Steering Angle Sensor Expenses Key to High Performance Car Control
Steering Angle Sensor Expenses Key to High Performance Car Control - Exploring the Digital Spine of High Performance
"Exploring the Digital Spine of High Performance" signals a significant evolution in how automotive engineering approaches the core of a vehicle's capabilities. Beyond merely adding screens and connectivity, the latest advancements see a profound integration of digital intelligence, essentially forming the car's nervous system. This isn't just about faster computations; it's about systems that learn, adapt, and predict, aiming to optimize every facet of the driving experience. However, this deep reliance on code and algorithms raises intriguing questions about the authenticity of human interaction with the machine, and whether such complexity inevitably inflates costs, making cutting-edge performance an even more exclusive domain. The ongoing push is to weave these digital threads into the very fabric of car design, creating vehicles that are not just mechanically superb but intelligently responsive, redefining what it means to truly connect with a high-performance machine in an increasingly digital world.
Consider the sheer deluge of information coursing through a high-performance machine; we're talking about a vehicle's core electronic architecture, its 'digital spine,' digesting upwards of 10 gigabytes of live sensor feeds every second. This isn't just data logging; it's immediate processing, requiring specialized multi-core processing units capable of calculations in the gigaflops range. The engineering challenge here lies not merely in processing capacity, but in ensuring that all these calculations happen with imperceptible latency, a vital aspect for instantaneous feedback in dynamic situations.
The archaic limits of the traditional CAN bus have largely been transcended in today's leading-edge supercars. We're now observing a widespread adoption of automotive Ethernet for the core network backbone, pushing data at speeds reaching 10 gigabits per second. This paradigm shift is indispensable for managing the ever-increasing bandwidth demands from the elaborate sensor arrays and tightly integrated control systems, moving beyond simple messaging to true high-throughput data streams for interconnected modules.
Intriguingly, the more sophisticated digital architectures in elite performance vehicles are now employing advanced artificial intelligence to forge a dynamic, real-time 'digital twin' of the car itself. This isn't just a static model; it's a continuously evolving representation that allows for highly granular predictive wear analysis and, more remarkably, adaptive recalibration of critical parameters like suspension damping or engine power delivery. While this promises unprecedented optimization, the robustness and potential for unforeseen interactions within such a rapidly adapting system remain a subject of rigorous scrutiny for engineers.
Beyond the common suite of vehicle dynamics sensors, the drive for ultimate precision in high-performance machines has led to the deployment of remarkably fast high-frequency accelerometers and gyroscopes. These units boast response times well under 500 microseconds, providing an ultra-fine-grain tapestry of data. Such exquisite detail is fundamental for the instantaneous adjustments demanded by active aerodynamic elements and the critically precise real-time management of torque vectoring systems, pushing the boundaries of what's possible in vehicle control.
For truly critical control pathways, especially in nascent steer-by-wire and brake-by-wire systems, the digital spine often integrates triple modular redundancy (TMR) into its core modules. This engineering choice is not trivial; it involves three independent computational paths, with a voting mechanism to ensure fail-operational capability. The intention is clear: maintain system functionality even in the extremely improbable scenario of a primary component malfunction, a necessary safeguard as these highly integrated systems replace direct mechanical links.
Steering Angle Sensor Expenses Key to High Performance Car Control - The Hidden Price Tag of Seamless AI-Driven Steering
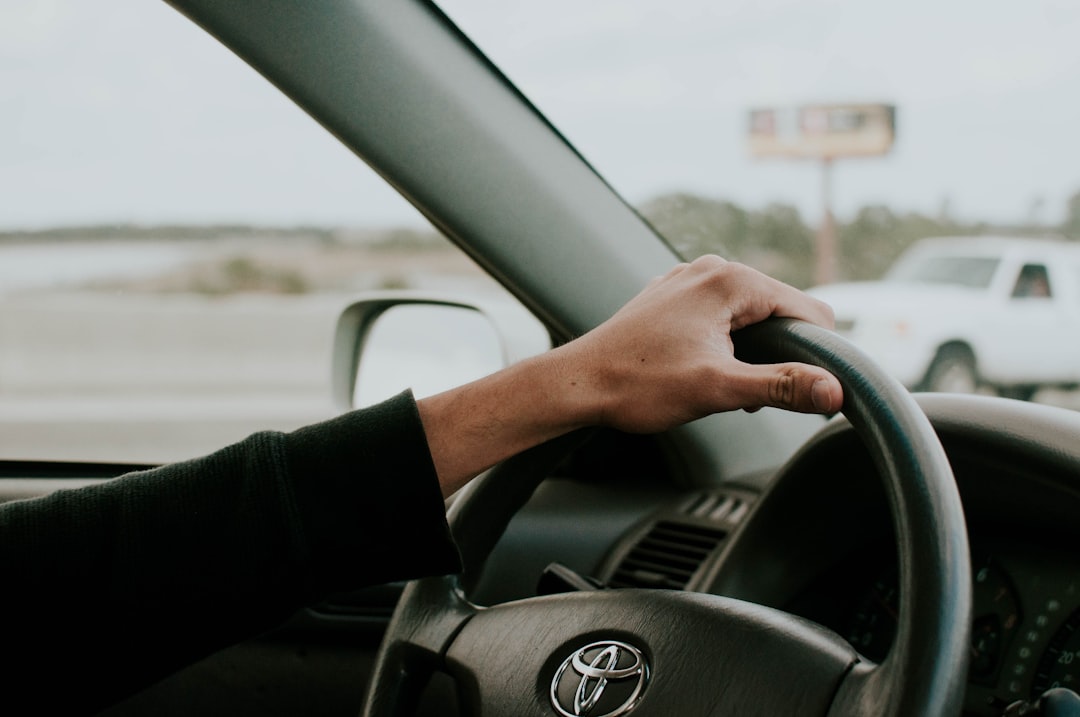
While the promise of AI-driven steering has reshaped expectations for vehicle control, it carries an often-unseen economic weight extending far beyond basic research and development. The profound reliance on high-precision steering angle sensors, for instance, isn't just about their individual cost; it’s about their deep integration into highly adaptive algorithmic control loops. This necessitates an unprecedented level of individual sensor calibration, not merely at assembly, but across varying operational conditions, requiring bespoke testing rigs and dedicated engineering efforts.
For car manufacturers, especially those in the luxury and supercar segments, achieving the "seamless" illusion demands intricate and often proprietary software stacks governing the steering feel and responsiveness. These aren't off-the-shelf solutions; they are tailored, meticulously refined algorithms that drive up the sustained investment in expert software engineers and extensive real-world validation processes. Ensuring the integrity and predictability of an AI that influences fundamental vehicle direction, particularly under extreme performance demands, introduces a continuous stream of validation cycles that significantly impact production timelines and associated expenses.
Furthermore, the longevity of these highly specialized AI systems remains a nuanced concern. As technology progresses rapidly, the potential for faster obsolescence of specialized hardware and proprietary software in AI steering creates a long-term economic question mark, hinting at future upgrade paths that might not be as straightforward or affordable as with conventional systems. The pursuit of this ultimate, digitally sculpted driving experience, while undeniably captivating, compels us to consider the hidden expenditures wrapped within the pursuit of unparalleled machine intelligence.
Implementing steering systems driven by artificial intelligence frequently demands tailor-made silicon, known as ASICs, designed specifically for running complex neural networks. Unlike more general-purpose computing units, these specialized processors are engineered from the ground up for instantaneous computations, ensuring the incredibly low lag times essential for responsive steering. This bespoke hardware, while offering unparalleled performance for the task, inevitably inflates the per-vehicle production cost beyond what standard processing elements would entail.
Validating the learning algorithms embedded within steer-by-wire systems to stringent safety standards, such as ASIL D, is a monumentally complex undertaking. This isn't just about verifying lines of code; it involves exhaustive computational simulations and probabilistic assessments, scrutinizing how the AI behaves across an unimaginable spectrum of scenarios. This rigorous validation process significantly prolongs development cycles and can easily balloon software engineering expenditures by hundreds of millions, all to ensure the AI's steering commands are consistently predictable and safe under any conceivable condition.
Developing the perceptive capabilities of AI-driven steering systems, which must accurately interpret varied road surfaces, weather, and crucially, human driver cues, necessitates a staggering volume of data. We're talking petabytes of meticulously gathered and annotated real-world and synthetic driving scenarios. The ongoing process of acquiring, categorizing, and refining these massive datasets represents a continuous operational burden, easily costing many millions and demanding dedicated teams to maintain their quality and relevance.
Another often-underestimated financial aspect stems from integrating advanced cybersecurity directly into the electronic control units responsible for AI steering. This involves dedicated cryptographic hardware and real-time intrusion detection mechanisms, meticulously designed to fend off increasingly sophisticated cyber incursions. Ensuring the uncompromised integrity of the steering system and, by extension, occupant safety against malicious attacks introduces considerable additional cost and layers of engineering complexity.
Ensuring AI-driven steering systems remain at peak performance throughout a vehicle's lifespan often relies on periodic, predictive software updates and recalibrations. These are typically delivered over-the-air (OTA), demanding a significant, secure cloud infrastructure and constant expert monitoring. This continuous post-sale refinement, necessary for the system to adapt to new road conditions, evolving traffic patterns, or algorithm improvements, introduces a substantial recurring expense, moving beyond the initial purchase price into a long-term service commitment.
Steering Angle Sensor Expenses Key to High Performance Car Control - Beyond the Wheel How Sensors Shape Future Tuning
As of mid-2025, the very concept of fine-tuning a high-performance or luxury vehicle is undergoing a profound transformation. Moving past traditional wrench-and-spanner adjustments, the emerging paradigm, captured in "Beyond the Wheel: How Sensors Shape Future Tuning," centers on the vehicle's capacity for real-time self-optimization. What's truly novel is the shift from static mechanical configurations to dynamic, software-driven adaptation, where intricate sensor arrays constantly inform and adjust every facet of performance, from power delivery to chassis response. This allows for an unparalleled level of immediate precision and a more intuitively connected driving experience. However, this intelligent evolution doesn't come without its own set of hurdles; the sheer scale of integrating such responsive digital systems into future supercar and bespoke luxury designs raises significant questions about accessibility, long-term adaptability, and the true cost of chasing this level of adaptive perfection.
Moving beyond the usual performance measures, leading-edge luxury vehicles are beginning to embed intricate acoustic and micro-vibration sensors. These systems continuously scrutinize the cabin's soundscape and structural resonances. The real-time data allows for adaptive engine mounts and sophisticated active noise cancellation, creating a quieter environment tailored to the immediate driving conditions – a remarkable feat of engineering, though one wonders if chasing absolute silence risks disconnecting the driver from genuine vehicle feedback.
The evolution of tire technology now includes sensors directly integrated into the rubber, offering a granular view of internal temperature variations and the precise pressure distribution where the tire meets the road. This extraordinary data flow permits onboard systems to deduce dynamic slip angles in real-time, facilitating an extremely nuanced adjustment of traction and torque delivery for optimized grip, pushing the absolute limits of adhesion. However, the cost implications and long-term durability of such embedded tech in a high-wear component remain an area of keen observation for widespread adoption.
An intriguing new direction in vehicle adaptation incorporates biometric sensors that interpret a driver's physiological state – things like heart rate variations, eye movements, and even subtle shifts in muscle tension. The vision is for the car's intelligent algorithms to adjust powertrain response, steering feel, and active suspension damping in real-time, theoretically aligning the vehicle's behavior with the driver's current intention and stress levels. While promising a highly personalized experience, the accuracy and ethical implications of interpreting human physiology to dictate machine performance warrant considerable scrutiny.
Advanced vehicles are now deploying ultra-high-resolution LiDAR and multi-spectral imaging. These sensors are generating incredibly detailed, real-time topographical maps of the road surface and estimating friction coefficients. This environmental information allows the car to proactively refine active suspension damping and powertrain behavior milliseconds before encountering changes in road texture or grip. This predictive capability is astounding, yet ensuring the robustness of such systems across all weather conditions and varied road debris presents a monumental calibration challenge.
Future high-performance machines are integrating networks of strain gauges and innovative quantum tunneling composites directly into their chassis. These embedded elements continuously monitor the real-time torsional rigidity and localized flex of the vehicle's structure. This granular data feeds into active structural components, enabling hypercars to dynamically modify their chassis stiffness and optimize handling balance for specific driving scenarios. The long-term reliability and maintenance complexity of such deeply integrated and dynamic structural systems will be a key area for engineers to address.
Steering Angle Sensor Expenses Key to High Performance Car Control - When Sensor Failure Disrupts the Performance Edge
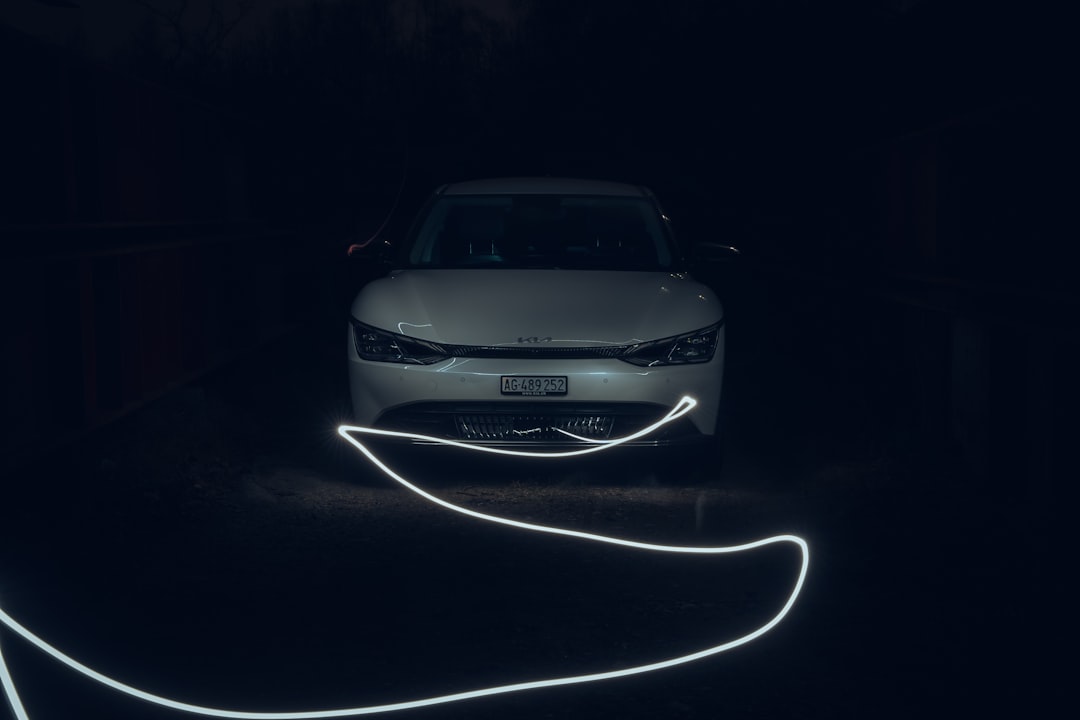
The very foundation of a high-performance car's dynamic capability rests upon an uninterrupted flow of accurate sensor data. When this intricate sensory network falters, particularly in bespoke luxury or supercar designs, the implications are profound. A simple fault in a vital component, such as the steering angle sensor, can swiftly transform predictable, exhilarating handling into a disconcerting experience, undermining the very essence of what advanced digital control systems promise. This susceptibility means that even slight inaccuracies or outright failures in the sensor array, crucial for modern, responsive steering algorithms, can quickly dismantle the meticulously calibrated harmony these vehicles are built upon. This vulnerability compels us to question the actual dependability of such advanced systems, simultaneously revealing the extensive, often unseen efforts required to sustain their flawless performance. As the automotive realm relentlessly pursues digital sophistication, the criticality of sensor dependability only intensifies, posing an intricate challenge for engineers, designers, and indeed, anyone who experiences these vehicles.
Here are five critical observations regarding instances where sensor failure impedes the pinnacle of vehicle performance:
Over time, with continued exposure to thermal cycles and micro-vibrations, the intrinsic accuracy of even robust sensors can subtly erode, leading to an imperceptible drift in data. This silent degradation can quietly pull advanced control algorithms away from their optimal operational parameters, slowly undermining the vehicle's meticulously calibrated performance envelope without triggering an overt fault. One observes a gradual lessening of the 'edge' that was initially engineered into the system.
Given the highly interconnected nature of modern vehicle control architectures, a seemingly minor sensor's slightly skewed output can propagate unexpectedly, subtly contaminating downstream calculations. For instance, a miniscule inaccuracy from a wheel speed reading might not cause a system error, but it could subtly compromise the precision of torque vectoring decisions, leading to non-optimal power delivery or an unmerited intervention from stability systems, thereby dampening true track capability.
When a critical sensor in a vehicle operating at the very edge of performance suffers a significant malfunction, the inherent safety protocols initiate a notably stringent 'limp-home' response. Unlike less demanding platforms, this often involves an immediate and severe curtailment of power and deactivation of core performance features, a direct reflection of the incredibly tight operational margins. At sustained high speeds, even a fleeting moment of sensor ambiguity can present an unacceptable risk to stability and precise control.
A surprising vulnerability lies in the specific sensors governing active aerodynamics. A malfunction in an air-speed pitot tube or a dedicated pressure sensor on a high-performance machine isn't merely about losing efficiency. It can critically imbalance the distribution of downforce at elevated speeds, leading to potential instability and, by design, the abrupt deactivation of sophisticated active elements like adaptive spoilers or diffuser flaps, fundamentally altering the vehicle's high-speed character.
The act of replacing even a single failed sensor in a deeply integrated, high-performance vehicle proves far more intricate than just the component cost. It frequently demands an extensive post-installation recalibration procedure, often utilizing bespoke diagnostic tools from the original equipment manufacturer. This necessity stems from ensuring the new sensor's output precisely harmonizes with the vehicle's complex, interconnected control network, adding a significant layer to the overall repair outlay.
More Posts from tunedbyai.io: