Motor Mount Repair Costs A 2024 Analysis of Parts and Labor Expenses
Motor Mount Repair Costs A 2024 Analysis of Parts and Labor Expenses - Average Motor Mount Replacement Costs in 2024
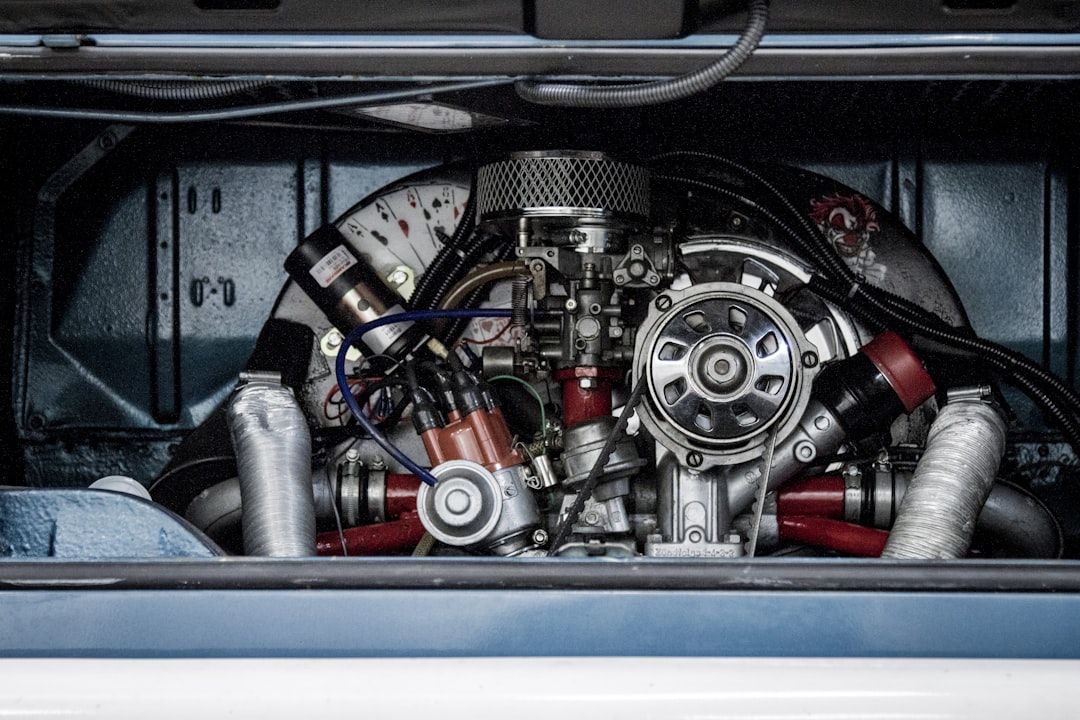
Replacing a motor mount in 2024 can cost anywhere from $250 to $500, with the difficulty of access to the mounts playing a significant role in the final price tag. The cost of replacement parts themselves can range widely, from as low as $50 for a basic mount to over $350 for more complex designs like hydraulic or active mounts. Labor costs are also a factor, usually falling between $193 and $243. However, some estimates put the total cost of a comprehensive replacement at a higher range, from $700 to $800, suggesting that some labor intensive replacements or the use of more expensive parts can drive up costs significantly. While aftermarket parts are an option that can lead to some savings, using original equipment manufacturer (OEM) parts may provide a longer lifespan and better integration with the vehicle. It’s also a good idea to consider replacing all motor mounts during a single repair, even if only one is showing signs of wear, since this can prevent future problems and maintain proper engine performance.
Based on data from various sources, the cost to replace motor mounts in 2024 is quite variable, ranging from roughly $300 to $800. This wide range is unsurprising given the diverse array of vehicles on the road today, with luxury and high-performance models typically driving up the cost due to more specialized components.
Labor costs represent a sizable chunk of the total expense, typically occupying about 50-60% of the bill. This is because accessing and replacing motor mounts can require anywhere from 2 to 4 hours of work, depending on the vehicle's design and how readily accessible the mounts are.
It's interesting to note that even basic rubber motor mounts can begin to degrade as early as five years after installation, especially in areas with drastic temperature swings. This shorter-than-expected lifespan is often overlooked, as most people assume parts will last far longer. Environmental factors clearly play a larger role than many of us realize.
Some automakers now advocate for proactive replacement of motor mounts as part of scheduled maintenance, which can prevent more substantial and costly issues down the line. However, this advice is often disregarded in favor of other more routinely considered maintenance items.
There's a growing trend towards polyurethane motor mounts, which promise a lifespan roughly double that of traditional rubber mounts. While that's certainly appealing, they do come with a 20-30% price premium. It's a trade-off between longevity and initial cost, representing a shift in consumer expectations for the durability of these components.
Motor mount replacement jobs sometimes unveil other underlying problems, like engine misalignment or excessive vibration, which adds to the total expense and repair time. It's a reminder that one issue can quickly snowball into multiple problems.
Hybrid and electric vehicles present unique challenges due to their distinctive weight distributions and power delivery systems. Consequently, their motor mount requirements often diverge, and replacement costs can be much higher than those seen in traditional gasoline-powered cars.
What's perhaps more alarming is the fact that failing motor mounts can lead to collateral damage elsewhere on the car, such as chassis cracks or exhaust system issues, escalating the total repair bill far beyond the initial estimate. This cascade effect highlights the importance of timely motor mount maintenance.
The constant innovation and introduction of new materials in motor mount design are driving up prices, which is not unexpected given the more complex engineering involved. Companies are actively working to improve vibration absorption, and this push for advanced performance will likely continue to impact the cost of replacements.
Finally, the location of the repair shop plays a role in the overall cost. Urban shops, faced with higher demand and cost of living, usually charge more in labor compared to their counterparts in more rural settings. This geographical influence adds yet another variable to the complex landscape of motor mount replacement costs.
Motor Mount Repair Costs A 2024 Analysis of Parts and Labor Expenses - Breakdown of Parts vs Labor Expenses

When evaluating the cost of fixing motor mounts, it's helpful to separate the price of parts from labor. The cost of replacement parts varies widely, with basic rubber mounts starting around $50 and specialized designs, like hydraulic or active mounts, potentially exceeding $350. Labor, however, is often the bigger expense, typically accounting for 50-60% of the total repair cost. This is because replacing motor mounts can be a time-consuming process, with the job taking roughly 2 to 4 hours depending on how accessible the mounts are within a specific vehicle's design. The complexity of getting to the motor mounts, combined with the mechanic's hourly rate (which can vary significantly by region), drives up the labor costs. Consequently, when estimating the overall expense of a motor mount repair, it's crucial to consider both the cost of parts and labor, as labor costs can be unpredictable and potentially inflate the final bill.
The cost of labor for replacing motor mounts can be a surprisingly large part of the total repair bill, sometimes exceeding the cost of the parts themselves. This is largely due to the difficulty of accessing and replacing the mounts in many vehicles, which can take technicians several hours. It's interesting how repair shop location impacts labor rates, with urban areas often charging significantly more, potentially due to higher overhead costs. This suggests that even with the same work, the price can fluctuate based simply on the shop's location.
The design of the motor mount itself can have a substantial influence on the cost of parts. For example, sophisticated mounts like hydraulic or active systems utilize specialized materials and engineering, leading to parts costs that can be many times higher than simpler rubber mounts. It seems many consumers don't fully grasp the complexity of these more advanced designs.
While replacing just the failed motor mount might seem like the logical course of action, technicians generally recommend replacing them all. This is because the failure of one can cause problems with other parts, potentially leading to a far more expensive repair in the future. This idea of a "domino effect" seems to get overlooked by some car owners.
We're also seeing a shift towards higher-quality polyurethane motor mounts. While these materials offer longer life, they usually come with a premium of about 20-30% compared to traditional rubber mounts. This highlights the growing focus on component longevity, but it forces car owners to consider the cost-benefit trade-off when making their choices.
Repair shop estimates for labor often come from standardized charts. However, these charts don't always factor in the specific quirks and challenges of each vehicle. This can lead to unexpected differences in the actual labor time and, therefore, the cost. There are simply no perfect formulas when dealing with the diverse variety of cars on the road.
Motor mounts are often underappreciated when it comes to routine maintenance. The environmental conditions they face, like extreme temperatures and the constant vibrations of the engine, contribute to wear and tear that can go unnoticed. These factors can impact the mount's lifespan far more quickly than we might think, highlighting the importance of keeping an eye on them proactively.
Interestingly, motor mounts can even play a role in how loud your vehicle is. As mounts wear down, the resulting increased engine vibration can create a whole variety of noises that might not be easily attributed to their actual cause. This can lead to a sort of a troubleshooting nightmare where other components are incorrectly identified as the source of the noise.
While tempting, the use of aftermarket parts may appear initially cost-effective but could result in shorter lifespans and compatibility issues, potentially leading to more repair expenses down the road. It's a reminder that cheap might not always be better in the long run.
Routine inspections of motor mounts aren't always a part of typical car check-ups. Yet, if these are performed regularly, potential issues can be addressed early, before they turn into expensive and complex repairs. This is a prime example of how prioritizing maintenance can lead to a smoother and cheaper ownership experience.
Motor Mount Repair Costs A 2024 Analysis of Parts and Labor Expenses - First Quarter 2024 Cost Reduction Trends
During the first three months of 2024, we saw some interesting changes in the cost of vehicle repairs. Most notably, the price of parts decreased by a significant 24%, continuing a pattern of lower costs seen previously. This seems to generally match the overall trends of inflation that were occurring. While repair labor costs dipped slightly by 0.8%, they remain a major factor in the total repair expense, especially for newer electric vehicles where labor accounts for over 40% of the repair cost. The shift in auto production back towards pre-pandemic levels appears to be impacting how parts are priced, with electric vehicle repairs requiring a larger share of the parts expenses. It's fascinating to see how this period reveals a dynamic shift in how automotive repairs are costing consumers, with a stronger focus on managing expenses.
During the first quarter of 2024, we saw some interesting trends in motor mount repair costs. Notably, parts costs dipped for the second consecutive quarter, falling by a significant 24%. This contrasts with labor costs, which experienced a slight 0.8% decrease after a period of rising prices. It's intriguing how these two elements are moving in different directions.
Overall, vehicle repair costs seem to be generally in line with broader inflation patterns. It's been observed that labor accounts for a larger portion of repair expenses in newer electric vehicles (EVs) compared to traditional vehicles, contributing 43.5% versus 34.8% respectively. Similarly, EVs represent a larger share of parts costs at 38.9% compared to 44.6% for non-EVs. This could be linked to the complexity of EV components and possibly their production volumes.
Interestingly, car production saw a surge in 2023 with a 9.6% increase compared to the previous year. While production is expected to settle back to pre-pandemic levels this year, the automotive market remains active. In the first quarter of 2024 alone, the US saw a 27% jump in light vehicle sales compared to the same period in 2023. This suggests a strong appetite for new vehicles despite potential concerns regarding the cost of repair.
EVs, while offering fuel cost savings estimated between $1,363 and $2,471 annually compared to gas-powered cars, still come with a premium of around 10% when buying new, with an average price of $48,451 for gas-powered vehicles. This might influence consumer choices, although the fuel cost savings do seem compelling.
However, we need to be mindful of larger economic trends as well. Labor costs are on the rise, with a 4% increase in unit labor costs in the nonfarm business sector during the first quarter of 2024. This trend is largely due to rising hourly compensation coupled with a minor increase in productivity. This rise in labor cost is projected to continue impacting the manufacturing sector, with expectations of a 5.2% increase in wages and benefits throughout 2024. This increasing cost of labor is bound to impact repair costs.
The cost of materials used in motor mounts is also changing, with a move towards newer composite materials that can reduce weight significantly. This is a testament to the continuous development of innovative materials, and it's important to watch how this might affect the cost of production and ultimately the repair sector. We're also seeing the inclusion of more advanced features like hydraulic and active motor mounts, which while promising in terms of performance, likely increase repair costs. This innovation cycle continues to push repair costs in various directions.
The data suggests that things are in flux, and repair cost trends can be challenging to predict with certainty. We are in a period of transition where the convergence of new material sciences, advanced engineering, evolving labor markets, and the continued growth of the electric vehicle segment is shaping the landscape of auto repair. Understanding these forces will be critical to anticipating future trends in motor mount repair costs.
Motor Mount Repair Costs A 2024 Analysis of Parts and Labor Expenses - Decline in Motor Mount Parts Pricing
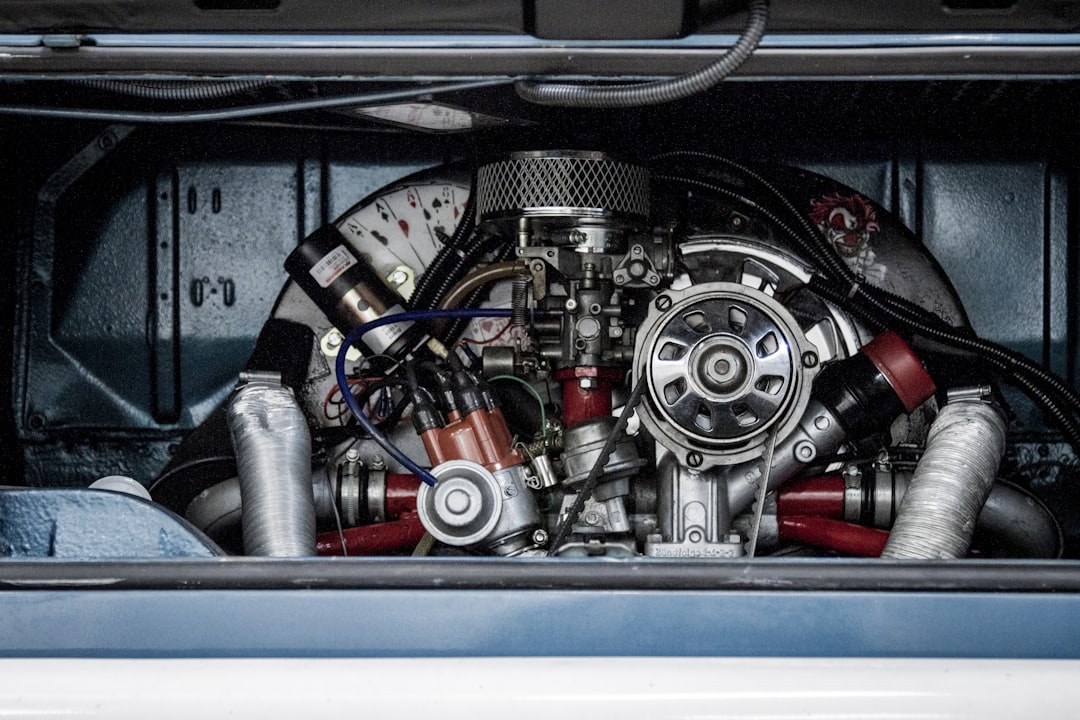
During the initial months of 2024, a decline in the cost of motor mount parts became apparent, with a 2.4% drop observed in the first quarter. This marks the second consecutive period of decreasing parts prices, a trend not entirely mirrored by labor costs, which also saw a slight dip. However, looking at the bigger picture, the yearly change in parts prices shows a modest 0.9% rise, while labor expenses have increased at a more pronounced rate of 4.9%. These fluctuations underscore the shifting landscape of repair costs, where short-term dips can sometimes conceal longer-term upward pressures. It's a reminder that while some temporary relief may be experienced, vehicle owners should be mindful of the potential for future cost increases in motor mount repairs.
The recent decline in motor mount part prices, a notable 2.4% drop in the first quarter of 2024, appears tied to a more stable automotive supply chain and increased production. This stands in stark contrast to the disruptions caused by the pandemic. It's intriguing that while labor costs only dipped slightly, they still dominate a significant portion of repair costs for modern electric vehicles, often exceeding 40% of the total. This highlights the growing complexity and specialized skills required for modern repair compared to traditional cars.
The more complex motor mount designs, like hydraulic and active systems, also contribute to their higher price tags, occasionally exceeding $350. This illustrates how advanced engineering can influence both performance and cost. Interestingly, the use of composite materials in motor mounts is growing, showing a potential for weight reduction without sacrificing strength. This not only impacts vehicle performance but also suggests a shift in production techniques and associated costs within the automotive industry.
The downward trend in part prices aligns with a notable increase in light vehicle sales – a 27% jump in the first quarter of 2024. This surge in demand might influence parts prices to remain competitive and accessible to consumers. It’s somewhat alarming how failures in motor mounts can lead to increased repair costs in other areas, like exhaust systems or chassis components. This happens due to the cascade effect of vibrations and misalignments caused by a failing mount. The interconnected nature of vehicle systems is highlighted in these unforeseen repair expenses.
Basic rubber mounts, known to degrade within five years, are still widely used, leading to potentially underestimated repair costs when they unexpectedly fail. It appears that the cost fluctuations of motor mount repair materials are influenced by global market trends. This includes the introduction of innovative materials that can increase initial costs but potentially reduce future replacements due to improved durability. The automation in assembly and the shift towards advanced manufacturing methods are influencing the economic landscape of automotive parts, with direct ramifications for motor mount pricing in the years to come.
One surprising observation is that higher-quality aftermarket parts, while potentially providing longer lifespans, come with a noticeable price premium – roughly 20-30% above standard options. This presents a curious challenge to consumers who must balance the immediate cost versus long-term value when choosing replacement parts. This underscores that the most expensive option is not necessarily always the most economical in the long run.
Motor Mount Repair Costs A 2024 Analysis of Parts and Labor Expenses - Labor Cost Fluctuations for Motor Mount Repairs
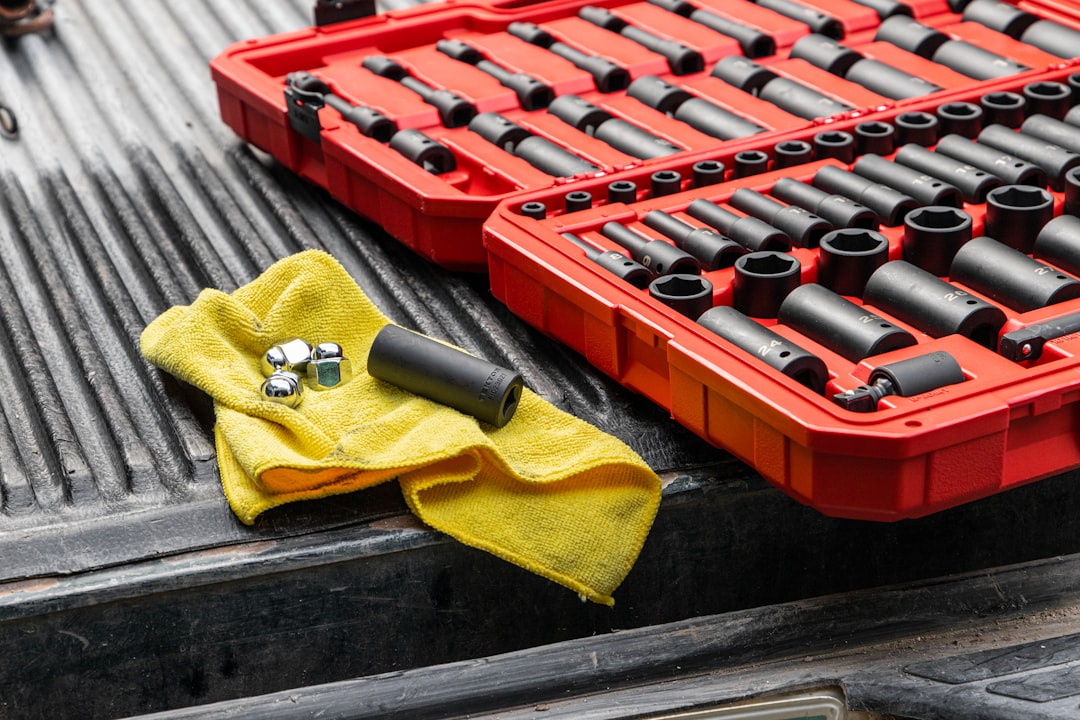
The cost of labor for repairing motor mounts continues to shift, influenced by factors like where the repair shop is located and how complex the vehicle's design is. Throughout 2024, labor costs have remained a substantial part of the total repair bill, typically making up about half to three-fifths of the final price. Estimates suggest labor costs usually range from around $193 to $243 per hour, but it's important to note that this varies by shop. The amount of time a mechanic needs to fix a motor mount can differ greatly based on the vehicle's design; a standard repair could take anywhere from two to four hours. It's noteworthy that while prices for parts have been trending downward, the increasing cost of labor remains a significant factor for vehicle owners, particularly with the expanding use of more complex motor mounts. Given this dynamic, it's prudent for consumers to be mindful of the possibility of unexpected labor expenses when getting their vehicles repaired.
The cost of labor for motor mount repair can fluctuate dramatically, influenced by the complexity of the mount's design. Hydraulic or active mounts, for instance, often demand specialized skills and tools, stretching repair times and increasing the labor portion of the bill. It's also notable that the location of the repair shop plays a major role. Urban repair centers tend to charge substantially more, possibly due to higher operating costs and demand, sometimes marking up labor rates by 30-50% compared to more rural areas. This wide geographical variation makes it difficult to pinpoint a consistent price for labor.
A failed motor mount can create a domino effect of problems. Beyond causing engine instability, it transmits excess vibrations through the chassis, potentially leading to accelerated wear on other components. This can dramatically increase overall repair expenses as issues arise that might otherwise not have occurred.
The automotive world is embracing newer, lighter-weight composite materials for motor mount construction. While these are innovative and can boost vehicle performance, they also add a premium to the cost of the parts. This shift in materials necessitates a change in repair strategies and can impact pricing.
A growing trend among auto manufacturers is recommending proactive replacement of motor mounts during scheduled maintenance. However, many drivers tend to overlook this advice, focusing on more common maintenance items. This oversight can result in unexpected and significant costs if a mount failure causes damage to other vehicle parts down the road.
Interestingly, the automotive supply chain seems to be stabilizing after the pandemic-related disruptions. This, coupled with increased vehicle production, has resulted in lower part costs, including those for motor mounts. However, the extent of these cost reductions varies among different types of vehicles.
It's easy to underestimate the lifespan of basic rubber motor mounts. They often show signs of wear as early as five years after installation, due to factors like extreme temperature fluctuations. This relatively short lifespan can lead to unexpected repair costs for vehicle owners.
The complexity of modern vehicles has led to a growing demand for skilled automotive technicians. This, in turn, has driven up the cost of labor. It's clear that as cars become more technologically advanced, the specialized skills needed to maintain and repair them become more valuable.
A worn motor mount can significantly change the soundscape of a car. It can introduce new noises that may initially lead mechanics down a troubleshooting rabbit hole, mistakenly blaming other components. This can lead to unnecessary repairs and added expenses.
The decision to use aftermarket parts for motor mount replacements often comes down to cost. While they are cheaper initially, they may not have the same lifespan or compatibility with the vehicle compared to original equipment manufacturer (OEM) parts. This can lead to more frequent replacements or repair needs down the line, creating a cycle of higher long-term costs.
While most routine vehicle inspections don't include an in-depth check of the motor mounts, it's wise to consider them. Routine checks can catch potential problems early, preventing major failures and significantly minimizing repair costs. Early detection is, once again, the best defense against higher repair bills.
Motor Mount Repair Costs A 2024 Analysis of Parts and Labor Expenses - Comprehensive Data Analysis Across Vehicle Types
The cost to repair motor mounts in 2024 reveals a complex interplay of factors that vary significantly depending on the vehicle type. This includes the design intricacy, especially for newer electric and hybrid models, along with changes in both the price of parts and labor costs. While the cost of replacement parts for motor mounts has shown a slight decrease in some areas, labor continues to be a considerable portion of the final repair bill. Labor costs are particularly notable in urban environments, where repair shop rates tend to be much higher. Adding complexity is the increased use of advanced materials and engineering in motor mounts, which may lead to higher upfront costs but possibly deliver extended lifespan. With these variables in play, understanding how motor mount repair expenses differ between various car types is crucial for vehicle owners making informed choices about maintaining their cars.
Examining motor mount repair costs across various vehicle types reveals a complex interplay of factors. The physical layout of different vehicles, like the placement of engine components in sports cars versus compact cars, significantly impacts the accessibility of motor mounts and, as a result, repair costs. The shift towards composite materials in motor mount construction offers benefits like weight reduction and improved vibration dampening. However, these advanced materials can lead to more involved and costly repairs due to their unique properties and the specialized tools needed to work with them.
Hydraulic motor mounts are a good example of how advanced engineering impacts repair costs. While these mounts excel at vibration control, their complexity means that repairs often require specialized skills and tools, making them a longer and more expensive repair process compared to more standard rubber mounts. The rate at which motor mounts degrade can be vehicle-specific. For instance, heavier vehicles like SUVs might experience accelerated wear on their mounts compared to smaller sedans due to the added stress on these components.
As motor mounts age and fail, they can introduce unexpected noises into a vehicle, potentially confusing mechanics during troubleshooting. These noise patterns can lead to a misdiagnosis of the problem, resulting in unnecessary repairs on other components—a costly side effect of neglecting a simple motor mount issue. The rising cost of labor for EV repairs is noticeable, as EV architecture and unique components contribute to the elevated costs. Labor typically accounts for over 40% of the total cost of EV motor mount replacement, highlighting how a vehicle's design affects repair costs.
The tendency to prioritize standard maintenance items, like oil changes, over the less frequently considered motor mounts can lead to costly surprises. Since motor mounts play a pivotal role in engine and vehicle stability, overlooking their importance can potentially lead to significant repair bills when a failure cascades into problems with other systems. Given the growing complexity of vehicles, DIY motor mount repairs are becoming increasingly challenging, particularly with modern cars incorporating mounts in hard-to-reach locations. It often becomes more practical and reliable to seek professional assistance to ensure a thorough and safe repair.
The location of the repair shop can dramatically impact the cost of a repair. Shops located in urban environments frequently have higher labor rates compared to those in rural areas, sometimes differing by as much as 50%. This difference is primarily due to variations in demand, operational costs, and the cost of living in these regions. While the failure of one motor mount may seem like an isolated issue, mechanics often advise replacing all of them during a repair. This approach helps prevent future problems and promotes optimal vehicle performance. Despite this guidance, vehicle owners frequently prioritize minimizing immediate costs, potentially overlooking the potential for future issues and expenses.
It is clear that vehicle type, the use of advanced materials, design complexity, and regional factors all contribute to varying motor mount repair costs. Understanding these diverse factors is crucial for consumers, as well as the automotive repair industry, to anticipate and adapt to changing repair needs and costs.
More Posts from tunedbyai.io: