Step-by-Step Guide Replacing the Alternator in a 2011 Hyundai Tucson
Step-by-Step Guide Replacing the Alternator in a 2011 Hyundai Tucson - Disconnecting the Battery for Safety
Prior to starting any work on the alternator, disconnecting the battery is a vital safety precaution in your 2011 Hyundai Tucson. This step is essential to minimize the risk of electrical shock or short circuits, which can occur when dealing with the car's electrical system. It's crucial to properly disconnect the battery terminals using the right tools – start by removing the negative terminal first, then the positive terminal. By disconnecting the battery, you're not only protecting yourself but also the car's sensitive electronics during the alternator replacement process. This step might seem small, but it can prevent more significant issues and ensure a smoother repair process, avoiding potentially unwanted electrical complications later.
1. Prior to any alternator replacement, isolating the electrical system by disconnecting the battery is paramount for safety. A car battery stores a substantial amount of electrical energy, and even seemingly minor accidents can lead to harmful consequences, making it a significant safety precaution.
2. A typical car battery in a charged state can output more than 12 volts. This potential can pose hazards when working near the electrical components. Disconnecting the battery during maintenance helps prevent unexpected activation of electronic systems that could potentially lead to accidents.
3. The 2011 Hyundai Tucson, like many modern vehicles, integrates intricate electronic systems. Disconnecting the battery avoids the risk of potentially harmful voltage spikes during repair. These spikes can cause permanent damage to sensitive electronic components.
4. The terminals connecting to the battery may accumulate corrosion over time, hindering their proper functionality. By disconnecting the battery, you can thoroughly inspect and clean these terminals. This step ensures a secure and effective electrical connection for optimum performance of the vehicle's electrical system once reconnected.
5. A misconception exists where simply switching off the vehicle's ignition is enough to guarantee a completely safe environment when performing mechanical tasks. This is a false assumption, as certain electronic systems remain partially active, even with the ignition off, until the battery is fully disconnected.
6. While the 2011 Tucson is not a hybrid or electric vehicle, it's worth noting that for vehicles with advanced hybrid or electric powertrains, disconnecting the battery becomes crucial due to the presence of very high-voltage systems.
7. In some instances, disconnecting the battery can potentially reset the vehicle’s computer systems. This can be beneficial in eliminating error codes or restoring adaptive memory parameters that may influence the vehicle’s operation following repairs.
8. Disconnecting the battery, though primarily a safety measure, acts as a safeguard against unintended airbag deployment. Airbag systems can activate even with relatively low voltages, highlighting the need for cautious handling during repair tasks.
9. It's also important to remember that older vehicles may have fewer integrated safety features compared to modern vehicles. This makes the necessity of disconnecting the battery even more critical for these models to prevent unpredictable activation of components like fuel pumps.
10. While disconnecting the battery is a prudent practice in most maintenance situations, it's worth noting that failing to adhere to prescribed procedures may void warranties related to specific electronic components. In such cases, any damage that may occur during the repair process without the battery being properly disconnected could lead to expensive repair bills, as certain manufacturer warranties might not cover repairs under these circumstances.
Step-by-Step Guide Replacing the Alternator in a 2011 Hyundai Tucson - Removing the Serpentine Belt
Removing the serpentine belt on your 2011 Hyundai Tucson is a necessary step when replacing the alternator. First, you'll need to find the belt routing diagram, usually located on a sticker under the hood or in the owner's manual. This will be crucial when you reinstall the belt later. Make absolutely sure the engine is off and has cooled down before you start. You'll need a ratchet or a specific serpentine belt tool to loosen the tensioner pulley. Follow the instructions to determine which way to rotate it to release tension on the belt. Gently slide the belt off of one of the pulleys while still keeping some pressure on the tensioner to avoid any sudden snapping. Once the belt is off, you can disconnect the alternator and move forward with the replacement. When putting the new belt on, it's absolutely essential to follow the correct routing to avoid causing damage to your engine. If you don't get it right, you could be in for a very costly repair down the road.
1. The serpentine belt on a 2011 Hyundai Tucson drives a multitude of accessories, including the alternator, power steering pump, and air conditioning compressor, highlighting its importance within the engine compartment. It's a single belt system that has replaced the older, more complex multiple belt setups, which is good from an engine weight perspective.
2. Before attempting to remove the belt, it's crucial to ensure the engine is off and has had a chance to cool down. This precaution safeguards against burns and allows for safer handling of components.
3. Finding the belt routing diagram, usually located on a sticker in the engine bay or in the owner's manual, is essential for both removal and reinstallation. These diagrams are critical for properly reinstalling the belt.
4. To remove the belt, a ratchet or a dedicated serpentine belt tool is usually used to loosen the tensioner pulley. The direction of rotation for the tensioner is important and you must refer to the service manual to do this correctly. This step creates the slack needed to remove the belt.
5. With the tension relieved, the belt can be carefully slipped off of the nearest pulley. If you're also changing the alternator, it is a good idea to disconnect the battery's negative terminal first, as safety needs to be a primary concern when working on electrical systems in your car.
6. Once the belt is removed, the alternator can then be addressed by unplugging its electrical connectors and removing the bolts that secure it to the engine block. It's a pretty straightforward process.
7. When the time comes to reinstall the serpentine belt, it's absolutely critical to verify that the belt follows the precise path laid out in the diagram. If the belt isn't correctly installed, damage to the belt and accessories is likely. Getting this wrong can cause future issues.
8. With the new alternator in place, the belt can be put back on around the various pulleys and the tensioner repositioned to re-apply tension. Make sure you don't over-tension the belt as this is just as bad as having the belt too loose.
9. Lastly, after reassembly, the alternator mounting bolts and tensioner need to be torqued to the manufacturer's specifications. Using a torque wrench is always recommended here.
10. The final step is to reconnect the negative battery terminal. You're then ready to start the engine, listening for unusual sounds or noticing any signs of misalignment. This check is just common sense, and helps to ensure that you've done a good job.
Step-by-Step Guide Replacing the Alternator in a 2011 Hyundai Tucson - Locating and Removing Alternator Mounting Bolts
To replace the alternator on a 2011 Hyundai Tucson, you'll need to locate and remove the bolts that hold it in place. Usually, there are two or three long bolts securing the alternator to the engine. Before tackling these bolts, it's important that you've already loosened or removed the serpentine belt, as this will give you room to work. Having an air-powered ratchet can really accelerate the removal process for these bolts, but make sure there's enough clearance to work within the engine bay without hitting other components. It's helpful to keep track of these bolts because they'll be used again to secure the new alternator, and you'll need to match the bolt holes to the new alternator to avoid issues fitting it. Once the new alternator is in and bolted down, make certain to reconnect all the electrical components correctly. You'll be happy you took the time to do it correctly, because electrical problems can be hard to trace, and this particular system in a 2011 Tucson has had some challenges in the past.
1. The alternator in a 2011 Hyundai Tucson is typically held in place by two or three long mounting bolts, often with Torx or hex heads. These head styles are likely chosen to provide a better grip for high torque applications, reducing the risk of stripping during tightening and loosening. It’s always interesting to see these design choices in action.
2. These mounting bolts, which secure the alternator to the engine block, are placed strategically to leverage the engine’s rigidity and evenly distribute the alternator’s weight. This setup aims to keep the alternator stable despite the vibrations and forces it encounters while running.
3. However, the exact arrangement and size of the mounting bolts can change depending on the car manufacturer. The 2011 Tucson, for example, requires a specific torque when tightening these bolts – likely within the 30-50 foot-pound range. Finding the exact specification is crucial, as incorrect torque could lead to premature bolt or alternator wear.
4. It seems that many automakers now use thread-locking compounds on alternator bolts. It makes sense – these compounds provide added friction, which helps prevent the bolts from loosening over time due to engine vibrations. It’s a simple trick that likely extends the lifespan of the bolts quite a bit.
5. Working on the Tucson’s alternator can be tricky because the front-wheel drive engine bay layout is typically tight, which can make access to the mounting bolts more difficult. One might have to employ special tools or techniques to get to them, and maneuvering around other parts can be quite challenging. This is just another illustration of how the engineers make trade-offs for assembly versus maintainability.
6. During reinstallation, it’s absolutely crucial to ensure the alternator is correctly aligned. If it isn’t, the mounting bolts will bear uneven stress, which can lead to fatigue and eventual failure – and that might not be immediately obvious. This reminds me of the importance of ensuring components are correctly positioned for even load distribution.
7. On some models, the alternator might be tucked away under other parts. To reach the mounting bolts, one might need to remove components such as the air intake or battery. This arrangement emphasizes the efficiency gains from an assembly standpoint, but it might make repairs or maintenance more complex later on. It always makes me wonder who thinks up some of these repair procedures.
8. These mounting bolts are often made from high-grade steel. This type of steel offers a better strength-to-weight ratio, making the bolts strong but still relatively lightweight, which is essential in automotive design where every gram matters. It makes me wonder what material studies went into choosing the specific type of steel here.
9. One risk associated with mounting bolts is something called "bolt stretch." This happens when a bolt is excessively tightened, causing the material to yield beyond its elastic limit. For this reason, engineers spend a lot of time setting specific torque limits for bolts, trying to make sure they stay within the elastic zone throughout their expected lifespan. It's fascinating to see the detailed specifications needed for even these simple parts.
10. Finally, if you encounter rusty or corroded mounting bolts, that can make removal a challenge. Beyond that, it might also indicate a potential problem with the engine bay’s overall exposure to the elements. A little rust prevention can go a long way, especially in parts that are critical to the operation of the vehicle. It makes you wonder how often people consider long term effects versus the costs associated with preventative maintenance.
Step-by-Step Guide Replacing the Alternator in a 2011 Hyundai Tucson - Detaching Electrical Connections
When replacing the alternator in your 2011 Hyundai Tucson, you'll need to disconnect the electrical connections at the rear of the alternator. This involves identifying and carefully removing the primary power wire as well as the connector that interfaces with the vehicle's wiring system. It's important to be mindful of these connections, as any mistakes during detachment or reattachment can potentially lead to future problems. Taking your time and being methodical will make the process of reinstalling the new alternator easier. It's a small detail, but it can really impact how smoothly the replacement process goes. Once you've carefully disconnected these electrical components, you'll be able to proceed with the physical removal of the old alternator itself. It’s a good idea to be gentle with the connections to prevent damage. Pay attention to how everything is connected, so that the reinstallation process is straightforward.
1. When disconnecting electrical connections related to the alternator, it's important to be mindful of static electricity. Discharges, even seemingly small ones, can potentially harm sensitive electronic components within the vehicle's electrical system. It's a reminder that working with electronics requires an awareness of static discharge precautions.
2. The alternator's electrical connections often employ spade connectors or multi-pin types, frequently crafted from materials like aluminum or copper to ensure good electrical conductivity. However, these metals are susceptible to corrosion, particularly in environments exposed to moisture or road salts. Regularly inspecting these connectors for corrosion and ensuring good contact can help prevent issues stemming from degraded connection quality.
3. The plastic housing surrounding most electrical connections is designed to withstand significant heat and vibration, which are common conditions within the engine compartment. Yet, these plastic materials are subject to thermal expansion and contraction. Over time, this can lead to cracking or degradation of the housing, particularly at stress points. This is a subtle reminder that the long-term performance of these plastic parts needs to be considered as part of the overall design.
4. Many alternator electrical connectors include some form of locking mechanism to prevent accidental disconnections while the vehicle is in operation. This is a sensible safety feature, but it can add complexity to removal and reinstallation. Understanding how these locking mechanisms work is important for a smooth repair process.
5. During the process of disconnecting electrical connections, it’s important to be careful not to strain or pull excessively on the wiring harness itself. The delicate internal structure of these wires can be damaged by harsh treatment, leading to broken internal strands and potentially resulting in shorts or other electrical faults. It’s curious to consider how the design of these harnesses might be improved to better withstand the constant vibrations and dynamic loads that cars are subjected to during operation.
6. The polarity of electrical connectors, positive and negative, is crucial when reconnecting them to the alternator. Connecting them incorrectly can easily lead to component damage or potentially even dangerous short circuits. This reinforces the importance of basic engineering principles like redundancy and fault tolerance. It’s important to try to design systems where human error doesn't have catastrophic consequences.
7. The alternator generates heat during normal operation, and this heat can accelerate the degradation of electrical connectors. The specific materials used for the connectors and their housing need to be chosen with thermal performance in mind. It makes you wonder about how long term thermal cycles are carefully considered as part of the design phase.
8. Modern cars often incorporate connectors that feature some level of water resistance, employing seals made of rubber or other materials to protect against moisture ingress. This is a beneficial design choice, especially in regions with wet weather. But these seals aren't indestructible and can degrade over time, creating potential paths for water or contaminants to reach the connector terminals.
9. When reconnecting electrical components after the alternator replacement, it's essential to use the correct wire gauge. Using a gauge that's too small can cause overheating due to increased resistance in the wire, potentially leading to electrical failure or even a fire. Adhering to the wiring specifications provided in service manuals is a necessary precaution.
10. If any electrical connectors are damaged during the process of removing the old alternator, it's recommended that replacement parts match the original equipment specification. This will help to ensure compatibility and maintain the overall reliability and performance of the alternator system. It's a reminder of how engineering choices cascade across many different subsystems. A small choice on a connector can impact everything else downstream.
Step-by-Step Guide Replacing the Alternator in a 2011 Hyundai Tucson - Extracting the Old Alternator
With the electrical connections and the serpentine belt out of the way, you're ready to physically remove the old alternator from your 2011 Hyundai Tucson. This process involves carefully extracting the alternator from its mounting location on the engine. First, you'll need to remove the bolts or nuts that hold the alternator in place. Make sure you've got adequate space to work as you remove the alternator, being mindful of any surrounding components. It's a good idea to keep track of all the hardware as you go to ensure proper reassembly later on. Once the bolts are removed, you can gently pull the old alternator away from its mounting points. Be mindful of any potential obstructions during removal, ensuring you don't force the alternator in a way that could cause damage. Once it's out, take some time to visually inspect the area where it was mounted. Look for any signs of wear or damage that might help understand why the alternator failed in the first place. This helps to prevent the issue from repeating itself in the future. Finally, you can set the old alternator aside, ready to replace it with the new unit.
1. The alternator in a 2011 Hyundai Tucson is a key component, not only for charging the battery but also for powering essential systems like the fuel pump and ignition. Its reliable operation is crucial for the vehicle to function correctly.
2. Removing an old alternator sometimes reveals hidden components like the tensioner or idler pulleys. Examining them during the removal process can identify signs of wear or impending failure, potentially preventing more complex repairs later. It's a good reminder that "while you're in there" is a great opportunity to do some inspection and preventative maintenance.
3. While taking apart the alternator system, you may encounter bolts designed to stretch slightly when tightened, known as torque-to-yield bolts. Some designs dictate that these bolts shouldn't be reused, as their structural integrity may be compromised, which could affect the quality of the reinstallation. This emphasizes that you must really understand the design of the specific components.
4. Many modern vehicles use alternators with integrated voltage regulators, so removing the alternator means handling not just a generator, but also a complex electronic circuit. Care is required to prevent damage to these delicate parts. This is a good example of the trend of putting more electronics in the car.
5. How the alternator is mounted has a huge effect on its lifespan. If the alternator is poorly aligned or secured, excessive vibration results. This harms the alternator's bearings and electrical connections, potentially leading to premature failure. This is a good illustration of how design can greatly impact reliability.
6. Without careful documentation of the electrical connections at the back of the alternator during removal, incorrect reconnection can lead to severe problems, including short circuits or system failures that might be hard to diagnose. It makes you wonder why more vehicles don't have some kind of built in diagnostic to help find these sorts of problems.
7. There are a lot of variations in alternator designs, and some are engineered with high efficiency ratings, generating more power with less engine load. Replacing the alternator with a part that doesn't meet the original specs can affect vehicle performance. It's interesting to consider the trade-offs made when designing these systems.
8. The weight of the alternator can vary considerably between models and designs. Handling a heavier unit carelessly can cause strain or damage to surrounding parts during removal. It's always important to take note of such aspects and try to protect sensitive parts as you work.
9. When disconnecting the alternator, be mindful of potential tension in the serpentine belt system. Sudden movements can cause the belt to snap or become misaligned, potentially impacting other belt-driven components. It's another reminder that the system of components can be coupled in surprising ways.
10. Finally, having all your tools readily accessible and understanding the specifics of the engine bay can save you a lot of time and frustration. Removing the alternator can be challenging even for experienced mechanics due to tight working spaces. This emphasizes the importance of knowing what you are doing and being prepared before you start.
Step-by-Step Guide Replacing the Alternator in a 2011 Hyundai Tucson - Installing and Securing the New Alternator
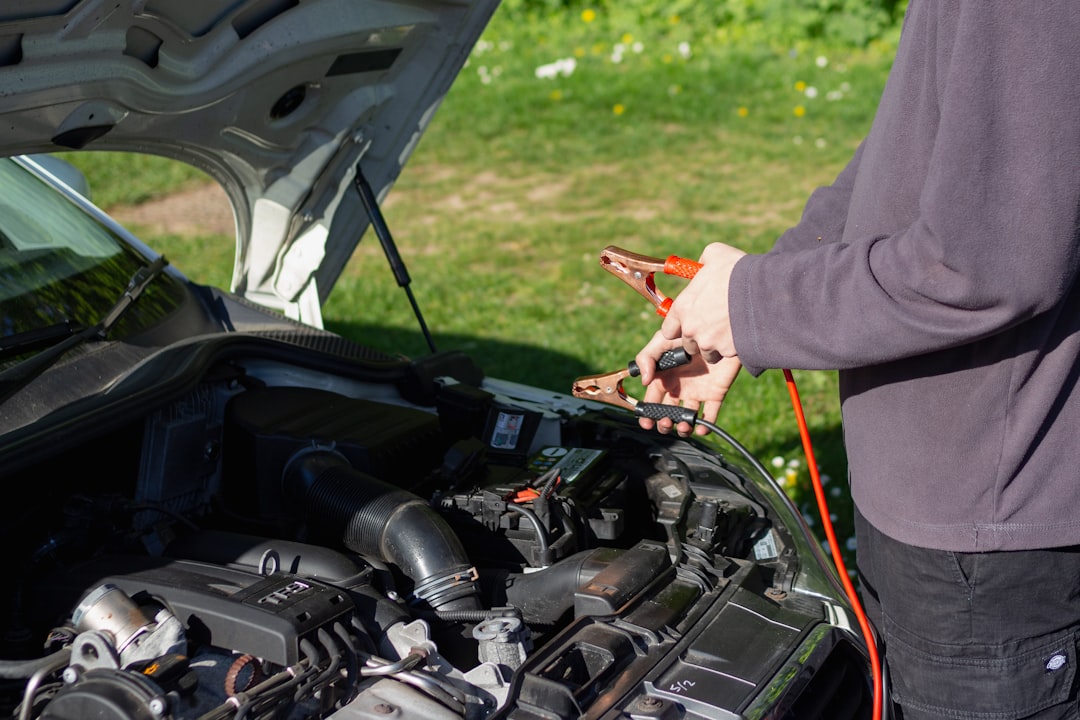
With the old alternator out and the area prepped, you can now install the new one. Carefully slide the replacement alternator into its designated mounting bracket, making sure it sits flush and aligns perfectly with the belt tensioner. Pay close attention to the orientation and make sure it's positioned correctly for the serpentine belt. Next, secure the alternator using the same bolts you removed earlier, and tighten them to the correct torque specified by Hyundai. Using the wrong torque can lead to the bolts loosening and creating problems later on. Once the alternator is securely fastened, it's time to reconnect the wiring. There's typically a main power wire and a harness, so ensure both are connected properly and that all connections are firm and secure. Loose connections can lead to problems with the electrical system in the future. Finally, re-install the serpentine belt, making sure it follows the correct path, and then reconnect the battery. You're almost finished with this process, and getting the belt tension correct can be important, but we'll cover that in a later section. If you follow these steps carefully, you should have a newly installed alternator that can get your Tucson back to operating normally.
1. When putting in a new alternator, always use a fresh alternator belt. This is pretty much a given for maximizing performance and extending its life. It seems obvious, but sometimes the simplest things get overlooked.
2. Before you install the new alternator, check the battery's charge. If it's low, use a battery charger to bring it up to snuff. This is to keep the alternator from overheating during the initial startup – a common oversight that can lead to further problems.
3. Slide the new alternator into the bracket and make sure it's lined up correctly with the belt tensioner. Getting this right the first time will prevent headaches down the road.
4. Secure the alternator with the same bolts you removed when taking out the old one. It seems like such a basic step, but it's easy to rush it and make a mistake. Double-checking here is definitely a good idea.
5. Reconnect all the wires to the new alternator, ensuring that the electrical connections are tight. This might seem like another simple step, but even a loose connection here can lead to intermittent electrical issues.
6. Carefully install the alternator, keeping any loose wires or the serpentine belt out of the way. The engine bay in these vehicles isn’t always the most spacious, so you’ll want to be careful to avoid snagging something while installing the unit.
7. If you're having a hard time putting the serpentine belt back on the alternator pulley, consider using a special tool to help out. It's definitely an easier way to get the job done and avoids any chance of getting it wrong.
8. If you're having trouble getting the alternator out, take a close look. There may be components or heat shields that need to be removed to get it out. You may have missed something in the first pass.
9. To make it easier to remove the belt, use the tensioner to create some slack. Or, you can loosen the tension bolt, which serves the same purpose. A slight amount of experience with these older cars really helps.
10. Once you’re done with the installation, hook the positive battery cable back up. This will get power flowing back to the vehicle. Hopefully, you’ve followed all of the correct steps and it will start up with no issues.
More Posts from tunedbyai.io: