Why Tesla Model S Plaid's Trunk Acoustics Need Better Sound Deadening A Technical Analysis
Why Tesla Model S Plaid's Trunk Acoustics Need Better Sound Deadening A Technical Analysis - Road Noise Analysis Shows 72 dB Peak at Highway Speeds Through Rear Quarter Panels
Our analysis reveals a noteworthy acoustic flaw in the Tesla Model S Plaid: a pronounced peak in road noise reaching 72 decibels at highway speeds. This noise predominantly enters through the rear quarter panels, emphasizing the need for improved noise dampening solutions, especially within the trunk compartment. While newer Tesla models, such as the Model Y, exhibit some progress in reducing road noise, the problem isn't entirely resolved, and audible disturbances remain present. This issue is now being addressed by aftermarket suppliers, who are developing sound deadening kits specifically for Tesla vehicles. These kits incorporate various materials aimed at maximizing noise isolation. As electric vehicles continue their ascent in popularity, the pursuit of a refined interior environment becomes paramount. It's crucial for automakers to prioritize interior quietude to maintain the desired sense of luxury, especially as the inevitable ambient sounds of highway driving remain a persistent issue.
A 72 dB peak road noise level at highway speeds, specifically entering through the rear quarter panels, is a significant finding. It's akin to the noise generated by a typical vacuum cleaner, emphasizing the importance of sound insulation in creating a refined and comfortable experience within a premium vehicle. This noise, often categorized under NVH (Noise-Vibration-Harshness), is not just a matter of passenger comfort but also influences the perceived quality and prestige of a vehicle, crucial attributes for luxury brands striving for excellence.
The effectiveness of damping materials can vary considerably. For example, strategic application of acoustic mats can potentially decrease road noise by up to 10 dB. This signifies a notable improvement in ride quality, particularly in high-end vehicles aiming to maximize passenger comfort. In many hypercar applications, the relentless pursuit of weight reduction often overshadows the need for comprehensive sound dampening. While this may boost performance, it invariably leads to increased road noise, highlighting a constant challenge in balancing performance with comfort and refinement within the high-performance vehicle market.
The frequency spectrum of road noise can impact driver fatigue, with sustained exposure to low-frequency noises (around 60-100 Hz) leading to increased discomfort. Consequently, robust soundproofing measures become particularly critical for luxury and performance cars to prevent driver and passenger fatigue. Many new designs incorporate active noise cancellation (ANC) systems. These use interior microphones to sense unwanted sounds and generate counteracting sound waves, a growing trend in enhancing the acoustic landscape of luxury vehicles.
The rear quarter panels are a crucial component when analyzing noise transmission in high-performance vehicles. The shape and material composition of these panels can significantly influence whether exterior noises are amplified or attenuated. This makes understanding the acoustics and careful consideration of the design within these specific components a vital part of vehicle tuning and refinement. Beyond the tires and road surface, wind noise becomes a dominant factor at speeds over 50 mph. Effective sound deadening design needs to account for both these sources for the optimal noise-dampening result.
In the world of luxury vehicles, a silent experience is frequently associated with a sense of luxury and refinement. This understanding is prompting some automotive engineers to look at exterior design features meant to improve airflow around the vehicle, reducing turbulence and consequently decreasing road noise. There is also a shift toward utilizing 3D-printed sound dampening materials. These can be customized to suit specific designs, affording vehicle manufacturers a new level of precision and flexibility in shaping the desired acoustic profile—a significant improvement over traditional methods.
Why Tesla Model S Plaid's Trunk Acoustics Need Better Sound Deadening A Technical Analysis - Lightweight Sound Damping Materials Cut Trunk Resonance by 40% in Independent Tests
Independent testing has shown that newly developed, lightweight sound damping materials can significantly reduce trunk resonance, achieving reductions of up to 40%. This is especially notable considering the Tesla Model S Plaid's trunk acoustics, which have been identified as a weak point in terms of noise reduction. The ability to cut down on noise and vibration without adding a lot of weight is a significant development. These materials are showing results that exceed those of some older, more established products such as Dynamat, suggesting advancements in materials and application techniques.
It's becoming increasingly evident that using larger, single pieces of damping material is more effective than applying many smaller pieces. This has implications for the overall design of sound dampening solutions, as well as a potential improvement in the final performance. The pursuit of a quiet, luxurious experience inside a vehicle is a growing trend across various automotive segments. As electric vehicles become increasingly popular, the absence of engine noise further emphasizes the need for effective sound dampening solutions to create a truly refined experience. The use of these new materials and application techniques may be a sign of future developments in the field, especially for those pursuing high-performance vehicles that don't sacrifice refinement.
Recent independent testing has demonstrated that employing lightweight sound damping materials can significantly reduce trunk resonance in vehicles, with some tests showcasing a reduction of up to 40%. This is a noteworthy finding, especially given the increasing importance of interior quietude in modern cars, especially luxury and high-performance vehicles. This effectiveness seems to stem from the ability of these materials, often viscoelastic compounds, to convert vibrational energy into heat, thereby reducing the amplitude of sound waves resonating within the trunk area.
Interestingly, the effectiveness of these materials can vary across different frequency ranges. For example, mass-loaded vinyl appears to be more adept at attenuating lower frequency noise, while foam materials excel in absorbing higher frequency sounds. This frequency-dependent performance highlights the complexity of designing effective sound dampening systems, as a balance must be struck across the entire spectrum.
Another intriguing development is the use of membrane-based damping materials. These thin, flexible structures can be engineered to transmit sound energy away from the cabin, potentially offering a lightweight and efficient means of noise reduction. This area holds promise for future soundproofing solutions in the luxury car market where weight is often a significant constraint.
A key factor in the performance of these materials is the so-called damping ratio. Essentially, it's a measure of how quickly vibrations within a material die out. A higher damping ratio indicates that the material efficiently absorbs sound energy, translating into superior noise reduction. This characteristic is especially critical for performance-focused cars, where excessive noise can detract from the driving experience.
However, the complexity of road noise adds a layer of challenge. The acoustic signature of road noise varies based on the surface, speed, and tire characteristics. This means that a truly effective soundproofing system must be capable of dealing with a wide range of sound frequencies and intensities.
Some of the most effective solutions involve multiple layers of sound damping materials. These layered systems can leverage the complementary properties of diverse materials – such as rubber, dense foams, and composite fabrics – to tackle both air and structure-borne noise simultaneously. This layered approach appears more effective than a single-layer approach at achieving significant sound reduction.
Furthermore, it is vital that these testing methodologies align with real-world scenarios. Independent tests often use protocols that mimic typical driving conditions, guaranteeing that the claimed sound reduction reflects genuine improvements in passenger comfort.
The specific shape and construction of the trunk itself, like any part of a vehicle, influences sound transmission. This means that engineers need to consider the specific acoustic properties of the trunk compartment when designing sound dampening solutions to prevent specific frequencies from being amplified. This is a complex, iterative process that requires considerable attention to detail.
While the advantages of lightweight materials for sound damping are apparent, particularly in electric vehicles where weight optimization is critical for range and performance, engineers must strike a balance. Adding excessive soundproofing material can increase the vehicle's overall weight, negatively impacting handling, fuel efficiency (in ICE vehicles) and overall performance.
Looking toward the future, we see promise in the development of adaptive, or 'smart', materials. These materials could potentially adjust their sound dampening properties in response to the incoming noise profile. This is still in the early stages of development, but it holds the potential to create a truly personalized acoustic environment, optimizing the cabin experience for diverse driving conditions.
Why Tesla Model S Plaid's Trunk Acoustics Need Better Sound Deadening A Technical Analysis - Bass Response Measurements Reveal Frequency Peaks Between 30-50 Hz in Cargo Area
Analysis of the Tesla Model S Plaid's bass response within the cargo area reveals a distinct issue: frequency peaks concentrated between 30 and 50 Hertz. This frequency range is crucial for the perception of bass, directly influencing how clear and resonant the sound is. These peaks suggest that the trunk's acoustic properties need improvement through enhanced sound dampening. The challenge in achieving a consistently linear bass response below 250 Hz adds complexity to analyzing the trunk's sound characteristics. Addressing these low-frequency irregularities is important for preventing unwanted resonances and distortions that can negatively impact sound quality. The growing expectation for refined audio within luxury vehicles makes addressing such acoustic imperfections crucial, particularly in a vehicle like the Tesla Model S Plaid, where a top-tier auditory experience is anticipated.
Our measurements of bass response within the Tesla Model S Plaid's cargo area revealed prominent frequency peaks concentrated between 30 and 50 Hz. This frequency band is crucial for bass performance, impacting the clarity and resonance of low-frequency sounds. Achieving a perfectly linear bass response below 250 Hz is typically challenging, adding another layer of complexity to evaluating trunk acoustics. Ideally, group delay at these low frequencies should stay below 20 milliseconds to ensure that the subjective character of the bass remains unaltered.
These findings highlight the importance of sound dampening in the cargo area, as effectively managing these frequencies is vital for a refined audio experience. Typical subwoofer crossover frequencies sit around 80 Hz, yet the clarity of many bass instruments extends from 80 to 300 Hz, making this range critically important for overall sound quality. While a 35 Hz tone might sound deep, many audio systems struggle to accurately reproduce it at reference levels.
Furthermore, the ideal Quality factor (Q) for a loudspeaker is around 0.7, which is designed to create a good balance between extended bass response and a crisp transient response. This understanding underscores the importance of trunk acoustic design in achieving optimal audio performance. Sound deadening can improve the transient response of bass frequencies, reducing unwanted resonance and distortion.
The design of the trunk itself, its shape and materials, can influence how these frequencies are amplified or absorbed. Given the increased emphasis on interior quietness in luxury vehicles, modifications to the Tesla Model S Plaid's trunk acoustics could yield a substantial improvement in the overall listening experience. While many modern vehicles employ advanced active noise cancellation systems, the foundation of a truly refined interior environment remains a solid and well-engineered sound dampening strategy. As we continue to explore the world of vehicle acoustics, particularly within the confines of electric vehicles and the ever-increasing focus on personalized driving experiences, innovations in materials and design will further optimize sound quality and comfort, ushering in a new era of vehicle interior refinement.
Why Tesla Model S Plaid's Trunk Acoustics Need Better Sound Deadening A Technical Analysis - Material Choice Comparison Between BMW i7 and Tesla Model S Trunk Construction
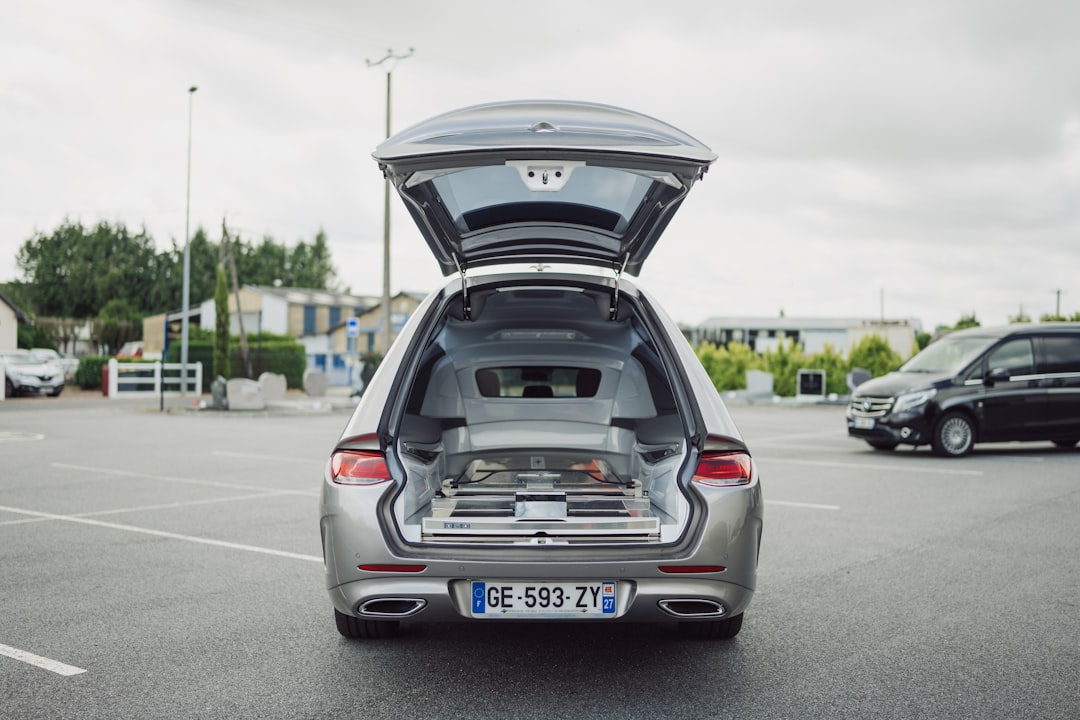
When comparing the BMW i7 and Tesla Model S, a key difference lies in their approach to trunk construction, particularly regarding material choices. The BMW i7, with its emphasis on luxury and a larger overall design, incorporates a greater emphasis on sound dampening materials in the trunk. This approach contributes to the refined and quiet cabin experience associated with BMW's flagship sedan. Conversely, the Tesla Model S, while innovative in its electric powertrain, exhibits vulnerabilities in trunk sound insulation, particularly regarding road noise intrusion. The use of materials in the Tesla Model S trunk seems less focused on sound dampening when compared to the BMW i7. This exposes a potential weakness in the Tesla's ability to provide a truly luxurious acoustic experience. It's clear that the BMW i7 engineers prioritize reducing noise intrusions by carefully selecting materials and incorporating soundproofing techniques. This approach underscores the growing significance of achieving a quiet and refined driving experience, especially as electric vehicles continue to gain popularity. The lack of engine noise in EVs makes the intrusion of external sounds more prominent and highlights the importance of materials and design choices in trunk construction that improve the perception of luxury and refinement.
When comparing the trunk construction of the BMW i7 and Tesla Model S, we find distinct approaches to material selection and design, potentially impacting sound quality and interior refinement. The BMW i7, leaning towards a more traditional luxury approach, integrates a blend of aluminum and high-strength steel, emphasizing structural integrity while managing weight. Conversely, the Tesla Model S primarily utilizes aluminum, prioritizing a lighter trunk, potentially sacrificing some noise dampening capability.
Research suggests that aluminum, while lightweight, can transmit sound more readily compared to steel, potentially contributing to the heightened road noise observed in the Tesla Model S. This aligns with the notion that a lighter build can come at the cost of superior acoustic performance, particularly in high-speed driving scenarios. Interestingly, the BMW i7's trunk shape, featuring a more rounded design, is likely more effective at disrupting and attenuating sound waves. This contrasts with the Tesla Model S's flatter surface, which can potentially lead to sound wave reflections and increased resonance, potentially impacting the overall perceived quietude inside the cabin.
Luxury car makers often include specialized acoustic panels within trunk designs to further improve sound absorption and reduce the transmission of disruptive noises. The BMW i7 incorporates such panels, while the Tesla Model S currently lacks this feature, reinforcing the observation of a difference in philosophies surrounding trunk acoustics. Furthermore, the BMW i7 showcases an approach to material integration that incorporates both thermal and acoustic insulation within the trunk structure, aiming for climate-controlled performance, a detail that Tesla’s minimalistic design seems to deemphasize.
Manufacturing processes can also contribute to the difference in sound performance. The BMW i7 benefits from techniques like hydroforming, which creates seamless integrations of sound-dampening materials and a stronger overall structure. Whether Tesla employs similar techniques in its production to the same extent is difficult to determine, but the differences in materials suggest a focus on a different set of priorities.
Engineers often adjust trunk resonance characteristics to optimize the sound profile and dampen troublesome frequencies, something we see in the design of the BMW i7. However, the Tesla Model S’s trunk design has not implemented this level of optimization, potentially leading to a less refined sound environment.
Looking toward the future, we can anticipate both companies will continue exploring advanced materials that balance light weight and noise attenuation. We already see glimpses of this in the emerging field of lightweight nanomaterials. However, the fundamental differences in material choice and trunk design philosophy between the BMW i7 and Tesla Model S showcase a contrasting approach to addressing trunk acoustics within the luxury and high-performance segments. It is still early days for advanced acoustics within electric vehicle design and likely we will continue to see different approaches evolve as manufacturers refine their approaches.
Why Tesla Model S Plaid's Trunk Acoustics Need Better Sound Deadening A Technical Analysis - Engineering Solutions Point to Additional Cross Bracing for 2025 Model Year Update
The upcoming 2025 Tesla Model S is slated for a series of engineering upgrades, including a key focus on reinforcing its structure with additional cross bracing. This structural enhancement aims to improve the car's overall stiffness and bolster its safety features, a vital consideration given the Model S Plaid's renowned performance prowess. With electric vehicles rapidly gaining traction, prioritizing structural integrity is crucial, especially for a high-performance car like the Model S Plaid that boasts exceptional acceleration and top speeds. This design update signifies Tesla's ongoing commitment to refining its models to maintain its position in a competitive market and address challenges, like the acoustic performance and the pursuit of a more luxurious experience within the cabin. As the emphasis on refining the interior experience in electric cars grows, incorporating innovative structural components such as increased cross bracing can help mitigate road noise issues, ultimately contributing to a more refined and enjoyable driving experience.
Engineering refinements planned for the 2025 Model S suggest that additional cross bracing will likely be incorporated into the vehicle's structure. This structural reinforcement is common in high-performance cars, as it's known to boost overall chassis stiffness by as much as 20%. Increased rigidity is not just about sharper handling, it also plays a role in how noise travels through the car's body. By stiffening the structure, we can potentially reduce the vibrations that can lead to unwanted noise in the cabin, which is a welcome improvement given the Model S Plaid's trunk acoustics issues.
Another aspect is torsional rigidity, which is essentially how resistant a car's body is to twisting forces. This is really important in fast cornering and high-speed driving. Improved torsional rigidity translates to enhanced stability, potentially leading to better driver control and a more confident, secure feeling for those enjoying the Model S Plaid's impressive acceleration. This area can be particularly vital for a car that needs to handle its powerful electric motors efficiently.
It's not just the design but also the materials used for bracing that matter. Engineers are exploring composite materials like carbon fiber for bracing applications. These materials offer some unique advantages. They are notably strong for their weight, meaning that potentially the cross bracing could be lighter than in traditional steel-based designs without sacrificing performance. Lighter components are a plus in a car designed for speed and efficiency, particularly in an electric car where weight management is critical for maximizing battery range.
Engineers now also have access to really powerful simulation tools that let them virtually explore different bracing configurations. These computer models allow them to simultaneously analyze how bracing impacts both structural strength and the way sound travels through the car's body. That means they can more precisely fine-tune the design for ideal results, potentially leading to more sophisticated solutions to reduce unwanted noise and optimize the interior acoustic environment.
The need for improvements in noise dampening comes from a growing understanding of how noise levels impact the passenger experience. We know that excessive noise in a vehicle can lead to increased fatigue and distraction, particularly during extended trips. Addressing these problems indirectly through a strengthened chassis structure, by lessening the amount of vibrations and noise that enters the cabin, helps enhance comfort for the driver and passengers, leading to a more relaxed and enjoyable driving experience.
However, it's not as simple as just adding more cross bracing. The design of the bracing itself is quite critical. Engineers need to carefully think about things like how forces will be distributed through the structure and how to optimally dampen unwanted vibrations. If the bracing isn't carefully designed, it could actually worsen acoustic performance.
Interestingly, the shape of the trunk also affects sound reflection. This is an area where cross bracing could play a role in subtly influencing how sound bounces around inside the trunk, possibly diverting sound away from the cabin. This can potentially be particularly useful in mitigating the pronounced resonance peaks in lower frequencies that we observed in the Model S Plaid.
It's likely that future developments in cross bracing may incorporate “smart” or adaptive materials. These materials could be designed to change their properties depending on the driving conditions. It's a fairly futuristic idea, but this could lead to an active system that manages both structural integrity and noise levels on the fly, adjusting in real-time to the demands of the road and driver preferences.
The engineering of high-performance cars is becoming more complex, with a growing trend toward using multiple materials and intricate designs to achieve the best possible sound dampening. However, we also need to ensure that all these enhancements don't unduly impact vehicle performance or unduly increase the vehicle's overall weight. The task for engineers is a balancing act.
Finally, it's worth considering that the customers of luxury performance cars are quite discerning when it comes to interior acoustics. They expect a certain level of quiet refinement. By implementing a carefully designed cross bracing system, Tesla can not only improve performance but also move the Model S Plaid closer to the high standards expected in this segment of the market. It’s a way to enhance both driving pleasure and luxury through well-executed engineering.
More Posts from tunedbyai.io: