Motorcycle Gloves Where Performance Meets Style and Protection
Motorcycle Gloves Where Performance Meets Style and Protection - Material Selection The Handwear Parallel to Automotive Composites
When looking at the composition of motorcycle gloves today, you can't avoid seeing the direct parallels with material selection in high-performance automotive design. Much like engineers choose sophisticated composite structures for everything from supercar chassis to suspension components, the focus for hand protection is increasingly on engineered materials that go beyond traditional options. While classic materials like high-quality leather still provide excellent abrasion resistance and feel, especially for certain riding disciplines, advanced textile weaves and composite inserts are becoming standard. Drawing lessons from racing applications and vehicle safety structures, materials like aramid fibers and carbon elements are integrated into gloves specifically for their strength, impact absorption, and resistance to tearing. It's a material science challenge similar to that in automotive development: finding substances that can withstand significant stress, improve durability, and potentially save weight, while for gloves, also needing to allow for dexterity, breathability, and comfort across varied conditions. This shared drive towards leveraging cutting-edge materials to elevate both safety and performance defines the frontier for both rider gear and advanced vehicle components.
Stepping back from the rider's perspective for a moment, there's a compelling technical story in the very materials that make up a performance motorcycle glove. It's a field where, perhaps unexpectedly, the challenges and solutions echo those faced in the engineering of advanced automotive structures and components. Considering the drive for lightweight strength and integrated safety in everything from supercar monocoques to high-performance brake systems, it's fascinating to see similar material science principles applied to something as seemingly simple as handwear. Here are a few points of connection that highlight this shared technical pursuit:
The internal architecture of protective inserts, particularly those guarding knuckles, often relies on composite laminates – frequently involving carbon fibers or similar high-modulus materials. The way these materials are layered and oriented isn't just about creating a hard shell; it's specifically engineered to manage and disperse impact energy across a surface and away from a single point, bearing a conceptual similarity to how complex load paths and energy absorption zones are designed into the composite or advanced alloy structures of a vehicle chassis to protect occupants during a collision. It's material working as a system, not just a bulk block.
Consider the sheer abrasion resistance required for a glove palm during a slide. The materials deployed here, often specialized synthetic leathers or fabrics reinforced with high-strength fibers like aramids, share a material ancestry with components facing extreme friction and heat in performance cars. Think about the aramid fibers woven into high-performance tire sidewalls for structural integrity under immense cornering loads, or the composite friction materials used in racing brake pads designed to withstand searing temperatures and aggressive wear cycles. The chemical backbone and physical properties sought – toughness, heat resistance, tensile strength – are strikingly similar, just applied to different scales and failure modes.
The integration of specialized protective elements, sometimes using materials that react dynamically to impact, points to a material behavior also being explored in cutting-edge automotive concepts. Some glove armor incorporates non-Newtonian polymers – fluids or gels that solidify dramatically under sudden shear force. While not a direct engineering parallel to, say, active magnetic ride control, the underlying principle of a material changing its state or viscosity in response to external input is a shared area of research, particularly in experimental adaptive damping elements or even dynamic structural mounts being considered for future vehicles seeking enhanced refinement or impact mitigation. The complexity of scaling this from a small armor insert to a vehicle system is, however, immense.
The selection of certain traditional materials, like high-quality kangaroo leather, for premium gloves is driven by a quest for an optimal balance of strength, low weight, and tactile feel. This pursuit of seemingly contradictory performance characteristics mirrors the rationale behind using specific lightweight yet strong composites or bespoke alloys in critical areas of a performance car body – aiming for rigidity and safety without incurring a significant weight penalty, which would compromise acceleration and handling. The material choice isn't just for aesthetics; it's a functional engineering decision based on a unique material property profile, much like opting for a specific carbon fiber weave for a suspension component versus a body panel.
Finally, the engineering of synthetic palm and finger materials for high-performance gloves involves careful consideration of polymer chemistry and surface texture to optimize grip under varying conditions (wet, dry, vibrating). This focus on the interface between the material and the user/control surface is a direct parallel to the meticulous design of steering wheel wraps, gear knob materials, or even pedal surfaces in driver-focused cars. The micro-geometry and tactile qualities are engineered to provide maximum control and feedback, sometimes using proprietary synthetic blends and surface treatments developed specifically for haptic performance, reflecting a shared understanding that the 'feel' is a critical aspect of control, whether gripping handlebars or a steering wheel.
Motorcycle Gloves Where Performance Meets Style and Protection - Ergonomics and Fit Designing for Control Like a Driver's Cockpit
For motorcycle gloves, the attention paid to ergonomics and achieving a precise fit serves a function much like the meticulous engineering of a high-performance driver's cockpit: it's all about maximizing control. Just as vehicle designers employ analytical approaches and data-driven models to optimize the interface between the driver and the machine – considering factors from physical dimensions to posture and the layout of controls – the design of effective hand protection increasingly focuses on this critical connection. Achieving a glove fit that feels like a natural extension of the hand isn't merely for comfort; it's fundamental to translating rider intent into precise inputs at the handlebars and levers. This close alignment is essential for reducing fatigue during extended periods, ensuring tactile feedback is clear, and enabling rapid, accurate adjustments in dynamic situations. It represents a design challenge where the human element is paramount, mirroring the complex process of creating a driver environment that supports peak performance and safety by minimizing strain and optimizing the interaction with vital systems.
Examining high-performance motorcycle gloves from a design and engineering perspective reveals how similar principles are applied to optimize the human-machine interface, much like the meticulous work done in developing a driver's cockpit in performance automobiles.
1. The characteristic pre-curved structure found in many rider gloves isn't merely an aesthetic choice or minor comfort feature. It represents a deliberate ergonomic effort to pre-dispose the hand into a natural, relaxed posture closely mirroring the grip required on handlebars. This mirrors the careful sculpting of a high-performance steering wheel rim or the angle and placement of pedals, engineered to align human anatomy for reduced strain during prolonged or aggressive use and to facilitate instantaneous control inputs. Poor execution here can lead to fatigue and hinder dexterity.
2. The strategic placement and construction of seams within a quality glove are critical engineering details often overlooked. The goal is to minimize potential pressure points and friction against the hand's complex surface geometry, much like how designers of premium automotive interiors obsess over the subtle transitions, stitching patterns, and padding profiles in seats and steering wheels to eliminate irritants that could distract a driver, especially at speed or over distance. A misplaced or poorly finished seam can become a significant liability, generating discomfort that compromises concentration and control.
3. The precision of the glove's fit in the palm area is fundamental to the tactile connection between rider and machine. This area functions as a crucial conduit for transmitting vital haptic feedback from the handlebars – vibrations that might signal changing road surface textures, tire slip, or engine behavior. This is conceptually analogous to how performance car engineers meticulously tune steering columns and pedal boxes to provide specific feedback – not just feel for the sake of it, but information critical for gauging vehicle dynamics and making informed control adjustments. Too much looseness or bunching in the palm interrupts this critical data stream.
4. Incorporation of flexible gussets or strategically placed stretch panels serves the function of allowing necessary articulation and freedom of movement for the hand and fingers to operate controls naturally (clutch, brake levers, switches) while still maintaining the protective integrity and a secure fit of the overall structure. This principle is seen in the engineered flex zones in racing footwear or specific cutouts and materials used in competitive seating that allow for rapid, unhindered footwork on pedals or full steering lock capability without restriction. If these flex zones are improperly designed or located, they can compromise either protection or functionality, potentially creating pinch points or limiting necessary range of motion.
5. Ultimately, the design of the interface between the gloved hand and the motorcycle controls revolves around facilitating precise micro-adjustments and feel. This focus on fine-grained control input mirrors the calibration process for accelerator pedal sensitivity, brake pedal feel, or even variable-ratio steering mapping in driver-focused vehicles, where subtle changes in pressure or movement translate into controlled and predictable responses. The glove, when properly designed for fit and feedback, becomes an extension of the controls themselves, enabling the rider to make the minute adjustments required for high-level performance, much like a driver relying on calibrated inputs at critical moments. Inconsistencies in this interface undermine a rider's ability to modulate inputs effectively.
Motorcycle Gloves Where Performance Meets Style and Protection - Impact Zones and Protection A Study in Engineering Safety Layering
Delving into the core safety function means examining the designated 'impact zones' on a motorcycle glove. Engineering analysis highlights critical areas like the knuckles, palm, and fingers as particularly vulnerable in a crash scenario. The underlying principle involves a layered safety design aimed at managing impact energy – effectively absorbing and distributing forces rather than just creating a rigid shield. This design effort is reflected in protective standards, such as EN 13594:2015, which grade gloves based on tested force transmission performance through their protectors. Achieving higher protection levels, like Level 2 which significantly reduces transmitted force compared to Level 1, requires integrating robust materials and structures, often presenting engineers with the challenge of balancing this heightened safety with practical concerns like maintaining sufficient dexterity. This targeted engineering focus on vulnerability points mirrors the detailed structural design in performance vehicles, where engineers similarly prioritize managing impact forces and safeguarding occupants within designed crumple zones and reinforced areas – a deliberate application of technical knowledge to mitigate predictable risks.
Consider the armor covering vulnerable areas like knuckles. It's rarely just a solid block. Beneath the hard surface, engineers often employ intricate internal geometries – think structures with voids or complex shapes, conceptually akin to the engineered substructures within vehicle pillars or impact beams designed to deform and absorb energy progressively during a collision. It's a deliberate architectural approach to manage force rather than simply resisting it, though predicting real-world impact dynamics on such complex hand anatomy remains difficult.
Then there are elements such as strategically placed palm sliders. Their purpose goes beyond mere material abrasion resistance. By presenting a smooth, low-friction surface upon contact with asphalt, they aim to prevent the hand from "catching" and twisting. This redirects energy, helping the hand and wrist slide instead of rotating violently, somewhat mirroring how specific aerodynamic or underbody treatments on high-performance cars can influence airflow or manage ground contact in dynamic situations to maintain stability. It's about controlling uncontrolled movement during an unexpected event.
Protection isn't typically achieved with a single monolithic material; it's a system. Many effective designs layer disparate materials – perhaps a tough, tear-resistant textile outer, followed by a more rigid impact plate, and finally a compliant, energy-attenuating foam layer closer to the skin. This multi-layering is engineered so each component handles a specific phase or type of load during an impact event, distributing and absorbing energy in stages, much like the designed sequence of deformation and energy absorption within a modern vehicle's safety cell and its surrounding crumple zones during a crash. Getting the interaction between these layers right across varied impact angles and energies is the engineering challenge.
Observe details like 'finger bridges,' often a connection between the pinky and ring finger. While seemingly small, this feature is intended as a structural link. In an impact or slide scenario, it helps to distribute forces away from the highly vulnerable outer fingers (particularly the pinky) towards the stronger structure of the hand and adjacent digits. It's a simple but effective load-sharing mechanism, conceptually aligning with how internal structural members within a vehicle chassis are tied together to channel and disperse collision forces away from critical occupant spaces. Its effectiveness, however, relies on the overall integrity and fit of the rest of the glove structure.
Furthermore, some advanced protective inserts incorporate materials whose protective properties are dependent on the speed of the impact. These are materials that remain relatively pliable and flexible during normal use (aiding comfort and dexterity) but stiffen dramatically and momentarily become far more resistant and energy-absorbent when subjected to a sudden, high-velocity force. This characteristic, known as strain rate sensitivity, is a property explored and utilized in various energy-attenuation components within vehicles, often in areas designed to manage specific, rapid impact scenarios. It's protection that adapts its state based on the severity of the event, though consistency in performance across extreme temperatures and multiple impacts is an area requiring careful validation.
Motorcycle Gloves Where Performance Meets Style and Protection - The Aesthetics of Function Handwear Styling and Vehicle Design Lines
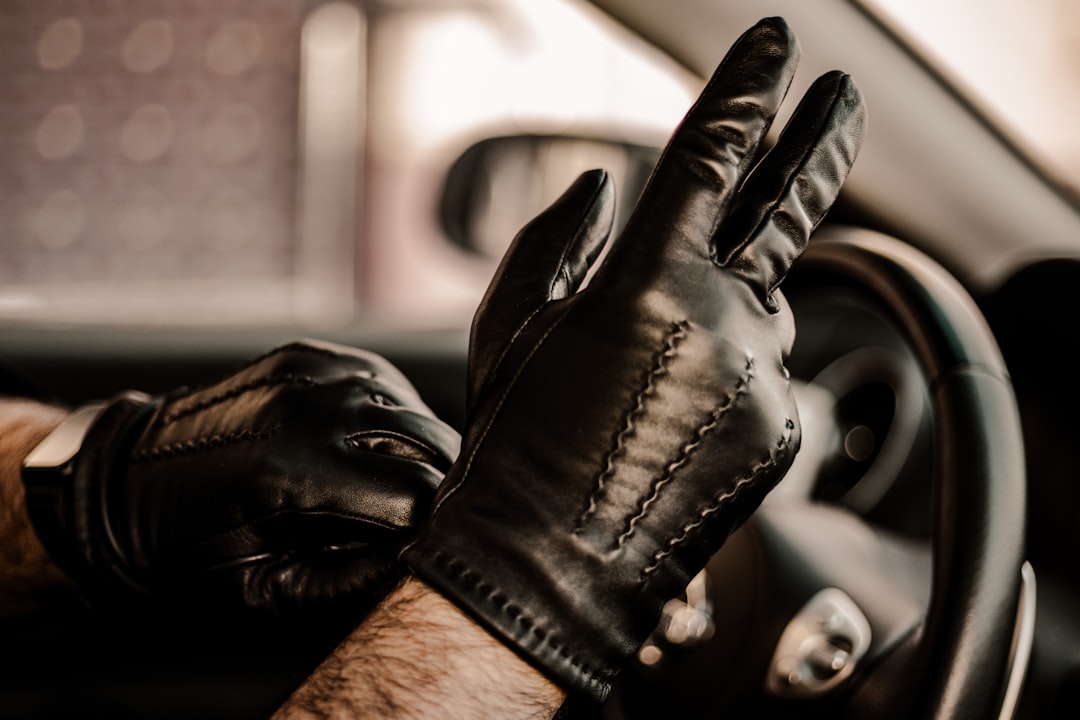
The aesthetics of function in handwear styling and vehicle design lines highlight the seamless integration of form and performance across both realms. Just as the sleek contours of contemporary vehicles, such as the VW ID.7 or the Jaguar E-Pace, marry aerodynamic efficiency with visual appeal, motorcycle gloves are increasingly designed not only for protection but also to embody a distinctive style. The interplay between materials and design choices reflects a shared ethos; both motorcycle gloves and luxury automobiles prioritize user experience through ergonomics and optimal functionality. This convergence of aesthetics and engineering is evident in how both industries leverage advanced materials and innovative designs to elevate their respective products, pushing the boundaries of what is possible while appealing to the senses. Ultimately, the narrative of style and performance in both gloves and vehicles underscores a broader cultural trend, where safety and elegance coalesce to create a compelling statement on the road and beyond.
Drawing from an engineering vantage point, examining high-performance motorcycle gloves offers a fascinating dialogue between form dictated by necessity and aesthetic expression. It highlights how the pressures of performance and safety inevitably shape design, often in ways that parallel visual trends and functional cues seen in automotive design.
1. Consider the significant, often angular shapes of integrated knuckle and finger protection elements. While their primary function is to absorb and deflect impact energy, their physical form is rarely a simple, smooth lump. Instead, designers often sculpt these hard points with contours and edges. This shaping, perhaps initially driven by the need to manage bulk, potentially offer some minimal snag resistance, or simply house the internal structure, results in aesthetic forms that visually echo the deliberately engineered surfaces found on vehicles designed for aerodynamic management or structural emphasis. Think of the complex profiles of a modern supercar's diffuser or the sharp creases on a fresh performance SUV's bodywork – functional components, yes, but styled with an aggressive, performance-oriented visual language that influences the overall aesthetic.
2. Look closely at the surface detailing. The strategic implementation of areas with different textures, perforation patterns, or material overlaps on a glove isn't purely random. These elements often serve specific functional needs – perhaps ventilation through micro-perforations in a leather palm, or flexibility provided by a stretch textile panel over knuckles, or defining an area of enhanced grip. Yet, the *visual patterns* and the way these functional areas are delineated and transitioned across the glove's surface creates a layered aesthetic. This mirrors how designers use contrasting textures, vents, or trim elements on a vehicle – say, the intricate mesh pattern of a grille that also functions as an intake, or the sculpted lines surrounding a functional fender vent on a tuned car – to break up surfaces, highlight areas of function, and contribute to the perceived dynamism of the design.
3. The lines created by seams and the careful cutting and joining of different panels are fundamental structural elements in a glove, necessary for shaping it to the complex geometry of the hand and ensuring durability. However, these required junctions become inherent visual lines. Much like the character lines, shoulder lines, or even the precise (or sometimes frustratingly imprecise) panel gaps on a vehicle's bodywork, these seams and panel boundaries define the volumes, guide the eye, and contribute significantly to the perceived quality and structure of the object. A well-executed seam or a taut panel on a glove communicates precision and form, analogous to how crisp, consistent lines enhance the visual integrity of a finely crafted car body.
4. Think about the closure systems – cuffs, wrist straps, finger retention mechanisms. These are purely functional components, necessary for securing the glove. Yet, their design and execution vary enormously, from simple Velcro tabs to complex ratchet systems or elaborate magnetic fasteners. Beyond merely serving utility, these elements are often integrated design features, using distinctive shapes, materials, and branding. They contribute significantly to the overall aesthetic and perceived sophistication of the glove, functioning much like the design of unique door handles, fuel filler caps, or integrated aero fasteners on a vehicle. These small, functional interfaces become part of the product's signature, influencing how it's interacted with and perceived visually.
5. The deliberate use of contrasting materials and finishes is a prominent aesthetic technique. Pairing matte leather with glossy carbon fiber, or a textured synthetic grip area with a smooth, protective overlay isn't just about using the right material for the right job. This creates visual boundaries and highlights distinct functional zones. It's a technique widely employed in vehicle design, both internally and externally. Consider the deliberate contrast between soft-touch dashboard materials, brushed metal trim, and perhaps piano black accents in a luxury car cockpit, or the exterior contrast between painted body panels, raw carbon fiber aerodynamic components, and polished exhaust tips on a high-performance model. This material blocking defines areas and enhances the visual appeal by leveraging the inherent properties and look of different substances.
Motorcycle Gloves Where Performance Meets Style and Protection - Tuning Your Rider Interface Handwear Choices and Performance Optimization
Optimizing your interaction points with a vehicle is fundamental, and for a motorcycle rider, this undeniably starts with the hands. Choosing the right handwear isn't merely about layered protection or a specific aesthetic statement. Instead, tuning your interface through glove selection becomes akin to calibrating the primary controls in a high-performance automobile – thinking about the nuanced feel of the steering wheel, the progressive resistance of the brake pedal, or the tactile response of a gear shift lever in a vehicle designed for precision. Your gloves are the critical layer mediating communication between your hands and the motorcycle's grips and levers. Getting this connection right, focusing on how the material feels under tension and through vibration, how the fit allows for unfettered dexterity, and crucially, how it transmits vital feedback from the machine, directly influences control precision. It's a process of refinement where the handwear shouldn't impede but should actively facilitate the transfer of rider intent and vehicle dynamics, much like how finely tuned automotive controls enhance a driver's connection and ability to push limits. However, finding that truly perfect union between hand and control, balancing security, feel, and durability across diverse conditions and manufacturing variances, remains a perpetual challenge given the sheer variables involved in both human anatomy and material performance under stress.
Stepping away from the specific realm of motorcycle handwear for a moment, it's intriguing to consider how the engineering challenges in optimizing a rider's interface with their machine echo principles seen in developing sophisticated automotive systems. Take, for instance, the intricate demands placed upon controlling temperature within performance vehicles – cooling high-output engines, managing battery thermal states in EVs, or maintaining a precise climate in a luxury cabin. This mirrors the complexity within high-end handwear, where designers must engineer integrated thermal regulation layers and airflow channels to manage internal moisture and external temperature extremes, ensuring a rider's hands remain at peak operating condition, much like ensuring critical vehicle components stay within optimal thermal envelopes.
Then there's the fundamental challenge of grip. Just as tire manufacturers painstakingly fine-tune the polymer blends and tread patterns of high-performance tires to achieve a specific, often critical, coefficient of friction across varied road surfaces and temperatures, the material science behind high-performance glove palms involves a similar meticulous approach. Engineers select and process specific synthetic blends or leathers and apply precise surface treatments to achieve an optimal, predictable interface with handlebars and controls. This is about more than just preventing slipping; it's about delivering a consistent haptic feel crucial for modulated inputs, a parallel seen in the engineered feel of steering wheels or pedal textures designed to convey critical feedback to the driver.
Consider the relentless pursuit of mass reduction in competitive motorsport or high-performance road car development. Every gram is scrutinized, every component analyzed for potential weight savings without compromising structural integrity or function. This mirrors a similar, albeit smaller-scale, engineering obsession in top-tier rider gear development. For competitive riders, minimizing handwear weight, even seemingly marginal amounts, is viewed as contributing to reduced long-distance fatigue and enhancing the micro-dexterity needed for precise control inputs – a philosophical alignment with the exhaustive gram-saving measures deployed in track-focused vehicles where carbon fiber, titanium, and complex alloys are employed not just for strength, but specifically for their superior strength-to-weight ratios, though the relative cost and complexity of glove mass reduction can be quite high for the gain.
Looking further ahead, the exploration of integrating micro-sensors directly into dynamic structures for real-time data acquisition is gaining traction. While currently more speculative for rider handwear, the concept of sensors providing feedback on things like hand strain, localized temperature variations, or even impact force vectors bears a conceptual kinship to the performance telemetry and sophisticated driver/occupant monitoring systems increasingly integrated into advanced race cars and some cutting-edge production models. The technical hurdles of creating robust, miniature sensors that can withstand flexing, vibration, and environmental exposure while reliably transmitting data from a user interface remain significant, a challenge also faced in developing sensor arrays for complex automotive environments.
Finally, the engineering required to build protective handwear that allows for the complex, multi-axis articulation of fingers and the hand while still providing robust impact and abrasion protection is a demanding task. It necessitates intricate composite layups, sophisticated joint designs, and material selections capable of repeated flex cycles without failure. This challenge isn't dissimilar to the engineering complexity involved in designing modern multi-link suspension systems or the articulated joints in advanced robotic manipulators used throughout automotive manufacturing processes – systems that require predictable movement across multiple planes while handling significant loads or resisting dynamic forces. Replicating the natural fluidity and adaptability of biological joints within a protective engineering framework is an inherently complex problem with numerous trade-offs.
More Posts from tunedbyai.io: