The Hidden Culprits 7 Unexpected Causes of Low Coolant in Your Vehicle
The Hidden Culprits 7 Unexpected Causes of Low Coolant in Your Vehicle - Cracked Engine Block Causing Invisible Leaks
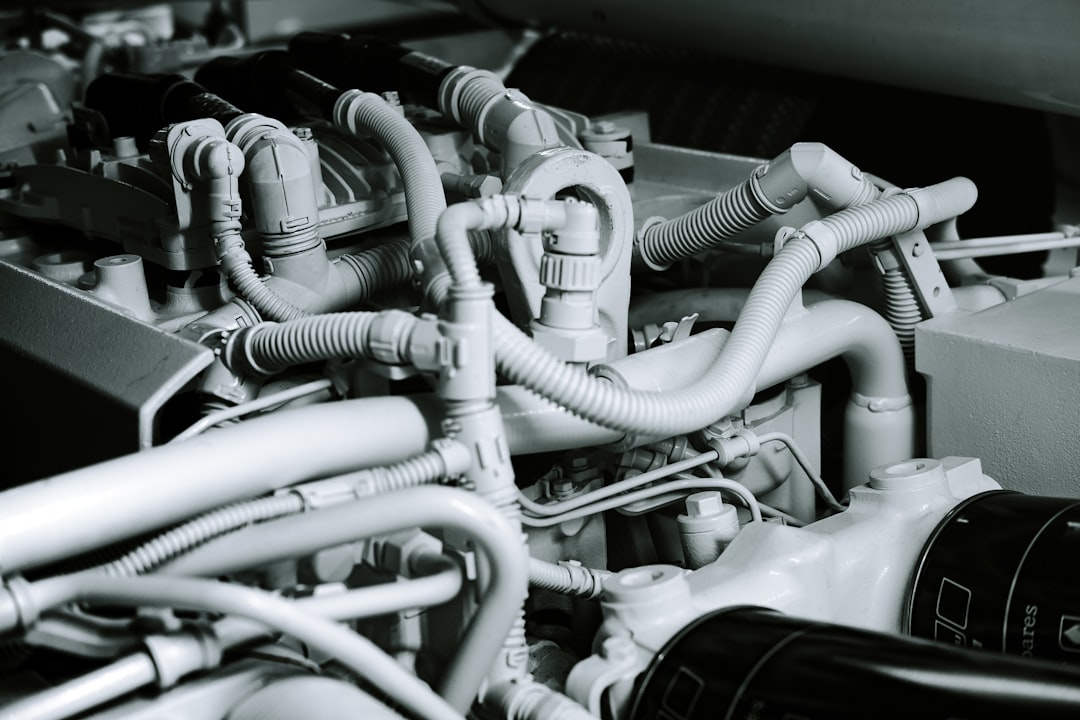
A cracked engine block can be a tricky issue when it comes to coolant leaks, often causing problems without any clear warning signs. While you might experience low coolant, engine misfires, or unusual white exhaust smoke, the source of the leak might be hidden within the engine itself. Coolant can leak into the combustion chamber without any noticeable external signs. Furthermore, if coolant and oil mix due to a crack in the engine block, you might find your oil looking milky or foamy. Things like overheating, neglect, and pushing the engine too hard can weaken the block and lead to these cracks. If ignored, a cracked engine block can severely harm your engine's performance and lifespan.
A fractured engine block doesn't always announce its presence with obvious external leaks. Instead, coolant can subtly seep into the oil pathways within the engine. This clandestine leakage often manifests as a milky, frothy appearance of the engine oil, a critical signal hinting at deeper engine problems.
Engine blocks, commonly fabricated from materials like cast iron or aluminum, are vulnerable to developing cracks under extreme pressure, sudden temperature shifts, or inherent flaws during manufacturing. These cracks can be exceedingly fine, making them nearly invisible without a close and detailed examination.
The engine's cooling system operates under considerable pressure, frequently exceeding 15 psi. A seemingly insignificant fracture in the engine block allows coolant to escape quietly. This leakage might not manifest as a noticeable drip or puddle, as the high temperatures inside the engine often cause the escaping coolant to vaporize.
While a visible coolant leak is readily diagnosed, these stealthy leaks can lead to catastrophic overheating. Even a seemingly small loss of coolant can disrupt the delicate thermal balance of the engine, creating a chain reaction that may ultimately cause devastating engine failure.
Some engine configurations strategically place critical components, such as the head gasket, very close to the engine block. A crack in the engine block can undermine the integrity of these components, creating unseen pathways for coolant to migrate, further masking the problem's source.
Certain driving circumstances, like high-speed driving or hauling heavy loads, can put further strain on already weakened areas of the engine block. This extra stress can transform what was once a small issue into a major failure over time.
Infrared thermal imaging offers a method for pinpointing temperature irregularities on the engine's exterior. This technique is particularly useful in detecting concealed coolant leaks by identifying abnormally cool patches due to the evaporating coolant.
Under normal conditions, engine oil and coolant don't intermingle. Their unexpected blending is a strong indicator of internal leaks, often caused by a damaged engine block or gasket, demanding further investigation.
A fractured engine block can also create pathways for combustion gases to escape into the cooling system. The resulting gas bubbles disrupt the normal flow of coolant, leading to excessive heating and possible engine damage.
Repairing a cracked engine block usually necessitates significant interventions, such as welding or specialized epoxy sealants. The severity and location of the crack heavily influence the practicality and affordability of such repairs.
The Hidden Culprits 7 Unexpected Causes of Low Coolant in Your Vehicle - Faulty Cylinder Head Gasket Allowing Coolant Seepage
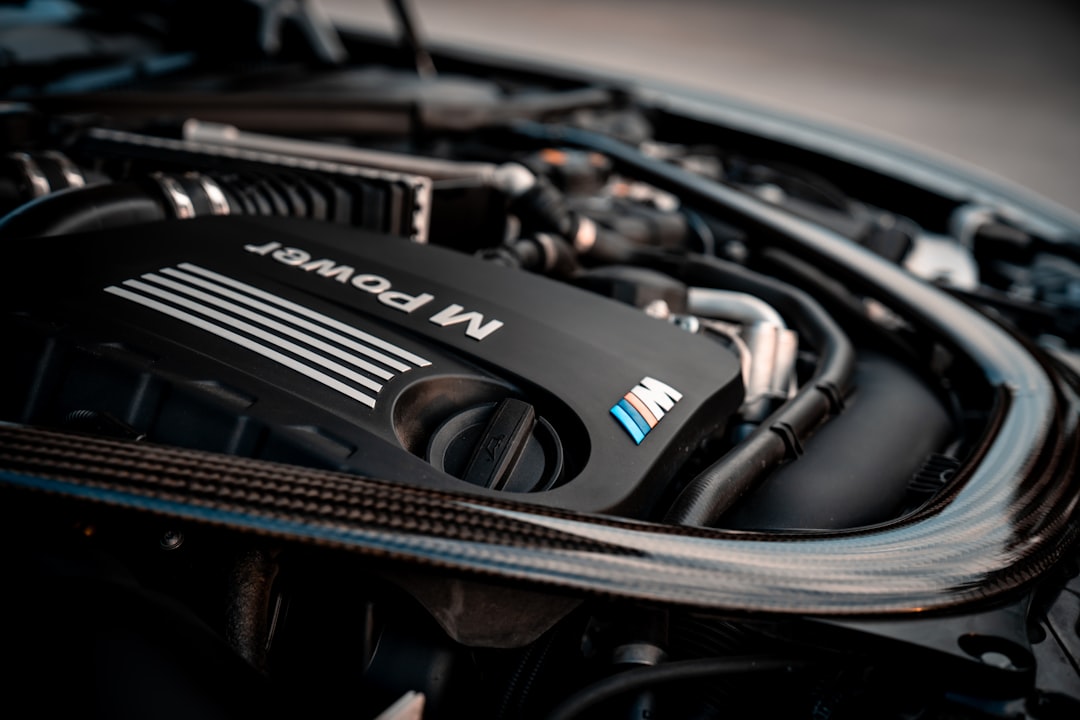
A faulty cylinder head gasket can be a sneaky culprit behind a dwindling coolant reservoir. It can create a pathway for coolant to leak into the combustion chamber, where it mixes with engine oil. This mixing can be a major issue, often resulting in a milky or frothy appearance of the engine oil, visible on the dipstick. You might also notice coolant drips around the cylinder head, indicating a potential external leak.
The cylinder head gasket is put under pressure during engine operation, and excessive engine stress or heat can lead to its failure, worsening the situation. Symptoms like engine misfires or unusual exhaust smoke can also be linked to a failed head gasket, though these might indicate a more serious underlying problem.
If you suspect a faulty cylinder head gasket, it's crucial to take action. Ignoring a coolant leak can lead to a significant decline in engine performance and cause costly repairs. It's important to be vigilant about maintaining appropriate coolant levels and regularly checking for signs of leakage to keep your engine running smoothly.
A faulty cylinder head gasket can be a sneaky culprit behind coolant loss. Its primary job is to seal the gap between the engine block and the cylinder head, preventing coolant from entering the combustion chambers. But when it fails, coolant can seep into the engine, mixing with the oil and leading to a range of issues. This mixture can compromise lubrication, wear down engine components faster, and lead to problems like hydrolock – a situation where liquid fills the cylinders, disrupting the engine's ability to compress air, which can cause severe engine damage.
While a damaged gasket might lead to obvious signs like overheating, white exhaust smoke, or a sweet smell, it's not always that straightforward. Some leaks are subtle, with coolant seeping out without readily apparent symptoms. The incredibly tight tolerances during manufacturing make head gaskets susceptible to even slight imperfections or misalignment during installation, increasing the risk of failure.
The relentless heat and pressure cycles an engine endures can put stress on the gasket's materials, leading to tiny cracks over time. This weakens the gasket, making it more prone to leaks. The coolant itself is designed to protect engine components from corrosion, but when it mixes with oil due to a failed gasket, this protective chemistry is altered, which can speed up corrosion processes and ultimately cause engine failure.
Sometimes, a failing gasket can lead to a loss of coolant without any visible external leaks. The coolant can escape into hidden oil passages, making it harder to track down the source of the problem. Though typically made of durable materials, head gaskets can degrade under extreme heat or exposure to certain contaminants, shortening their life and increasing the likelihood of leaks.
While replacing a head gasket often involves labor-intensive repairs, overlooking the early warning signs can result in even higher costs. Continued thermal stress and contamination can significantly damage your engine, potentially leading to a complete engine replacement. Furthermore, the precise location of a leak caused by a faulty head gasket can lead to steam or vapor escaping from the engine's intake, sometimes leading mechanics on a wild goose chase in their attempts to pin down the root cause of the coolant leak. It's a reminder of how seemingly small components like gaskets can have a big impact on the health of your engine.
The Hidden Culprits 7 Unexpected Causes of Low Coolant in Your Vehicle - Deteriorating Radiator Hoses Leading to Slow Drips
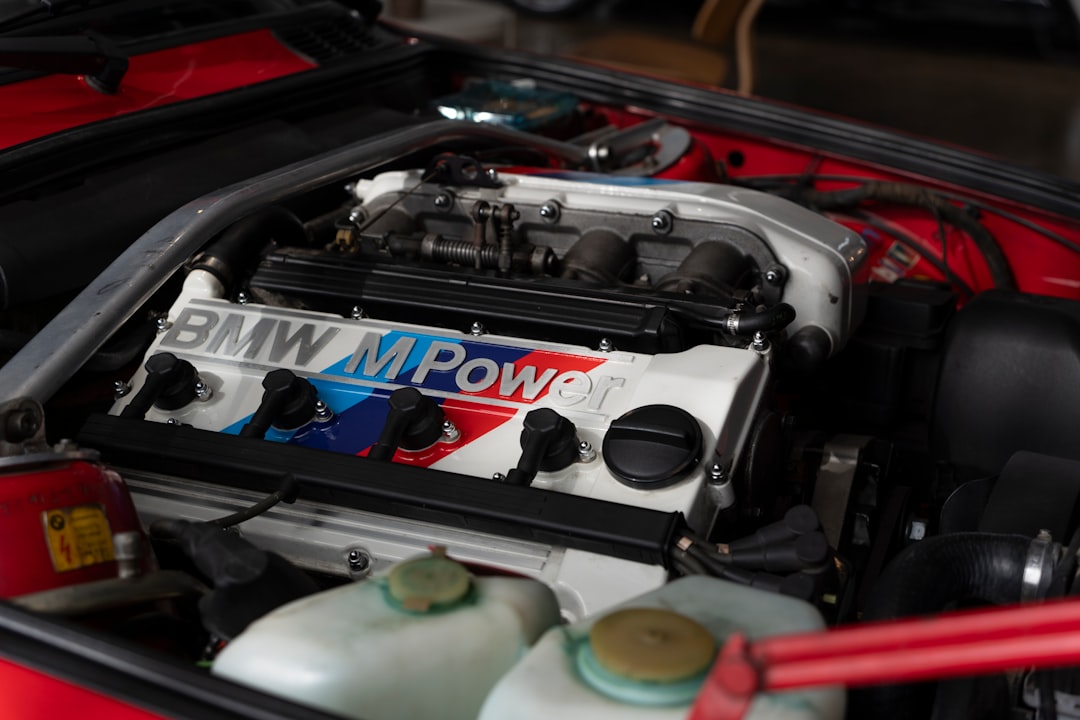
Radiator hoses, like any other rubber component in a vehicle, degrade over time. This deterioration can lead to slow, often subtle, leaks of coolant. These leaks can be hard to spot initially, making it difficult to notice the gradual depletion of the engine's coolant. If left unchecked, this slow leak can reduce the cooling system's effectiveness and lead to engine overheating. A common indicator of a failing radiator hose is coolant leaking onto the ground beneath the vehicle. It will often appear as a green liquid with a slightly sweet odor. The lower radiator hose, which connects the bottom of the radiator to the water pump, is a particularly critical part of the system. Damage to this hose can quickly disrupt the engine's cooling, often resulting in overheating problems. To maintain the health of your engine, it's important to regularly inspect and maintain your radiator hoses. Catching these issues early can prevent a major inconvenience and expensive repair down the road.
### Surprising Facts About Deteriorating Radiator Hoses Leading to Slow Drips
Radiator hoses, often overlooked, can be a surprising source of slow coolant drips. These seemingly insignificant leaks can gradually deplete your coolant, potentially leading to engine overheating and damage if ignored. Let's examine the intriguing factors that contribute to their deterioration.
First, the hoses themselves are susceptible to the passage of time. Made from rubber or silicone, they're constantly exposed to the harsh environment under the hood—extreme heat, engine oil, and the corrosive chemicals in the coolant itself. Over time, these exposures lead to a gradual weakening of the material, creating tiny cracks that may not be immediately visible to the naked eye.
Moreover, the constant fluctuations in temperature caused by the engine's cooling system put further strain on the hoses. As coolant heats and cools, the hoses expand and contract, potentially leading to stress points and ultimately leaks. This constant cycling can slowly weaken hose material, making them prone to bulges, cracking, and eventual drips.
The cooling system is designed to operate under pressure, often exceeding 15 psi. As hoses degrade, they may start to bulge or weep coolant under this pressure. Ironically, this high-pressure environment can mask the early signs of leakage, making the problem harder to detect until the leaks become more prominent.
Ozone, naturally present in the atmosphere, can also accelerate hose degradation. Especially in hoses exposed for long periods, ozone can attack the rubber, causing surface cracking and making them more vulnerable to eventual leaks.
The coolant itself plays a role in hose deterioration. Many coolants have additives designed to inhibit corrosion in the engine, but these same chemicals can be corrosive to rubber over time. These additives slowly degrade the hose's internal structure, making it less flexible and resilient, increasing the likelihood of slow leaks developing.
Furthermore, the placement of hoses in the engine compartment subjects them to bending and twisting. If improperly installed or if aftermarket modifications place undue stress on the hoses, it can create minute fractures in the hose material that eventually lead to leaks.
Another fascinating aspect of hose failure is a phenomenon called "internal delamination". This internal breakdown happens when layers within the hose start to separate due to chemical degradation and thermal cycling. Such internal failures are invisible from the outside, making them incredibly difficult to diagnose until the coolant starts to escape.
Even the seemingly simple hose clamp can play a role in coolant leaks. If clamps are not tightened correctly or if they rust over time, they might not hold the hose securely. This looseness provides an escape route for coolant, resulting in slow drips.
Additionally, the relentless vibration caused by the engine can contribute to the weakening of the hoses. These vibrations, combined with thermal cycles, cause micro-cracks that expand over time. Eventually, this cumulative damage makes the hoses more susceptible to leaks.
Thankfully, many hose-related coolant leaks are preventable. By conducting regular visual inspections and maintenance, you can identify signs of wear like bulges, cracks, or soft spots in the hose material. Catching these issues early can help prevent significant coolant loss and potential engine damage.
It's crucial to acknowledge that these are the more insidious kinds of coolant leaks, the slow drips that many drivers either don't notice or dismiss. But they can be signs of a deteriorating cooling system, and it's best to address these issues before they escalate into a more serious problem.
The Hidden Culprits 7 Unexpected Causes of Low Coolant in Your Vehicle - Corroded Heater Core Resulting in Gradual Loss
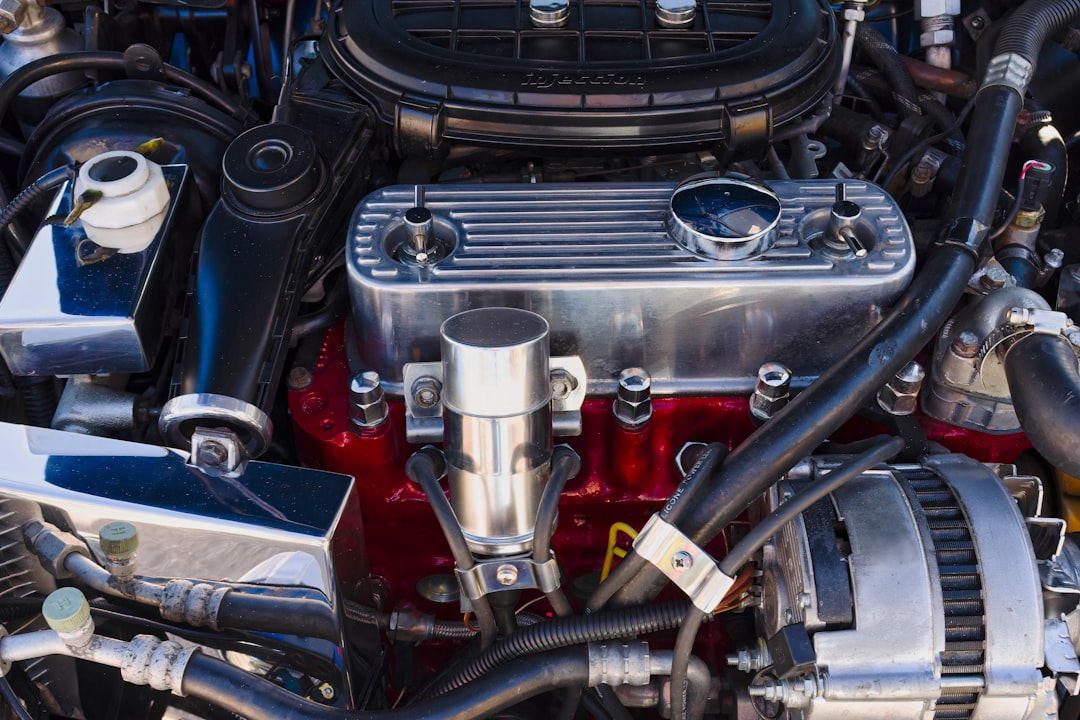
A corroded heater core can lead to a slow, often unnoticed, loss of coolant in your vehicle's cooling system. This corrosion can create small leaks that gradually deplete the coolant reservoir. One of the more noticeable signs of a corroded heater core can be coolant accumulating on the passenger-side floor, often accompanied by reduced heating output from the vents. This is a situation to be aware of because the coolant leaking into the interior can cause a variety of issues, including interior damage and potentially, overall performance issues of the vehicle. It's important to address a suspected corroded heater core quickly as ignoring it can worsen the corrosion and lead to potentially costly repairs. The neglect of regular maintenance on the heater core can hasten the corrosion process, making it more likely that major problems will develop and lead to the need for larger repair jobs. Keeping a close eye on coolant levels and noting any signs of coolant leaks in the interior is a prudent step that can help avoid more serious issues with your engine down the road.
A corroded heater core can lead to a gradual and often unnoticed coolant loss, typically manifesting as a puddle in the passenger footwell. This might seem like a minor issue at first, but it's worth understanding the contributing factors that accelerate this process.
One intriguing aspect is the role of **electrolysis**. Stray electrical currents within the vehicle's electrical system can interact with the coolant, creating a corrosive environment that speeds up metal degradation in the heater core. Ensuring proper grounding can potentially mitigate this issue.
The **material composition** of the heater core also matters. Many are made of aluminum or brass, each exhibiting unique corrosion characteristics. Aluminum, for example, is prone to galvanic corrosion when in contact with other metals, emphasizing the importance of using compatible components in the cooling system.
Though usually smaller than radiators, a heater core's influence on coolant levels can be substantial. A slow leak can result in the loss of several hundred milliliters of coolant over time, which, if ignored, can lead to engine overheating.
**Temperature swings** also play a role. The heater core operates under significant temperature variations as the engine warms and cools. This constant expansion and contraction places stress on the material, accelerating corrosion and leading to difficult-to-detect pinhole leaks.
Inspecting the heater core isn't always easy. Hidden deep within the dashboard, it's often not readily accessible. Many vehicle owners might only realize there's a problem when they encounter coolant odors inside the vehicle or experience foggy windscreens.
The **coolant itself**, while designed to protect the engine, can also contribute to corrosion. Coolant additives degrade over time, leading to possible pH imbalances that foster corrosion.
**Contaminants** in the cooling system can also accumulate within the heater core. Debris such as dirt, rust, and scale can obstruct coolant flow, creating hot spots and accelerating corrosion rates in those areas, ultimately causing leaks.
The connections to the heater core, often made of rubber hoses, are subject to deterioration. If these **connections fail or loosen**, they can leak coolant, possibly mimicking a heater core problem when the issue lies elsewhere.
The age of a vehicle and the maintenance history can also be factors. **Older vehicles** with infrequent coolant changes are at a greater risk of developing corrosion. Older coolant can lose its protective properties, increasing the acidity of the coolant and the likelihood of leaks.
The heater core's constant exposure to **heat and moisture** creates the perfect breeding ground for corrosion. This combination accelerates the corrosion process within the enclosed environment, frequently resulting in slow coolant leaks that might go undetected until they become serious problems.
It’s crucial to be aware that even slow, subtle leaks can eventually lead to serious issues. A corroded heater core can be a source of unseen coolant loss, and understanding the various factors that contribute to this corrosion can aid in prevention and early detection.
The Hidden Culprits 7 Unexpected Causes of Low Coolant in Your Vehicle - Malfunctioning Thermostat Causing Pressure Buildup
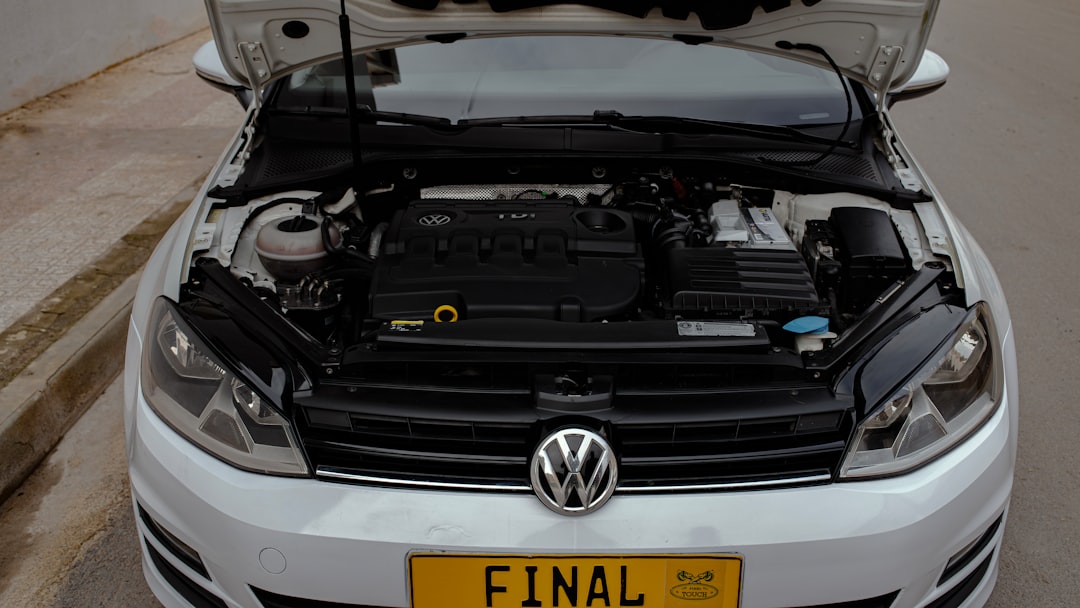
A faulty thermostat can be a sneaky cause of low coolant, often leading to serious engine problems. When it gets stuck in the closed position, it prevents the flow of hot coolant to the radiator, causing the engine to overheat. This blockage leads to a buildup of pressure within the cooling system, and can increase the likelihood of coolant leaks, especially around the thermostat housing. If you notice the upper radiator hose getting hot while the lower hose remains cold, it's a strong sign that coolant isn't circulating correctly due to a problem with the thermostat. If you disregard these issues, they can lead to major engine damage from overheating, highlighting the importance of regular cooling system checks. Recognizing the part the thermostat plays in your vehicle's cooling system can help you avoid expensive repairs and keep your engine running smoothly.
A malfunctioning thermostat can disrupt the delicate balance of a vehicle's cooling system, leading to unexpected pressure buildup. This often occurs when the thermostat fails to open or close properly, preventing the normal flow of coolant to the radiator. If the thermostat gets stuck closed, the engine can overheat as the coolant isn't effectively circulated to dissipate heat. This can cause the upper radiator hose to become very hot while the lower one stays cool, a telltale sign of poor coolant circulation.
The inability to regulate temperature can result in the coolant reaching temperatures far higher than intended, sometimes surpassing its boiling point. This overheating leads to the formation of vapor bubbles within the coolant, causing a phenomenon called vapor lock, which further disrupts circulation and amplifies pressure within the system. Modern cooling systems are designed to operate within a specific pressure range, typically around 13-16 psi. A malfunctioning thermostat can push these pressures far beyond their intended limits, increasing the risk of leaks, or even catastrophic failures in components like hoses or gaskets.
The rapid pressure changes caused by a faulty thermostat can lead to cavitation – a process where vapor bubbles implode, which can slowly erode metal parts of the cooling system. This weakens the integrity of these components and degrades the cooling system's ability to manage the engine's heat. Engines naturally experience thermal cycling as they heat up and cool down, but a failing thermostat can intensify these cycles. This repeated expansion and contraction stresses the joints and components, making them more susceptible to leaks and overall deterioration.
Interestingly, a malfunctioning thermostat can actually interfere with overheating warnings. If the engine isn't reaching the proper operating temperature due to the thermostat's malfunction, it can produce misleading readings, making accurate diagnostics difficult. Furthermore, an overly hot engine can lead to incomplete combustion, increasing the output of harmful emissions. Modern engines are built to operate within a tight temperature range for optimal efficiency and emissions control, and a faulty thermostat can disrupt this equilibrium.
Diagnosing thermostat-related issues can be challenging as many of the symptoms, such as poor heater performance, unusual engine oil temperatures, or strange noises from the cooling system, also present with other problems, like a failing water pump or a clogged radiator. Ultimately, a thermostat that's not working correctly can cause severe engine damage. Persistent overheating and excessive pressure can warp cylinder heads or damage piston rings, leading to expensive repairs.
Modern cars are increasingly relying on electronic thermostats that provide precise temperature control. While these advanced systems offer improved control, they can also experience failures due to electrical problems, further highlighting the complexity of diagnosing coolant system issues and potential for unexpected pressure issues. It underscores the importance of regular maintenance and vigilance in noticing any changes in engine behavior, particularly related to temperature and cooling.
The Hidden Culprits 7 Unexpected Causes of Low Coolant in Your Vehicle - Damaged Water Pump Impeller Reducing Circulation
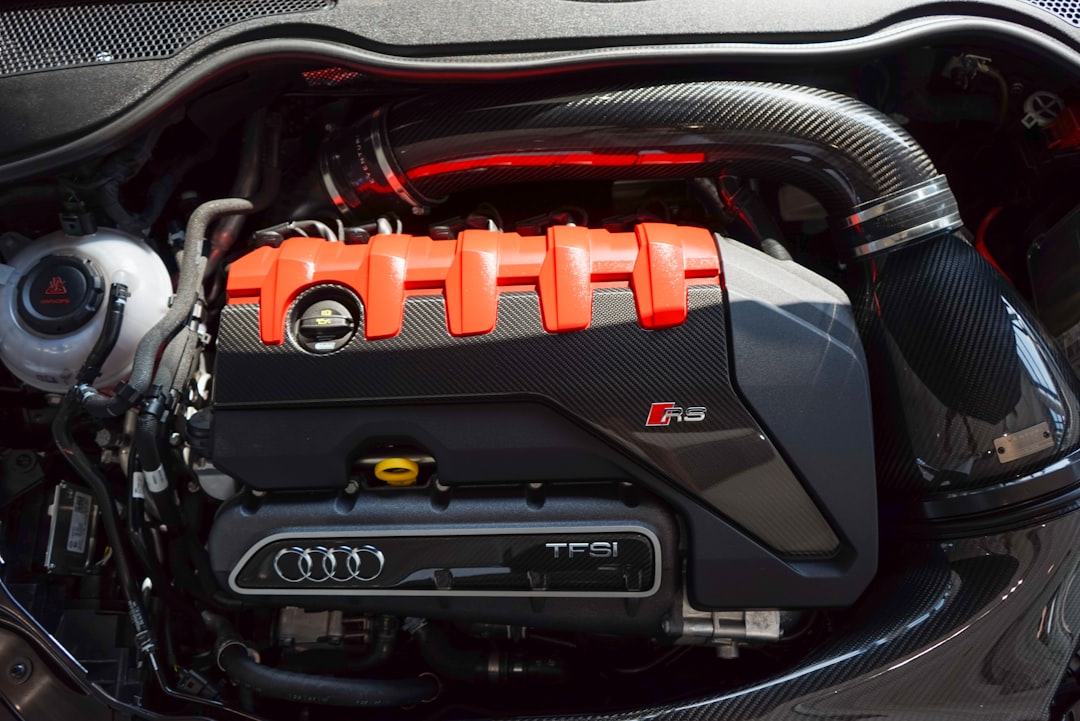
A damaged water pump impeller can significantly hinder the flow of coolant throughout your engine's cooling system, often leading to overheating. This component, responsible for circulating coolant, can become damaged over time due to various factors such as wear and tear, rust buildup, or a poorly functioning drive pulley. When the impeller is damaged, it can't effectively push the coolant through the system. This reduced coolant flow can result in a variety of warning signs, including erratic temperature gauge readings and unusual bubbling or boiling in the radiator. If you notice these warning signs, it's a strong indicator that the coolant isn't circulating as it should. While often overlooked, a damaged impeller can lead to serious engine problems if left unaddressed. Maintaining the water pump and its components through regular checks can prevent overheating and promote engine longevity.
A damaged water pump impeller can quietly sabotage your engine's cooling system by reducing coolant circulation, potentially leading to overheating. This seemingly simple component plays a crucial role in maintaining the engine's thermal balance, and even minor damage can significantly impact its performance. The impeller's design often incorporates intricate vanes to maximize coolant flow, and any damage to these vanes can dramatically reduce the pump's efficiency.
The cooling system operates under pressure, and a damaged impeller might not be able to sustain it, leading to decreased flow rates and increased engine temperatures. Additionally, the damaged impeller can increase the chances of cavitation – the formation and collapse of vapor bubbles in the coolant. This phenomenon generates shock waves that can further erode the impeller, worsening the problem and eventually hindering circulation.
Interestingly, a damaged impeller often doesn't come with immediate obvious signs. Drivers might not notice any unusual sounds and may only become aware of a problem when the engine starts to overheat or they see a gradual, slow climb in the temperature gauge reading. Without proper circulation, the engine block can experience uneven temperature distribution, leading to localized hot spots. This uneven temperature can cause warping of engine parts or cause issues with critical seals and gaskets.
Furthermore, a malfunctioning impeller can accelerate wear and tear within the cooling system. Not only does the impeller itself suffer, but the pump housing and bearings can experience premature wear and tear, potentially creating a chain reaction of problems. The coolant itself is also important here as many modern coolants are formulated with additives that protect the cooling system from corrosion. When circulation is restricted due to a damaged impeller, these additives can be less effective, potentially increasing the risk of corrosion in localized areas, and ultimately affecting the engine's lifespan.
A compromised impeller can also impact the flow rate of the coolant itself. During high-demand situations like towing or uphill driving, the engine requires increased coolant flow to dissipate heat effectively. A damaged impeller may not be able to maintain the necessary flow rates, possibly leading to overheating.
One of the reasons for water pump failures can be a lack of regular maintenance. Many car owners don't realize how important it is to check the water pump during routine maintenance checks. Recognizing early warning signs, such as fluctuating coolant levels and changes in the engine's heating behavior, can help in preventing major issues later on. Impeller material composition can also play a significant role in its lifespan. Many impellers are made from plastic or metal, and the type of coolant used can affect how quickly the impeller deteriorates. If a coolant is too corrosive, or it's missing some crucial additives, then the impeller can degrade more quickly. This is why regularly checking coolant quality is important for ensuring the long-term health of your water pump.
Understanding how a water pump operates, and specifically the impeller's role, is essential for proactive vehicle care. A damaged impeller can be a silent saboteur, slowly undermining the cooling system and potentially causing significant engine damage. Staying informed about these potential issues can help drivers make better decisions and avoid expensive repairs.
The Hidden Culprits 7 Unexpected Causes of Low Coolant in Your Vehicle - Worn Out Freeze Plugs Allowing Coolant Escape
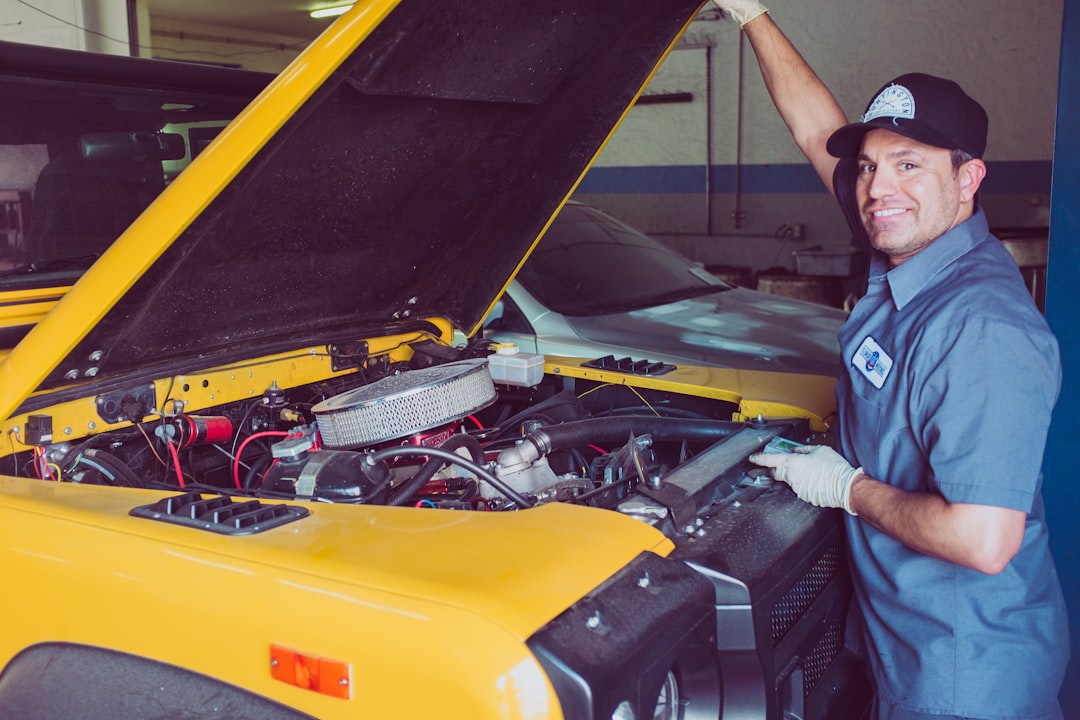
Worn-out freeze plugs, often overlooked, can be a surprising cause of coolant loss in your vehicle. These small, usually metal plugs are strategically placed in the engine block to prevent damage from freezing temperatures. However, over time, they can become weakened by corrosion or develop cracks due to age or exposure to harsh elements within the engine bay. This can lead to leaks, allowing coolant to escape and disrupt the delicate balance of your engine's cooling system.
If you notice coolant pooling under your vehicle, particularly after the engine has been running, or experience an unexplained rise in engine temperature, it could be a sign that one or more freeze plugs have failed. These symptoms point towards coolant escaping rather than flowing efficiently through the cooling system as it should.
Causes of freeze plug wear and tear are often related to the chemical environment within the cooling system. Factors like rust, corrosion, and even inconsistencies in the coolant itself can accelerate the degradation of these plugs. This emphasizes the importance of maintaining the proper type and concentration of coolant in your engine as recommended by your vehicle's manufacturer.
Neglecting a leaking freeze plug can have significant consequences. It can lead to engine overheating, causing serious damage to critical engine components. In some cases, it can even lead to a complete engine failure, a scenario easily avoided with timely inspection and repairs. Keeping your cooling system in optimal condition includes paying attention to these smaller components, like freeze plugs, for early signs of wear. Regularly inspecting and replacing worn-out plugs helps prevent significant problems and keeps your engine running smoothly.
Worn-out freeze plugs, often overlooked components within an engine's cooling system, can be a surprising source of coolant leaks. These plugs, typically made of metal, are designed to prevent the engine block from cracking due to the expansion of freezing coolant. However, over time, the constant vibration of the engine and the repetitive temperature changes during operation can cause these plugs to weaken and eventually fail.
One of the more intriguing aspects of freeze plug failure is their often hidden location deep within the engine block. This makes visual inspections challenging, meaning that leaks often go unnoticed until they become significant, potentially leading to engine damage due to overheating. Furthermore, the symptoms of freeze plug failure can easily be mistaken for other cooling system issues like a faulty head gasket or a damaged water pump. This overlap in symptoms makes diagnosis more complicated, requiring a thorough inspection to pinpoint the true cause.
Another interesting point is the concept of galvanic corrosion, which can play a part in the deterioration of freeze plugs. Similar to other components within the cooling system, freeze plugs can be subject to this process when they are in contact with dissimilar metals. This process causes a slow breakdown of the metal, making them prone to developing cracks and leaks.
The manner in which a freeze plug is installed can also have a noticeable impact on its lifespan. If a freeze plug is not installed correctly or if it's over-tightened, it can be deformed, potentially leading to premature failure. This emphasizes the importance of following the correct installation procedures and torque specifications during any repair or replacement.
It's also important to understand that freeze plugs serve as a pressure release mechanism, though it's a secondary one. While they help prevent engine block damage from freezing coolant, they can also release pressure when the cooling system is under extreme stress. A failed freeze plug can alter the cooling system's pressure in unpredictable ways, which can make the engine more prone to overheating.
Unlike many other cooling system components, freeze plugs are often ignored during regular maintenance checks. This oversight can lead to gradual coolant loss over time, and it highlights the importance of making sure these critical parts are kept in good condition.
The type of material used to create freeze plugs can also affect their durability. For example, aluminum freeze plugs might corrode faster in certain conditions compared to those made from cast iron. This distinction emphasizes the need to choose suitable materials when replacing a failed plug.
Finally, the condition of freeze plugs is an indicator of the overall health of the cooling system and is a reflection of the care that's been given to it. By keeping an eye on these crucial components, we can gain insight into the health of the entire cooling system, potentially helping prevent significant damage and costly repairs from overheating and coolant loss.
In conclusion, worn-out freeze plugs can be a silent contributor to coolant loss and potential engine damage. While they may not be the most commonly examined component in the cooling system, their role in protecting engine integrity and releasing excess pressure shouldn't be underestimated. Regularly monitoring coolant levels and seeking professional assessment if any leaks are suspected are vital in maintaining engine health.
More Posts from tunedbyai.io: