By feeding cool air to the engine's critical components, Ferrari aims to reduce thermal stresses, minimizing the risk of premature ignition. Moreover, the use of advanced 320-bar fuel injectors ensures precise air-fuel mixture control throughout the engine's operational range, which is fundamental in preventing issues with knocking.
Finally, the 296 GTB's lightweight construction, enabled by the extensive use of carbon fiber, offers a subtle but impactful benefit. Reducing the overall vehicle mass decreases the strain on the engine. The engine doesn’t have to work as hard to achieve performance, potentially reducing the risk of knock in high-demand scenarios. Coupled with sophisticated engine mapping strategies that dynamically adapt to driving conditions, the Ferrari engineers have created a remarkably potent and potentially refined engine. The 296 GTB, in this aspect, appears to be a testament to Ferrari's continual engineering refinement, using data collected through a dedicated telemetry system to optimize performance and durability.
While it's difficult to definitively comment without in-depth testing and extensive analysis, the Ferrari 296 GTB appears to offer a fascinating glimpse into the future of Ferrari engine design. It's an ambitious project that merges innovative hybrid technology with a powerful and compact V6 engine. Whether this signifies a true departure from the traditional Ferrari sound and feel is debatable, but its sophisticated approach to detonation control and engine management presents a compelling case for its future potential. It remains to be seen how the 296 GTB will stand the test of time and track usage, but from a technical perspective, it represents an intriguing development in high-performance automotive engineering.
Understanding Engine Pinging A Critical Guide for High-Performance Engine Tuning and Prevention - Mercedes AMG One F1 Derived Anti Knock Systems for Street Use
The Mercedes-AMG One is a remarkable feat of engineering, a hypercar that bridges the gap between Formula 1 racing and road-going vehicles. Its heart is a hybrid powertrain combining a potent gasoline engine with four electric motors, generating a combined output of 1049 horsepower. This allows for blistering performance, catapulting the car from zero to 60 mph in under 3 seconds and achieving a top speed of over 219 mph. But the AMG One is more than just raw power. It features an innovative suite of anti-knock systems derived directly from Formula 1 racing. These systems are designed to combat engine knocking, a phenomenon that can damage high-performance engines if left unchecked. The ability to constantly monitor and control crucial parameters like fuel delivery and ignition timing allows the engine to operate optimally, minimizing the risk of damaging knock under any condition.
It's a bold experiment to bring Formula 1 technology to a road car. While the allure of such extreme performance is undeniable, it poses interesting questions about the long-term implications. The AMG One clearly prioritizes performance, and in doing so, pushes the boundaries of what's possible with high-performance engines. However, this also necessitates innovative solutions to address the challenges that come with such extreme power, especially regarding the risk of engine knock which can impact reliability and potentially shorten the engine's lifespan. It's a testament to the evolving nature of supercar design and technology, where the marriage of luxury and performance demands increasingly sophisticated solutions to both enhance and protect the driving experience. The AMG One, a pinnacle of engineering prowess, represents a bold foray into the future of hypercar design, forcing us to consider the delicate balance between unrestrained power and engine longevity in a world of constantly advancing technology.
The Mercedes AMG One, a fascinating marriage of Formula 1 technology and road-legal practicality, showcases a complex approach to combating engine knock—a problem that can plague high-performance engines. The car's powertrain, derived directly from the world of F1, is a testament to transferring competitive engineering into a consumer vehicle. It relies on a sophisticated network of sensors to constantly monitor the engine's health, looking for the subtle signs of knock, which is a form of premature combustion. This data is then used by the engine control unit to fine-tune ignition timing and fuel delivery, adjusting on the fly to optimize performance and prevent potential damage.
The AMG One's clever cylinder deactivation system is another way they tackle knock. By allowing the engine to operate with fewer cylinders when under lower load, they effectively reduce the heat buildup and mitigate the chances of knock-inducing situations. The engine itself, a 1.6-liter V6 hybrid, utilizes a “hot V” design, which positions the twin turbochargers between the banks of cylinders. This design choice, while potentially tricky, is thought to improve turbocharger response and minimize turbo lag—crucial elements in managing knock, especially when you're dealing with instantaneous power demands.
Further contributing to managing knock, the AMG One utilizes variable geometry turbochargers. These ingenious devices adjust their vanes based on the engine's current demands, a smart way to fine-tune boost pressure and keep the engine within an optimal operating window. The high-pressure fuel injection system, boasting pressures beyond 350 bar, plays a vital role in precisely metering fuel into the cylinders—a key factor in achieving stable combustion and preventing knock under heavy loads.
Knock sensors, integrated throughout the engine, allow the system to differentiate actual knock from normal engine variations. This precision in identification is essential for reacting swiftly and effectively. It's apparent that thermal management is a high priority in this high-performance engine. Water-to-air intercoolers and active aerodynamic elements help control intake air temperature, minimizing the risk of detonation.
Interestingly, the AMG One utilizes machine learning to refine its strategy over time. This means the engine can adapt to driving styles and various conditions, learning to optimize combustion and reduce the likelihood of problematic knock events. This combination of intricate sensors, adaptive control systems, and machine learning makes the AMG One a very sophisticated example of how engineers are using complex techniques to manage engine knock. The AMG One doesn't just highlight impressive performance—it demonstrates the intricacies of high-performance engine design and the challenge of ensuring a delicate balance between extreme output and durability. It's a peek into the future of engine tuning and the need for increasingly sophisticated solutions to meet the demands of powerful, yet reliable vehicles.
Understanding Engine Pinging A Critical Guide for High-Performance Engine Tuning and Prevention - Nissan GT R R36 Updated ECU Programming for Knock Prevention
The Nissan GT-R R36 has received updated ECU software, specifically focusing on improving knock prevention and boosting engine performance. This update, likely a new version of EcuTek's RaceRom, boasts faster flash times and more advanced logging features. These improvements are essential for tuners as they provide real-time insight into engine behavior, enabling them to precisely adjust the engine's calibration. The ability to utilize different fuels with the integration of FlexFuel support is another notable improvement. It allows tuners to adjust ignition timing and air/fuel ratios to manage engine conditions, reducing the potential for knock across a wider range of fuel types. To ensure comprehensive vehicle diagnostics, Nissan also provides the GTR ECU Connect tool, which allows tuners to simultaneously monitor both the engine and transmission ECU data. This ability to capture data from both systems offers a far more complete picture of vehicle operation and can significantly contribute to refined tuning. The overall update showcases an ongoing push within Nissan's performance engineering efforts, with a clear intent to both improve performance and minimize engine damage through a dedicated focus on knock prevention. This highlights the level of sophistication required for achieving significant power gains in these high-performance vehicles. While this is a step in the right direction for the GT-R, only time will tell if these advancements truly enhance reliability in the long run or if they merely scratch the surface of managing the complexities of preventing knock in a high-power tuned engine.
The Nissan GT-R R36 showcases a refined approach to engine control, particularly in the realm of knock prevention. The updated ECU programming utilizes sophisticated algorithms to analyze real-time data from the engine, allowing it to make dynamic adjustments to fuel maps and ignition timing. This strategy aims to minimize the risk of detonation, especially under the high-performance demands the GT-R typically encounters. A network of sensors, including those that monitor vibrations and other signs of abnormal combustion, plays a crucial role in detecting knock early. This advanced knock detection allows the ECU to respond quickly by adjusting fuel delivery and ignition timing to maintain optimal combustion conditions and safeguard engine health.
Engine temperature management also plays a vital part in preventing knock. The R36 features improvements in its intercooling and cooling pathways, crucial for keeping the engine within an optimal temperature range during high-intensity driving. The goal is to reduce the thermal stresses that could potentially lead to detonation. Moreover, the ECU's programming allows for dynamic mapping adjustments based on real-time driving conditions. This adaptable nature ensures the engine operates efficiently across the rev range, optimizing power while simultaneously mitigating the chances of knock.
The variable geometry turbochargers employed in the R36 also contribute to this strategy. By adjusting their vane angles based on engine load and demand, they allow for more precise control of boost pressure and airflow, directly affecting combustion stability. Furthermore, the R36’s engine benefits from lightweight materials in its construction, leading to lower overall mass. This reduction in weight places less stress on the engine, potentially reducing heat buildup and knock risk. The inclusion of a high-pressure direct fuel injection system (exceeding 300 bar) enhances fuel delivery and atomization, leading to more precise combustion control and reduced knock susceptibility.
The R36’s revised air intake design is also noteworthy. It emphasizes a smoother airflow path with minimized turbulence, improving the delivery of cool air to the engine. This attention to detail promotes a consistent and cooler air supply, contributing to the prevention of knock. Interestingly, some tuning methodologies now incorporate predictive analytics to analyze engine performance across various scenarios. This forward-looking approach allows the ECU to anticipate potential knock and proactively adjust settings to prevent it before it occurs. Finally, the GT-R R36's ECU operates as a central control hub for numerous vehicle systems, including traction and stability control. This complex interconnectivity enables a more holistic approach to performance tuning, where the detection and mitigation of knock can trigger other systems to help maintain overall vehicle stability and engine integrity. It is clear that Nissan has invested considerable effort in fine-tuning the R36's engine control, using a multi-pronged approach that encompasses engine design, thermal management, and advanced ECU programming to improve performance while reducing the detrimental effects of knock.
More Posts from tunedbyai.io: