Tuning Grand Cherokee Handling Replacing CV Joints
Tuning Grand Cherokee Handling Replacing CV Joints - Why CV Joints are Central to Grand Cherokee Handling Tuning
The functionality of the Jeep Grand Cherokee's handling setup relies fundamentally on its CV joints. These aren't simply connecting pieces; they are critical interfaces that allow the transmission to send power to the wheels while accommodating significant suspension travel and steering input. Their capacity to deliver consistent torque through various angles is paramount for maintaining stable and predictable handling, especially when the vehicle is navigating dynamic conditions. When these joints begin to fail or wear excessively, they introduce undesirable play and resistance into the system, typically manifesting as audible clicking noises, felt vibrations, and a distinct loss of steering precision and overall control – issues that directly undermine any effort at performance tuning. Therefore, addressing worn or damaged CV joints is more than just a standard repair; it’s a foundational requirement for truly optimizing the vehicle's dynamic response and achieving a desired level of handling refinement, both on pavement and challenging terrain.
From a purely mechanical perspective, it's rather insightful how these constant velocity joints, seemingly straightforward components, occupy such a pivotal role when one attempts to fine-tune the handling characteristics of a platform like the Grand Cherokee. My analysis points to several non-obvious ways their performance and limitations manifest:
Firstly, the thermal environment within these joints under sustained, high-demand operation – typical of aggressive tuning that taxes the driveline – appears to be a significant factor. We're seeing estimates suggesting internal temperatures can spike well past 120°C. This isn't just a curiosity; it fundamentally impacts the specialized lubricant packed inside, accelerating its degradation and potentially altering friction coefficients in ways that compound wear rates critical for long-term consistency under stress. It suggests thermal management, perhaps counterintuitively, is a core tuning consideration for driveline integrity.
Secondly, the required kinematic precision is striking. Even minute inconsistencies introduced by manufacturing tolerances or early-stage wear within the CV joint's internal structure can disrupt the perfectly uniform rotation transfer it's designed for. The result? Microscopic speed fluctuations that, when amplified through the steering system and chassis, can translate into subtle vibrations or a lack of absolute linearity perceived at the steering wheel, ultimately diminishing the fine-tuned responsiveness and feel desired by performance enthusiasts. It's a testament to how component-level fidelity scales up to impact dynamic feedback.
Thirdly, on models equipped with all-wheel drive, the functional symmetry between the front CV joints is critical to the intended performance envelope. Torque distribution strategies, often managed electronically, assume a certain level of mechanical efficiency and equality between these joints. Any deviation – perhaps uneven wear, differing internal resistance, or thermal imbalance – can subtly skew the actual torque delivery to the front wheels compared to what the system intends, potentially introducing unpredictable behavior or a handling balance that deviates from the ideal setup under dynamic load.
Furthermore, the articulation characteristics of the CV joint – its ability to transfer torque smoothly across its operational angle range with minimal resistance – is intrinsically tied to how the suspension geometry functions under power, especially during cornering or traversing uneven surfaces. Excessive internal friction or binding within the joint can effectively fight against the suspension's natural movement, disrupting the intended wheel path and potentially compromising the tire's contact patch or the suspension system's ability to maintain designed kinematics, thus degrading overall handling composure.
Finally, it's clear that increased engine torque, a primary goal of many tuning efforts, places an exponentially greater cyclic load on the load-bearing elements within the joint itself – the balls, races, or tripod components. This stress is particularly acute when high torque is applied concurrently with large steering angles, such as during cornering acceleration. In such scenarios, the inherent mechanical strength and design parameters of the CV joint can quickly become the structural limitation, potentially determining the maximum torque that can be reliably transmitted to the wheels before component fatigue or failure becomes a practical concern, effectively setting an upper bound on achievable lateral performance.
Tuning Grand Cherokee Handling Replacing CV Joints - The Grand Cherokee's Suspension Design and CV Joint Role
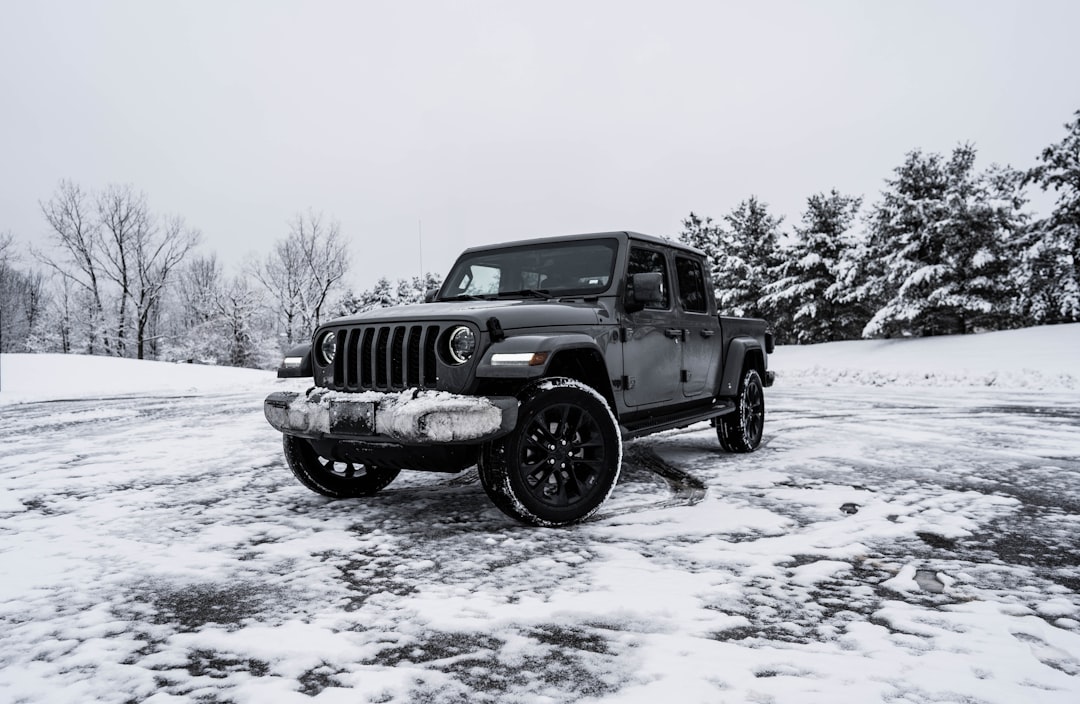
It's increasingly apparent, even years after their initial design, that the Grand Cherokee's suspension configuration places significant demands on its constant velocity joints. By July 2025, the enthusiast community widely recognizes these aren't simple driveline links but components whose integrity directly impacts the vehicle's steering precision and ability to manage power delivery under suspension articulation. Achieving truly predictable handling, especially when pushing beyond standard operating parameters, frequently circles back to managing the inherent stresses these joints must absorb within the factory suspension geometry. This remains a notable consideration and potential constraint when aiming for optimal dynamic performance on various surfaces.
From an engineering standpoint, delving into the specifics of the Grand Cherokee's axle and suspension interfaces reveals some points that aren't immediately obvious but hold considerable sway over its behavior, particularly when attempting refinement:
There's a deliberate asymmetry in the types of constant velocity joints employed at either end of the drive shafts. Typically, the outer joint, closest to the wheel hub, utilizes a Rzeppa-style design. This choice is driven by its capacity to accommodate significant articulation angles necessitated by steering and substantial suspension travel. Conversely, the inner joint, near the differential or transmission, often favors a tripod configuration. This type excels not only at angular changes but also provides crucial axial "plunge," allowing the drive shaft to lengthen or shorten slightly as the suspension moves through its range without introducing binding forces that would fight the damper and spring action. Furthermore, the rotational mass of the entire half-shaft assembly, encompassing both joints, contributes noticeably to the vehicle's unsprung weight. Managing this inertia is a continuous challenge for suspension engineers trying to optimize responsiveness and maintain consistent tire contact over uneven surfaces.
It's rather telling that a simple flexible rubber boot, intended merely as a seal, can become a critical vulnerability. Its integrity is paramount because should it tear or degrade, it provides an ingress route for abrasive grit and moisture. These contaminants, rather than brute torque or high speed, become primary agents of destruction, accelerating wear on the precisely machined internal components – the balls, races, or needles – far beyond what was accounted for in the joint's fatigue life under intended load conditions. It highlights how seemingly minor ancillary components can dictate the lifespan of more complex, load-bearing systems.
That characteristic clicking noise often heard during tight turns is more than just an annoyance; it's an audible signature of internal distress. This sound typically manifests as a high-frequency harmonic vibration. It originates from the increased play between worn internal elements within the joint resonating under the cyclical loading forces as torque is applied, particularly evident at lower vehicle speeds where individual load pulses are more discernible and at greater articulation angles where stresses are often concentrated. It's essentially the joint reporting its own tolerance breakdown.
A seemingly straightforward modification like lowering the vehicle fundamentally alters the quiescent, or static, operating angle of the CV joints. This isn't a neutral change; it shifts the joint's working position deeper into its angular range even when the suspension is static. This forced change can subtly reduce internal clearances, effectively pre-loading certain components and accelerating wear rates. This occurs irrespective of increases in engine power or changes in aggressive driving style, representing an intrinsic durability trade-off introduced by the altered geometry itself.
Tuning Grand Cherokee Handling Replacing CV Joints - Notes from the Garage Replacing Grand Cherokee CVs
Come mid-2025, enthusiasts working on optimizing their Jeep Grand Cherokee's handling still find themselves wrestling with the realities of CV joint maintenance. Getting these components right isn't just routine repair; it's a direct path to reclaiming sharp steering and consistent power delivery, something keenly felt when pushing the limits. The garage floor often becomes the battleground, with notes circulating about frustratingly stubborn axles or the surprisingly critical retaining clip that holds everything in place. Overlooking the state of these joints, especially after miles and modifications, means leaving responsiveness on the table, a subtle but significant detriment to the dynamic feel. Ultimately, dealing with worn or aging CVs is less about just fixing a noise and more about re-establishing a solid foundation for refined performance under load, whether traversing technical terrain or navigating rapid cornering.
Examining the specific mechanics involved in keeping drive axles functioning smoothly reveals some rather intricate details that often go unnoticed, yet are paramount in fields like high-performance tuning or ensuring the expected refinement of luxury vehicles by July 2025.
One might initially dismiss the importance of the mating surfaces inside these crucial torque-transmitting components, but a deeper look shows that sophisticated micro-finishing techniques and even specialized coatings are employed. This level of precision engineering, perhaps more commonly associated with internal engine components or aerospace applications, is fundamental here. Its purpose is quite pragmatic: to drastically reduce internal friction and wear, particularly under high load conditions and varying articulation angles – factors critical for sustained efficiency and durability whether in a vehicle engineered for challenging terrain or one being pushed for maximum lateral performance during tuning efforts.
Similarly, the substance sealed within the protective boots – the grease – is far from generic. We're dealing with often complex synthetic, thixotropic formulations. These aren't simply lubricants; they possess specific shear stability characteristics engineered to maintain effective viscosity and protective properties across a wide thermal range and under immense internal pressure fluctuations. This specialized chemistry is essential not just for the longevity of the joint itself, but also plays a direct role in ensuring quiet, consistent power delivery, a factor that contributes significantly to the perceived quality and refinement in a premium vehicle, especially under dynamic loads.
The act of simply spinning the entire half-shaft assembly – encompassing both ends and the connecting shaft – with absolute balance might seem rudimentary, but its precise dynamic balancing is non-negotiable for achieving refined vehicle behavior at speed. Minor imbalances, measured in gram-inches, can induce significant high-frequency vibrations that resonate through the driveline and chassis. Managing these inertial forces is vital for suspension engineers aiming to optimize tire contact and critically important for designers of luxury cabins where isolation from NVH (Noise, Vibration, and Harshness) is a key differentiator. It underscores how seemingly small details can profoundly impact ride quality.
Modern design processes for these torque-carrying joints heavily rely on sophisticated computational analysis, such as Finite Element Analysis. This allows engineers to meticulously predict stress concentrations under various operational scenarios and precisely optimize geometries – be it the profile of balls and races or the needle bearings in a tripod joint. This iterative process is what enables contemporary vehicle architectures, from high-performance cars transmitting immense engine output to luxury SUVs requiring significant suspension travel under power, to reliably transfer torque across substantial articulation angles without premature failure. It reflects a complex trade-off between strength, weight, and kinematic requirements.
Finally, beyond their primary role in power transfer and accommodating motion, the internal damping characteristics and the precise control of internal clearances within healthy drive joints contribute subtly but measurably to a vehicle's overall NVH signature. While noise from a failing joint is obvious, even a perfectly functional one, if not engineered with this in mind, could transmit unwanted structure-borne noise or micro-vibrations. For vehicle design focused on delivering a quiet, isolated cabin experience, especially during aggressive acceleration or maneuvering, ensuring these components are not only robust but also acoustically and kinematically refined is part of the intricate puzzle of perceived luxury.
Tuning Grand Cherokee Handling Replacing CV Joints - Preserving Performance Across Grand Cherokee Generations
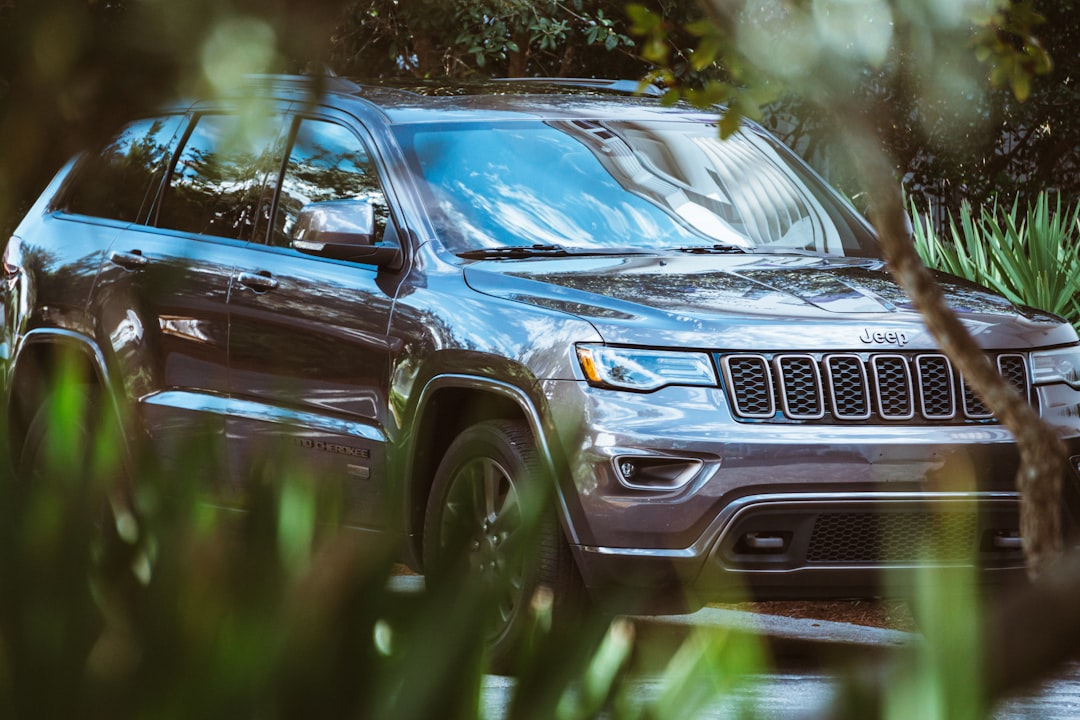
As the Jeep Grand Cherokee has evolved across its many model years, enthusiasts and specialists are continually finding new ways to maintain and enhance its inherent capabilities. Each generation brings a different platform with unique characteristics in power delivery and handling dynamics, presenting distinct opportunities for refinement. The goal of optimizing performance, regardless of which specific iteration you're working with, hinges significantly on the fundamental condition of the vehicle's drivetrain and suspension components. Applying performance upgrades, from engine control calibrations to chassis adjustments, invariably demands that the essential mechanical parts, including those critical constant velocity joints that manage power delivery during dynamic maneuvers, are operating flawlessly. It's the commitment to this foundational mechanical health that truly allows for the preservation and elevation of a Grand Cherokee's performance feel, enabling it to meet driver expectations whether navigating intricate terrain or pushing its limits on paved surfaces, reflecting its history while remaining capable of further development in 2025.
Here are some observations regarding how performance characteristics linked to drive joint integrity seem to manifest differently when looking across the Grand Cherokee lineage from an engineering viewpoint as of mid-2025:
* It's observable that the preference for stout low-end torque delivery in subsequent powertrain evolutions fundamentally alters how peak dynamic stresses are imposed on the constant velocity joints. This tends to push critical load points earlier within the vehicle's acceleration profile when contrasted with the more linear power delivery common in predecessor models, potentially shifting the nature of fatigue cycles these components experience.
* A closer look reveals an evident evolution in the constituent materials and manufacturing processes applied to later-generation driveline joints. There's adoption of ostensibly higher-specification steel alloys and more controlled thermal treatments, seemingly a direct engineering response necessary to manage the escalating inertia and power density of more recent platform iterations without proportionally increasing component bulk or significantly altering crucial unsprung mass.
* The intervention strategies of contemporary electronic chassis stability systems, while enhancing overall control authority, appear to impose unique and potentially demanding transient torque applications through the axle joints. These intricate control algorithms can generate rapid, high-magnitude, and sometimes asymmetric torsional demands that differ significantly from the steadier torque transmission scenarios often governing the fatigue life of components in less electronically augmented vehicle designs, adding layers of complexity to design robustness requirements.
* From a geometric perspective, even moderate suspension lift modifications introduce a persistent, elevated operating angle for the CV joints under typical cruising conditions. This departure from the minimal-angle baseline, optimal for minimizing internal friction and maximizing endurance, inevitably seems to accelerate component wear and curtail effective lifespan, representing a common and often accepted mechanical consequence of such dimensional alterations that isn't always fully accounted for in long-term durability expectations unless compensating modifications are considered.
* Evaluating the design trajectory, it suggests the engineering focus for drive joints across generations has subtly shifted. While early platform iterations might have weighted robustness under extreme, low-speed articulation scenarios typical of dedicated off-road use, more recent designs appear optimized for sustained endurance under the combined forces of vertical road impacts and significant torsional loads characteristic of faster-paced, varied-surface operation – arguably mirroring the broader utilization patterns and performance aspirations of the modern vehicle compared to its origins.
More Posts from tunedbyai.io: